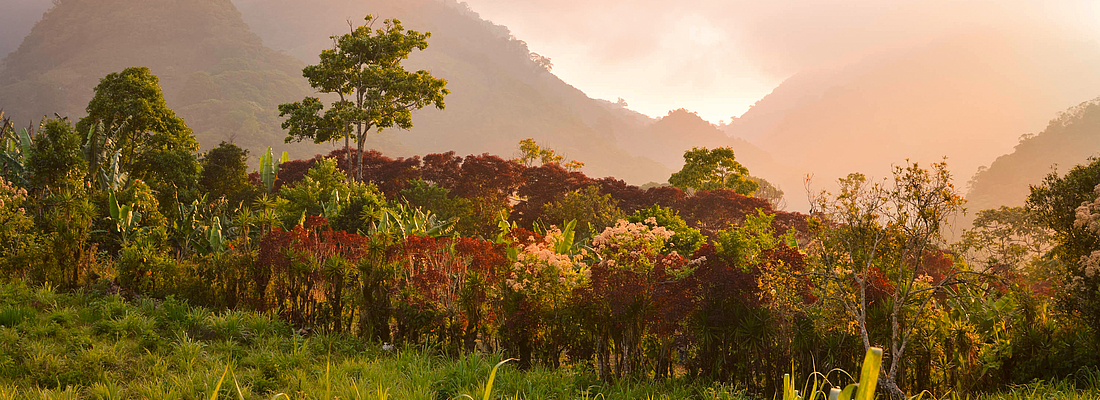
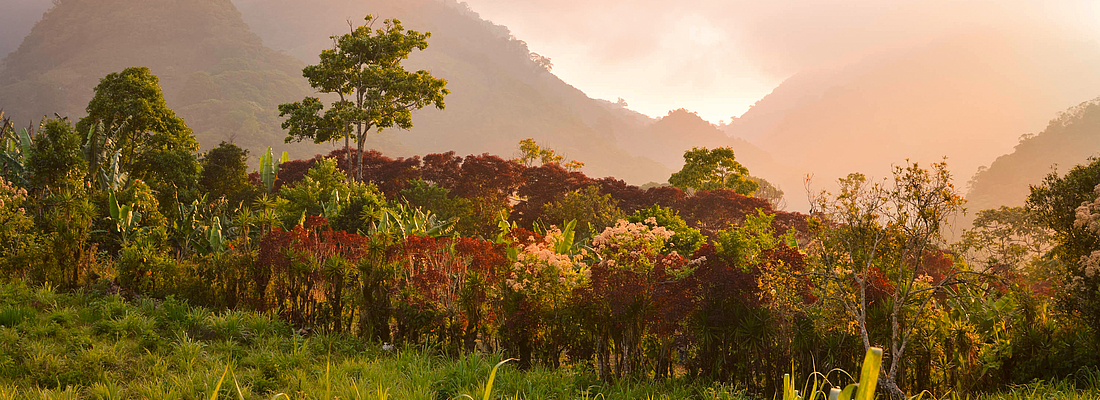
Find out how George Gatlin of the Invema Group established a collection and recycling system in Honduras to support the country and its people.
An inspiration for all: George Gatlin is quite the live wire: his story of success is just as fascinating as it is unique. Gatlin has established a new kind of recycling system in his homeland of Honduras. He is, of course, earning money from the venture but his main motivation has always been to help protect the environment and to support his poor and underprivileged compatriots. His company, the Invema Group, is headquartered in San Pedro Sula and has a second site in El Salvador. It employs 470 staff and processes 12,000 metric tons of used material, including 2,000 metric tons of PET bottles, each month.
It all began with a 21-year-old George Gatlin driving around Honduras in a small lorry in 1994 setting up collection points for aluminium cans. “I’d taken it into my head that I was going to reuse valuable waste material. I went around shops and bars asking them to keep used cans for me, which I would pay for and collect from them. When I went back the following week, no one had collected any cans because they hadn’t believed me,” he says, grinning. Fortunately, that soon changed and his career as a metal trader took off. It wasn’t long before he was dealing with other types of metal such as steel and copper, and finally also PET bottles. With great effort, an open and friendly manner, and a way of addressing the needs of the people, he’d soon established an extensive collection network with area-wide coverage, gradually establishing partnerships with a growing number of suppliers.
