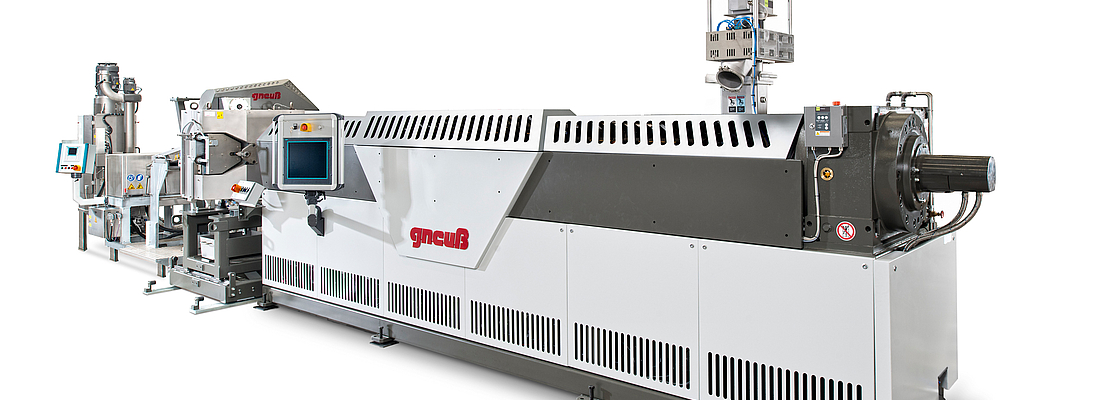
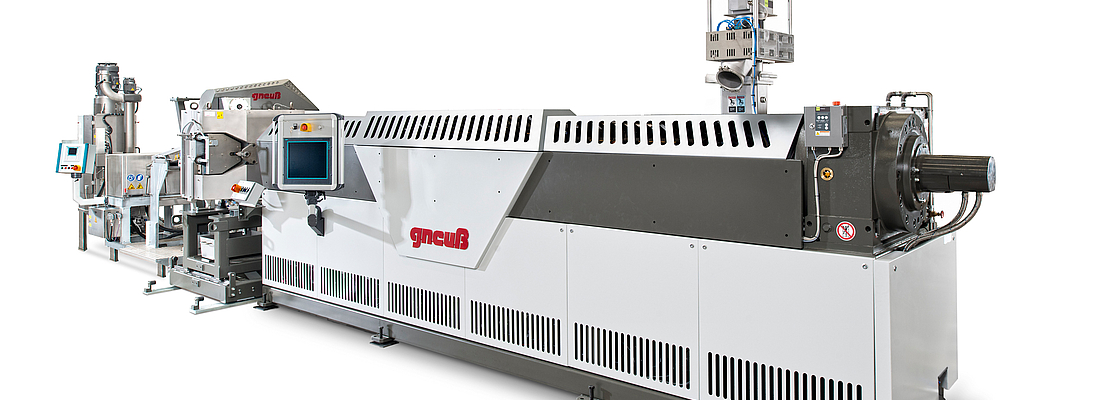
PET bottles to bottle grade chips
PET Bottle to Bottle Recycling with the MRS Extrusion Concept
The recycling of post consumer PET bottles to bottle grade chip is common practice today. There is, however, a clear trend toward ever increasing quality requirements in the future. With the optimum technology, it is possible to recycle PET bottles almost indefinitely, thereby achieving a real recycling cycle.
One special characteristic of PET which can make its processing difficult is its hygroscopic behaviour. During storage and during the washing of post consumer bottles, water molecules from airborne moisture or from surface contact diffuse into the PET. During the extrusion process, these water molecules break down the molecule chains (hydrolysis) resulting in a drastic reduction of the viscosity, unless the water is removed.
Manufacturing Process
After collection, coarse separation of foreign particles and materials takes place. Subsequently, the bottles are ground into flake. These flakes are washed in a hot wash process where dirt, labels and adhesive from the labels is removed. In a floatation bath, polymers are separated according to their specific gravity. The most common foreign polymer, PP (bottle caps) are floated off. The PET bottle flakes are then placed in a centrifuge to remove the surface water. Metals are separated out and further separation of PVC and in most cases, colour sorting takes place.
