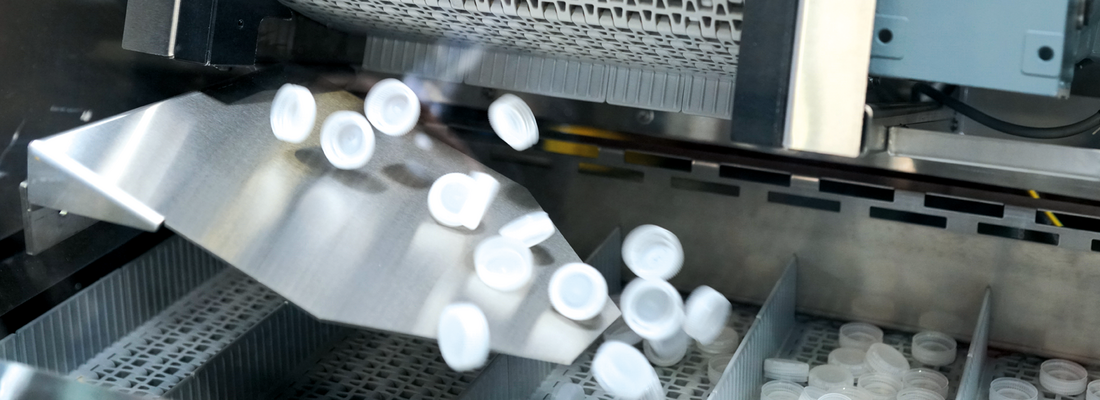
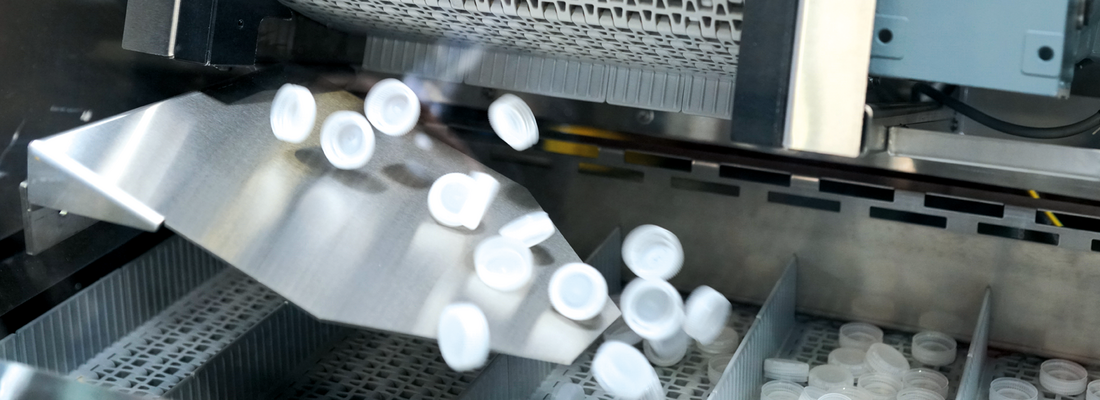
Injection Machine + Cap Mould + Vision Inspection | Meeting at Sumitomo (SHI) Demag Plastics Machinery | My dialogue partners: Arnaud Nomblot, Director - Business Development Packaging, Christoph Wynands, Product Manager High-Performance Injection Molding Machines (both Sumitomo (SHI) Demag Plastics Machinery GmbH) and Rolf Steinmetz, Managing Director IMD (EMEA) GmbH
No, we are not talking about tethered caps today. They have been at the top of the caps and closures agenda for years. Pros and cons continue to accompany their technological development, and consumers now see a variety of technical solutions on the supermarket shelves - and not just on PET bottles, but on other packaging units as well.
No, this article is about current and future challenges in the production of closures. We want to focus on the performance, energy consumption and system approaches of modern production systems.
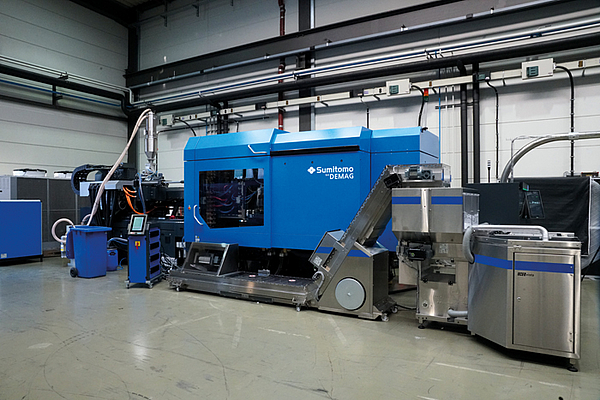
Cap production as a system
The new all-electric PAC-E high-speed injection moulding machine from Sumitomo Demag has been available to numerous customers for test purposes at the Schwaig site over the past few months. Before the system is shipped to the NPE in Orlando, USA, I took the opportunity to talk to three specialists - directly at the modern PAC-E machine: Arnaud Nomblot, Christoph Wynands (both Sumitomo (SHI) Demag Plastics Machinery) and Rolf Steinmetz, IMD, were my partners in dialogue about the exciting challenges of current and future cap production.
