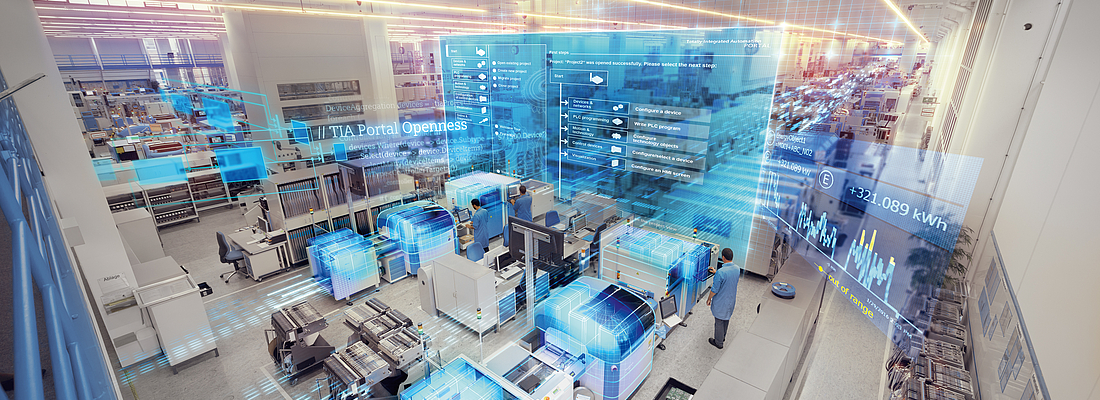
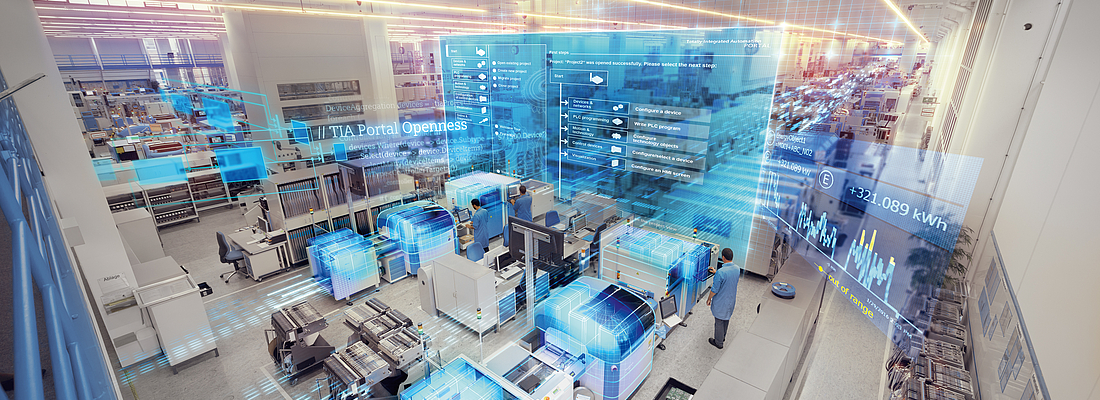
Smarter use of data and stronger integration of engineering and production value chains help utilize the benefits of digitalization
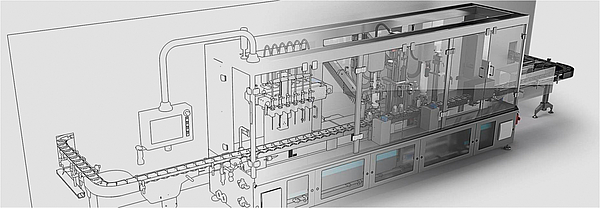
Fig 1: Integrated engineering software (“Integrated Engineering”) helps achieve a shorter time-to-market and improve workflows thanks to a consistent database
Business reports and news features from recent months show that the market for PET packaging is not just healthy but also promising: growing demand for packaged beverages and food in emerging markets is triggering investment in new packaging lines and resulting in large orders for equipment manufacturers. At the same time, however, pressure from competitors and consumers is on the rise: PET bottles and containers need to be lighter, more stable, highly customizable, and recyclable – and be able to compete on price with other packaging materials such as glass containers. Reducing materials, energy, and weight has become crucial in choosing the right packaging for food and beverages, as well as in addressing consumers’ increasing awareness of health and ecological issues. Equipment manufacturers and plant operators need to employ advanced tools and workflows to keep up with these changes and exploit the potential of digitalization.