These bottle flakes are then processed on an extruder. The PET is melted and homogenized and filtered. The filtration system uses a woven wire mesh filter element to collect typical contaminants such as sand and other fine particles.
To ensure a homogeneous melt, a static mixer is typically used.
Subsequently, the PET is pelletized. Depending on the type of pelletizing process used, the result is spherical or cylindrical PET pellets or chips.
These pellets or chips are dried, crystallized and go through an SSP process (solid state polymerization) where the viscosity is raised to the required level.
Depending on the throughput rate, this final processing stage can be a continuous process (for larger throughput rates). For smaller throughput rates, typically the more flexible discontinuous processes are used.
Manufacturing Process with Gneuss MRS Technology
The Gneuss MRS technology is an attractive alternative to conventional recycling technologies and opens new possibilities with regards to flexibility, quality and energy efficiency.
The gentle treatment of the polymer in the MRS extruder and the fact that the material processed on this extruder means only relatively short residence times in the SSP result in a low amount of yellowness and excellent transparency.
Thanks to its great flexibility, the MRS concept is particularly well suited to the processing of smaller flows of materials of different types (colour, source) combined with a discontinuous SSP whereby the viscosity can be set individually for each batch.
The PET chips of pellets can be used for the most diverse applications: for fibres, sheet for thermoforming and of course for injection moulding performs for bottles.
Additionally, it is possible to produce chips or pellets from up to 100 % post consumer bottles for products which come into direct contact with foodstuffs.
The MRS extrusion process has a LNO (letter of non objection) from the FDA for processing 100 % PET bottle flake to food contact products both with and without a subsequent downstream SSP process.
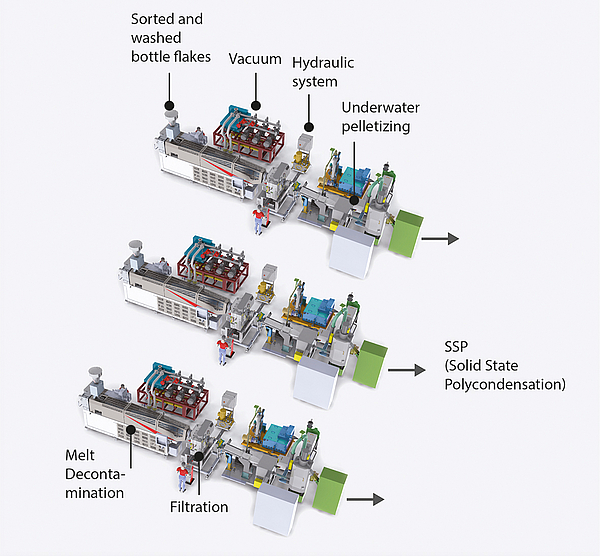
The importance of moisture extraction in the PET extrusion process
Today, the established technology for the minimization of degradation of the PET is to dry the material before processing it on a single screw extruder. The drying of PET is complicated, maintenance intensive and expensive in terms of investment costs, factory space and running costs due to the high-energy consumption as the material is typically dried using dry air at 180°C. The fact that the material has to be dried for up to 8 hours also reduces the PET processor’s flexibility.
In the processing of PET with an extruder at normal processing temperatures, a chemical process takes place in that any water molecules, which may be present, reduce the PET chain lengths, which results in a reduction in the viscosity, which in turn reduces the mechanical properties of the final product.
In order to avoid this problem, the pellets are conventionally pre-dried over a long period in order to remove the moisture prior to extrusion in order to prevent hydrolysis. This chemical reaction is, however, reversible and the point of equilibrium can be driven to one or the other side by reducing or increasing the water content. This phenomenon can be used to positive effect during extrusion. By removing the water molecules during processing, the damaged PET molecule chains can rebuild themselves. The physical prerequisites for the removal of water molecules are described by the diffusion process, which can be formulated with the help of the Fick’s first law:
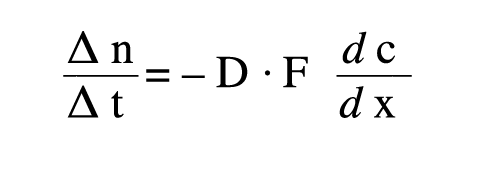
This law shows that the quantity of water removed (D n) will increase in relation to the residence time (D t) the larger the melt surface area (F) and the driving concentration incline (dc) and the thinner the polymer layer (dx). In other words, the better the polymer is mixed and the better the surface is exchanged, the more the chemical equilibrium will move toward long chain molecules with better mechanical properties.
