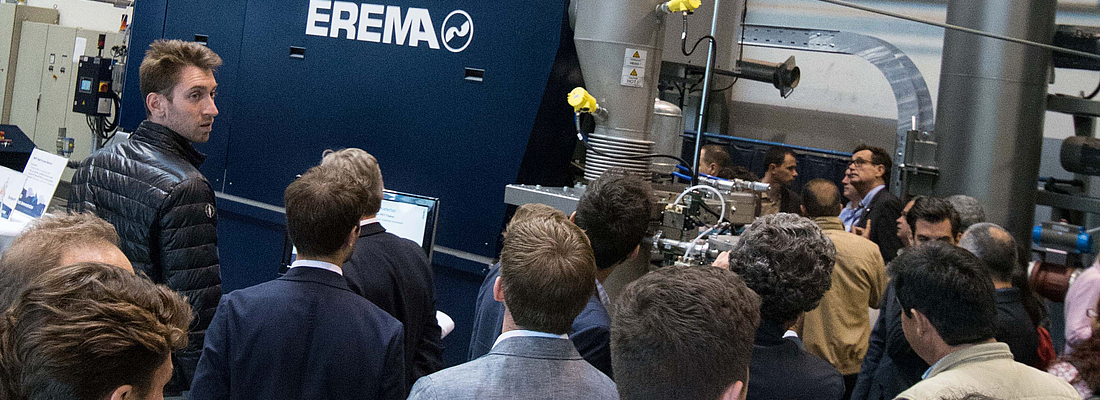
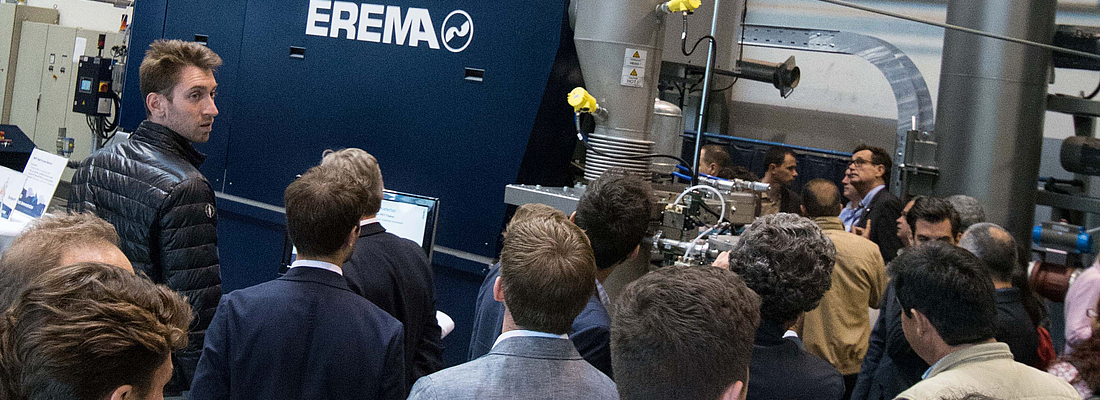
Around the world 167 Vacurema systems made by Erema, the Austrian recycling plant manufacturers, are processing over 1 million tonnes of postconsumer material every year to make rPET for direct food contact. In this short interview we spoke with Christoph Wöss, who is responsible for Business Development Management Application Bottle at Erema about the Vacurema technology.
What are the main reasons for the success of VACUREMA technology?
On the one hand our decontamination process fulfils the criteria of both the FDA and EFSA and many major branded companies. The parameters for direct food contact compliance are monitored and saved continuously throughout the recycling process. Any material which goes beyond the defined limits is removed from the production line. Secondly, Vacurema offers recyclers dependable cost-efficiency. No additional predrying is necessary as amorphous flakes in the vacuum reactor are not only decontaminated before extrusion, they are also dried and crystallised. Additionally, we use core components for our recycling systems which save costs on a day-to-day basis in continuous operation. One example of this is the utility-free vacuum pump which requires no water to create the vacuum. Compared to other pump systems, this means considerable operating and maintenance cost savings after just one year.
In conversations with prospective customer, ecological aspects are being cited with increasing frequency as a key factor when choosing which recycling plant to buy. Through the pretreatment in the vacuum reactor and our ecoSAVE® technology we can offer considerably lower energy consumption than conventional technologies in the marketplace. Just one example: the specific energy consumption of our inline sheet system is only 0.29 kWh/kg (incl. sheet downstream). This has also been clearly confirmed by an independent research institute.
Where is currently the biggest potential in recycling for direct food contact?
