If two or more single machines can be combined to form a block, this gives the users thereof many benefits. Shorter conveying segments and, as a result, a much smaller machine footprint speak for the compact system. In addition, there is less maintenance effort and fewer spare parts are required. Established machine technology can be blocked in many areas – in the filling and packaging and palletizing sections and in many different applications, from still water through beer to mixed milk beverages, for example.
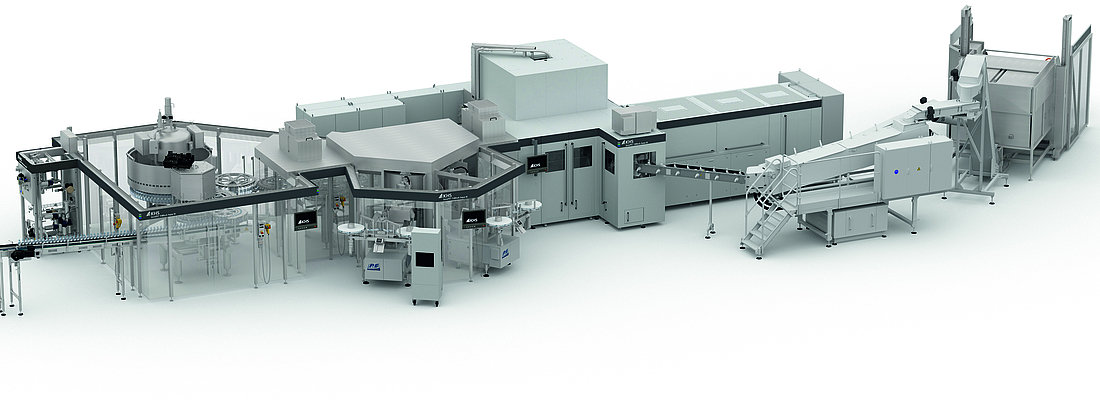
As one of the leading manufacturers of filling and packaging systems for the beverage, food and non-food industries, with its latest additions for the hygienic filling of sensitive beverages KHS has further augmented its program of blocked systems, for instance. We are carrying on a trend where KHS is itself one of the pioneers. Back in 2002 and 2004 we presented our initial plans at various international trade shows. In 2008 the KHS InnoPET BloFill stretch blow molder/filler block then went into operation; at the time this was one of the first on the market and is still a successful model today.
In 2018 the portfolio now caters for a whole range of different customer requirements. However, the systems currently available are by no means the end of the story. On the contrary: at KHS the entire blocking concept is so modular that we can offer a huge diversity of systems. Our open architecture and intelligent block interfaces enable totally different individual systems to be created quickly and easily. Unlike the standard systems frequently found KHS also supplies flexible systems like these in the medium capacity range.
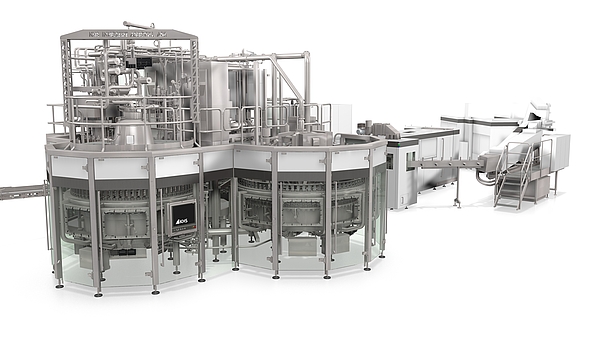
FLEXIBLE BLOCKING
The use of blocked machinery is not only prudent where the focus of the operation is on the stretch blow molder; the filling or packaging and palletizing section can also be at the center of the block setup. Modular systems in the packaging segment also have a long tradition. In principle all KHS packaging machines have been constructed in this manner for over 20 years. A tray shrink packer is also a block system in a broader sense of the word. Unlike in the USA, where we still have a tray packer and straight film packer in our portfolio which are joined by a turner or stacker, in Europe all of the components have long been merged to create a single machine. Here, the individual variants carry great weight, for in blocked systems there are many possible options for modularization. Accordingly, this means that the machinery is flexible in its configuration.
MORE THAN JUST A GROUP OF SINGLE MACHINES
Thanks to the compact block design and direct connection of two or three machines, among the most obvious advantages and synergies of such systems are the lower space requirement and omission of air conveyors – with all of the positive knock-on effects these entail. These primarily include lower acquisition costs, simple and efficient operation and less maintenance effort. As the compact machine has a smaller footprint, fewer materials are needed. Depending on the application, directly linking the individual components and introducing an intelligent drive concept and safe bottle handling make for very efficient block performance control.
