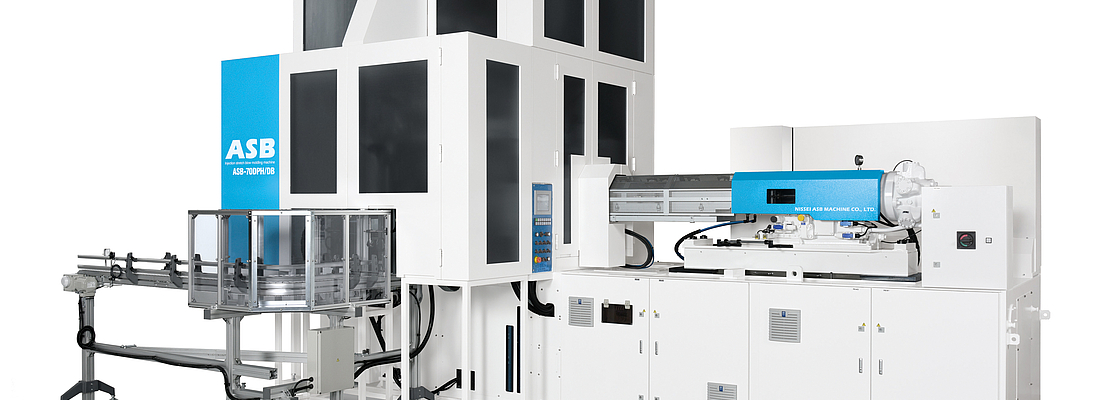
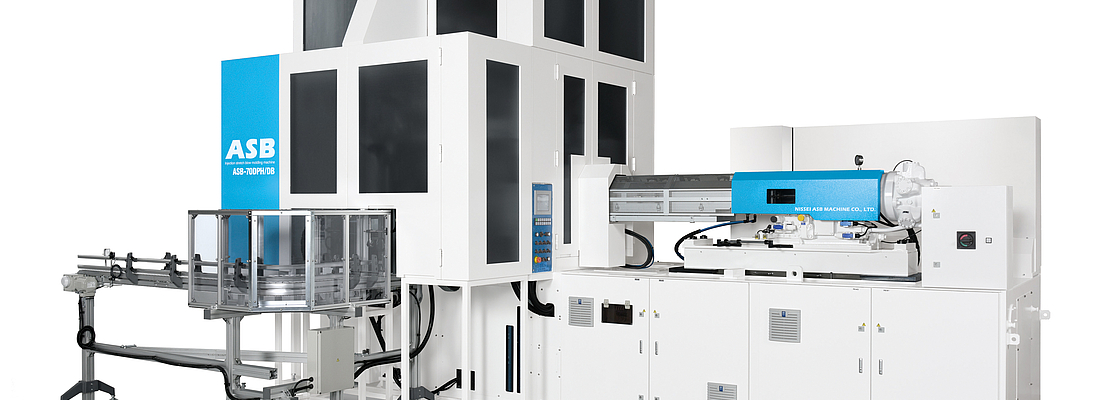
For many years Nissei ASB has been at the forefront of hot fillable PET container technology with the current state of the art being their advanced re-heat blow HSB Series.
However, recently they took a step back to re-evaluate the markets where these levels of technology are not always affordable or fully utilized, and developed the concept of incorporating the HSB Double-Blow Heat-Set process into their highly versatile mainstream product – the 4-station one-step ISBM model ASB-70DPH v4.
The resulting ASB-70DPH/DB model is a machine that has top-end heat-setting performance combined with the traditional versatility of the one-step process for diverse container designs and molding resins making it attractive in markets where hot filling represents a niche opportunity yet production flexibility is still required.
The machine made its global debut at K2016 molding a 90°C heat resistant ketchup bottle that attracted strong interest and even as this article went to press, the first Double-Blow version of the hugely popular ASB-12M small scale production model was being exhibited at Plastivision 2017 in India. With the positive feedback that has already been received, expectations are high, and plans are already afoot within ASB Group to expand development to other ASB-Series models.