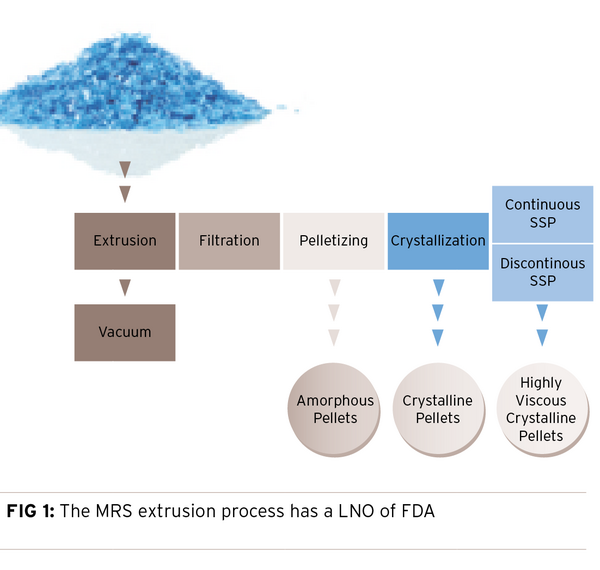
Devolatilization with the MRS extrusion concept
With the MRS extruder, PET pellets are processed direct, without pre-drying the material. During extrusion (in the melt phase) the polymer surface is greatly enlarged and exchanged at an extremely high rate, thereby enabling volatiles to be extracted (Fick’s law of diffusion).
The MRS (Multi Rotation System) extruder can be described in general as a single screw extruder with a very special degassing section. The polymer melt is delivered into a large single screw drum.
The drum contains eight small extruder barrels, parallel to the main screw axis.
Installed in these small extruder barrels are the “satellite” screws, which are driven by a ring gear in the main barrel. The satellite screws rotate in the opposite direction to the main screw while they rotate around the screw axis. This disproportionately increases the surface exchange of the polymer melt.
The extruder barrels which are cut into the drum of the multi rotation system are approximately 30% open to ensure the optimum melt transfer into the barrels and so that the evacuation can take place without restrictions. Further, precise control of the melt temperature is possible as the temperatures of all the surfaces in contact with the melt can be controlled accurately.
Thanks to its patented multiple screw section, the MRS makes a very large area available and permits unmatched degassing performance, even with a vacuum of only 20 to 40 mbar.
This makes the processing of undried flakes or pellets with up to 1 % residual moisture (10.000 ppm) possible.
Further positive effects of the MRS technology are the 100% dehumidification of PET as well as the possibility of increasing the intrinsic viscosity of this material.
Thanks to the multi rotation elements, a melt surface is made available which is far greater than that of conventional extruders. For example: the MRS system creates a melt surface exchange rate which is 25 times greater compared with a co-rotating twin screw extruder.
The melt treatment is extremely gentle, resulting in a particularly high quality final product for example with regard to yellowness.
Compared with other multi screw systems, the MRS is characterized by its extremely compact and rugged design. The rotating satellite screws run in individual bearings and are therefore comparable with a drum containing a number of single screws.
The evacuation or degassing system is modular and can be ideally matched to the individual requirements, thanks to its remarkable performance. The position, length and design of the modules can be varied.
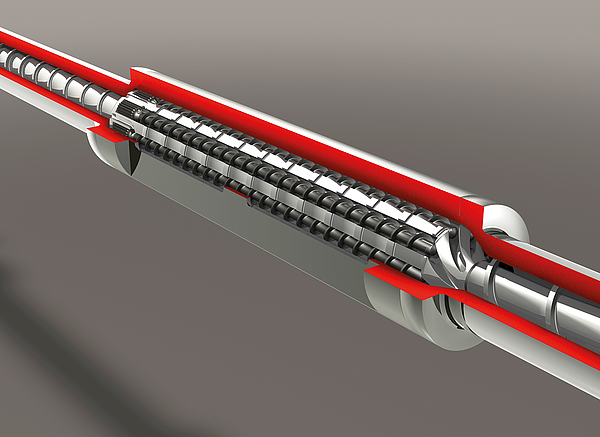
FIG 2: Multi Rotation Section
Online measurement and control of the processing parameters
Today, the monitoring, logging and analysis of processing parameters is a key element in plastics processing in order for example to be able to trace problems relating to a customer complain but also to be able to react as quickly as possible to changes in these parameters. Through this monitoring, a continuously high product quality can be ensured.
