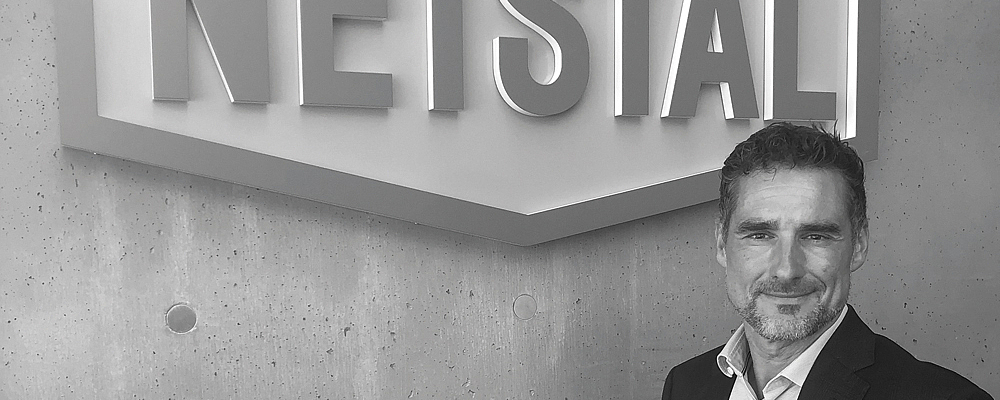
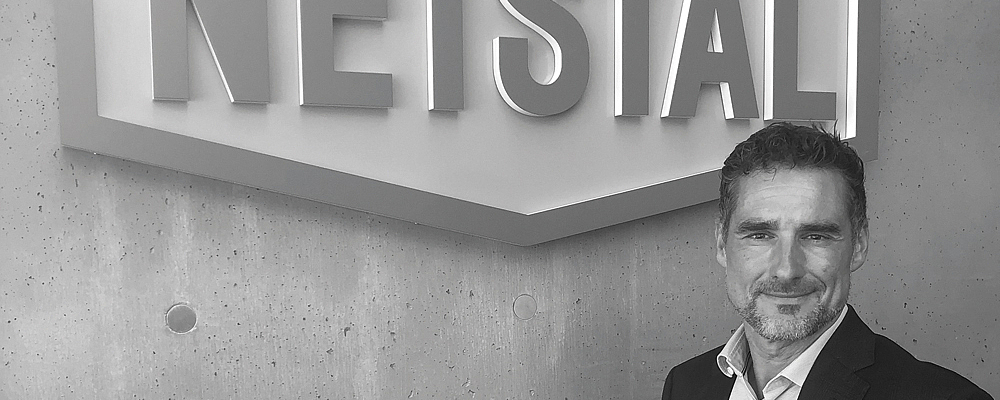
(Photo credit: NETSTAL)
Preform Business
NETSTAL: PET Preform Business: Strategy • Technology • Trust
It’s back! The NETSTAL sign is again decorating the building at the headquarters in Näfels, Switzerland. - MEETING with Renzo Davatz, Stefan Kleinfeld, Michael Birchler.
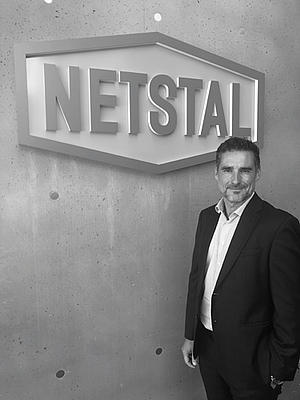
After two years, it’s back, the company nameplate. And not only that. There is also a comeback as a company: NETSTAL Maschinen AG is starting up again as an independent unit, under the umbrella of the KraussMaffei Group.
Renzo Davatz, the old and new boss of the NETSTAL team, is very happy about it and is aware of the responsibility. The term “trust” plays a major role this afternoon when we sit together with him and Stefan Kleinfeld (Product Manager PET and CAP) and Michael Birchler (Head of Marketing and Communication) in Näfels. Renzo Davatz is happy to take on responsibility - and at the same time knows about the trust that is placed in him and his team from Munich, the headquarters of the KraussMaffei Group. “NETSTAL is a promise,” he posted on social media when his colleagues posted photos of the new company sign. “Our team is highly motivated to meet the expectations of our customers more than ever before”.
