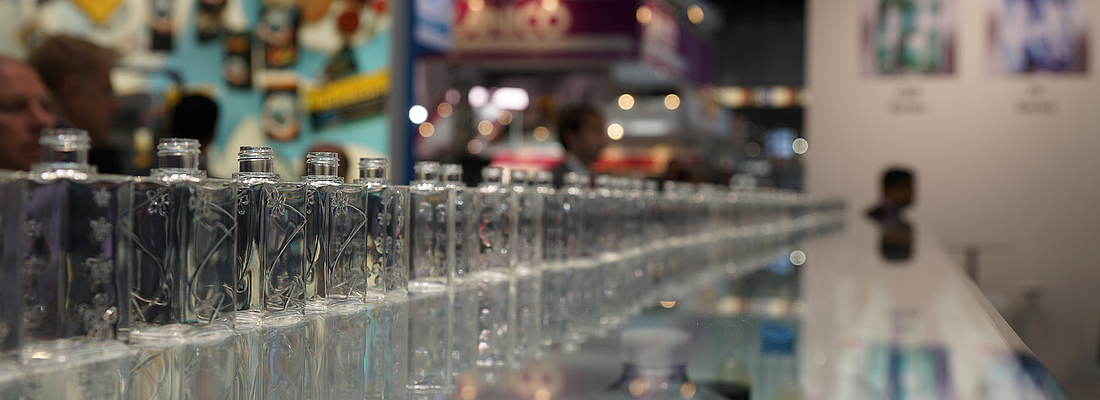
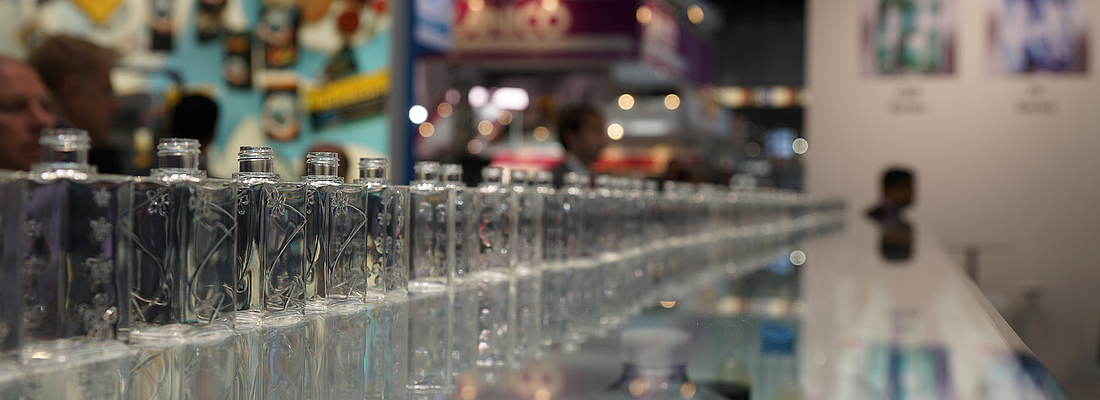
The international packaging industry meeting this year was met with satisfaction all round: the indicatorsof public opinion and economic success show upward trends, the Messe Düsseldorf reported recordexhibitor numbers, exhibitors were delighted to welcome decision-makers among other visitors, andvisitors poured praise on interpack for its unique role as an exhibition and communication platform.Digitalisation, Industry 4.0 and sustainability were among the main topics at the world’s largest trade fairfor the packaging industry, which took place from 4-10th May, as is tradition, in Düsseldorf.
PACKAGING IS MORE THAN PROTECTION
Although the topic of sustainability has been pervasive inthe industry for years, it seemed even more present thisyear. Increasing numbers of companies are taking a closerlook at the issue, motivated by a range of factors includinglegal requirements, their ecological conscience, or economicbenefits. To emphasise this, some exhibition booths in theSave Food Pavilion and mainly in Hall 9 had set up greendisplays adorned with nature-themed accessories includingplants, blossom and fruit. Then again, sustainability is a broadtopic area, which was reflected in the diverse presentationsgiven at interpack. To mention one aspect, the packaging itselfcan be sustainable, since it ensures that the filled material –particularly in the case of food products – does not go off.Comparing the carbon footprint of the packaging with that ofits content reveals that the former constitutes a maximum of2% of the total footprint.
