Starlinger recycling technology is a division of Starlinger & Co. Ges.m.b.H., the market leader in PP woven bag machinery. Since the product launch of the first PET recycling line in 2003 the Austrian company has established itself as a high-tech supplier of recycling equipment for bottle-to-bottle recycling and high-viscosity applications. Its SSP technology, based on the Starlinger iV+ process (recoSTAR SSP 1800, viscoSTAR 75 and 120), reduces the AA content in pellets and ensures thorough decontamination (including additives such as oxygen scavengers) as well as a substantial IV increase.
Flexibility and user-friendliness are paramount to Starlinger when it comes to new developments. The latest technological achievements comprise capacity increase, energy saving measures, and easy adaptability to customer material. In addition, Starlinger has been granted food contact approvals by various countries and brand owners.
recoSTAR PET iV+: System overview
The recycling process consists of two main steps: the continuous extrusion process (recoSTAR PET) and the semi-continuous solid-stating of the produced pellets for IV increase and food contact suitability. For the solid-stating process Starlinger’s iV+ system with recoSTAR SSP 1800 or viscoSTAR 75/viscoSTAR 120 is used.
Process description:
The pre-cut or ground material is fed from the pre-drying unit directly into the extruder which uses the heat from the drying process. Volatile contaminants as well as monomers are extracted in a high-vacuum degassing unit. Solid contaminants are filtered out with a double-piston back-flushing screen changer (DPB) before pelletising.
After the pelletising operation the regranulate is transported immediately into a crystalliser which also uses the residual heat from the still warm granulates. Then the granulate is conveyed into the pre-heater on top of the SSP reactor for further heating. After reaching reaction temperature, approximately three batches per hour are discharged into the reactor vessel.
The pellets remain in the reactor vessel under heat and vacuum conditions for a set reaction time. The two factors temperature and time allow the relinking of the molecular chains: Polycondensation takes place. The required IV increase is controlled solely by means of the adjustable residence time – no additives are required. After the set residence time has elapsed, the pellets are discharged batch by batch into the optional cooling chamber and cooled down under controlled conditions to improve colour values.
Quality of the recycled material:
The melting point, crystallinity and flow characteristics of the output material are the same as those of virgin material. The recycled granulate is suitable for products with food-contact and has an AA level of less than 1 ppm. The IV can be adjusted according to the intended application of the recycled material (e.g. for strapping bands, the IV value is around 0.96 dl/g). Per hour residence time an IV increase of about 0.01 – 0.02 dl/g can be achieved.
Features:
The whole system is continuous and works according to the FIFO (first-in, first-out) principle with a defined residence time. This ensures that every particle receives the same treatment and thus is completely safe for food-contact. It also guarantees continuous IV increase and allows changing the residence time to adjust the IV.
Because of its modularity, the machine system is completely flexible and can be adapted immediately to market changes which occur constantly due to e.g. varying input material or altering requirements of R-PET users. If, e.g., a longer residence time is required, either an additional SSP reactor can be added to the installation for maintaining the same output capacity, or the amorphous pellets are redirected into a silo for storage and are solid-stated later or sold for e.g. sheet application.
Available machine sizes
The recoSTAR PET (HC) and recoSTAR basicPET series are available in five different extruder sizes and cover an output range of 180 – 2 000 kg/h. The capacity of the individual SSP units is 250 kg/h or 1200 kg/h, depending on the respective residence time. Higher capacities can be reached by means of parallel arranged additional units.
Country and brand owner approvals
Already one year after starting the planning and construction of the first SSP reactor, Starlinger obtained a letter of non-objection from the US Food and Drug Administration FDA. Although not valid worldwide, it clearly indicates that Starlinger machines reach a high level of decontamination. In November 2007 the FDA has issued a second letter of nonobjection stating that R-PET produced on a recoSTAR PET iV+ is suitable also for hot-fill applications.
