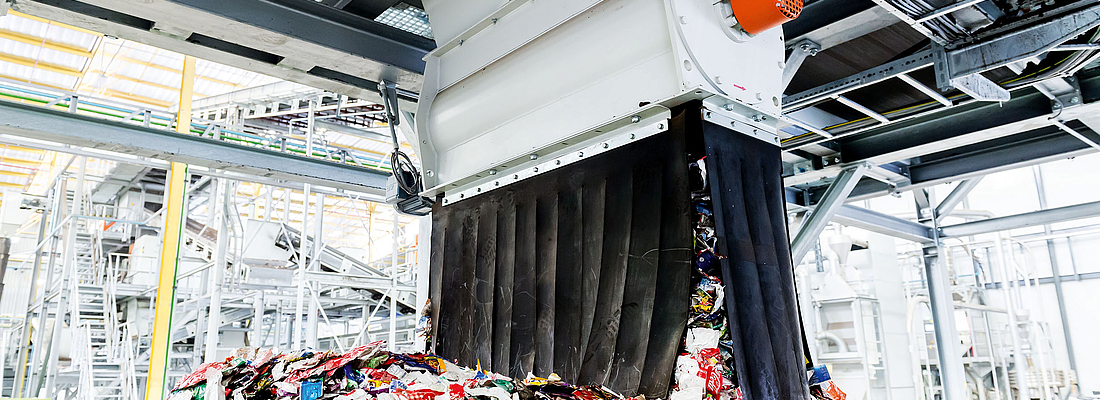
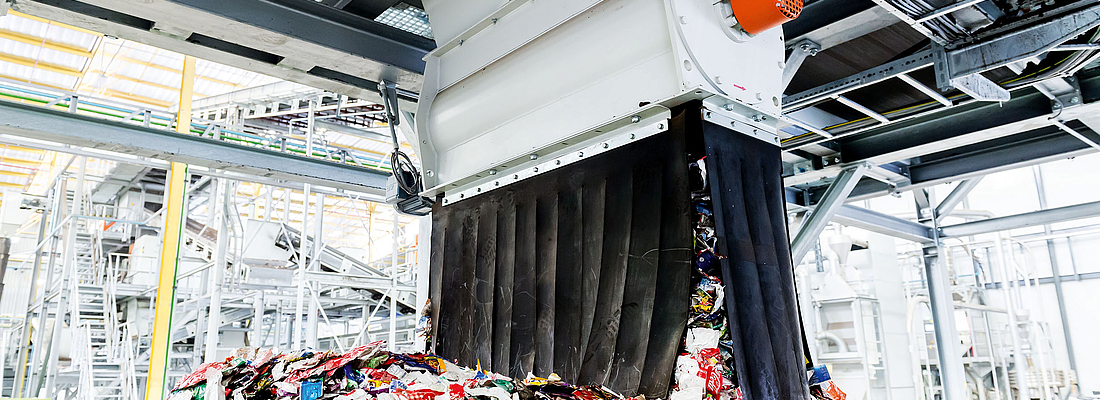
Mpact, one of the country’s leading paper and packaging producers, and its new division Mpact Polymers in late 2015 started operations with its MetaPure bottle-to-bottle PET recycling system. The plant has been designed with a capacity to process almost a quarter of the PET bottles produced by the South African beverage industry into bottle-grade PET.
In Wadeville, about 60 kilometres east of Johannesburg, Mpact has inaugurated a new line of business. The MetaPure PET recycling system is the logical continuation of the recycling operations run by this listed South African company.
According to PETCO, the national Extended Producer Responsibility Organisation for the PET sector, the demand for PET in South Africa is growing by approximately eight per cent annually. In 2015, the total South African market for PET (virgin and recycled) was approximately 210,000 tons, close to 70 percent of which was processed into PET bottles, primarily for use in the beverage industry. More than 74,000 tons of PET bottles were collected for recycling in 2015, the majority of which were processed into polyester staple fibre, or recycled into bottle- and food-grade recycled PET resin, thereby fully closing the loop in bottle-grade recycling.
With the new Krones recycling system, Mpact can now process 29,000 tons of used PET bottles into 21,000 tons of rPET raw material. The choice of location was logical: Gauteng Province, in which the new system is operating, consumes a large majority of PET containers in South Africa. The recycling of PET bottles is, of course, primarily a high-volume business, which is why the collection points are mostly concentrated in towns and large cities. Nonetheless, Mpact is aiming to increase the collection from rural areas with carefully targeted projects. This is particularly important, not least, in the context of the high unemployment rate (25 per cent) in the country, and the poor chances of being hired as a trainee here.