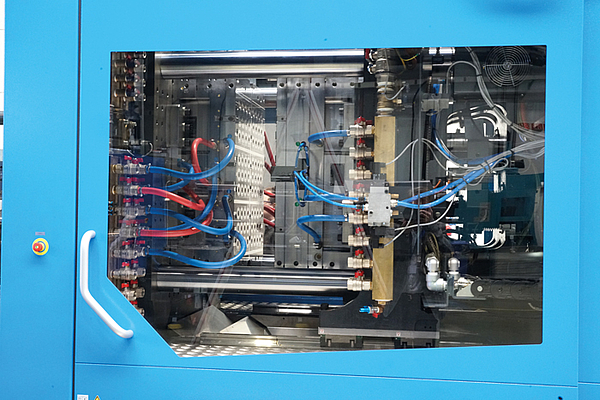
Challenges
It quickly became clear that high-end requirements can only be met with a sophisticated system development approach. So what are the current and future challenges for manufacturers in the closure business to succeed globally? And what does this mean for suppliers of machines, moulds and inspection systems?
The upshot: the challenges are driven more than ever by the ecologic and economic aspects demanded by brands and manufacturers. Ecological means: minimising the use of virgin materials and maximising the use of recyclates. A closed recycling loop from cap to cap is an interesting idea, although there are still a few hurdles to overcome. Eliminating the use of colour masterbatches, for example, would be a first step. From a cap manufacturer’s point of view, economical means minimising energy consumption and maximising output with a minimum scrap rate. This is about technology and processes, and increasingly about the use of AI. Where is the future development heading to meet the increasing environmental and economic demands? Our discussion inevitably leads us to the idea of inline production.
Whatever path cap production takes in the future, everyone involved in a cap system already has a duty to deliver: Machines, moulds, inspection and quality monitoring systems - all at the highest level. ROI as a metric puts additional pressure on the development of machines and technologies, because: the key variables for realising an ROI of, say, two years are cycle time and energy consumption. It appears that the developers of new production machines and quality control systems will have to make almost quantum leaps and consistently implement the system approach to cap production in order to meet these targets.
Inline production
Is inline production already an option for the cap market? We are familiar with wall-to-wall production concepts in PET bottle production, and there are inline concepts for preforms. Can we imagine something similar for caps and closures? And what does that mean for the mould, the machine and the closure?
Our discussion revealed that it is still too early to see a clear trend, but the temptation is there - and there have already been a few attempts in the market. This is not surprising as the energy and logistical advantages are obvious.
The main challenge in implementation is the inherent shrinkage behaviour of the plastic in a 24-48 hour time window and possibly beyond. Shrinkage reduction is a complex challenge. Material, masterbatch and process control are all critical to achieving short cycle times. Inline production would be a new production method where shrinkage values would have to be taken into account in the mould design. There is still a lot of material development work to be done before the shrinkage values are suitable.
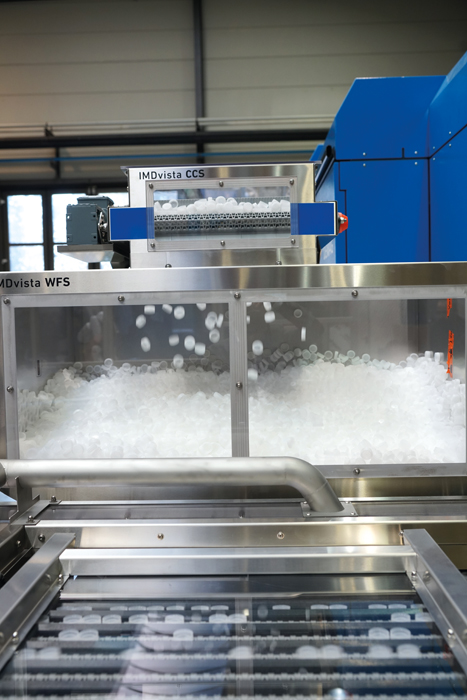
Quantum leaps bring uncertainties
“It is not only the new development itself that concerns us as suppliers, but also how it will be received by the customer,” says Nomblot. Customers are signalling that they want absolute certainty before they make a purchase decision: The development has to be mature, the performance excellent, the energy savings significant - in general, a new machine has to be very attractive.“
Confidence
The PAC-E has been in pilot production at selected Sumitomo Demag customers in the market for a year and a half. Nomblot: “This enables us to make optimisations and gain experience in production.“ The approach creates confidence - not only among customers, but also in the development and sales departments - before the official start of sales. Last but not least, successful sales of new systems require delivery times that are acceptable to the customer. The processes involved in machine production must be optimised and guaranteed in the supply chains. Nomblot: “We have taken the time to do this and are now looking forward to the imminent sales release.”