During extrusion, the most important factors with regard to the properties of the final product are the melt temperature, the melt viscosity and the melt pressure(s) in the machine. With the help of these parameters, the failure of heater zones or cooling fans, variations in the raw material parameters and wear in the line can be monitored. Dangerous situations can be avoided if equipment is for example automatically shut down if a too high-pressure increase takes place quickly.
Through the use of melt pressure and melt temperature sensors and with a known throughput rate and known geometry, the flow resistance of a liquid can be calculated and from this, the dynamic viscosity of the medium can be extrapolated. This is a measurement of the average molecular weight of the polymer which defines its properties such as elasticity and stretch or elongation.
The Gneuss Online Viscometer measures the viscosity of the polymer upstream of the die and is equipped with a control loop to regulate the vacuum on the MRS extruder, thereby ensuring that the viscosity is automatically held at a controlled, constant level.
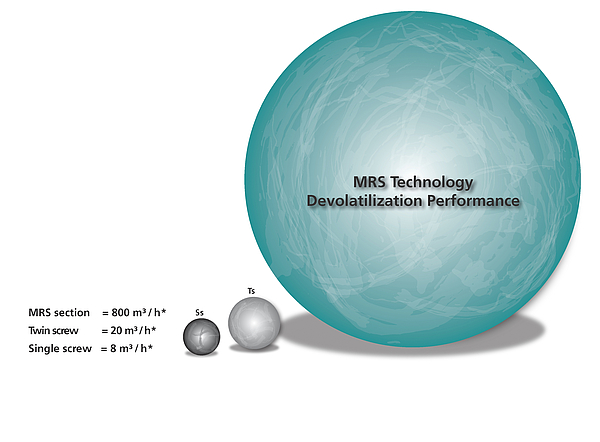
FIG 3: Comparison of different extrusion concepts;
* These values were calculated on the following basis:
Throughput rate = 1000 kg/h, Residual moisture level = 10 000 ppm, Vacuum = 25 mba
Melt filtration as a key element with regard to quality assurance and the economic aspects of the process
Before the polymer enters the die, all kinds of contamination should be removed, in order to achieve the highest quality requirements with regard to transparency (sheet) or tensile strength (sheet for thermoforming, strapping tape) and of course to protect the downstream components from damage. The Rotary Melt Filtration Systems from Gneuss are particularly suited to this purpose as they operate fully automatically and pressure constant.
The RSFgenius filtration system with its back-flush piston concept is a class of its own in the group of the so-called back-flush screen changers. It is an “all-round” system, based on a fully-automatic, pressure-constant and process-constant mode of operation, and it guarantees an end product without dimensional or quality variations. Thanks to the back-flush piston concept, an almost 100% screen cleaning is obtained even with very low filtration finenesses, which guarantees a multiple re-use of the screens. The quantity of melt lost through purging is minimal, i.e. lower than 1%. Today, this filtration system represents the highest standard on the world market, referring both to technical performance and cost efficiency. It is especially suitable for direct recycling processes.
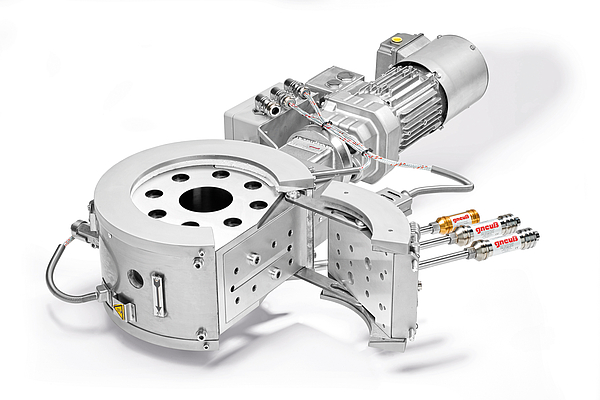
FIG 4: Online Viscometer VIS
Advantages of the MRS technology for Bottle to Bottle Recycling
The MRS Extrusion system offers the highest level of flexibility. This extruder can be fed with both crystalline and amorphous pellets/flakes with varying viscosities. The viscosity of the material leaving the extruder can be adjusted individually via the vacuum degassing system to suit the requirements of the application.
