Now as before, saving raw material is the most efficient method to clearly reduce the production costs of PET containers. However, to save material at the expense of the container’s stability has been out already for a long time, since this gives not only the bottle a cheap appearance, but the potential customer also concludes on a content of inferior value. At worst the packaging even becomes a source of irritation. This is why discounters have already drawn consequences from negative experiences and actually increased the bottle weight again. This step is underpinned not least by customer dissatisfaction with bottle properties far below the end-user’s expectations.
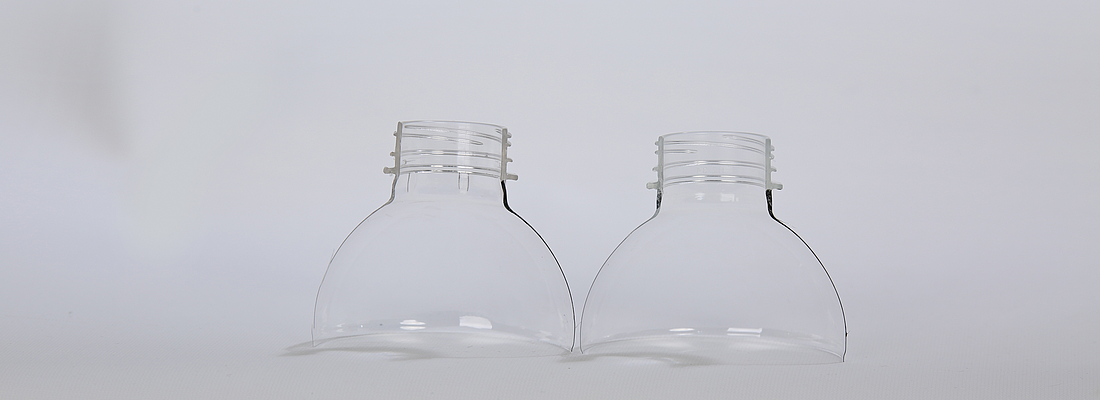
Economize on the material below the bottle neck
Mind you, PET bottles hold potential for material savings by all means. No matter whether from the discounter or established high-price beverage producers, when cutting a present-day bottle you soon discover unnecessary material in the base area and below the bottle neck which doesn’t contribute to the container’s stability. This is exactly where, especially in the case of discounter products, the material distribution on the PET bottle could be optimized towards better stability without extra material.
Technical solutions to realize this material redistribution do exist especially for the bottle’s base area and are by now implemented as initial measures. Depending on the application, technologies such as Mint-Tec permit to successfully save up to 5% PET material at the base of the bottle. At the bottle’s neck, on the other hand, one hasn’t succeeded so far to reduce the portion of unnecessary material.
Creative Packaging Solutions (CPS) and its team of developers have now coped with exactly this problem: They’ve jointly developed a new technology which allows to economize on the material below the bottle neck by reducing the wall thickness, and this without weakening this area in any way. The quality of both neck and thread is fully maintained (Fig. 1).
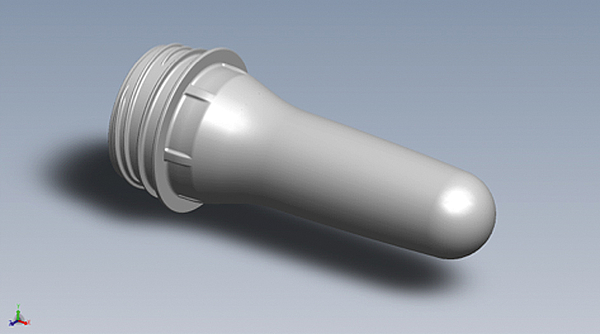
Fig. 1: Neck-Lite preform
Injection moulder’s point-of-view
From the injection moulder’s point of view a reduction of the wall section below the bottle’s neck appears at first sight to be impossible. The arguments are well known: The thinner wall would freeze too fast for a good moulding process, the neck and thread shrink in an uncontrolled manner on account of the missing hold pressure during cooling. In final consequence the bottles wouldn’t be tight any more.
The Neck-Lite technology of CPS now permits to clearly reduce the wall thickness below the bottle neck in PET bottle production and to permanently save the material in question. This is achieved by leaving 4 to 12 equispaced ridges serving as melt channels through which the hold pressure can be kept effective for the avoidance of shrinkage. By this the bottle’s neck retains its tight tolerances which guarantee the tightness of the closure (Fig. 2).