Of course also a variety of national approvals have been achieved, e.g. from Austria, Germany or Australia (via customers). Other national approvals are pending or being filed by customers (e.g. France, Finland). For approval in the European Union, all necessary challenge tests have already been completed to supply the required decontamination data to EFSA. This is especially important for European customers as the approval procedure for them is simplified when they can use the approval granted to Starlinger instead of having to carry out challenge tests themselves.
One of Starlinger’s highest priorities is achieving brand-owner approvals. In order to protect their brand, those (usually) global players have especially stringent requirements concerning repeatable high decontamination results in recycling processes. Every single flake must meet the prescribed process parameters in order to pass through the system. The proven recoSTAR first-in first-out philosophy has satisfied the requirements of two major brand-owners, one of them being PepsiCo. Also other brand-owners are highly interested in allowing the use of R-PET for their food-contact products and are in close contact with Starlinger recycling technology regarding this matter.
PepsiCo approves recoSTAR PET iV+:
The Starlinger PET recycling line recoSTAR PET iV+ (with recoSTAR SSP or viscoSTAR) has received approval from PepsiCo by means of a customer audit.
The Commercial Approval Letter states that up to 50% of the granulate used for the production of CSD and hot-fill bottles with direct food contact may be produced on a recoSTAR PET iV+ with accordingly defined parameters. The approval is based on the second letter of non-objection issued by the FDA (extended to include hot fill applications), granted to Starlinger in October 2007.
One, but not the only, important criteria for obtaining the approval was the excellent decontamination capability of Starlinger's recycling and solid state polycondensation technology, which has been verified during the challenge test for the FDA approval.
The Starlinger recoSTAR PET iV+ also meets two other assessment criteria in the audit: quality management and automation. The line is equipped with a “food grade” button and automatically switches over to non-food grade process mode when a parameter fails. As soon as all parameters are met again and, consequently, the regranulate produced fulfils all decontamination requirements, the line switches back to food grade process mode.
Although the approval is recognised worldwide, each recycling company must undergo the PepsiCo audit process itself.
Latest technological developments
Capacity increase:
Higher production costs, e.g. due to increasing energy costs, make it even more important that production systems have high output capacities and at the same time are still costeffective. Starlinger thus has further enhanced its proven system and now introduces five PET extruders with optional HC (High Capacity) design: With the same extruder diameter, output can be raised by up to 30 % with only a minor increase in costs.
IV increase
IV increase depends on a variety of factors such as the IV value of the granulate at the start of the process, the quantity and type of contaminants, etc. Nevertheless, Starlinger has been able to speed up the solid stating process and thus the IV increase with a special version of the SSP unit. Either the possible IV increase during a specified amount of time is higher, or the residence time of the granulate becomes shorter.
Energy saving:
Due to the increased production capacity, production output is higher while the installed kW remain almost the same. This means less kW consumption/kg, which in turn results in cost savings. In addition, many components are designed to work with cooled water; thus, no chiller is required. Also, excess energy from the previous process step is preserved and used in the next step: For inline crystallisation after the pelletising process, for example, the residual heat of the pellets is used, which leads to a reduction of the energy consumption by 0.05 kW/kg.
User-friendliness and easy maintenance:
The extrusion unit and the SSP reactors feature a special easy-to-maintain vacuum pump system that does not require fresh water. The system is equipped with a central greasing unit and a central water distributor. Consequently, there is almost no waste water to dispose of and the whole equipment is more environmentally friendly.
During pre-drying automatic filters are used for dedusting flakes from washing lines, which in turn results in easy maintenance and longer maintenance intervals.
Adaptation to customer material:
Input material changes constantly due to new resins and additives. The equipment can be adjusted accordingly: The modular system facilitates adaptation to customer requirements and allows upgrading of existing lines by exchanging or adding individual components.
Also the process parameters such as process temperature and residence time (to reduce yellowing caused e.g. by AA blockers) can be specified according to customer needs.
The recoSTAR PET line can be optionally equipped with a desiccant air dryer for predrying – it has proven especially useful for removing contaminants which are integrated in the resin structure (e.g. AA blockers). These contaminants are filtered out by means of condensate separators. Optionally a hot-air drying system can be supplied for higher output capacities or for flakes with higher moisture content.