I think it has to be in PET sheet production. The share of rPET compared to virgin material has increased considerably in recent years. With the Vacurema inline sheet system it is even possible to produce 100% rPET sheet for direct food contact – with full throughput capacity and the best filtration. One particular benefit for plant operators is the high degree of flexibility in the choice of input materials. This enables you to mix washed bottle flakes quite easily with production waste such as skeleton waste and edge trim to make 100% rPET sheet directly from the melt. The recyclers and producers also benefit from great flexibility in plant configuration. This is because it can be easily combined with the customer’s preferred downstream sheet unit. In addition to this the Vacurema technology can be retrofitted on existing PET extrusion facilities. In this case the existing extrusion system is fed with dry, crystallised and decontaminated flakes.
Mr. Wöss, thank you very much for your statements.
The comPETence center provides your organisation with a dynamic, cost effective way to promote your products and services.
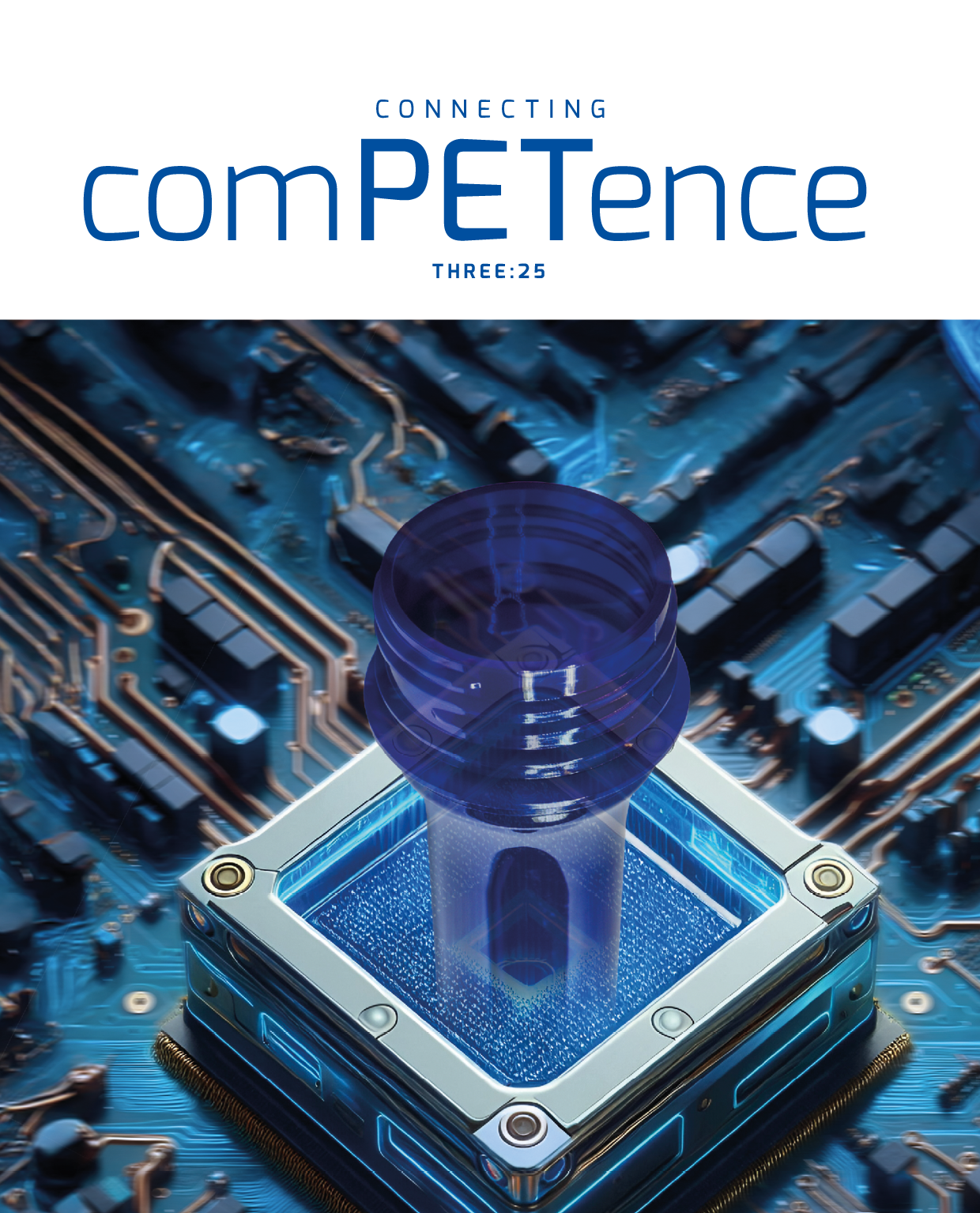
magazine
Find our premium articles, interviews, reports and more
in 3 issues in 2025.