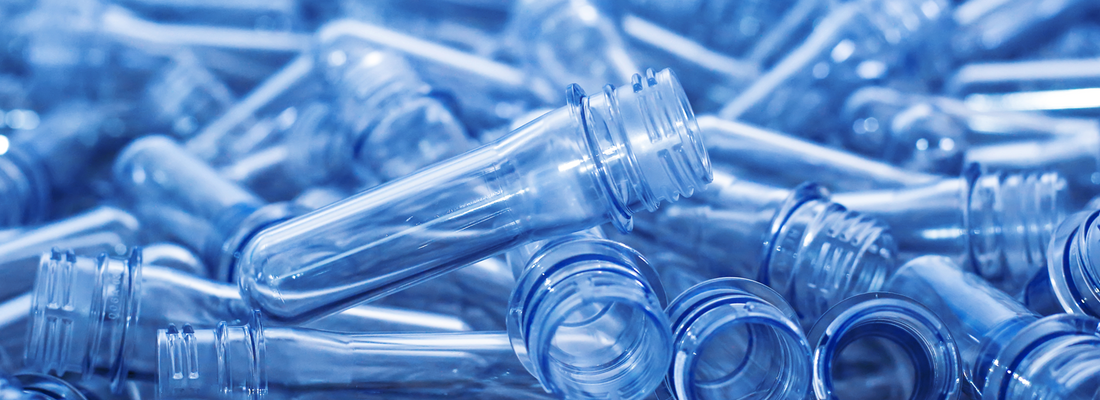
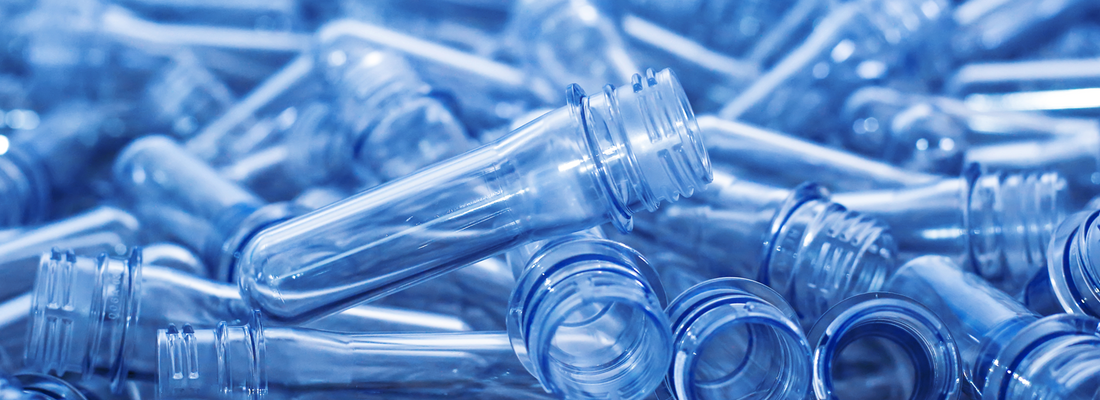
Material Handling
Revolutionizing rPET preform production: Advanced solutions for the future of beverage packaging
PET Solutions has recently completed the installation of a cutting-edge production line for a leading client in the beverage industry, designed specifically for the processing of recycled PET (rPET) in preform production. With an impressive throughput of approximately 6,000 kg/h, the plant integrates state-of-theart technologies aimed at optimizing performance, ensuring energy efficiency, and maintaining consistent material quality throughout the production process. This installation serves as a testament to the potential of sustainable manufacturing practices in a growing market that increasingly demands eco-friendly packaging solutions.
External Silo Loading System: Efficient and Safe Material Handling
The first stage of the plant’s operations involves the handling and loading of raw materials into four external silos, which are supplied by Ergomec, part of Pegaso Industries. These silos are equipped with advanced pneumatic transport systems that securely transfer materials while maintaining strict standards for contamination control.
The system is designed to automate material flow, ensuring a continuous and steady supply of material to the downstream feeders. This not only enhances the operational efficiency of the plant but also minimizes the risks associated with manual handling, reducing contamination risks and improving safety. The use of pneumatic transport ensures that the materials are transferred in a controlled and clean manner, which is especially critical when handling recycled PET.