Davatz explains the reasons for the change in strategy and first explains how the previous name change came about in 2019: From KraussMaffei’s point of view, the one-brand approach of the group made perfect sense, and Davatz found the implementation at the K trade fair stand very successful. He cites two reasons for the new change: On the one hand, the customer’s request was very emphatic, and on the other, KraussMaffei High Performace AG has excellent growth prospects. The medical sector with its challenging applications was in great demand during the pandemic and produced significant growth. And the second pillar, PET, is getting ready to take off with the new concept of side removal. “We want to double the PET business,” says Davatz. Against this background, KraussMaffei made the decision to give the NETSTAL brand its own organizational structure back. NETSTAL Maschinen AG is returning to Näfels, and the service organizations in the various countries are also becoming independent again.
At the same time, KraussMaffei has withdrawn entirely from the PET business. “The last two PETForm machines will be delivered at the end of 2021; then there is only the PET-LINE product portfolio,” reports Stefan Kleinfeld and emphasizes that the services will, of course, continue to be offered.
This brings us to the second topic because we are curious to see how the new PETLINE, presented in September 2020, has developed. After all, with introducing the side entry principle, NETSTAL presented a machine with a high degree of novelty. What about the risks that high levels of innovations bring with them? What happened this year? “We sell significantly more top entry machines than last year,” was his surprising answer - and he smiled. This is possibly due to the need to catch up - and customers probably want to secure what is familiar to them. “The top entry machines are and will remain an integral part of the product range as long as there is a reasonable demand.” And that currently seems to be the case.
''Our team is highly motivated to meet the expectations of our customers more than ever before.'' - Renzo Davatz
Current status of the new PET-LINE series: The machine with 4000 kN clamping force was presented with sales release in autumn 2020. The variant with 3000 kN clamping force followed in May 2021. Several machines of both types have already been sold. The next expansion will be the 5000 kN machine. “It’s a kind of upscaling the same concept,” explains Kleinfeld.
And how is business going with the new machine? “With the launch in September last year, we knew that the budget phase for 2020 was already over. So we were able to use the time to gain experience,” says Davatz, and Kleinfeld adds, “And we are fortunate that we receive valuable technical feedback from the field tests where the customers’ machines are running. That helps us a lot.“
The feedback from customers regarding the quality is also very positive. In particular, the compatibility with existing tools at the customer’s site has kept its promise. “There is a lot of confirmation that we did a lot right.” The gentlemen also rave about the measured values: In comparison, energy consumption, heating output and AA values are significantly better; the plasticization has proven suitable for 100% rPET processing. The engineers are also optimistic about the flake processing and are currently investigating the limit for the new screw. And so, the team feels perfectly prepared for the upcoming budget phase and the resulting orders. The term “trust” is used again: “We have done everything to ensure that our customers get what they order and do not have to fear disappointment.
The NETSTAL people also want to create trust through their service network - and the team attaches great importance to its quality. “We support our customers, and we help to develop and master the new operating philosophy we train. We support the change, be it from top entry to side entry or the manufacturer”, says Davatz. The company trains their service technicians, including those working in the branch offices, in Näfels. Two departments work together to achieve the optimum: the application engineering and the department.
Concerning the support for the elements that partners supply - for the tools, NETSTAL cooperates with MHT and Otto Hofstetter; for the dryers with Piovan and Eisbär - there are service levels. The goal is the single point of contact: depending on the depth of the questions, either NETSTAL people or the service of the partner companies are responsible. As a result of the pandemic, NETSTAL will make the service even more decentralized. “The fact that we had our branch offices and that our service people could travel to the customer without crossing borders helped us a lot during the pandemic.”
The pandemic did not affect the sales launch of the new PET-LINE with side entry very much, said Davatz. Due to the travel restrictions, the visits to the “exhibition stand” in the hall in Näfels could not take place as the NETSTAL team would have liked. But the customers appreciated well the digital presentations. The PETline team had several opportunities to present the machine to large teams. “Such large groups from one company, even from different locations, can only be reached virtually.” And in this way, many detailed questions could be answered and specified individually.
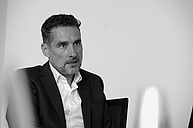
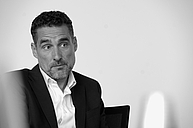
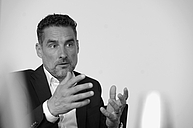
Over the months of the field tests, there was no need to make large-scale technical improvements. Davatz: “We just had a lucky hand.”