Amorphous pellets or chips made from PET processed on the MRS with a defined viscosity can be processed immediately. Alternatively, the pellets or chips can be crystallised and can even be processed in an SSP where higher viscosities are required.
Advantages of Gneuss Technologies for Repelletizing:
-Decontamination of volatiles, oils and odors
-LNO for food contact use from the FDA for up to 100% post-consumer recycled content
-Extraction of residual monomers
-Uniform, homogeneous pellets
-Amorphous, crystallized or highly viscous crystallized pellets
-High IV level
-Effective dispersion of fine particles
-High transparency, low yellowness
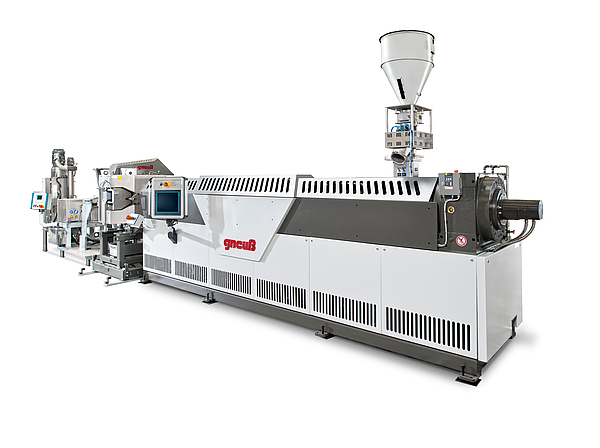
FIG 5: Self-cleaning Rotary Filtrationsystem RSFgenius
MRS case example application
Some years ago, a manufacturer of bottle flakes in North America has chosen to add value to his production by adding an extrusion line and sell chips instead/in addition to flakes.
With the MRS Extrusion concept, this company was able to avoid cost intensive, complicated and potentially damaging pre-treatment of the flakes prior to extrusion.
In the meantime he was very successful and found his market for his high quality chips, so he decided to increase his capacity, now PET is processed with a throughput rate of up to 3.000 kg/h in total from washed bottle flake to a high value PET bottle grade chip.
The MRS extruder, operating at a vacuum of 25 to 30 mbar permits very short residence times in the downstream SSP.
The Melt Filtration System type RSFgenius filters the material as fine as 20 µm in a single filtration step.
The Online Viscometer measures the viscosity of the polymer upstream of the die and is equipped with a control loop to regulate the vacuum on the MRS extruder, thereby ensuring that the viscosity is automatically held at a controlled, constant level.
The specific energy consumption of the MRS technology is 15% to 25% less than conventional technologies, not to mention the higher flexibility and less maintenance on dryers and/or high vacuum systems.
Furthermore, the melt has a very good molecular weight distribution without low-molecular components, so that deposits at the pelletizing die are rare. Thanks to the gentle treatment of the melt inside the MRS processing unit, the yellowness value is very low, the pellets are homogenous and have both high transparency and quality.
Thanks to the very high polymer melt surface area and its degassing efficiency the customer is able to produce pellets for direct food contact later on, not only fiber and sheet pellets, but also pellets for bottles, and he has been able to fulfil even the very high demands of the global players in this market as well.
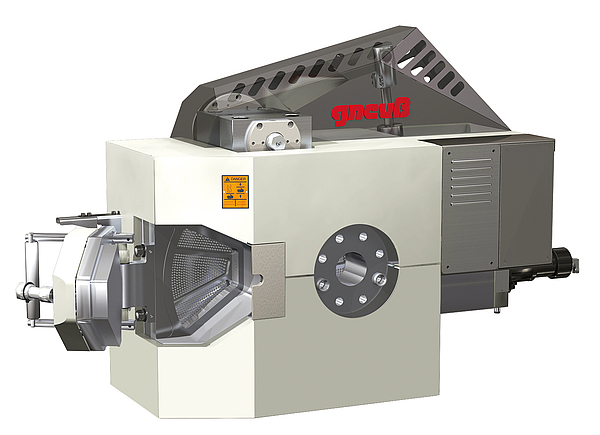
FIG 6: MRS Extruder with Rotary Filtrationsystem RSFgenius, Online-Viscometer VIS and Underwater pelletizing
The comPETence center provides your organisation with a dynamic, cost effective way to promote your products and services.
