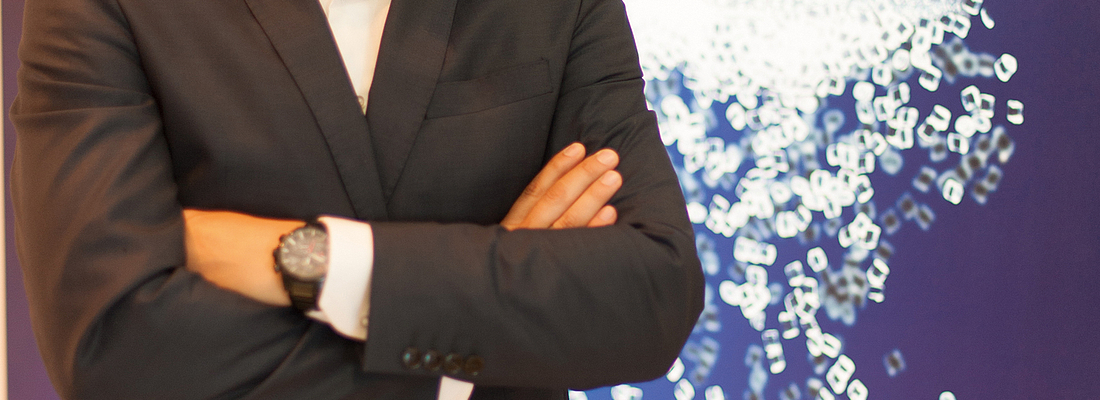
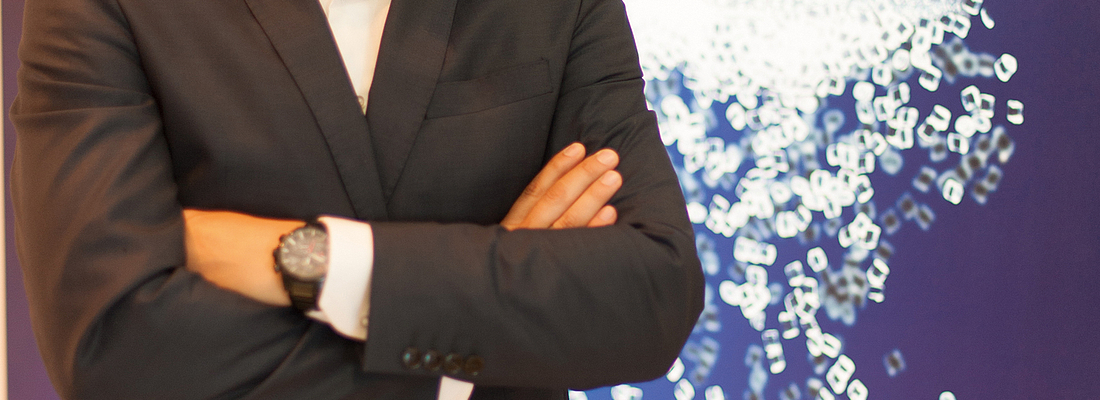
PET has been regarded as a prime example of plastic recycling for a number of years. No other plastic has a value chain which has been analysed so thoroughly with handling processes (separation, collection, sorting, recycling and reprocessing) that are so carefully tuned to each other.
Turnaround in PET recycling trend: from recycler to producer
The great economic and sustainable success of PET recycling, however, suffered a major setback in 2013 as a result of the low oil price. The price of virgin material was suddenly more or less on a par with that of recycled pellets. This development in the market prompted recyclers in particular to reconsider their business model and led to new forms of collaboration between recyclers and brand owners. Working together brought benefits for both sides: recyclers had a reliable market of buyers for their recyclates and brand owners were able to make the reuse of rPET a USP compared to their competitors and have a positive image with consumers for promoting sustainability. Besides increased collaboration with brand owners, the direct processing of PET flakes to make semi-finished or end products emerged as a further trend. As a result, many recyclers extended their recyclate portfolio by adding sheet/strapping end products.