What is a “Hot Fillable PET Container”
In the standard stretch blow molding process, PET chain molecules in the body of the finished container contain stress because they have been stretched at a temperature which is much lower than the melting point. This locked-in stress is what gives the PET bottle its very high physical properties, but it also means that the container will continue to shrink for the first 72 hours after molding and will suffer severe and uncontrolled shrinkage if subsequently heated within 5-10°C of the Tg of PET.
Hot filling temperature ranges are open to many interpretations but temperatures up to around PET’s Tg are often referred to as “semi-hot fill”. But, this may also be influenced by the viscosity of the filled contents and cooling conditions after filling that affect the total heat load on the container.
Once above the Tg, required heat resistance depends on the individual food including its viscosity, the line environment, filling temperature, dwell time and rate of cooling as they all impact the total heat load experienced by the container.
Additionally, a number of food types such as pickled vegetables may be pasteurized after filling and capping which places a different set of demands on the container.
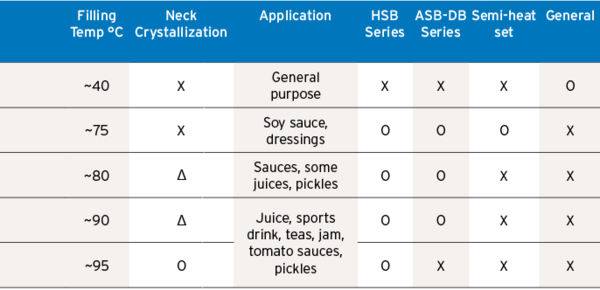
Table 1: Neck Crystallization - O - Required, ? - Depends on container and food specification, X - Not required
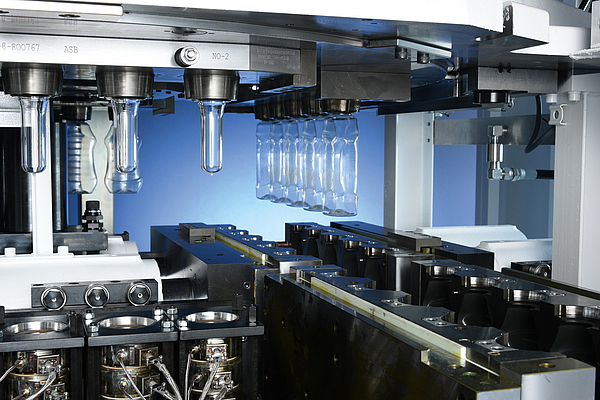
Fig. 1: Two sets of blow molds clearly identify this as an ASB-70DPH/DB
The Double Blow Molding Process
1.Preform temperature prior to blowing is similar to standard stretch blow molding.
2.Stretch-blowing into the 20% oversized primary mold that is heated to around 180°C and where crystal growth is initiated.
3.After depressurization, the container is allowed to shrink far enough to enter the secondary mold as stress is relieved and crystal growth continues.
4.Final shaping is performed in the secondary mold with virtually no additional stretching. The container is heat-set at around 120°C and blow air is circulated to provide cooling.
5.The finished container is hot fillable at up to 90°C (ASB Series) or higher if neck crystallizing is added.

Fig. 2: The double blow molding process
Double Blow vs Single Blow
-Performing the Double-Blow process provides several advantages over other heat setting methods;
-Immediate filling temperature limit tends to be higher for a similar specification container.
-Higher crystallinity means the container is better able to resist absorption of moisture that lowers the performance of all heat-set containers. As a result the storage life of empty containers is extended for seasonally filled products.
-Greater stiffness in the body allowing lighter weight for a given performance.
-Up to 30% increase in gas barrier over a standard bottle provided by high crystallinity.
-Stress relieved material suffers less shrinkage effects after hot filling also allowing lighter weight.