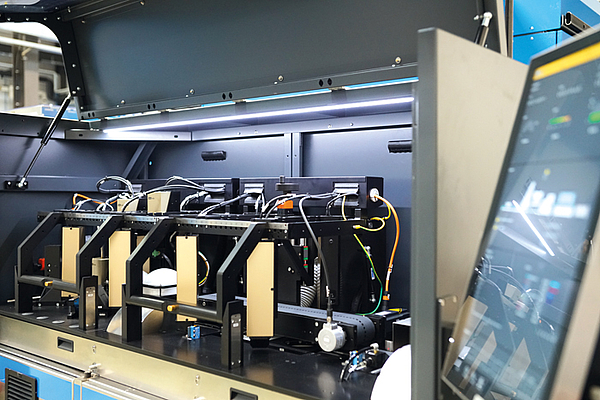
Main components of a modern cap system
Injection moulding machine
Sumitomo Demag’s aim with the new high-speed machine was to develop a fully electric injection moulding system on a new scale. The Sumitomo portfolio currently includes two all-electric models for the packaging market: There is the all-electric IntElect S for thinwall applications and special closures. And there is the PAC-E, of which Nomblot says: “It is still exciting to find out where the limits of the machine and its applications lie”.
According to Nomblot, an application comparison showed that the all-electric system scored highly in terms of energy consumption, with a 70% saving in electricity. Given the high cost of electricity in many countries, this would result in a payback period of approximately one and a half years.
According to Christoph Wynands, the main source of these savings is around half the energy required for injection via servo motors. Electrical savings are also possible on the clamping unit. Direct drives are much more efficient than hydraulic systems. According to Wynands, the maximum injection speed is lower with the PAC-E (550 mm/s compared to 1000 mm/s with the hybrid), but the dynamics are significantly higher. “This allows us to achieve the same or better results because the whole machine is designed for the short strokes required for packaging applications.
_______________
''It is still exciting to find out where the limits of the machine and its applications lie.'' - Arnaud Nomblot
_______________
Nomblot: “We’re not afraid to compare our performance with the competition. We have already demonstrated double-digit percentage reductions in energy consumption in some applications.” Nomblot and Wynands are proud that all this has been achieved using Sumitomo’s applicationspecific technology: “The machine incorporates our in-house designed and manufactured equipment: bespoke motors, frequency converters, control technologies and components such as special “injection moulding spindles”.
Cap mould
During our visit, the PAC-E demo model in Schwaig was running a 72-cavity mould from Z-MOULDS® with a hot runner from MHT (a member of the Krones Group). With a mould size of approx. 700 x 950 x 650 mm, this is a compact mould. The mould is equipped with the standard Z-MOULDS® z-slide with a 70 x 70 mm pitch. According to the manufacturer, this patented z-slides® technology (see. fig. 5) with a flat parting line is the key to the fastest cycle times on the market, minimal maintenance, low wear and ease of use of the mould.
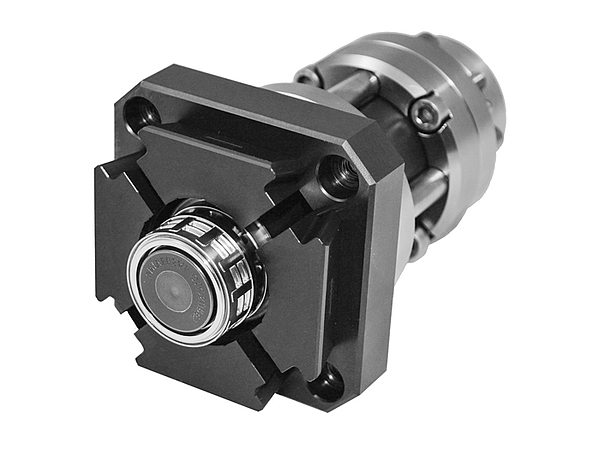
At our meeting, the PAC-E system produced a 1g cap with a diameter of 26mm - perfect for use in the still water market. The cycle time during the test run on the machine was below 2 seconds, which corresponds to a production of over 1 billion caps per year. With this setup, the system will be exhibited at NPE 2024 in Orlando, USA.