BIOPLASTICS ARE GAINING GROUND
Bioplastics are discussed time and again in conjunctionwith sustainability. Bioplastics have been established fora number of years but have only really caught on so far inniche applications. The difficulties in establishing themselveswas, and still is, a consequence of their price, which amountsto around three times as high as conventional plastics.Nevertheless, increasing companies are taking up the topic,and larger raw material producers alongside many start-upsand small enterprises are gradually expanding their portfoliosto include bioplastics. BASF, Braskem and Total Corbionamong others presented bioplastic solutions at interpack.It is important to differentiate between the different sortsof raw material. Bioplastics encompass plastics which aremanufactured from renewable raw materials such as greenpolyethylene from Braskem or the polyamide UltramidFlex F38 L from BASF, and also other plastics which arebiodegradable and/or compostable. In the case of compostablebioplastics, a distinction has to be drawn between those whichbiodegrade after 12 months in normal domestic compostconditions, and those which degrade after three months inindustrial composting plants, due to the higher temperatures.Of course, there are also bioplastics which are both bio-basedand biodegradable, for example the polyester PLA from TotalCorbion.It should also be noted that the so-called drop-in solutions,which use a sustainable resource instead of a fossil resourceto manufacture the monomer for a polymer which makesplastic, are no different from conventional plastics in theirprofile of properties nor in their recoverable nature. They stillhave to be recycled, deposited or thermally processed, justlike any other. This often leads to the discussion of whetherit is acceptable to use resources which could also be usedas food, such as sugar cane or corn, to create plastic. Thisquestion has to be dealt with on a case-by-case basis and willnot be explored in this article.
LAWS PROMOTE THE USE OF BIOPLASTICS
Bioplastic suppliers are currently enjoying an additional boostthanks to the current changes in statutory requirements.France is one of the pioneers in this respect. According to anew law which came into force on 1 January 2017, all fruit andvegetable bags must be manufactured from renewable rawmaterials and biodegrade in domestic compost. Another lawis set to follow in 2020, stipulating that all catering articlesmust be compostable at home, in contrast to the currentlaw which permits them to be compostable in industrialcomposting facilities. Carrier bags have been banned in Italyfor several years, though compostable bags are still allowed.“In Finland, biodegradable plastic films are commonly used forfood packaging,” says the Export Manager Marko Päiväniemiof the Finnish company Plastiroll Oy from Ylojärvi, which hasbeen manufacturing 100% compostable films for over 20years. He comments that the poor H2O barrier actually provesadvantageous for fruit and vegetables, as it replaces the needto make perforations to prevent the packaging from foggingup. A disadvantage of this packaging is that is can only beused for six to nine months. In addition to foils, bioplasticsare also used in manufacturing deep-drawing packaging.“We are the first manufacturer to offer fully recyclable highbarrierpackaging for meat,” explains Stefan Corbus, AccountManager at Eval Europe in Melsele, Belgium. The corn starchbasedpolymer Plantic is manufactured from the starcheswhich are not suitable for consumption as food products. “Theoxygen barrier is currently almost as high as that of EVOHproducts, and we manufacture a 3-layer composite to providean additional water vapour barrier,” explains Stefan Corbus. A3-layer composite made of Plantic and PET is already on themarket in Australia and is used to package meat. Recycling isreportedly not a problem, as the starches are washed out inthe washing station and the PET is simply processed again.The company also provides fully compostable, high-barrierpaper packaging which can be sealed. Plantic CF is a biobasedPBS, which can be laminated onto paper and is evenhome compostable up to a strength of 250 ?m.
