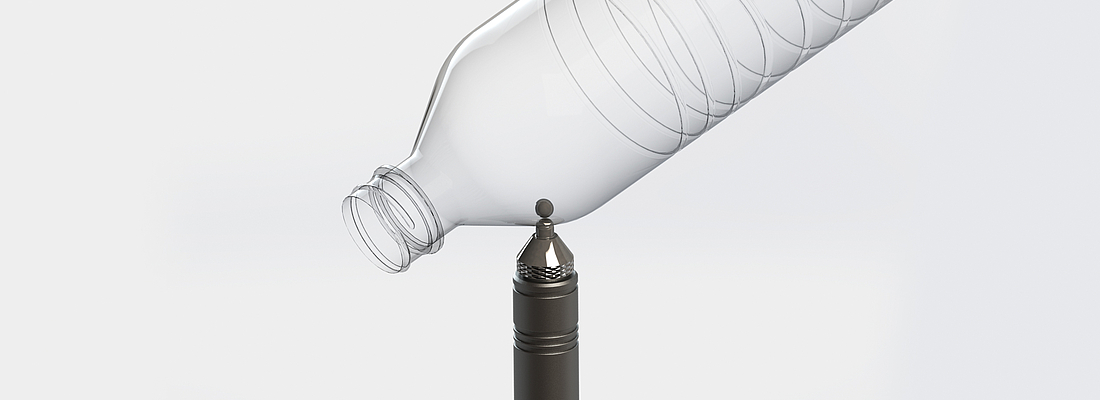
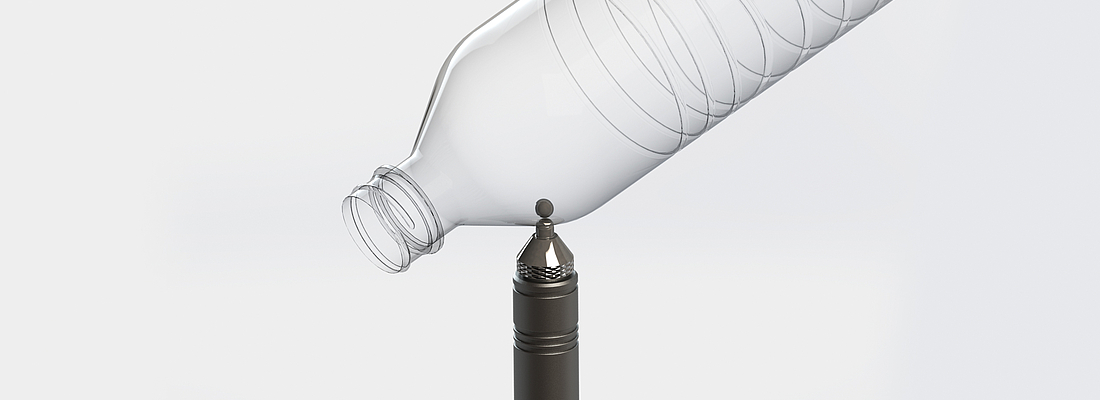
Whether it is food or beverages, shampoos or cosmetics, ensuring consumers receive fresh products is of the utmost importance to the wide array of companies who provide these daily essentials. Aside from providing quality product in the first place, what these products are contained in plays a quintessential role in ensuring freshness and consistency.
Multi-layer plastic bottles and containers are a diverse and popular option for housing consumer goods. Maintaining freshness by way of several layers of plastic, these bottles and containers are often characterized by their ultra-thin barrier layer.
The Barrier Layer
The barrier layer within multi-layer plastic containers is essential for quality control. Comprised of materials such as EVOH or PET, the barrier layer is the thinnest layer within the structure while also boasting the highest price tag.
Ensuring that the barrier layer is not only present but consistent throughout the structure is essential for quality control, as even the smallest imperfection can jeopardize the integrity of the product and ultimately cost both time and money.
Quality Testing via Destructive Testing
Measuring individual layers within multi-layer preforms, bottles and containers enables manufacturers to understand the quality and consistency of their packaging product while meeting testing standards.
Typically however, the testing of these plastic structures has been invasive, ineffective and limited.