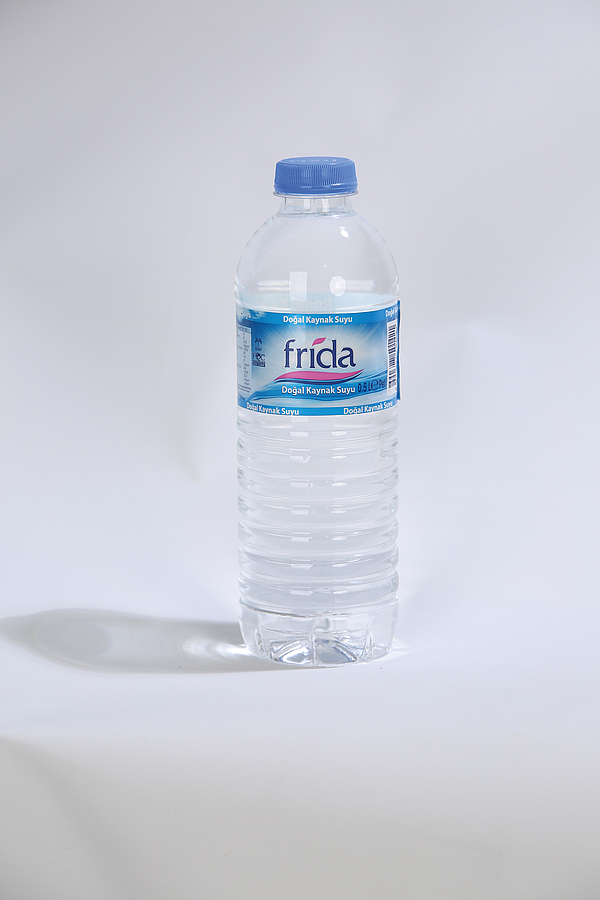
Fig. 2: PET bottle with Neck-Lite
These ridges or melt channels form a sort of window which at first glance doesn’t at all look like a weakening, but on the contrary like a brace. It suggests a strengthening of the area despite the fact that material has been removed. Apart from this, the reduced wall section supports the blowing process in that way, that reheating in the blowing machine requires less energy in the neck area. In this way we also achieve more longitudinal stretching which gives the material a considerably higher stiffness. The blowing process causes the windows resulting from the hollowing-out to resume the original outer diameter so that there are no negative effects on the subsequent handling and filling (Fig. 3).
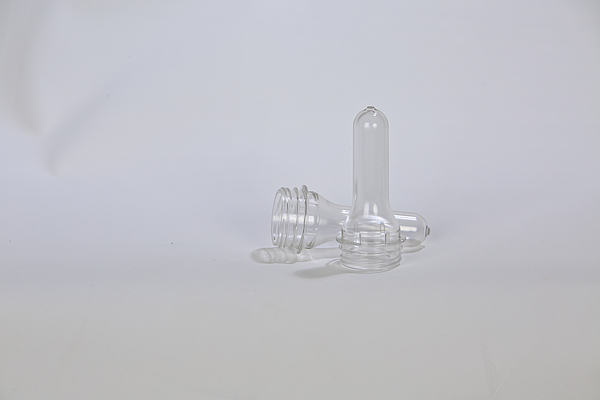
Fig. 3: Preform with Neck-Lite
For the optimal blowing process Neck-Lite brings additional advantages also as regards the need for energy: The energy consumption for IR heating in the neck area has been reduced. Material stretching in this area has been optimized as well, thus increasing the mechanical strength of the PET material significantly.
The production examples shown in Fig. 4 demonstrate the energetic advantage of a Neck-Lite preform over the standard execution in the case of a 0.5l bottle weighing 10.5g. Here, the benefit of the Neck-Lite preform is a weight saving of 0.25g, i.e. of approx. 2% of the total weight. A pleasant effect was also that, thanks to the thinner wall in the neck area, the heater setting in the IR oven could be reduced from 4.0W to 3.6W per bottle. The energy saving in this case amounts to 10% in total.
Energy savings
Assuming a typical production line with an annual output of about 500 million bottles in the above production example, the saving thanks to Neck-Lite amounts to: 125,000Kg of PET material p.a., i.e. approx. 130,000 €. From the energy point of view, one reckons with approx. 50,000KW to process (by injection moulding) the above saved material and 200,000KW for the optimized blowing process, which leads to a saving of 250,000KW in total, i.e. a further approx. 25,000 €. In addition the ecological aspect which is of even greater importance.
Neck-Lite represents a further significant step to improve the image of the PET bottle. Sensible material savings reduce not only the cost of the container, they also relieve the environment and convince the end-user. At approx. 4-5 months the return of investment (extra cost in case of new investment) is also worth looking at. Moreover, this solution can be adapted to any existing mould.
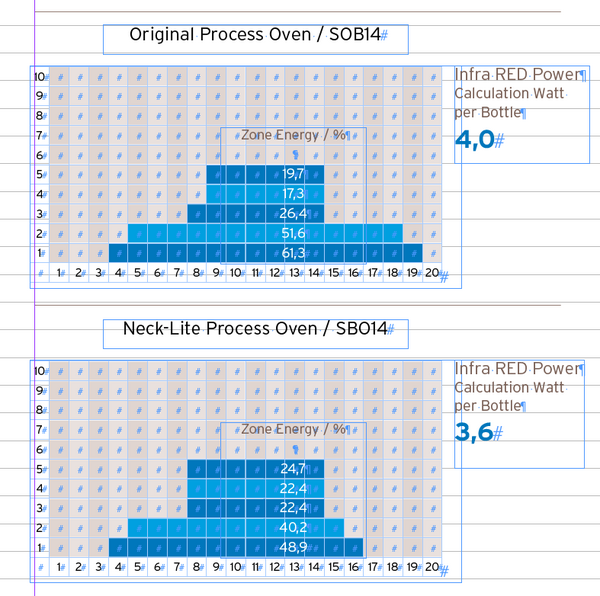
Fig. 4: Comparison of oven settings for
standard neck versus Neck-Lite
Neck-Lite with its visible braces makes for a very positive and unique appearance also from a marketing point-of-view. Not only is an increased stability suggested, but the recognition factor is also considerable. If this look is generally associated with a material saving, one can by all means highlight also the ecological aspect of these containers.