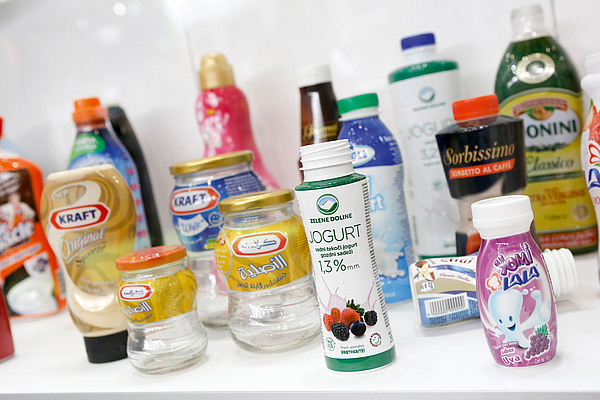
THE BIGGER PICTURE:THE LATEST NEWS ON PAPER
Speaking of paper, numerous paper packaging solutionswere on display at interpack. Susan Janssen, SustainabilityMarketing Manager at Wipak B.V., Sittard, Holland,presented a thermoforming paper composite which boastsa 45% decreased carbon footprint in comparison to anEPS tray. “As a renewable raw material, paper is a popularalternative to plastic among some of our clients,” she says.At the same time, she also pointed out that there is no singlesustainable solution. Individual sustainable solutions mustbe found depending on the product and market, as thereare many other factors which influence the sustainability ofpackaging, including weight, thickness, regional availability orrecyclability.
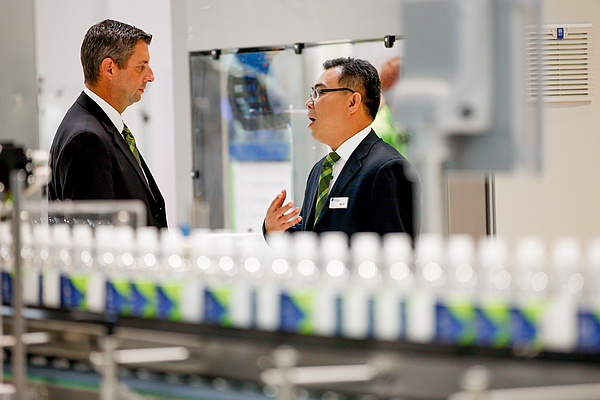
SUSTAINABLE BOTTLES: PEF
While interpack did not centre on bottles as a packagingsolution, there was still some sustainable or technicalnews. Synvina, the joint venture from BASF and Avantium, presented bottles made from the 100% bio-based polymer PEF. The PEF bottles on display were real eye-catchers – the PET processing industry is already waiting to get a closer look at the PEF material, and also the products manufactured using it. Synvina aims to extend its globally leading positions in furandicarboxylic acid (FDCA) and poly-ethylene-furanoate (PEF). FDCA is manufactured from regenerative raw materials and is an important building block for the manufacturing of PEF which is suitable for food packaging, foils, plastic bottles and much more. PEF has a higher O2 and CO2 barrier in comparison to PET, which gives it the edge in food and drink packaging. Gerald Michael, Global Business Manager at Synvina: “PEF also has a higher mechanical strength and stiffness, allowing packaging to be manufactured with very thin walls, and reducing the amount of packing material required.” PEF has recently received interim approval from EPBP for the recyclability in the European bottle recycling market. This should enable PEF bottles to be recycled using the same methods as conventional PET bottles and disposed of through existing recycling systems. A final statement based on PEF quality, packaging designs and regional launch markets will be issued before market introduction.