One such testing technique called the Hall effect, utilizes a Magna Mike probe to measure the wall thickness of a plastic preform, bottle or container. Although non-destructive, this time-consuming technique requires direct contact with the sample under test, is limited to measuring only the overall wall thickness versus individual layers and cannot measure the barrier layer – arguably the most important layer within the structure.
Another common testing technique involves the manual cutting of the preform, bottle or container under test and then peeling and measuring each layer individually. This technique is not only highly destructive, time consuming and prone to human error, it is also limited to a small sampling and extremely wasteful as the plastic preform, bottle or container is destroyed in the measurement process.
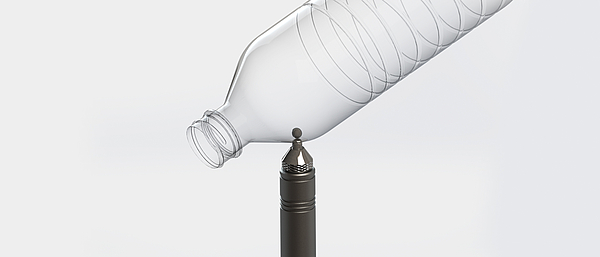
Fig. 1: A Magna Mike probe can be used to measure only the overall wall thickness
Cut the Cutting with Terahertz Waves
In a day and age where time is money and waste reduction is viewed as universally essential, inefficient and ineffective quality assurance practices are a thing of the past; yet when it comes to plastic thickness measurement, manual cutting has proven to be the top solution for this important task.
Fortunately, terahertz-powered solutions have recently emerged as the new hero in this traditionally wasteful tale; but how?
With the help of terahertz waves, multi-layer plastic preform, bottle and container manufacturers can measure, identify and inspect both the barrier layer and the surrounding base layers in a non-invasive, non-destructive way.
Multi-layer measurement systems such as IMDvista LAYER, are entering the manufacturing scene as the non-destructive answer to a largely destructive problem; and at the heart of the system? Terahertz technology.
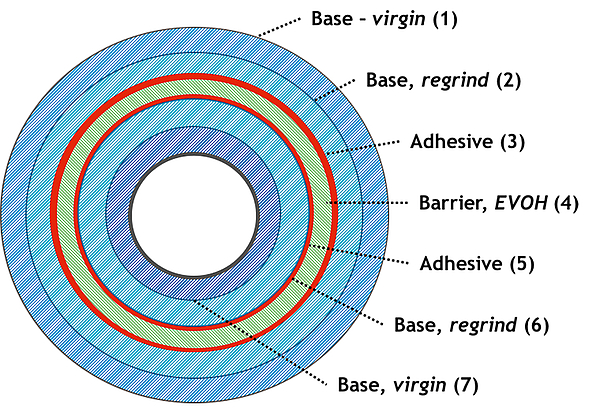
Fig. 2: An example of the several different layers within a multi-layer plastic structure
Non-Destructive Testing Gauge, Powered by Terahertz Waves™
The core technology behind IMDvista LAYER is Waterloo, Ontario based TeTechS’ TeraGauge™, a non-destructive testing gauge powered by terahertz waves™.
Terahertz waves have long been viewed as too elusive for use in the “real” world but their unique properties make them ideal for use in multi-layer plastics thickness measurement. Non-contact and non-destructive, terahertz waves can see through both opaque and translucent materials which other modalities, such as infrared, cannot.
With the power of TeraGauge™ inside, IMDvista LAYER enables users to conduct quick, accurate and precise measurements of individual layers within both mono and multi-layer plastic structures. What’s more, this terahertz-powered system can measure up to 10 layers ranging in thickness from 0.01mm to 5mm in a matter of seconds while enabling users to locate and measure the costly, ultra-thin barrier layer within the plastic preform, bottle or containers.
TeraGauge™ works based on the terahertz time-domain principle to essentially send short terahertz pulses that penetrate the sample under test and reflect back into the gauge at each layer. The reflected pulses then have their time-delay measured which corresponds to the thickness of the layers of the plastic bottle or preform. The difference between the time delay of two reflected pulses, allows for the calculation of the precise thickness of the individual layers within the plastic structure.