Gravimetric Dosing System: High Precision for Optimized Material Blending
A critical component of the system is the gravimetric dosing technology, which provides ±0.1% dosing accuracy for incoming materials. Capable of managing up to eight different components, the system offers throughput rates ranging from 50 kg/h to 3,000 kg/h, ensuring that the precise material proportions required for preform production are maintained at all times.
The dosing system is equipped with real-time monitoring and an adaptive recalibration feature, which guarantees that material quality remains consistent throughout the production process. By utilizing a Siemens S7 PLC, the system provides operators with real-time control through a userfriendly 7-inch touchscreen interface. This allows for precise monitoring and fine-tuning of material flow, contributing to enhanced product quality and reducing the chances of error during the production process.
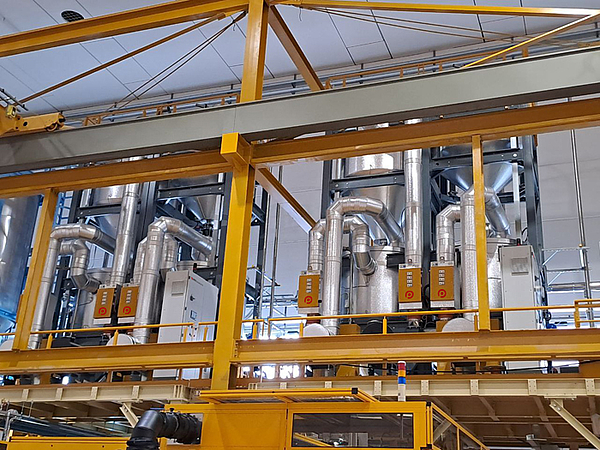
DRV Vacuum Drying Technology: Advanced Moisture Removal
At the core of the plant’s operations lies the DRV technology, a continuous vacuum drying solution optimized for drying both rPET and virgin PET materials before injection molding to produce preforms. The DRV system operates under reduced pressure, which not only improves energy efficiency but also helps protect the material from overheating and degradation.
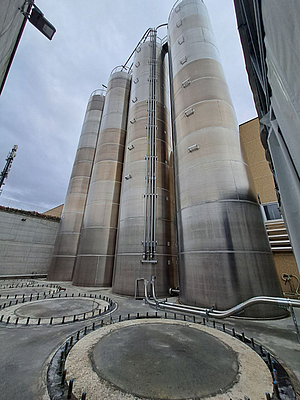
Key advantages of the DRV system include:
- Material Protection: The low-pressure operation prevents thermal degradation and preserves the quality of the material, preventing common issues such as yellowing, which is often seen with traditional drying systems.
- Energy Efficiency: The DRV system operates with a significantly reduced energy footprint compared to conventional systems, eliminating the need for oil condensers and providing considerable energy savings.
- Fast and Uniform Drying: The four-hopper drying process ensures that the moisture content is consistently reduced, optimizing the material for the next stage of production. This uniform drying process is essential for maintaining the quality and consistency of preforms.
- Quick Material Changeover: The system reduces changeover times by up to 65%, enhancing the overall efficiency of the plant and reducing downtime between production runs.
- Minimal Maintenance: The design of the DRV system requires minimal maintenance, ensuring fewer interruptions and higher operational uptime.
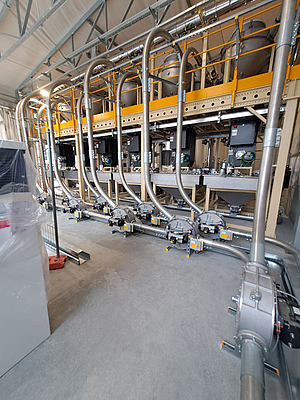
Energy Efficiency and Sustainability: A Green Approach
The entire plant is designed with a strong emphasis on sustainability, reducing the environmental impact of the production process while improving operational efficiency. The integration of energyefficient technologies, such as the DRV drying system, the gravimetric dosing system, and the automated material flow management, all contribute to lowering energy consumption and operational costs. This energy-conscious design is aligned with the global shift toward sustainable manufacturing practices, which are becoming increasingly essential in the face of growing environmental concerns.