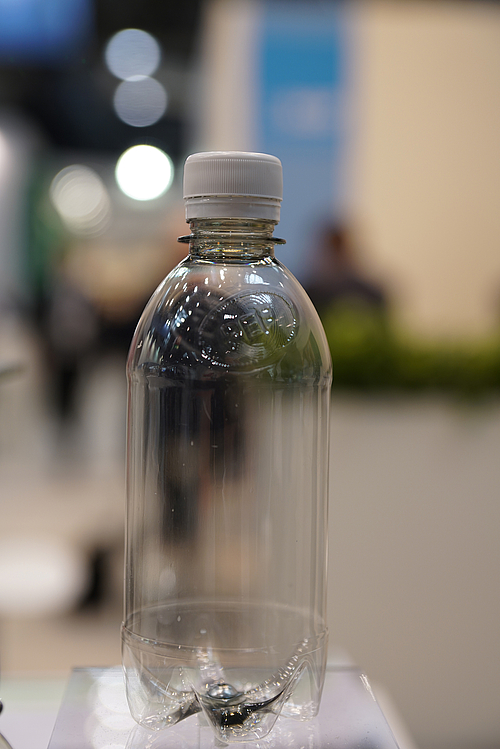
Synvina‘s PEF bottle
GREINER PACKAGING – BACK AT INTERPACK
For the first time in nine years, Greiner Packaging waspresenting its diverse range of innovative products atinterpack. The key focus at the stand was on solutions in thefield of barriers and shelf life, sustainable products, recycledmaterials and lightweighting. Innovative technologies for moreconvenience have been presented, as well as special solutionsfor the ageing population and strategic approaches in the areaof globalization. Thomas Edbauer, Sales Manager: “Changinglifestyles have an increasing impact on our environment. As aplastic packaging producer we have the responsibility to serveconsumer needs and, at the same time, act in an ecologicallysensible way. Our barrier packaging solutions are a great wayto do so: they meet consumer demands of extended foodshelf-life without having preservatives added and, thus, helpto prevent food waste.“
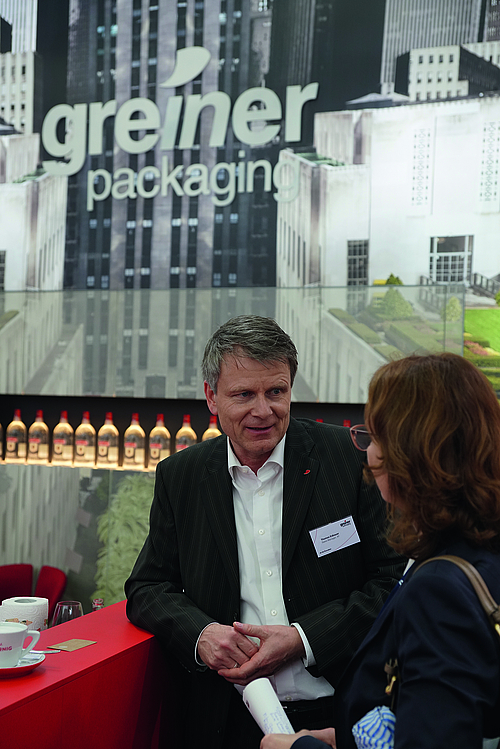
Thomas Edbauer, Greiner Packaging
SIPA WITH THE NEW MODEL SFL 6/8 EVOSIPA
was premiering a new model in its range of SFL linearblow molding systems. The SFL 6/8 EVO features 8 blowingcavities and allows a 48% output increase compared to the6 cavities top of the SFL range with 10,800 b/h. Productionlevels of as many as 2000 bottles per hour per cavity are nowpossible. Result is 16,000 bph with only 8 cavities. This isdue to faster press movements and improved blowing valve.“The SFL 6/8 EVO provides a perfect scale-up opportunityfor the big converter, enabling them to manage complexpackaging with a small and flexible blowing platform. All thenew developments we have built into the unit, together withthe low cost of maintenance, result in the lowest total cost ofownership, TCO, on the market, to guarantee both operationalexcellence and business flexibility.” says Enrico Gribaudo,General Manager at SIPA.Not only the new machine was presented at the SIPA booth,also the booth concept is new: “This is also our warming-upfor the Drinktec”, says Roberta Gualtieri, Marketing Managerat SIPA.