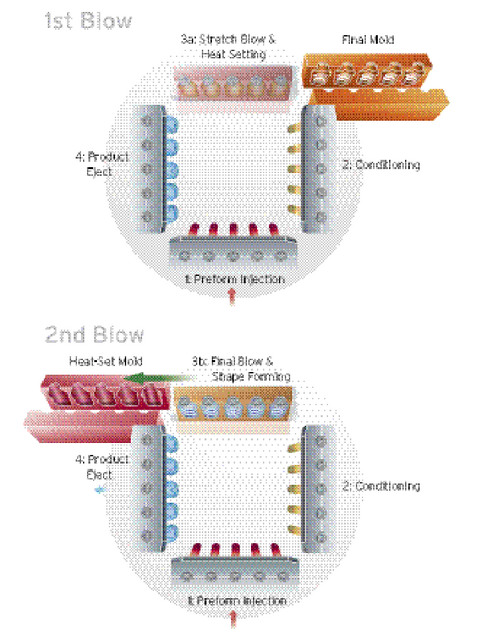
Fig. 3: Schematic of the One-Step Double-Blow Process
Necks & Caps
Since preforms in the one-step process come direct from the injection station, there is no opportunity for neck crystallization before blowing, however a majority of containers can achieve adequate performance just by slight thickening of the amorphous neck section. Even in ASB’s well established two-step process utilizing the PM & HSB Series with the CM Series preform neck crystallizer, the neck crystallizing step may be omitted due to the market or converter requirements.
For severe cases where a crystallized neck is essential, ASB is already pursuing development of a suitable post molding neck crystallizer as an add-on for the one-step molding approach.
For hot fillable containers with a neck diameter of 38mm or less, heat-resistant caps are readily available and may be used in combination with a non-crystallized, thicker neck section of the bottle.
Once the neck diameter goes over 38mm, either crystallization becomes necessary or specific caps such as the hybrid metal / plastic type will be required that are readily available in sizes up to 82 mm.
For post-fill pasteurization, neck crystallization will generally be necessary and if the filler wishes to use a GPI standard steel cap in a project that is a replacement of a glass container, then neck crystallization is a must as these caps exert point contact on the neck that will surely cause deformation on a heated amorphous neck.
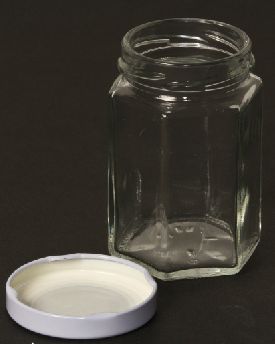
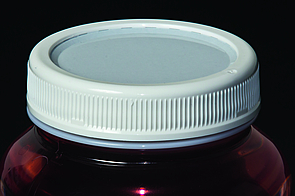
Fig. 4: a) GPI Standard Lug Type Cap; b) Hybrid Cap with Metal Top & Plastic Thread
Head Space & Vacuum Absorption
Liquid products and particularly the air in the headspace will shrink with cooling to an extent that a 500ml bottle filled at 90°C, then cooled to 20°C will undergo approx. 15cm3 of volume reduction. Minimizing the headspace reduces this effect to a large extent, but some form of vacuum absorption design (structure) is always required to prevent deformation caused by external air pressure.
I. Panel Vacuum Design
Panels are placed on the body at even intervals formed by inserts in the blow mold. This design is commonly used in beverage and liquid soup containers. It allows a lighter bottle because high strength is not required in the body.
II. Bottom Vacuum Design
By allowing the base to flex, panels are not required in the body, however horizontal ribs may be required depending on the weight and total heat load.
III. High Weight
It is difficult for the designs mentioned above to be included in small containers. Therefore a suitable weight specification will be required.
IV. Oval Container
Oval shapes such as ketchup containers perform better than expected in absorbing vacuum because a slight reduction in minor diameter results in a large volume change that is virtually unnoticeable.