Stage 1: Front end
In the facility’s courtyard, the PET bottles from the collection points are delivered in bales. The material is introduced to the front end, which opens them up in a bale-breaker to distribute bottles evenly on the conveyor. The first metal removal is performed using a permanent magnet to remove ferrous metal. The next unit is a ballistic separator, which in two stages removes flat contaminants like foils from the bottles, and lighter ones like dirt, dust and glass, etc. In the de-labeller unit, the containers are now fed between two drums, which mechanically remove labels, which are then separated out and disposed of in skips. A cascade-structured near-infra-red (NIR) sorting station detects coloured PET bottles and foreign plastics, and ejects them. At the end of this cascade, only transparent and light-blue PET bottles are then passed to the downstream process. As part of a dual checking system, the NIR sorting stage is followed by a manual sorting station. At the grinders, the final station in the front end, the bottles are shredded into small flakes.
Now that only a minimised proportion of contaminants remains, the downstream washing module can operate more efficiently. “Thanks to dry removal of labels and dry grinding, the washing process has significantly lower water and energy consumption, in fact the water consumption is running at approximately 2.5 litres per kilogram of rPET, which is about 40 per cent lower than the industry’s standard figure,” explains Ronald Fairbanks.
Stage 2: Washing module
The shredded flakes are conveyed to a silo of the washing module, and then precleaned in a dry mixer and the downstream zigzag sifter, to remove light-weight fractions like dust or label residues. They come into contact with water for the first time in a pre-washer, where they are treated at moderate temperatures. Jets and mechanical friction remove any entrained dirt particles. In the downstream caustic bath, any remaining labels and adhesives are detached in a mixture of hot water and caustic. Due to the size of the system as a whole, two caustic washers are installed at Mpact Polymers. The caustic solution used is prepared in a two-stage caustic treatment system featuring the Parcival filtration system, enabling it to be subsequently re-used in consistent quality. Then, the polyolefins are removed from the flow as well, that is the material of the bottle closures. This is accomplished using a sink-float process in a density separator: the polyolefins float to the top, while the heavier PET falls to the bottom. This ensures very good flake quality. These PET flakes are then rinsed again with hot water in several stages and mechanically and thermally dried using hot air. Finally, in the washing module, any remaining residues of metals are separated. At the same time, the flakes are sorted by size using three sifters, and any flakes that are too small will be rejected.
Stage 3: Decontamination module
In this step, the sorted and washed flakes are treated to create bottle-grade recyclate. For reasons of capacity, two decontamination modules with equal outputs were installed at Mpact Polymers. Tests conducted by the Fraunhofer Institute in Germany on the MetaPure recycling system operated at Mpact Polymers have confirmed that the material produced complies with regulations covering the safety of using rPET in food-grade packaging. The FDA certification for Krones’ decontamination process also underlines its general efficacy. The decontamination modules are, for reasons of hygiene, located in a separate room with a positive air pressure. From a buffer silo, the washed flakes are first of all pre-warmed in the first heating worm, then dried in the second worm, and brought up to process temperature, which is well below PET’s melting temperature. This is followed by the heart of the decontamination module: the vacuum reactor, where migrated constituents are expelled from the materials and the intrinsic viscosity (IV value) is increased.
“Very swift decontamination”
After this treatment, food-grade PET flakes are now ready for use. It’s precisely this stage, too, that accounts for the recycling system’s relatively low energy consumption.
In the downstream extruder, the flakes are melted, extruded through a melt filter and pelletised. There, too, the energy consumption is lower in relative terms, because the flakes are already warm and dry from the decontamination process. The crystallisation of the pellets also utilises the residual heat, and does not require any additional energy input. Once the products have cooled down, they are packed in big bags, and undergo extensive and thorough quality checks.
“Quite definitely: pellets instead of flakes”
There were several reasons why Mpact opted for producing pellets instead of flakes as the end-product. “Flakes require higher capital investment for the preform production operation: the pre-dryers need to be duplicated for equal thermal treatment compared to pellets. Furthermore pellets are more compact than flakes, and mean lower transportation costs. When new technologies like recycling are introduced, of course you’re looking to avoid all possible risks. These advantages, particularly the lower logistical costs, offset the higher energy costs entailed by producing pellets,” explains John Hunt. “So quite definitely: pellets instead of flakes.” Ronald Fairbanks adds: “What’s more, rPET pellets behave better than rPET flakes when mixed with virgin PET.” The system started operating in the middle of 2015, with installation being expeditious, “because lots of the kit had been pre-assembled before being stripped down and placed into containers”, says Ronald. After only six weeks from commissioning, the first decontamination module’s OEE (overall equipment effectiveness) was at 80 per cent. “Cooperation with the Krones team was very good right from the start, both with the sales people and with the technicians, fitters and the commissioning team,” says a content Ronald Fairbanks.
Long-term thinking
Krones South Africa has invested in the staff dedicated to the recycling system, one of whom is the Lifecycle Service Manager. Ronald Fairbanks sees this as an indication of Krones’ commitment to support Mpact Polymers to ensure long-term stable operation of the new technology.