Technical quality, reliability, availability of the new PET-LINE - none of this gives the team any worries. But there is another big topic in the room, and it affects the entire market across all industries: material availability or material shortage, longer delivery times and rising prices. “What is happening is irrational,” says Davatz. Combining cumulative orders with material availability will pose challenges for the industry. “But it won’t dissuade us from our goal - to double the PET business.”
The comPETence center provides your organisation with a dynamic, cost effective way to promote your products and services.
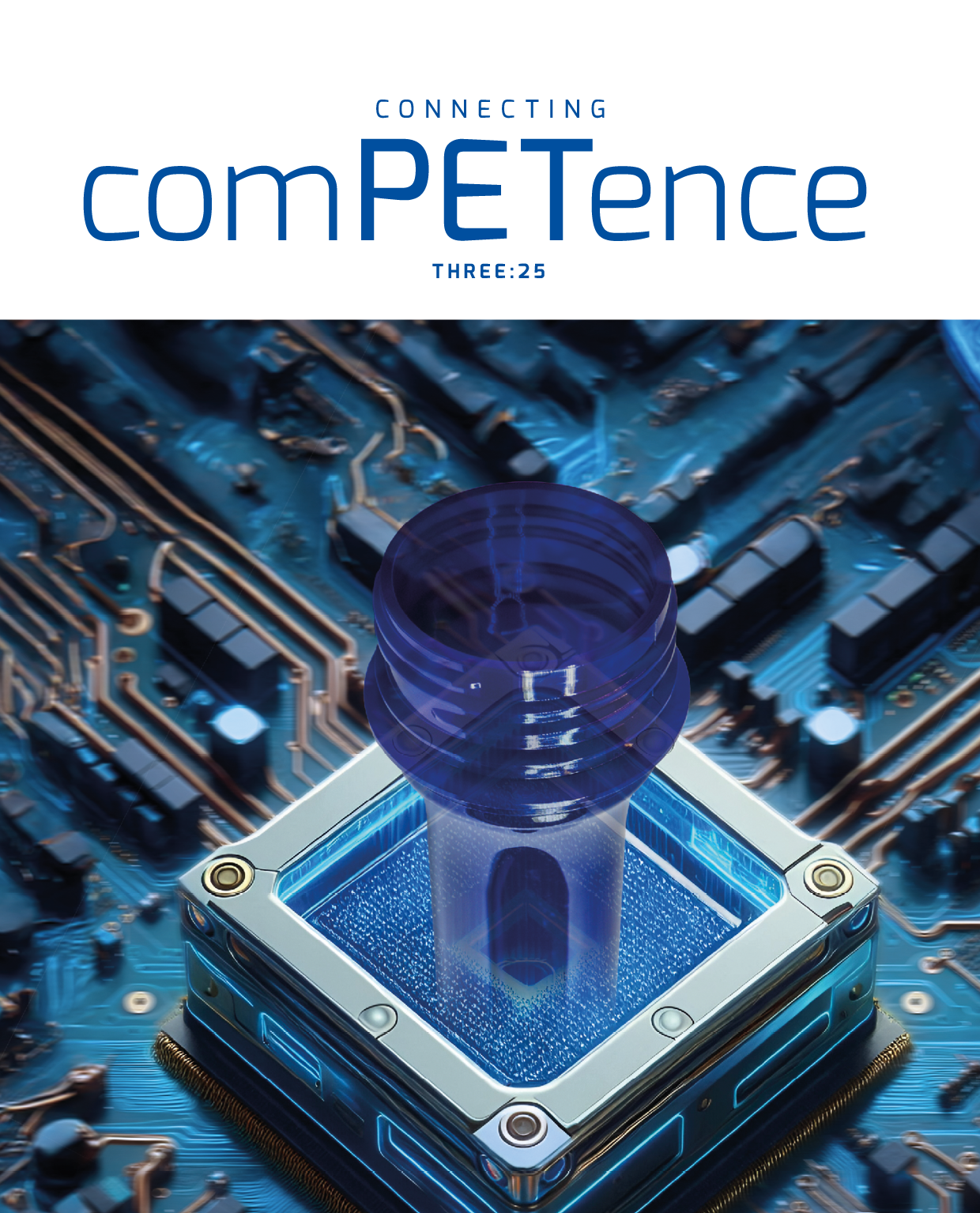
magazine
Find our premium articles, interviews, reports and more
in 3 issues in 2025.