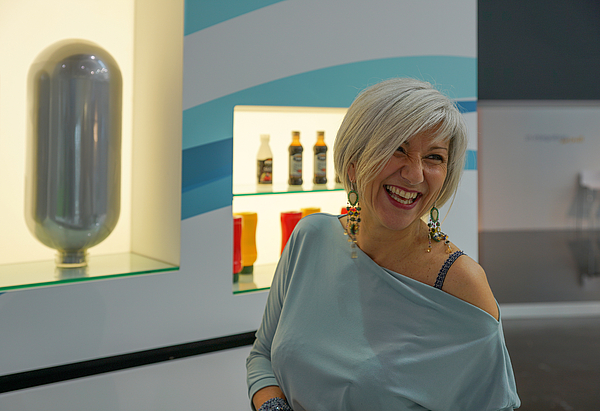
Roberta Gualtieri, SIPA
NISSEI ASB WITH THEIR SMALLEST ISBMMACHINES
ASB focused on their smallest class of one-step ISBMmachines, the ASB-12M, produced since the early 1980s. Thissuccessful and extremely flexible machine has a vast rangeof capabilities for production of all types of PET containersincluding light-weight bottles, all the way through to heavyweightcosmetic containers to the highest quality. Many startupcompanies took advantage of its ability to process manytypes of resins in addition to PET and the low total cost ofownership. The model displayed at Interpack was fitted withthe optional long stroke injection unit that provides a 50%increases in available shot-size, expanding the scope for largecontainers, heavy-weight cosmetic bottles, or materials suchas polypropylene that have lower density.
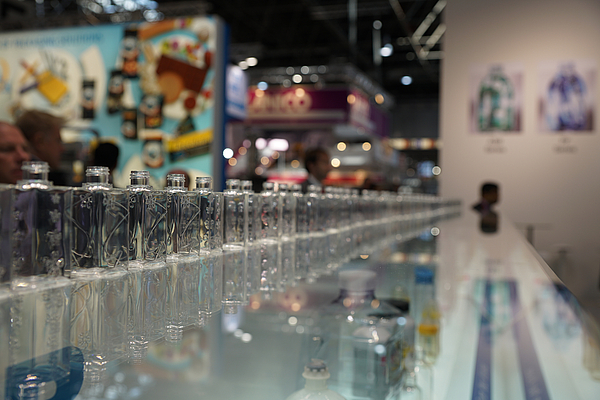
NISSEI ASB
SLEEVER WITH SUSTAINABLE TURNKEYSOLUTIONS
At the Sleever International booth, different sustainableturnkey solutions for innovative shrink sleeves have beenpresented, all based on the Combisteam machine technology:A shrink sleeve made of low density PET (LDPET® - RecyclingForever) is Sleever International’s answer to the recyclabilityof PET bottles. LDPET, which includes a low density PET film,allows separating sleeves from bottles without any manualoperation. Thanks to a specific density, the LDPET can beeasily sorted out in sedimentation tanks. The LDPET flakesfloat whereas the PET bottle flakes sink to the bottom of theSynvina‘s PEF bottle Thomas Edbauer, Greiner Packaging Roberta Gualtieri, SIPA NISSEI ASB Sleever International, Eric Fresnel, President (right) andSofiane Mameri, Communication Managertank. In addition the printed film uses inks that are specificallydesigned to withstand the materials segregation treatmentwith no risk of contamination for the PET flakes. The LDPETturnkey solution that includes a Combisteam® machine allowsa full or partial labeling of bottles ranging from 20 cl to 2liters, with production outputs between 15 000 and 30 000bottles per hour.
In the case of light sensitive products, transparency has tobe combined with protection against visible and invisible raysto prolong shelf life and preserve the product’s organolepticqualities. Clear PET bottles are now equipped with theopaque DUOLIFE® “Absolute Armor”, an innovative sleeveoffering extended shelf life for dairy products. Regarding therecyclability this light barrier solution using clear PET bottleshas considerable advantages over opaque PET bottles causingdifficulties within the recycling process.LWPET – “Feathery Footprint” is a sleeve solution fordairy products in polyethylene bottles. At Interpack, it waspresented in demonstration on the Combisteam®-LWPETmachine. Sofiane Mameri, Communication Manager atSleever International: “LWPET enables to reduce shrinksleeve carbon footprint by 50%.” This new product isbased on 3 developments: a new 20 microns PET film, aspecific flexoffset printing technology and the new sleeving 9697equipment, the Combisteam®- LWPET. “LWPET brings ananswer to environmental issues”, says Mameri. SleeverInternational customers can find information on Sleevers’packaging solutions with the MYPACK CONNECT app.