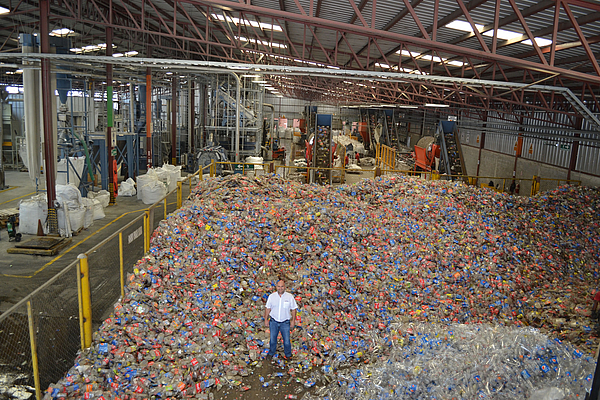
“No one believes me in the beginning ”
From zero to 84%
The collection rate for PET bottles in Honduras is now at 84%, which is significantly higher than in some western European countries. George Gatlin explains his successful strategy, saying: “Very different suppliers come to us with very different volumes but everyone is paid fairly, everyone gets a good price.” He has a total of 8,000 suppliers, from whom he buys used materials – metals and PET bottles – worth $200,000 each day. Other than a few major suppliers, his main sources are individuals, among them pensioners, single parents and disabled people. “Income levels are quite low in Honduras and collecting waste materials is a good way of boosting that income for some families,” explains the businessman, who cares deeply about the people he works with. As they collect and deliver the waste material, each supplier takes part in a bonus programme. “Our suppliers collect points, which, when they reach a certain number, they can exchange for schooling for their children, life or health insurance for the family, or even new living room furniture,” explains George Gatlin, as if it was the most natural thing for a businessman to improve the living conditions of his suppliers. “That’s how we establish trust and supplier reliability.” Because the competition never sleeps. The concept developed by George Gatlin as a lone warrior is being imitated by others, and he now has four competitors in Honduras. Despite that, the Invema Group owner is full of confidence that the company will continue to grow because he is always innovating and ready to invest, he has long-established contacts with the major buyers in the market and he is always thinking up new ideas. Which was another reason for attending this year’s K.
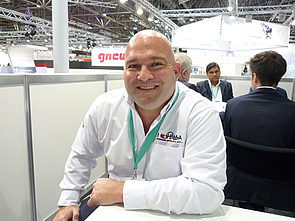
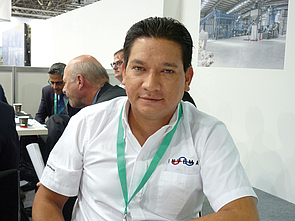
Fig. 1: Always looking to innovate – George Gatlin from Honduras and his production manager attended the K trade fair in Düsseldorf to buy new plant components for his growing company.
Fg. 2: George Gatlin is full of praise for his people in Honduras: “I’m so happy to have such well-qualified staff who always have everything under control at our enormous PET processing plant.”
Always one step ahead
Invema processes 2,000 metric tons of PET each month. “In the beginning we just crushed the PET bottles into bales and sold them on. When our competitors began to copy us, we started producing regrind, which also inspired imitators. We’ve now gone one step further and are producing regranulate with FDA approval and we’ll soon also be making film,” says the Honduran entrepreneur. He approached Coca-Cola, one of the major consumers of PET, and succeeded in acquiring them as a customer. The soft drinks manufacturer is very keen to produce the PET bottles sold in Honduras, which contain 25% regrind, using “domestic” recyclable material. “Coca-Cola is very happy with the quality of the regranulate we produce,” boasts George Gatlin. This major customer also insists on comprehensive quality control procedures and documentation, which is why Gatlin is currently setting up a laboratory equipped with all the necessary testing devices.
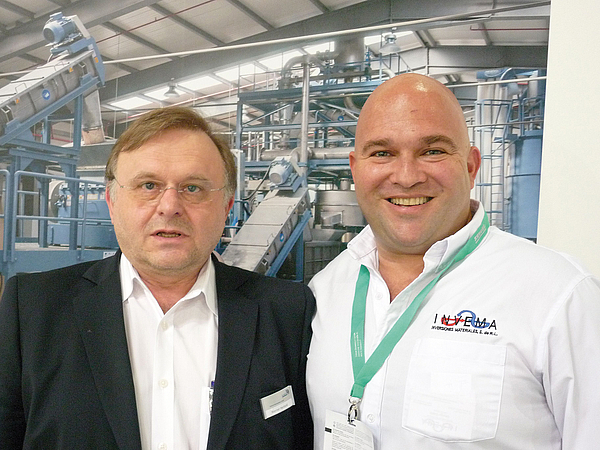
Fig. 3: Werner Herbold and George Gatlin hold one another in high esteem: “We’ve got good chemistry. The PET washing station was only paid for upon delivery, such is the trust between us.”