Applications, countries, references
Although only on the market since 2003, Starlinger PET recycling lines are used in many fields of application and many countries by now. A total extrusion and solid-stating capacity of more than 50 000 t per year for bottle-grade R-PET was installed in 2007 alone. Starlinger PET recycling lines are also used for producing food-grade regranulate for PET sheet production and for in-house recycling of preforms. A modified version – the recoSTAR basicPET iV+, of which several lines have already been installed – is used for recycling PET strapping bands, fibres and non-wovens.
The majority of the lines are installed in Western and Central/Eastern European countries, but also in Australia, the Middle East, and the Americas. In the course of this year Starlinger’s first installation in Bolivia, South America, has been finished.
To see some of the recoSTAR recycling lines in operation it is possible to visit reference customers upon request.
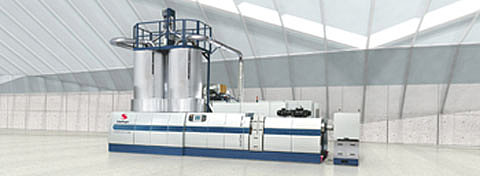
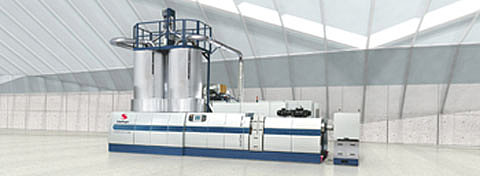
Starlinger recoSTAR PET iV+: Thinking high capacity and high quality in PET recycling
Starlinger recycling technology is a division of Starlinger & Co. Ges.m.b.H., the market leader in PP woven bag machinery. Since the product launch of the first PET recycling line in 2003 the Austrian company has established itself as a high-tech supplier of recycling equipment for bottle-to-bottle recycling and high-viscosity applications. Its SSP technology, based on the Starlinger iV+ process (recoSTAR SSP 1800, viscoSTAR 75 and 120), reduces the AA content in pellets and ensures thorough decontamination (including additives such as oxygen scavengers) as well as a substantial IV increase.Flexibility and user-friendliness are paramount to Starlinger when it comes to new developments. The latest technological achievements comprise capacity increase, energy saving measures, and easy adaptability to customer material. In addition, Starlinger has been granted food contact approvals by various countries and brand owners.recoSTAR PET iV+: System overviewThe recycling process consists of two main steps: the continuous extrusion process (recoSTAR PET) and the semi-continuous solid-stating of the produced pellets for IV increase and food contact suitability. For the solid-stating process Starlinger’s iV+ system with recoSTAR SSP 1800 or viscoSTAR 75/viscoSTAR 120 is used.Process description:The pre-cut or ground material is fed from the pre-drying unit directly into the extruder which uses the heat from the drying process. Volatile contaminants as well as monomers are extracted in a high-vacuum degassing unit. Solid contaminants are filtered out with a double-piston back-flushing screen changer (DPB) before pelletising.After the pelletising operation the regranulate is transported immediately into a crystalliser which also uses the residual heat from the still warm granulates. Then the granulate is conveyed into the pre-heater on top of the SSP reactor for further heating. After reaching reaction temperature, approximately three batches per hour are discharged into the reactor vessel.The pellets remain in the reactor vessel under heat and vacuum conditions for a set reaction time. The two factors temperature and time allow the relinking of the molecular chains: Polycondensation takes place. The required IV increase is controlled solely by means of the adjustable residence time – no additives are required. After the set residence time has elapsed, the pellets are discharged batch by batch into the optional cooling chamber and cooled down under controlled conditions to improve colour values.Quality of the recycled material:The melting point, crystallinity and flow characteristics of the output material are the same as those of virgin material. The recycled granulate is suitable for products with food-contact and has an AA level of less than 1 ppm. The IV can be adjusted according to the intended application of the recycled material (e.g. for strapping bands, the IV value is around 0.96 dl/g). Per hour residence time an IV increase of about 0.01 – 0.02 dl/g can be achieved.Features: The whole system is