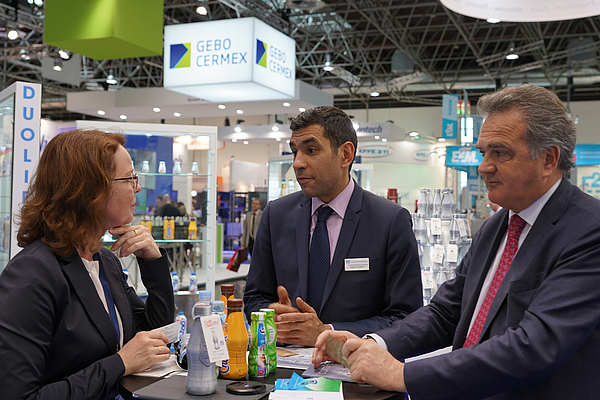
Sleever International, Eric Fresnel, President (right) and
Sofiane Mameri, Communication Manager
MILLIKEN WITH UV ABSORBER FOR PET
Also Milliken offered a light barrier solution: With ClearShield®Colorless UV absorber Milliken introduces an additive thatprotects the product from UV light without having anyimpact on the clarity and transparency of the resin. The newabsorber is applicable in personal care, household cleaningproducts, various solid foods and spices and also juices andenergy drinks. For vitamin packaging where such protectionis vital since most vitamins are sensitive to UV light, heatand oxygen, ClearShield is of special interest. Integrating UVprotection into the package instead of the product means thatproducers can simplify formulations of their products andthus respond to consumer demands and reduce stabilizersand preservatives. Since it is often possible to also reduceformulation complexity costs can be reduced. Also at the endof the value chain, Simon Bousquet, Development EngineerChemical Division, sees the advantages of the ClearShield UVadditive: “ClearShield is a clear alternative to dark or coloredcontainers. Such opaque PET materials tend to make therecycle stream dark, which can make recycling more difficultand lessen the value of the reclaimed product.”
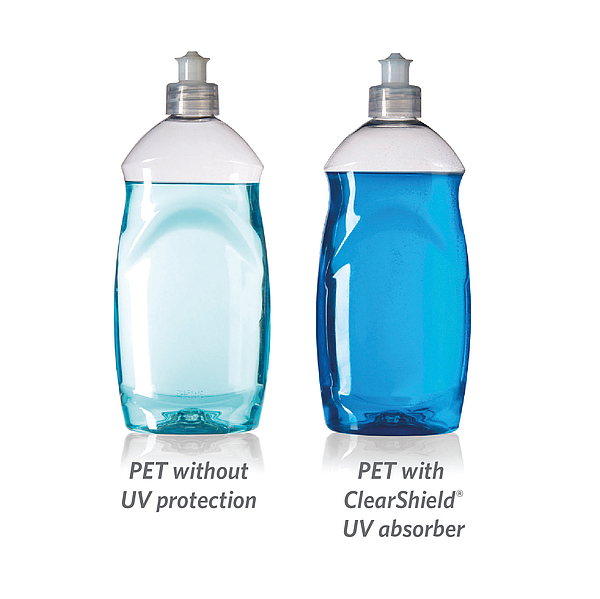
Milliken
SUSTAINABILITY IS NOT POSSIBLE WITHOUTRECYCLING
Recycling products are more sustainable than theircompetitors made from virgin materials, conserve existingresources and tend to have a smaller carbon footprint.When talking about bioplastics and recycling, we quicklycome up against certain limits. Drop-in solutions avoid theproblem, however experts have warned against distortionof the recycling process through degradable bioplastics.Furthermore, it becomes necessary to provide even betterconsumer information, as consumers need to know whichplastic product can go in which waste bin – otherwise toomany non-biodegradable plastics could end up in the organicwaste and vice versa. But who is going to check? Such issueshave led many companies to use recyclable materials fromthe outset to manufacture their packaging solutions, such asthe Danish packaging manufacturer R. Faerch Plast AS basedin Holstebro. Vice President Jesper Emil Jensen on the topic:“We completely avoid processing bioplastics. We produce ourPET films and tray exclusively from mono material becausewe are convinced that this is most effectively recycled.”Nowadays, the company uses around 60% more recycledmaterials than virgin resins and manufactures compoundsolutions with virgin materials, of course, as with PET. Thecompany Starlinger & Co. GmbH from Vienna presentedsolutions using