The two key challenges
There are two key challenges in the complex market of PET production drive innovation: the need to differentiate products from the competition and to address the growing awareness for resource-efficient and cost-efficient packaging of beverages and food. Several new technologies illustrate this: Traditional labeling of PET bottles can now be replaced by direct printing, which saves paper and adhesives and allows for a highly customizable and visually appealing bottle design. As an alternative to the established shrink-wrapping of multipacks, PET bottles can now be glued together, which reduces plastic waste and makes the packs easy to carry. Glass-coated PET bottles are used to preserve taste-sensitive beverages, combining the beneficial features of glass and PET for lightweight, neutral packaging. PET packaging solutions have been recently presented for food that is traditionally packed in cans to reduce resource consumption and improve in-store product presentation with a clear can design. These general market trends pose a significant challenge for production equipment manufacturers and food and beverage companies. Production needs to be more flexible and responsive, as well as cost- and resource-efficient. Fortunately, these challenges are already being tackled with smart, integrated IT and automation solutions and new, data-driven technologies for the engineering and operation of production equipment.
Integration of data and systems
So how can digitalization help streamline processes and exploit synergies along the PET production value chain? In a recent market and technology study, Siemens identified two major application areas in which digitalization offers multiple benefits for both OEMs and plant operators: providing integrated engineering software from design through to commissioning to enable digital engineering along the entire lifecycle – often called “Integrated Engineering” – and the vertical IT integration from the sensor through to the cloud and the networking productions systems to support tasks such as condition monitoring and asset management – known as “Integrated Production”. Thanks to its integrated set of solutions, Siemens enables data exchange and consistency along the PET production lifecycle. By integrating data from production planning and concept design, mechanical design, electrical design, software development, commissioning and operation, the industry can benefit from a shorter time-to-market and consistent engineering. In addition, vertical data integration will help foster new service and operation models that will improve uptime, streamline maintenance, and facilitate production benchmarking across sites and products.
Tools for evaluating planTs, designs, and concepts
The first crucial step in production is planning the right set of systems that will help meet the demands placed on volume, efficiency, and flexibility. Digitalization supports this step by ensuring the capacity of a planned production line is perfectly aligned with the product, selecting suitable machines and the optimum layout, and providing a digital twin of the line to validate the design. Tools such as Tecnomatix Plant Simulation help verify the productivity of the layout and machinery. These tools can be used to create digital models of production systems and to run experiments and what-if scenarios without disturbing existing production systems or, when used in the planning process, long before the real production systems have been installed. Extensive analysis tools such as bottleneck analysis, statistics, and charts help evaluate different manufacturing scenarios to enable fast, reliable, and smarter decision-making during the early stages of production planning.
For OEMs, data-based workflows can help streamline the mechatronic design of production equipment and ensure that the machine concept meets the specifications of the production planner in terms of capacity, stability, and flexibility. As part of its industry software portfolio, Siemens offers the Mechatronic Concept Designer for rapid evaluation of machine concepts in a virtual environment. The software incorporates the configuration, kinematics, motion profiles, geometry, and sequence of operations into a comprehensive equipment model to assess, verify, and optimize equipment properties and performance. With new machines, this can drastically reduce the number of prototypes required and significantly speed up time-to-market. On existing machines, the Mechatronic Concept Designer can also be used to simulate and assess modifications and extensions, thus helping streamline the retrofit of production lines, introduction of new products or versions, and capacity upgrades.
As the software for evaluating the mechanic and electric design of production equipment is part of the integrated Siemens industry software suite, the same set of data and information can be used to optimize the drive and control performance of a packaging or production line. With processes designed to achieve maximum performance, the corresponding equipment is usually operating close to or at maximum productivity. Mechanical and electrical properties such as weight, durability, jitter, and torque therefore need to be optimized as one complex system. Model-based, digital optimizations can help verify that the mechanical system is aligned with the dynamic behavior of the process and supports the selection of the optimum drive solution for the task at hand. Based on the results of the design phase, the PLC, motion control, and HMI system can then be simply programmed using consistent project data.
From delivery to operation – faster
One of the most critical factors in setting up or modifying a PET production line is commissioning. Have all the components been selected and configured properly? Does the equipment work as specified? Can it be integrated into the line and production environment as planned? Answering these questions on a real machine on the production floor will cost a lot of time and money. Thanks to tools for virtual commissioning, which have already been successfully deployed in many industries, production equipment can be verified and optimized prior to commissioning and operation. To complement its tools for the design and concept phases in the equipment lifecycle, Siemens offers integrated software solutions that work with either simulated or real control systems, mirror signals in the automation solution, and exchange data with other models for more detailed testing and analysis. Libraries, templates, and macros support the creation of the simulation model, resulting in a virtual machine that can be operated in the same way as its “real” counterpart but without the risks, impact on production, and at much lower costs. Commissioning can also be carried out parallel to the production of the actual equipment, which helps shorten time-to-market. As well as the initial commissioning, simulation of control and equipment behavior can help identify bottlenecks and weak points in the process, simulate faults and failures to help optimize resources consumption and productivity, and test the correct interaction of the machine or unit with the surrounding production equipment. This results in higher productivity, throughput, and line availability. Furthermore, virtual commissioning software can also be used to train operators and service personnel in a safe and controlled environment, which also contributes to higher overall productivity.