Mould design must also meet the demands for higher productivity per system described above. This means higher and higher output volumes per system, combined with consistently lightweight closure designs and a constant or decreasing footprint in production.
The latest development of the 55x55mm pitch, as Michael Fink, CEO of Z-MOULDS, reports on request, is an answer to ecological and economic requirements and a real innovation (see fig. 6). With this pitch, the 72-cavity mould described above would be approximately 600 x 750 x 650 mm, therefore fitting on smaller machines with smaller tie-bar spacing. This mould not only has a smaller machine clamping area, but also faster cycle times due to the lower mould weight and the greatly reduced drop height of the closures.
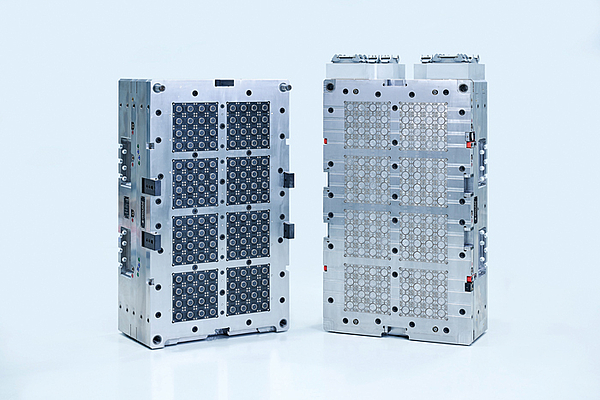
Inspection
The caps were demoulded at around 85°C in the test run and cooled down to around 29°C on the conveyor - without active cooling - before being transferred to the bunker. From there they are transferred to the waterfall sorter. With the opening facing up, the caps are indexed and separated at a distance for the calibrated inspection and measurement system IMDvista CAP MASTER (see fig. 7).
_______________
''We’re not afraid to compare our performance with the competition. We have already demonstrated double-digit percentage reductions in energy consumption in some applications.'' - Arnaud Nomblot
_______________
IMDvista’s new CAP MASTER in-line testing and measuring system allows caps to be inspected and measured with absolute values. This is a departure from the previous reliance on relative values. This new approach to measurement places particular demands on the stability of the inspection platform. The specially designed backbone provides an essential concept and the new mechanical structure for consistent and reliable calibration.
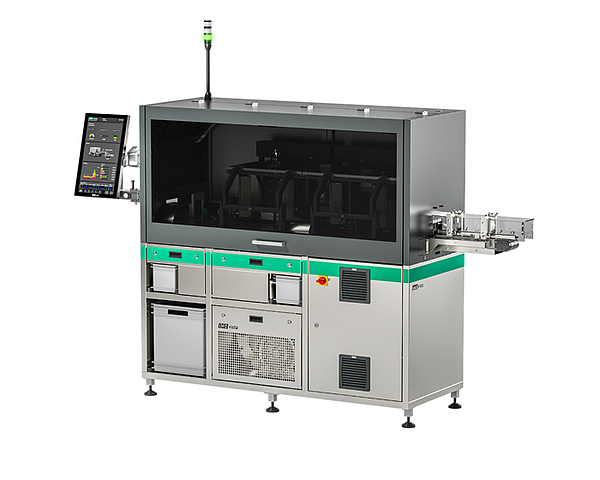
A new feature is that calibration is performed using certified calibration standards (see fig. 8). The calibrated test system also offers significant advantages for the production of identical closures at different production sites. The fact that the systems can be reproduced mechanically and software-wise at any time also gives the operator the assurance that errors in handling or software settings can be completely ruled out. Once the mechanical setup is complete, calibration or validation is easily performed using an automated process in the software. All systems are delivered with the same reproducible settings, both mechanical and software, as previously defined in the calibrated laboratory feasibility study.
Behind the IMDvista CAP MASTER, the caps are deflected into a mini-cyclone at a speed of up to 4,500 caps/min. The caps themselves have no contact with the wall due to the air turbulence on the inner wall. This reduces dust generation.