recyclable materials, displaying sacks andbig bags made of PET woven mesh, both manufactured from100% recycled PET.Duales System Deutschland GmbH from Cologne presenteda smell-minimizing and translucent HDPE made from 100%post-consumer materials. The first bottle made of thistype of HDPE containing cleaning agent is already on themarket, provided by the company Werner & Mertz underthe brand name “Emsal”. There is also a PET bottle whichis manufactured from 98% recycled PET and has a PP capproduced from regrind. Werner & Mertz offer a cleaning agentfrom the “Frosch” brand in this bottle. Both recycling bottlesare manufactured by the company Alpla.
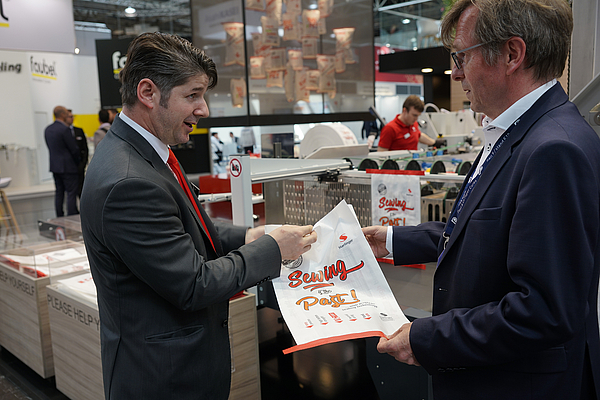
Starlinger: Sacs and big bags made of 100% rPET
SMI
At Interpack 2017 SMI was exhibiting the new fully electronic,compact rotary stretch-blow moulder EBS K ERGON inECOBLOC® configuration with a volumetric filler.The new EBS K ERGON series is available with 2, 3 and 4cavities and allows the user to benefit from all advantagesof the rotary technology in a range of outputs (from 3-4,000up to 8-9,000 bottles/hour) usually served by linear blowers.
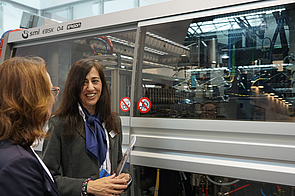
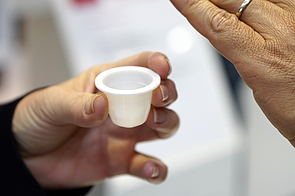
Daniela Dadda, SMI
CCM CONTINOUS COMPRESSION MOULDING
SACMI showed a continuous hydraulic compression press formanufacturing plastic coffee capsules made of a compostableresin.CCM hydraulic rotary presses are specially designed toproduce thermoplastic products by means of compression. Acontinuous work cycle is carried out, during which the plasticmaterial is fed by a plasticization unit, cut into suitably sizedpellets and then inserted in the cavities, moulded and cooledwhile completing the rotary cycle. An hydraulic system clampsthe moulds at a pressure which can be adjusted even whilethe production cycle is in progress, thus being able to modifythe thickness of the cap/capsule top/bottom panel just bymodifying parameters in the HMI, without changing any partin the mould.Iacopo Bianconcini: “SACMI know-how and extensiveexperience in compression technology, and its intrinsiccarachteristics (lowest cycle times in the industry, qualitycontrol on every capsule, energy saving, weight consinstency,easy and flexible mould maintenance), finally enable the fastgrowing single-serve players (being them converters or endusers)to gain competitive advantage, lowering the productfinal TCO. Having visited all the Interpack pavillions, thepresence of single serve capsules was massive, but actuallyonly at SACMI booth there was a machine producing them,in a compostable resin, and being it the ‘debut’ at a publicexhibition of the compresison technology in this specificsegment, the echo of it was huge, above our expectations“.