Mechanical engineering in the field of plastic recycling also had to react to the low oil price and customers’ changing requirements. At EREMA, the Austrian manufacturer of recycling systems, the order situation in the PET sector has shifted over the last 18 months to 85 per cent machines which produce end products directly from PET flakes. Further to this, EREMA joined forces with SIPA last year and developed the VACUREMA® Inline Preform system. Food-contact compliant 100% rPET can now be produced for the first time directly from post-consumer PET flakes in a single pass. By combining injection and compression techniques this system allows you to produce preforms that are up to 10% lighter than even the lightest injection moulded preforms. The trend towards recyclers seeing themselves more as producers will also prevail in 2017 – as a result of the oil price, the demand of well-known brand owners and also because of more and more politicians calling for a circular economy.
Circular economy as an opportunity and challenge in PET recycling
The European Union is committed to and striving for a circular economy in the interest of a sustainable approach to raw materials. The following recycling rates have been proposed for the plastics recycling sector: 65% of municipal waste and 75% of packaging waste within the EU by 2030. This proactive political approach will, in general, strengthen the upward trend in plastics recycling but also point out the challenges in no uncertain terms. In the initial stage, efficient collection systems are crucial in achieving these targets. There are currently no binding plans for national collection systems. There are a multitude of collection systems in place throughout Europe, ranging from the yellow bag for plastic to the deposit systems. Regardless of which system is used it can be said that PET has the highest collection and recycling rates of all polymers. The most recent PCI Wood Mackenzie Report (autumn 2016) documents that close to 59 per cent of the PET bottles in circulation in the EU were collected and recycled in 2015. This means 5 per cent growth compared to 2014. The findings of the study show the following picture of the immediate future: the collection and recycling of PET from the post-consumer sector will continue to rise but the increase will level out in percentage terms. The reasons for this lie in the difficulty of keeping PET clean-sorted as the number of product categories is growing all the time. These range from new types of PET milk bottles in France and Spain and aerosols in shaving foam cans to the wide variety of material compositions in PET thermoforming products. The latter include for example plastic trays for pre-packed salads or fruit and vegetables or packaging which may consist of several layers of polymer and is used to extend the shelf life of cheese and sausage products. These polymers with different property profiles (including viscosity, transparency, colour or bulk density) have an impact on the recycling process and the end application. Groups of experts within the Petcore Europe association are already working on these future product cycle challenges. Two working groups have been established as a result: the “Working Group on Opaque and Difficult to Recycle (ODR) PET Packaging” and the “Working Group on Recycling PET Thermoforms”.
The former was launched in May 2016 and works on an end-of-life strategy to improve recyclability. The working group looking into thermoforms has existed since June 2015 and has over 30 representatives of companies and organisations in the manufacturing industry and recycling sector. The aim here is to increase the amount of PET in thermoforms in Europe while at the same time offering sustainable recycling processes for these products.

Understanding PET recycling as the social responsibility of producers and consumers
PET is already making good progress in drawing level with the most sustainable industries such as metal, glass and paper. Closing the product cycle even further calls for support above all from producers and, in the broader sense, from receptive consumers. The market for organic products is booming especially because of increasing demand from consumers. So why not pay attention to the origin and composition of the packaging, too? This awareness/sustainability consideration would mean additional leverage for PET recycling.
With regard to sustainability, mandatory recycling rates for the use of rPET in end products, an EU-wide ban on landfilling or a note on PET bottles indicating the proportion of recycled materials would be just some exemplary political measures to push recycling.
The fact that the PET sector offers space for innovative ideas can be seen for example in another Petcore Europe project called “Polymark”. The objective is to develop a series of marker technologies for PET products. These should contain information such as properties or the structure of the product which can be recognised and assigned by a sorting device. The new technologies offer for the first time a mechanical method for the efficient sorting of plastics.
The PET industry needs more such showcase projects to keep recycling at a high level and also be able to master the new challenges.
The comPETence center provides your organisation with a dynamic, cost effective way to promote your products and services.