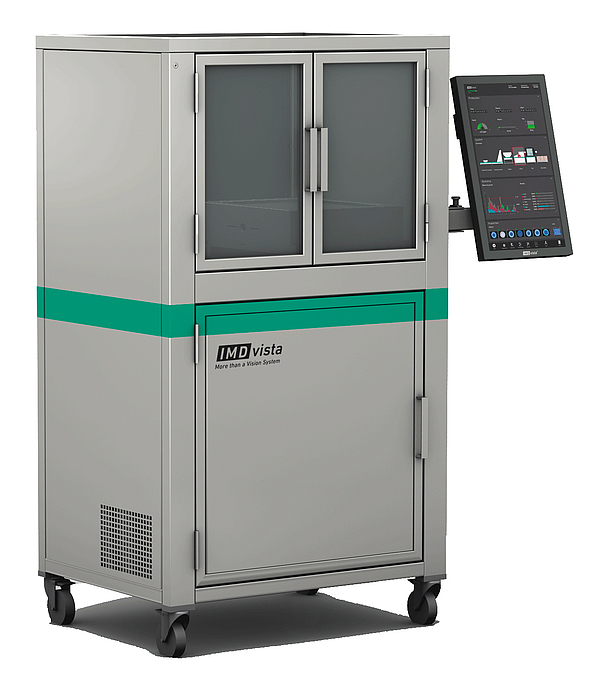
Fig. 3: IMDvista LAYER is a multi-layer thickness measurement system for cylindrical plastics
A New “Wave”
Compared to traditional measurement techniques, terahertz technology such as TeTechS’ TeraGauge™, is proving to be the quick, reliable and non-destructive solution to a long-time problem. As a direct result, TeTechS along with its partners are gaining market leadership within the plastic bottle and container manufacturing industry by providing a whole product solution with IMDvista LAYER.
By meeting real-world needs while simultaneously providing manufacturers with repeatability, ease of use, and confidence in the quality of their products, terahertz waves are ultimately powering a new wave: effective and efficient thickness measurement.
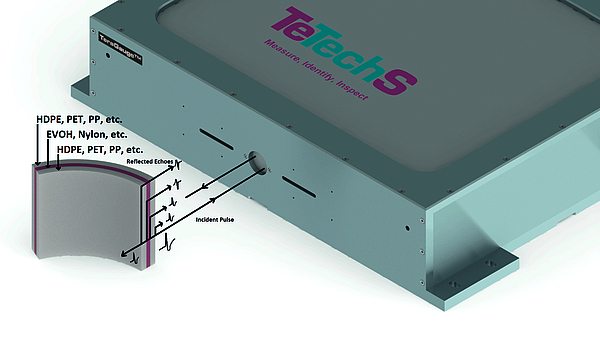
Fig. 4: TeraGauge™ utilizes the terahertz time-domain principle to measure multi-layer plastics
The comPETence center provides your organisation with a dynamic, cost effective way to promote your products and services.
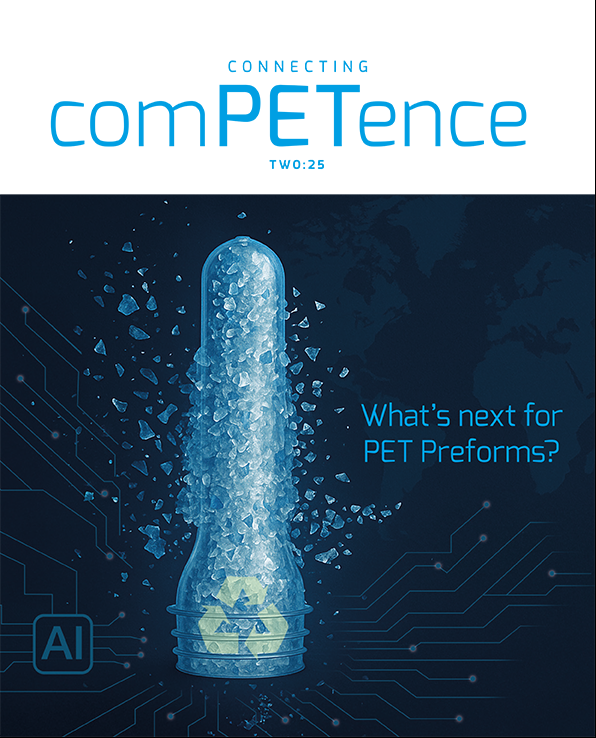
magazine
Find our premium articles, interviews, reports and more
in 3 issues in 2025.