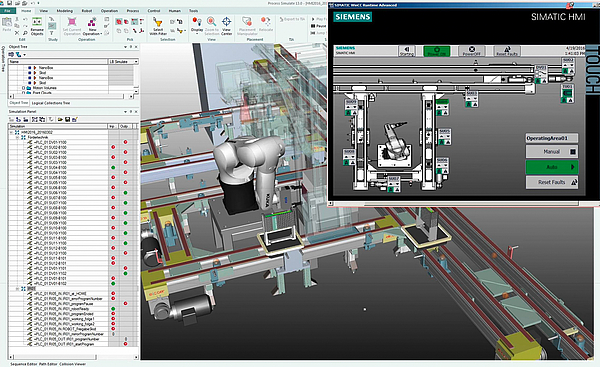
Fig 2: Advanced design and simulation tools integrate design and engineering processes, using one model and data set for design, analysis, and optimization
From industry cloud to service innovation
While the lifecycle integration of engineering and equipment data is already in use in today’s production environment, the vertical integration of production data into IT systems and data clouds remains highly controversial. It is true that vertical integration requires investment in IT and data security – however, these investments are also necessary without any cloud connection, as virtually every production line has a connection to the company network – and that means a connection to the Internet as well. Nevertheless, companies often see vertical integration as an unnecessary security and productivity risk, and fail to recognize the potential for process improvements and business opportunities, especially in industry services. OEMs can use equipment data to ensure the reliable and efficient operation of their machines and systems at the installation site – no matter where this site may be, thus saving travel expenses for servicing and supporting proactive and condition-based maintenance. The Siemens Cloud for Industry provides a secure environment for storing, retrieving, and analyzing equipment data, and on the production floor, the Connector Box enables simple and secure data connectivity in accordance with established industry standards. The OEM can acquire real-time equipment data to analyze and optimize resources and energy consumption, reduce downtime, and recommend actions for process and operational improvements as required by the equipment operator. The production data will also provide valuable feedback for the construction and engineering processes used by the OEM to improve machine or equipment designs.
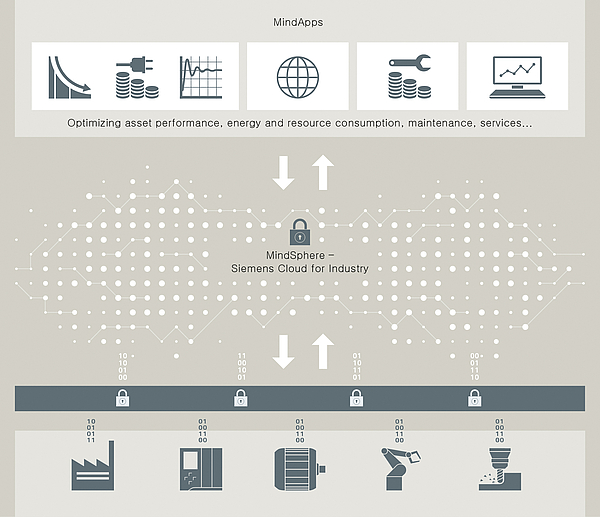
Fig 3: MindSphere Cloud for industry with open application interface for individual customer applications and completely new business models.
Aking the next step
Ultimately, data integration can form the basis for the development of new business models for equipment suppliers. Instead of shipping a piece of equipment to their customers, suppliers can provide and bill services for production, for example, uptime or resource efficiency. Alternatively, they can charge their customers for actual production services measured by media consumption or operational hours. Integration of new technologies such as virtual reality applications – today mostly limited to consumer gadgets and the gaming industry – will also provide new ways of working in an immersive environment, not only to manipulate data but also to modify processes, for example, the handling path of a packaging robot. Together with various industry partners, Siemens is involved in several pilot projects to explore the potential benefits of such applications and to turn ideas into solutions that can be efficiently and economically deployed in PET production processes – from the concept to the commissioning and operation.