All heat-resistant containers will suffer some measurable level of deformation by vacuum after filling but with good design and processing, the visual quality remains unchanged
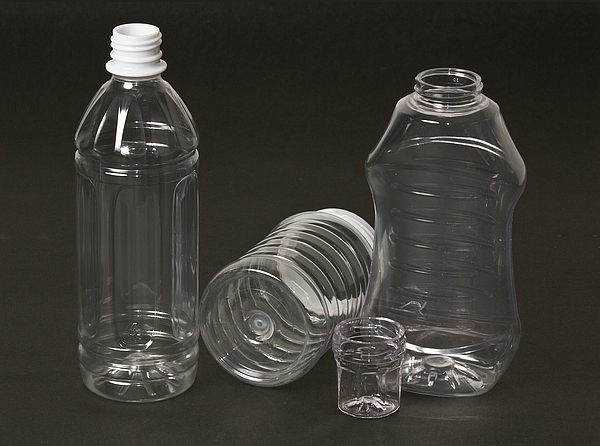
Fig. 5: Left to Right: Panel, Bottom, High Weight, Oval
Market Opportunities of One-Step
Hot-Fillable Containers
While glass replacement is the most obvious market, there is also significant opportunity to replace other plastics such as multilayer extrusion blow molded jars and bottles in HDPE and PP enabling easier recycling and improved aesthetics.
Food and drinks such as juices, tea, coffee beverages, sauces, ketchup, rice wines, vinegar, marmalade and cooked and pickled vegetables are all candidates for hot-filling. While it is true that some of these products are already in unmodified PET, in many global markets this is only possible where there is still wide scale use of additives and preservatives to maintain the food quality.
Typically as a region becomes more affluent, its consumer base become more health conscious and ASB sees an ongoing demand to move away from dependence on preservatives as a positive business opportunity. Some food companies also see this as a marketing tool to promote their healthy food products and additionally, by using high heat-resistant molding, the containers can be lighter and the food expiry date can be extended.
Of course, aseptic filling is always going to be the process of choice for highly developed beverage markets with very high production volumes, but despite its lowered entry costs over the last few years, aseptic still remains daunting in terms of investment, operation costs and training for many developing and specialized markets.
It is these speciality markets where one-step injection stretch molding has always thrived since it was originally conceived nearly 40 years ago, and if ASB has it calculations correct, the new molding solution that the ASB-70DPH/DB has brought to the market could well be the next “hot” chapter in its unfolding story.
The comPETence center provides your organisation with a dynamic, cost effective way to promote your products and services.
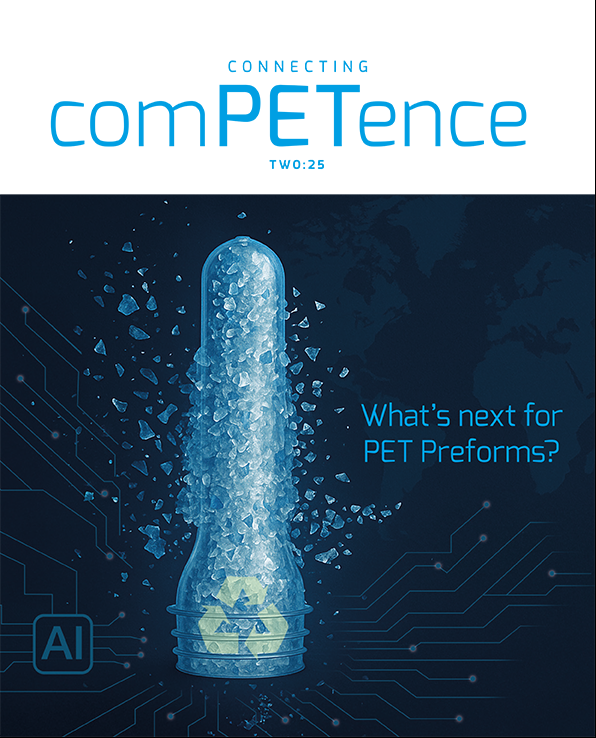
magazine
Find our premium articles, interviews, reports and more
in 3 issues in 2025.