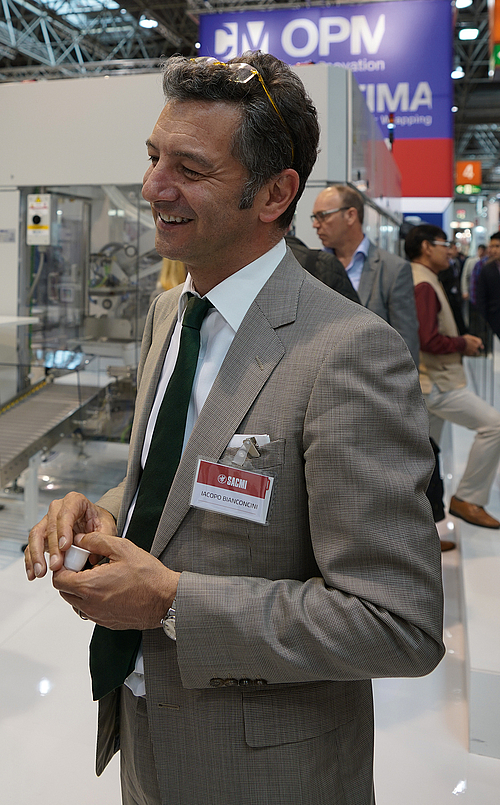
Iacopo Bianconcini, SACMI
This article has introduced some of the sustainable solutionspresented at interpack giving paradigmatic examples andwithout any pretension of being complete. There are countlessother solutions and many research projects exploring thetopic. Bioplastics and recycling as well as the resultantdiscussions will surely remain talking point for the industryat the Drinktec, at the upcoming PETnology Conference andin the coming years. There is a lot to look forward at theupcoming events and the next interpack in 2020.
The comPETence center provides your organisation with a dynamic, cost effective way to promote your products and services.
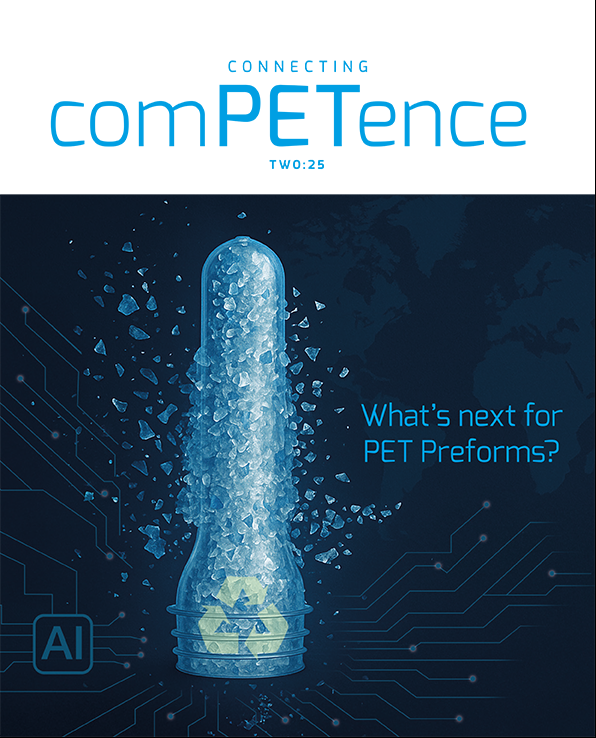
magazine
Find our premium articles, interviews, reports and more
in 3 issues in 2025.