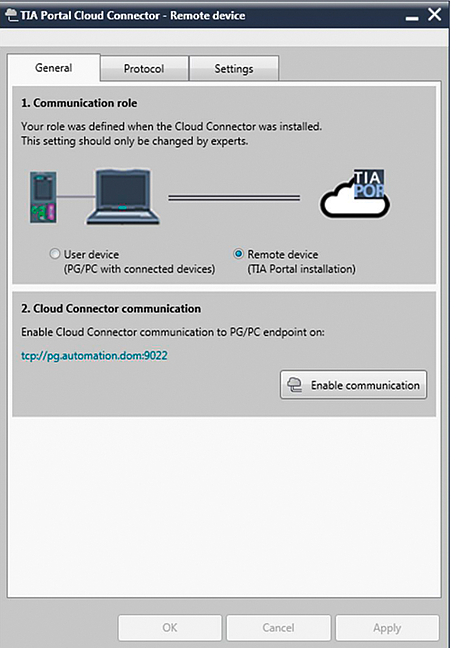
Fig 4: Plug and play connection of SIEMENS products (Engineering in the TIA Portal)
The comPETence center provides your organisation with a dynamic, cost effective way to promote your products and services.
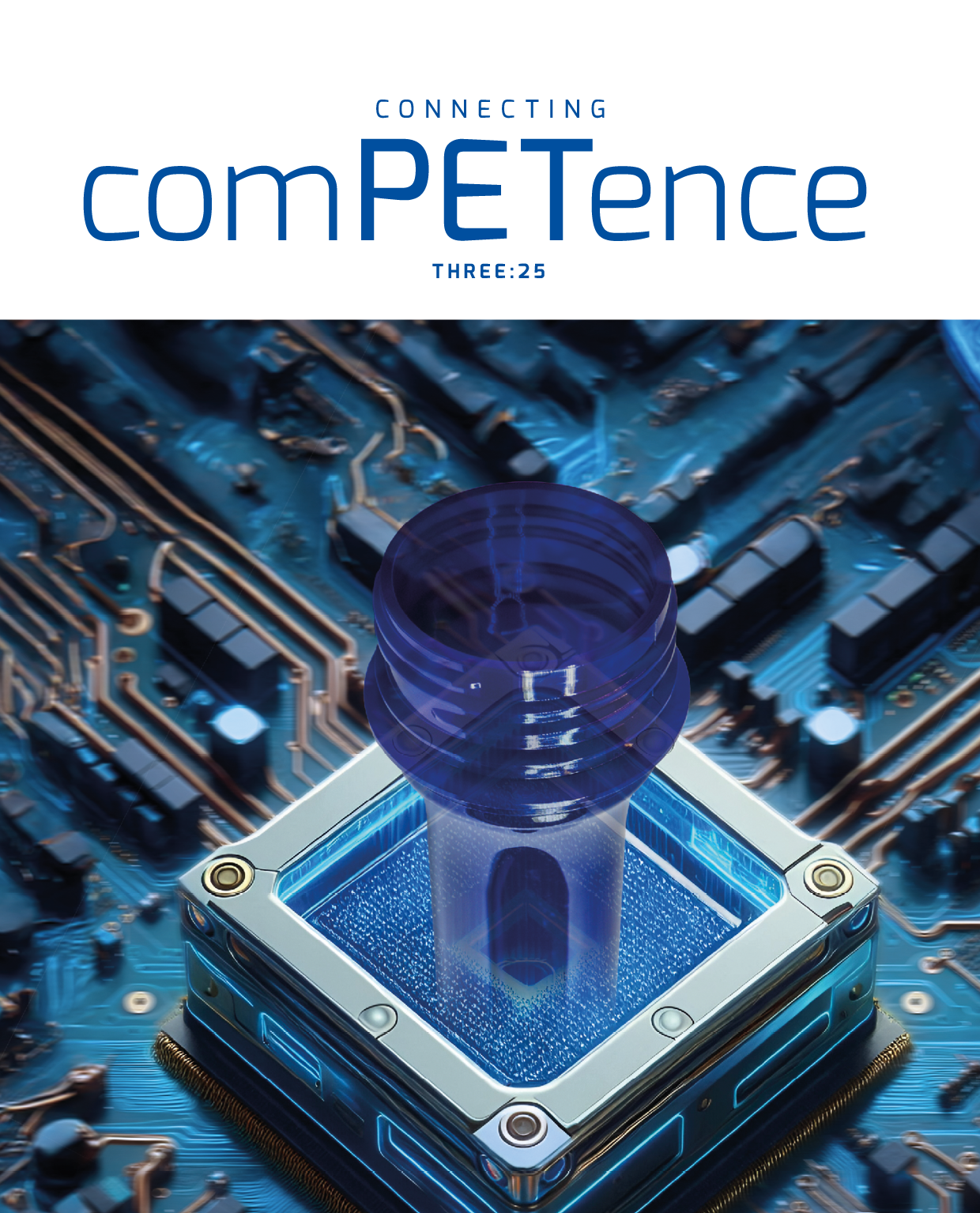
magazine
Find our premium articles, interviews, reports and more
in 3 issues in 2025.