continuous and works according to the FIFO (first-in, first-out) principle with a defined residence time. This ensures that every particle receives the same treatment and thus is completely safe for food-contact. It also guarantees continuous IV increase and allows changing the residence time to adjust the IV.Because of its modularity, the machine system is completely flexible and can be adapted immediately to market changes which occur constantly due to e.g. varying input material or altering requirements of R-PET users. If, e.g., a longer residence time is required, either an additional SSP reactor can be added to the installation for maintaining the same output capacity, or the amorphous pellets are redirected into a silo for storage and are solid-stated later or sold for e.g. sheet application.Available machine sizesThe recoSTAR PET (HC) and recoSTAR basicPET series are available in five different extruder sizes and cover an output range of 180 – 2 000 kg/h. The capacity of the individual SSP units is 250 kg/h or 1200 kg/h, depending on the respective residence time. Higher capacities can be reached by means of parallel arranged additional units.Country and brand owner approvalsAlready one year after starting the planning and construction of the first SSP reactor, Starlinger obtained a letter of non-objection from the US Food and Drug Administration FDA. Although not valid worldwide, it clearly indicates that Starlinger machines reach a high level of decontamination. In November 2007 the FDA has issued a second letter of nonobjection stating that R-PET produced on a recoSTAR PET iV+ is suitable also for hot-fill applications.Of course also a variety of national approvals have been achieved, e.g. from Austria, Germany or Australia (via customers). Other national approvals are pending or being filed by customers (e.g. France, Finland). For approval in the European Union, all necessary challenge tests have already been completed to supply the required decontamination data to EFSA. This is especially important for European customers as the approval procedure for them is simplified when they can use the approval granted to Starlinger instead of having to carry out challenge tests themselves.One of Starlinger’s highest priorities is achieving brand-owner approvals. In order to protect their brand, those (usually) global players have especially stringent requirements concerning repeatable high decontamination results in recycling processes. Every single flake must meet the prescribed process parameters in order to pass through the system. The proven recoSTAR first-in first-out philosophy has satisfied the requirements of two major brand-owners, one of them being PepsiCo. Also other brand-owners are highly interested in allowing the use of R-PET for their food-contact products and are in close contact with Starlinger recycling technology regarding this matter.PepsiCo approves recoSTAR PET iV+:The Starlinger PET recycling line recoSTAR PET iV+ (with recoSTAR SSP or viscoSTAR) has received approval from PepsiCo by means of a customer audit.The Commercial Approval Letter states that up to 50% of the granulate used for the production of CSD and hot-fill bottles with direct food contact may be produced on a recoSTAR PET iV+ with accordingly defined parameters. The approval is based on the second letter of non-objection issued by the FDA (extended to include hot fill applications), granted to Starlinger in October 2007.One, but not the only, important criteria for obtaining the approval was the excellent decontamination capability of Starlinger's recycling and solid state polycondensation technology, which has been verified during the challenge test for the FDA approval.The Starlinger recoSTAR PET iV+ also meets two other assessment criteria in the audit: quality management and automation. The line is equipped with a “food grade” button and automatically switches over to non-food grade process mode when a parameter fails. As soon as all parameters are met again and, consequently, the regranulate produced fulfils all decontamination requirements, the line switches back to food grade process mode.Although the approval is recognised