Hot washing for high quality regrind
Once the waste processor takes delivery of the PET bottles, they are sorted by hand according to colour and contaminant. “We are currently investing in an automated NIR sorting system. This will improve sorting quality and automate the sorting process,” says George Gatlin about another building block in his strategy of growth and quality improvement. After sorting, the bottles are shredded in two Herbold Meckesheim granulators, each of which has a capacity of 1,800 kg/h. “Invema works with wet granulators that are part of the overall washing process. The granulators are also fitted with a special force feeding system for PET bottles to guarantee a high level of efficiency,” emphasises Werner Herbold, Managing Director of the German machinery manufacturer Herbold Meckesheim. Invema is also unusual in that the company processes the whole bottle, including the cap and label. This PO fraction is separated in the downstream cold-water tank, using a swim-sink separation process and is post-washed in a hydrocyclone separation stage, before being sold on. The PET fraction is channelled into the hot washing station, where any remaining content, stickers and labels are efficiently removed. This is done at an enormous throughput capacity of 3 t/h and with automated dosing of the cleaning agent and caustic solution. “We opted for the Herbold hot washing station because it consumes less water and less power, and is cheaper to operate than our previous cold washing station,” explains George Gatlin. “Herbold was the only company that was able to meet our technical requirements and our price expectations,” says the satisfied owner of the Invema Group, who is working with very narrow margins between the purchase price for post-consumer material and the selling price for regrind. After passing through the washing station, the flakes are dried; they are then completely clean. “We are extremely happy with this technology. We’re impressed not only by the excellent performance of the hot washing station but also by how easy it is to operate – just switch it on and it runs by itself,” says George Gatlin in praise of his machine supplier.
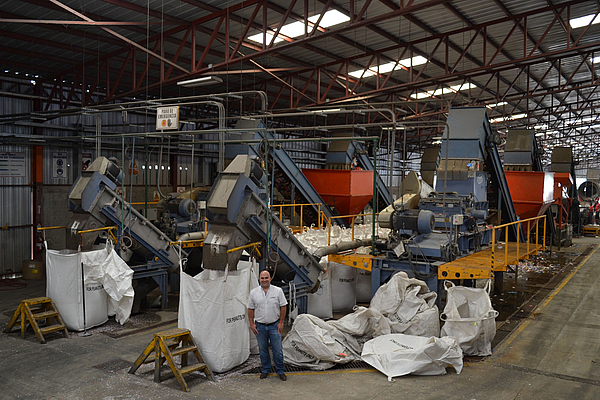
Fig. 4: The two wet granulators are part of a larger washing station and each one has a throughput capacity of 1.8 t/h. Photo: Invema
Planning for further growth
Invema sells some of the flakes directly. “Our customers value the high quality of our flakes.” The company processes the rest of the flakes into regranulate itself on a regranulation line made by the Austrian company Starlinger GmbH. This material is then sold on to companies such as Coca-Cola. “In future, we intend to produce film as well as the regranulate. This will create more added value and, of course, give us an additional competitive advantage,” reveals George Gatlin. He recently ordered an additional Starlinger recycling line with an in-line film production function for this purpose. It is scheduled for installation in March.
The Invema Group currently employs 470 people: 370 in Honduras and 100 at a second location in El Salvador. These employees handle the receipt, separation, processing and sale of a total of 12,000 metric tons of used material each month – 9,000 metric tons in Honduras and 3,000 in El Salvador. George Gatlin, ever the entrepreneur, is convinced that his company will continue to grow over the coming years. He is therefore not only investing in his suppliers and in new plant technologies for processing post-consumer material, but also in renewable energy sources. He has installed 3,640 solar panels on the roofs of his plants, enough to produce 1 megawatt of power – one third of his company’s total energy needs.
The comPETence center provides your organisation with a dynamic, cost effective way to promote your products and services.
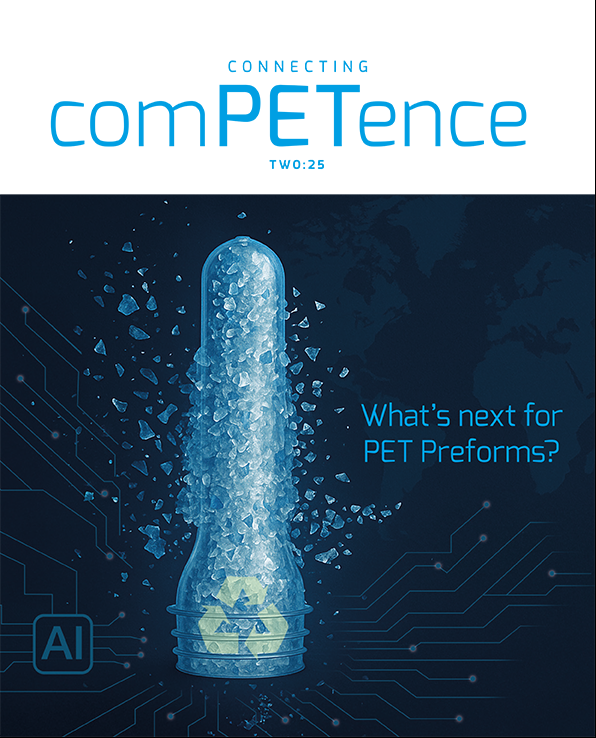
magazine
Find our premium articles, interviews, reports and more
in 3 issues in 2025.