Concluding on Neck-Lite in brief, one can state that, at a reasonable cost and with an attractive return of investment of approx. 4 months, material savings can be implemented on PET bottles without deterioration of the container’s mechanical strength. This is of benefit also for the blowing process. Thanks to its good recognition factor the favourable appearance of Neck-Lite can be applied as a convincing sales aid!
The comPETence center provides your organisation with a dynamic, cost effective way to promote your products and services.
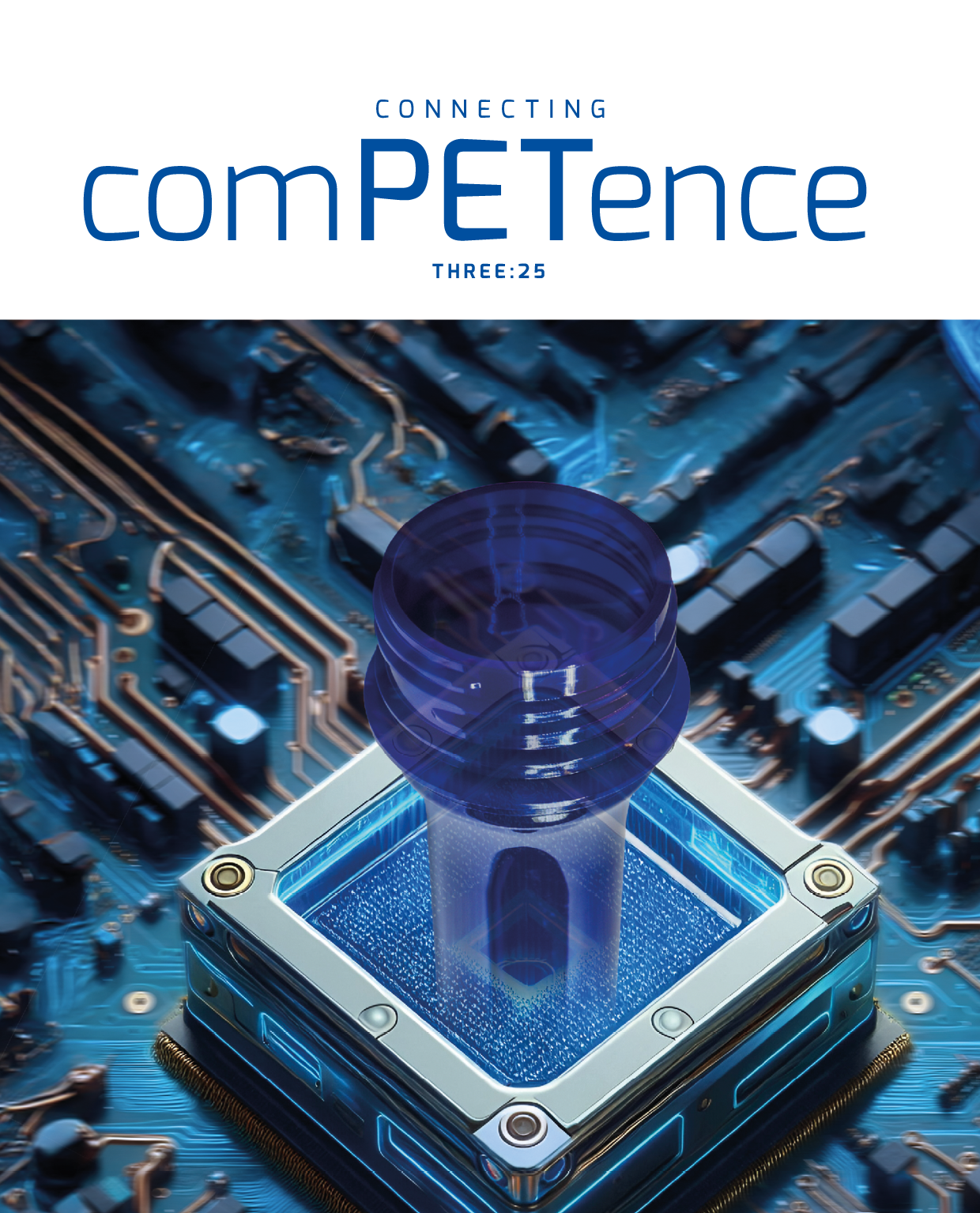
magazine
Find our premium articles, interviews, reports and more
in 3 issues in 2025.