worldwide, each recycling company must undergo the PepsiCo audit process itself.Latest technological developmentsCapacity increase:Higher production costs, e.g. due to increasing energy costs, make it even more important that production systems have high output capacities and at the same time are still costeffective. Starlinger thus has further enhanced its proven system and now introduces five PET extruders with optional HC (High Capacity) design: With the same extruder diameter, output can be raised by up to 30 % with only a minor increase in costs.IV increaseIV increase depends on a variety of factors such as the IV value of the granulate at the start of the process, the quantity and type of contaminants, etc. Nevertheless, Starlinger has been able to speed up the solid stating process and thus the IV increase with a special version of the SSP unit. Either the possible IV increase during a specified amount of time is higher, or the residence time of the granulate becomes shorter.Energy saving:Due to the increased production capacity, production output is higher while the installed kW remain almost the same. This means less kW consumption/kg, which in turn results in cost savings. In addition, many components are designed to work with cooled water; thus, no chiller is required. Also, excess energy from the previous process step is preserved and used in the next step: For inline crystallisation after the pelletising process, for example, the residual heat of the pellets is used, which leads to a reduction of the energy consumption by 0.05 kW/kg.User-friendliness and easy maintenance:The extrusion unit and the SSP reactors feature a special easy-to-maintain vacuum pump system that does not require fresh water. The system is equipped with a central greasing unit and a central water distributor. Consequently, there is almost no waste water to dispose of and the whole equipment is more environmentally friendly.During pre-drying automatic filters are used for dedusting flakes from washing lines, which in turn results in easy maintenance and longer maintenance intervals.Adaptation to customer material:Input material changes constantly due to new resins and additives. The equipment can be adjusted accordingly: The modular system facilitates adaptation to customer requirements and allows upgrading of existing lines by exchanging or adding individual components.Also the process parameters such as process temperature and residence time (to reduce yellowing caused e.g. by AA blockers) can be specified according to customer needs.The recoSTAR PET line can be optionally equipped with a desiccant air dryer for predrying – it has proven especially useful for removing contaminants which are integrated in the resin structure (e.g. AA blockers). These contaminants are filtered out by means of condensate separators. Optionally a hot-air drying system can be supplied for higher output capacities or for flakes with higher moisture content.Applications, countries, referencesAlthough only on the market since 2003, Starlinger PET recycling lines are used in many fields of application and many countries by now. A total extrusion and solid-stating capacity of more than 50 000 t per year for bottle-grade R-PET was installed in 2007 alone. Starlinger PET recycling lines are also used for producing food-grade regranulate for PET sheet production and for in-house recycling of preforms. A modified version – the recoSTAR basicPET iV+, of which several lines have already been installed – is used for recycling PET strapping bands, fibres and non-wovens.The majority of the lines are installed in Western and Central/Eastern European countries, but also in Australia, the Middle East, and the Americas. In the course of this year Starlinger’s first installation in Bolivia, South America, has been finished.To see some of the recoSTAR recycling lines in operation it is possible to visit reference customers upon request.
The comPETence center provides your organisation with a dynamic, cost effective way to promote your products and services.
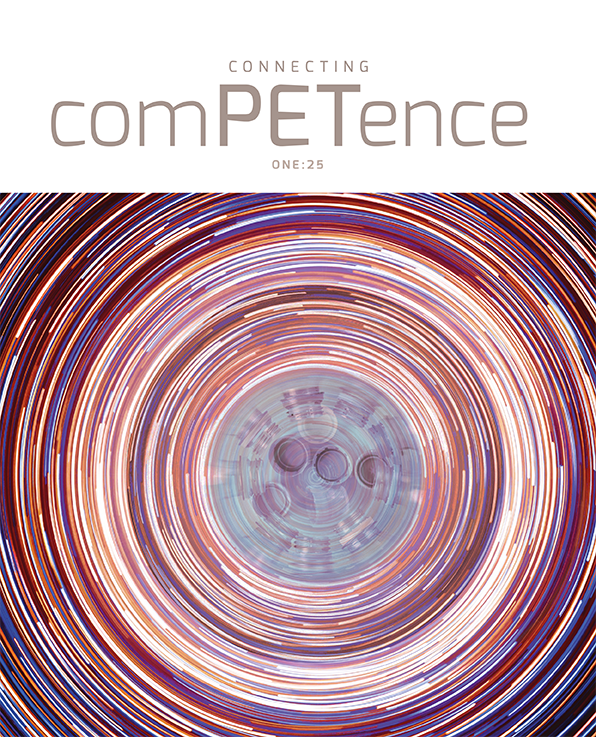
magazine
Find our premium articles, interviews, reports and more
in 3 issues in 2025.