Another important aspect is operation. Where several operators are usually required to man the buffer segments when moving from one machine to another, the components on a block are rarely more than one or two steps apart. This makes work very much easier for the operator and helps to prevent blind spots in line operation. These could cause the stretch blow molder to stop if there is a backup, for example, or, vice versa, that the filler halts production if no more bottles are fed onto the line. Larger screens which are networked with one another further simplify control and the increasing standardization of components and processes reduces both the time and effort needed for training and the manpower requirement.
In order that things remain simple and convenient for operators during servicing, the idea is that each block should be treated as one machine.
This ensures that all technical support, whether this be provided in the form of conversions, servicing or spare parts, comes from a single source. In a nutshell, the advantages of blocked machinery for operators are as follows: everything KHS develops regarding blocked systems lowers the total cost of ownership or TCO. After all, the intention is to facilitate the economic success of our customers. On the other hand, we also help our clients to adapt their production process to current market and consumer requirements which are increasingly affecting the packaging itself in particular.
SPECIAL CASE: ASEPTIC SYSTEMS
In some respects KHS treats the six hygienic fillers blocked with standard stretch blow molders in its portfolio differently from the classic filler block. When special hygiene requirements apply, savings in materials or personnel are less of an issue. Rather, the focus is on keeping the aseptic zone as small as possible in order to minimize the risk of microbiological contamination.
The most important classification criteria for aseptic systems are the hygiene categorization classes specified by the VDMA or German Engineering Association. A distinction is made between the following three categories for the filling of sensitive products:
I. CLASS III (ULTRACLEAN FILLING)
includes low-germ filling products such as fresh juice and slightly carbonated spritzers; depending on the product specifications also natural and drinkable yoghurt with a shelf life of fewer than 14 days.
II. CLASS IV (EXTENDED SHELF LIFE)
affects dairy products in the cold chain, such as ESL milk with a shelf life of under 28 days, natural and drinkable yoghurt, cold-filled smoothies and iced tea and fruit juices which have to be filled without the risk of recontamination.
III. CLASS V (ASEPTIC FILLING)
includes germ-free products to be filled, such as UHT milk and cream, which uncooled have a shelf life of several months, and non-carbonated water, juice beverages and near-water beverages.
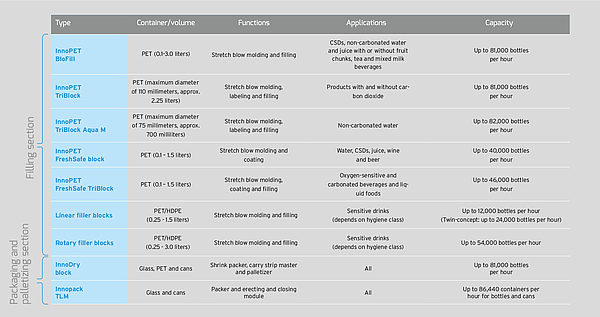
HYGIENIC LINEAR AND ROTARY FILLERS
In hygienic filling KHS thus provides suitable systems as linear or rotary filler blocks to cater for all requirements. The Innosept Asbofill ABF, a tried-and-tested linear filling system for the medium capacity range, has now been made more powerful than ever before through the introduction of three new developments. A new transfer module enables it to be blocked with a standard KHS stretch blow molder, for instance. Moreover, the modular system permits various modules to be retrofitted or replaced at a later date. Thirdly, the first chunk filler for the aseptic segment from KHS can fill bigger particles than was the case to date, thus giving beverage producers maximum flexibility when designing their products.
A new transfer module forges a basic link between the rotary stretch blow molder and the linear filler. In this development the continuous rotational motion of the stretch blow molder has been successfully converted into the linear, step-by-step cyclic movement of the filler.
Whereas the linear platform is superior to larger rotary systems when it comes to smaller batches and capacity ranges of up to 12,000 bottles per hour especially, the strengths of the latter lie in other forms of application. Using standardized modules the filler can be configured depending on which hygiene class a bottler’s products fall under and precisely tailored to suit the exact specifications of each and every customer. Adjusted to the operator’s requirements, the new KHS concept can cater for outputs ranging from 24,000 to 54,000 bottles per hour. The system offers plenty of scope as regards the bottle size, too; the combination of container volume and output capacity can be configured for 500 milliliters, 1.0 or 1.5 liters.