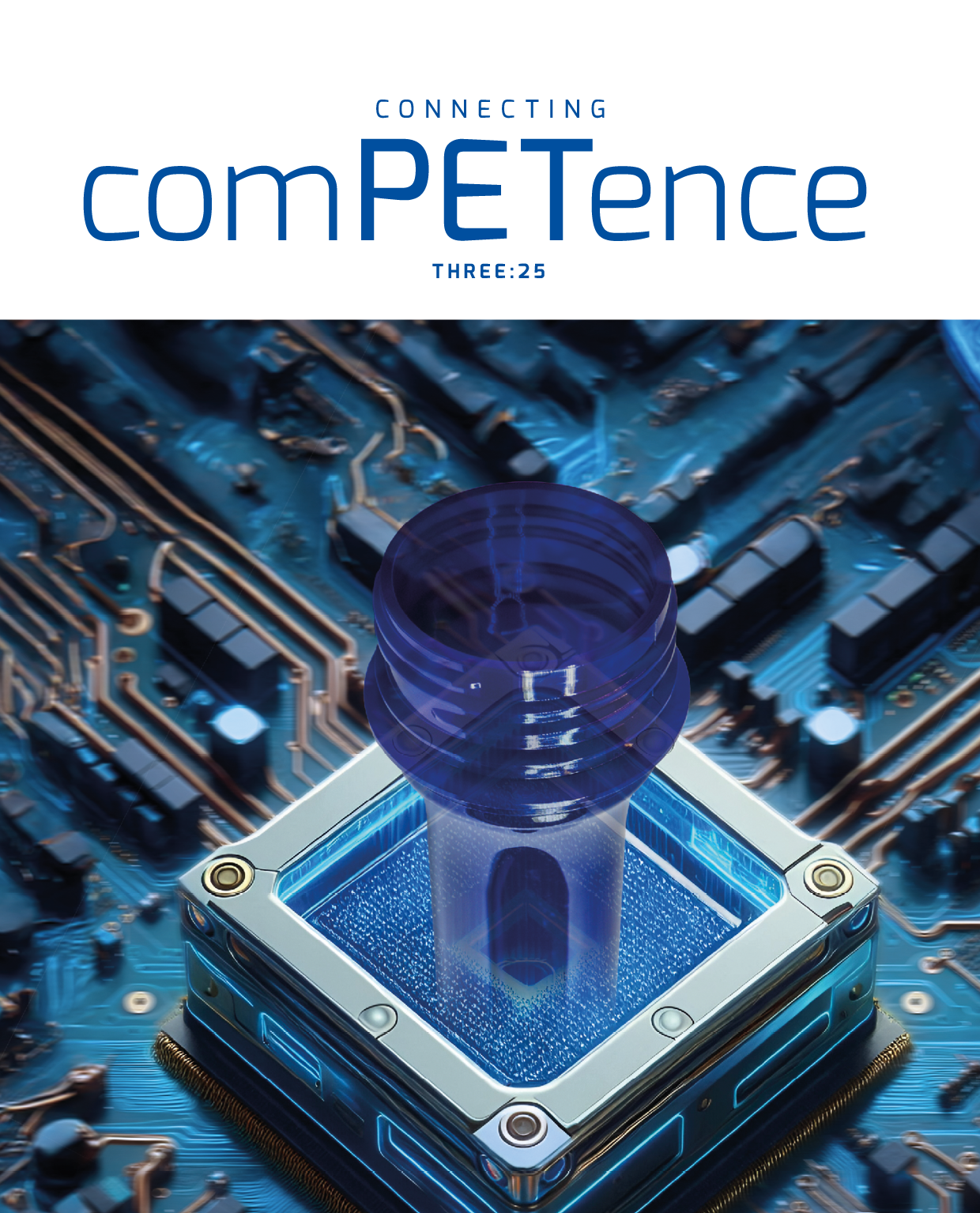
magazine
Find our premium articles, interviews, reports and more
in 3 issues in 2025.