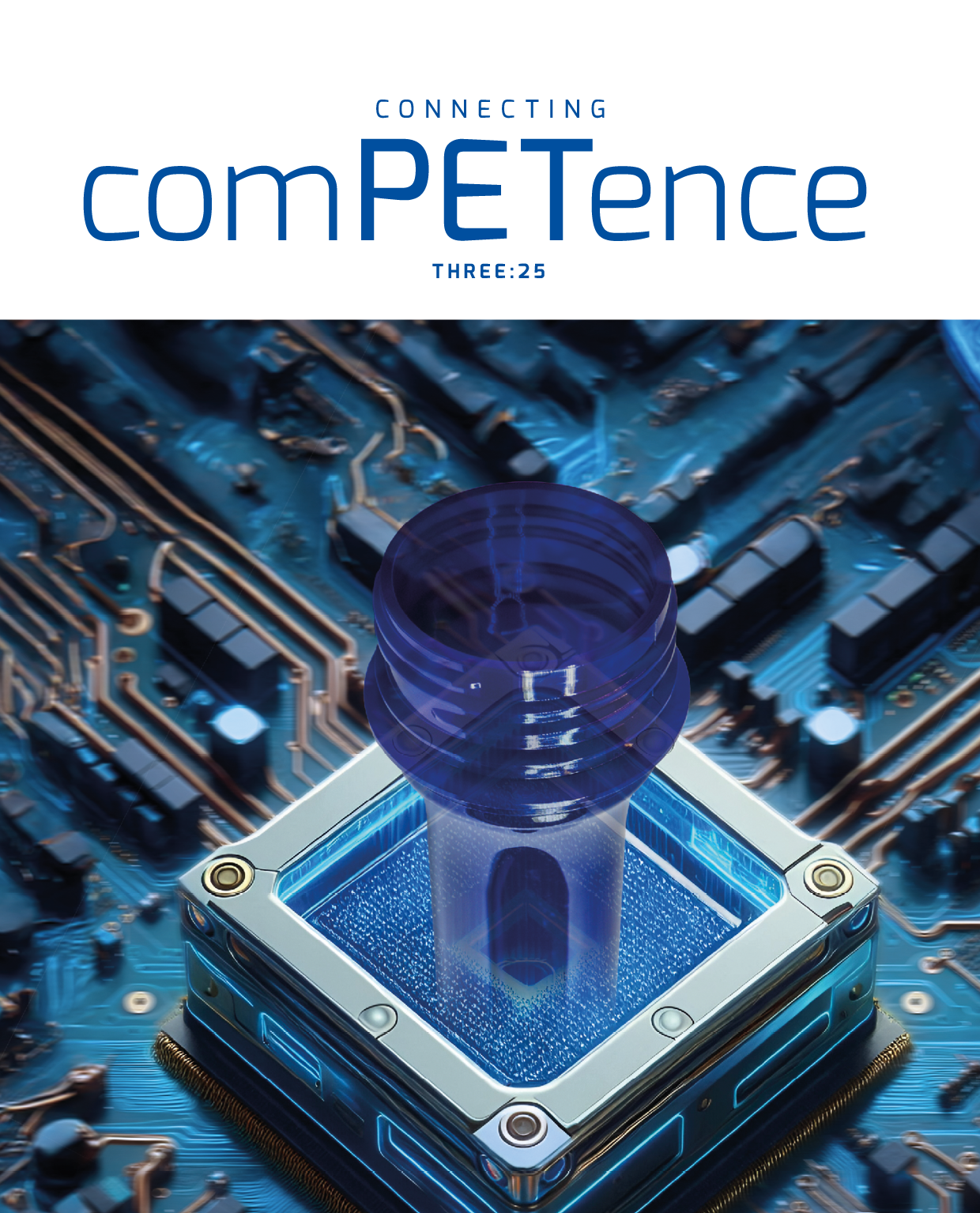
magazine
Find our premium articles, interviews, reports and more
in 3 issues in 2025.