The modular system for bottlers of sensitive beverages provides three major advantages: firstly, thanks to the concept of modularization customers can configure their machines according to their exact requirements. This is important as oversized systems not running at full capacity often cause longer downtimes which always increase the risk of microbiological contamination. Secondly, modularization leads to standardization, which in turn means that in principle all basic and module parts can be pre-produced and stocked by KHS. The customer thus benefits from shorter delivery times. And thirdly, the modular system also generates certain cost benefits. These savings give KHS additional scope for integrating further safety systems, with which we consistently endeavor to permanently increase the standard of safety on our aseptic filling machines.
The comPETence center provides your organisation with a dynamic, cost effective way to promote your products and services.
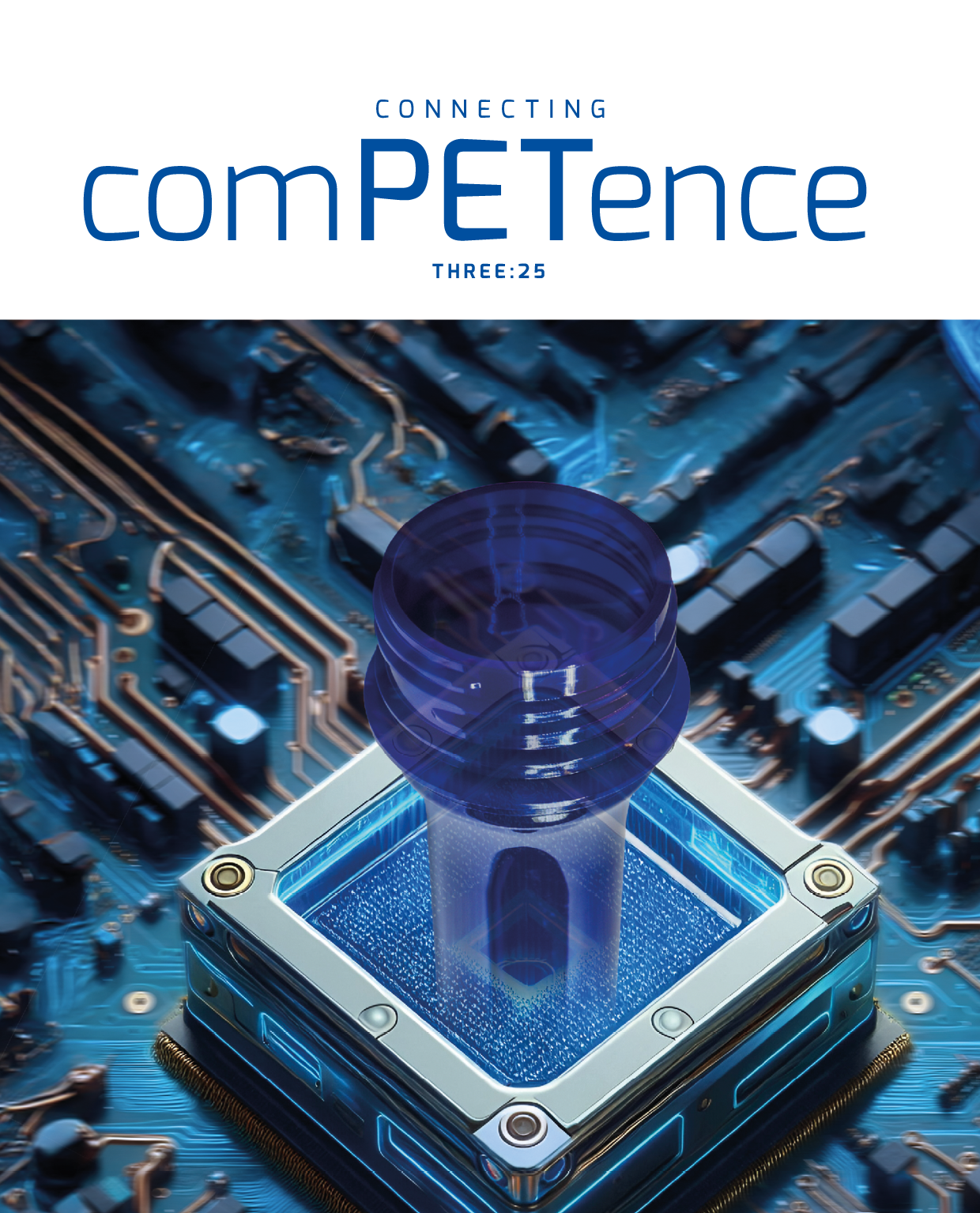
magazine
Find our premium articles, interviews, reports and more
in 3 issues in 2025.