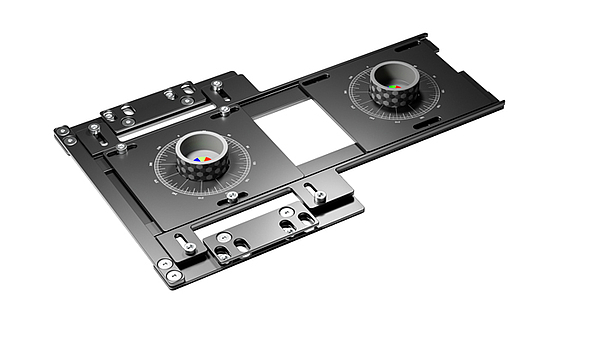
The system idea
Arnauld Nomblot sums up: “A production system always has interfaces. It is good to define the interfaces precisely. But - in addition - it is much better to have control over the interfaces in order to achieve optimal processing and production."
The comPETence center provides your organisation with a dynamic, cost effective way to promote your products and services.
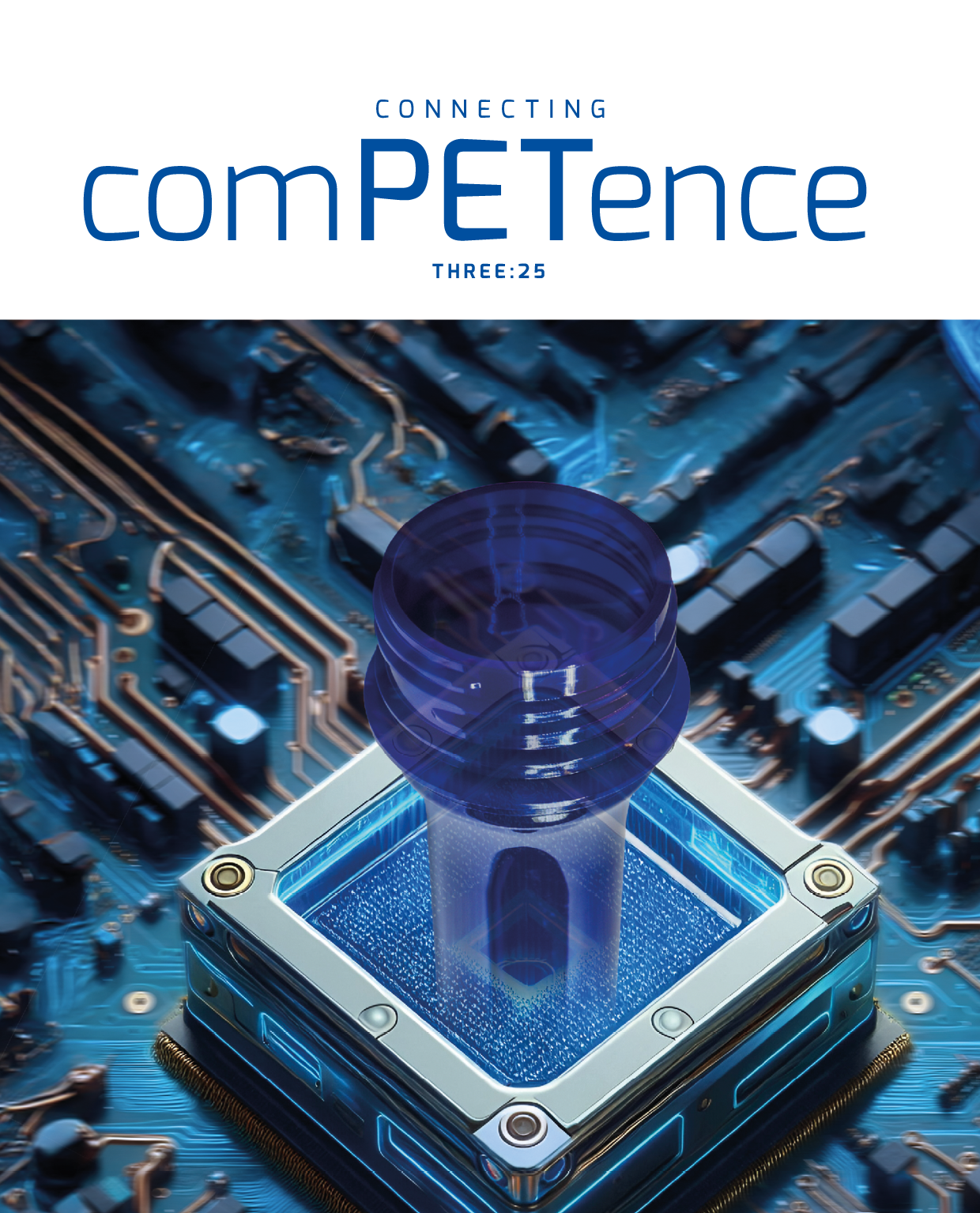
magazine
Find our premium articles, interviews, reports and more
in 3 issues in 2025.