Mpact uses the pellets itself for making its own preforms or sells them to converters or directly to the beverage industry. Mpact sees an option for upsizing the recycling system in future if need be. As soon as the logistical capacities for used-PET‚ preform and pellet transportation in all of South Africa are fully utilised and the economic preconditions in place, further systems could also be set up on a decentralised basis, e.g. in Cape Town or Durban. Mpact CEO Bruce Strong explains: “The challenge at the moment is still to increase the collection quota. The prospects for further growth in this segment are positive. With partners like Krones, we can continue to prosper. Because here it’s not only the capital investment costs that are right, but the operating costs as well. And Krones’ excellent reputation speaks for itself. Krones doesn’t focus on short-term profit, but takes a long-term view. It’s precisely for that reason that Krones and Mpact’s goals are aligned.”
The comPETence center provides your organisation with a dynamic, cost effective way to promote your products and services.
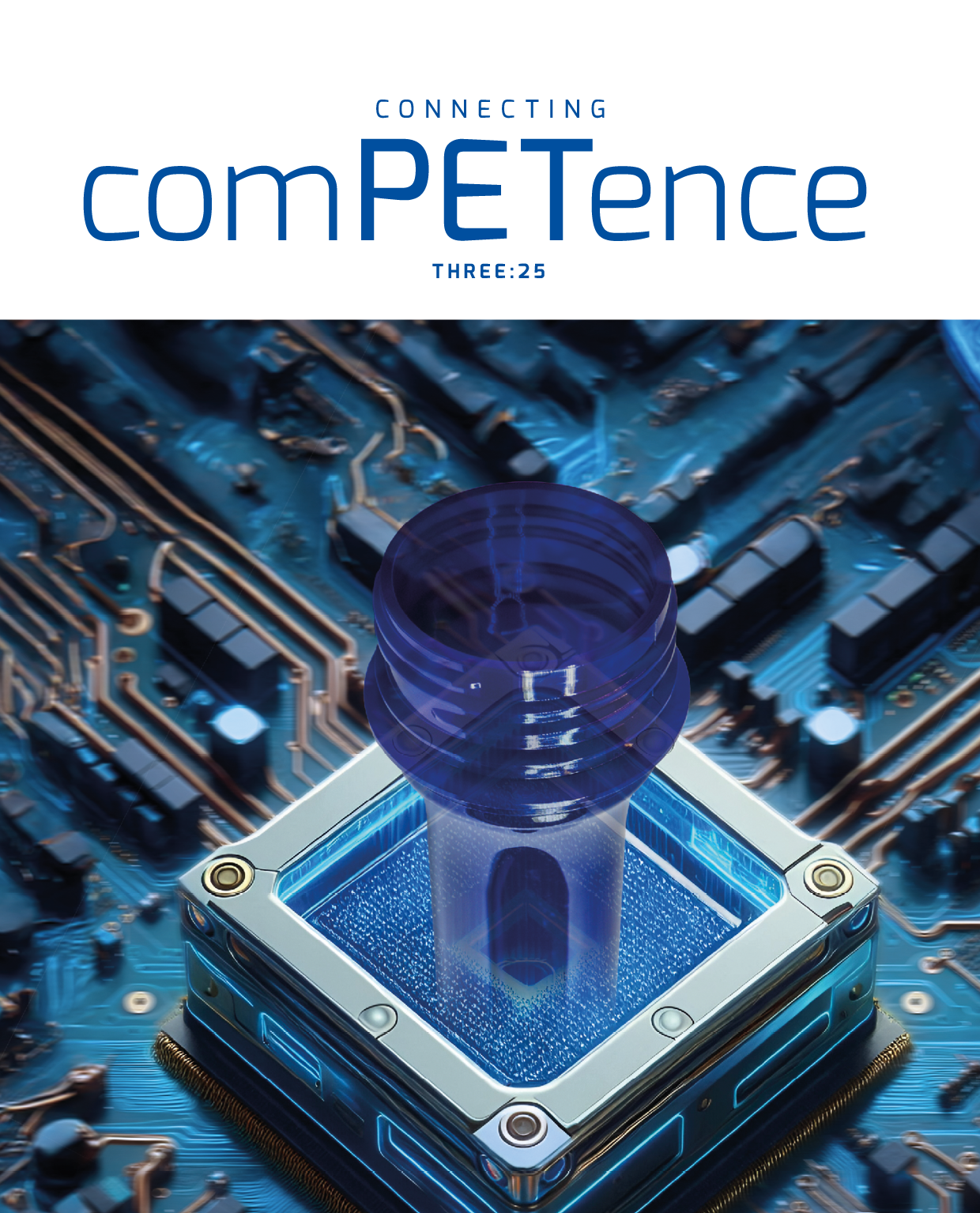
magazine
Find our premium articles, interviews, reports and more
in 3 issues in 2025.