The plant’s focus on optimizing the use of recycled PET ensures that the system plays a significant role in the circular economy, reducing the reliance on virgin materials. The use of rPET not only supports sustainability goals but also helps reduce the ecological footprint of the beverage industry’s packaging solutions, aligning with growing regulatory demands for eco-friendly products.
Integrated Control Systems
A vital aspect of this plant’s success lies in its integration of advanced control technologies. The plant’s operations are managed by a Siemens S7 PLC, which coordinates the various subsystems, ensuring seamless interaction between each component of the production line. This integration ensures that material handling, dosing, drying, and other processes are synchronized, reducing the potential for errors and optimizing production efficiency.
The touchscreen interface provides operators with real-time access to all critical process parameters, allowing for rapid adjustments to be made as required. This real-time control enables operators to monitor and fine-tune operations, ensuring high production quality and minimal downtime. Additionally, the system’s data collection and diagnostics capabilities facilitate predictive maintenance, ensuring that any potential issues are addressed before they result in production stoppages.
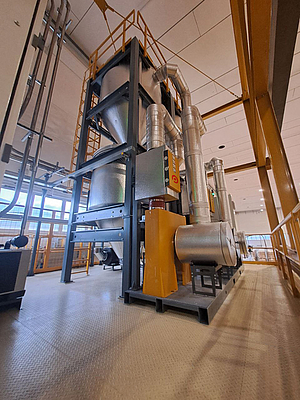
Predictive Maintenance: Proactive Interventions and Operational Reliability
PET Solutions’ predictive maintenance system is engineered to reduce unplanned downtime and optimize the performance of production lines. By leveraging a network of advanced sensors, the system continuously collects real-time data on the operating conditions of each machine and plant component. This enables the early detection of anomalies and the identification of potential failures before they occur. Through predictive data analytics, maintenance activities can be scheduled in a targeted and efficient manner, minimizing emergency interventions and extending the operational life of equipment. This approach significantly lowers operating costs while enhancing system reliability and ensuring consistent production flow.
End-to-End Traceability: Complete Supply Chain Control
Full supply chain visibility is a cornerstone of efficient production — and PET Solutions achieves this through an advanced end-to-end traceability system capable of tracking every stage, from raw materials to final delivery. This system allows realtime monitoring of material flow and production progress, ensuring that each operation is precisely recorded and tracked through digital data capture. The result is a significant reduction in manual errors and improved inventory management. Moreover, this comprehensive traceability ensures full compliance with quality standards and enhances transparency across the entire supply chain, effectively addressing increasing customer demands for safety and sustainability.
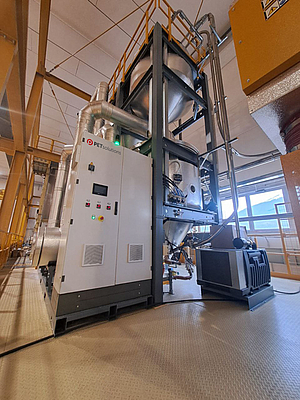
Operational Excellence
The combination of automated material handling, precise dosing, energy-efficient drying, and integrated control systems ensures that the rPET preform production plant is both highly efficient and reliable. The plant is able to maintain high throughput while consistently producing highquality preforms that meet stringent industry standards.
The system is designed to optimize the processing of recycled PET, a challenging material due to its variability in quality, while maintaining tight control over energy usage and production costs. This results in a highly cost-effective, environmentally friendly solution that addresses the beverage industry’s increasing demand for sustainable packaging.
Leading the Way in rPET Preform Production
This advanced rPET preform production plant demonstrates PET Solutions’ leadership in the field of sustainable manufacturing and innovative packaging solutions. Through the integration of advanced technologies such as gravimetric dosing systems, DRV vacuum drying, and automated material handling, the plant not only optimizes production processes but also reduces the environmental impact of PET production.
The focus on energy efficiency, sustainability, and advanced automation positions this plant as a model for the future of rPET preform production. PET Solutions continues to set the standard for innovation and sustainability, offering solutions that not only enhance operational performance but also contribute to a greener, more sustainable packaging industry.
The comPETence center provides your organisation with a dynamic, cost effective way to promote your products and services.
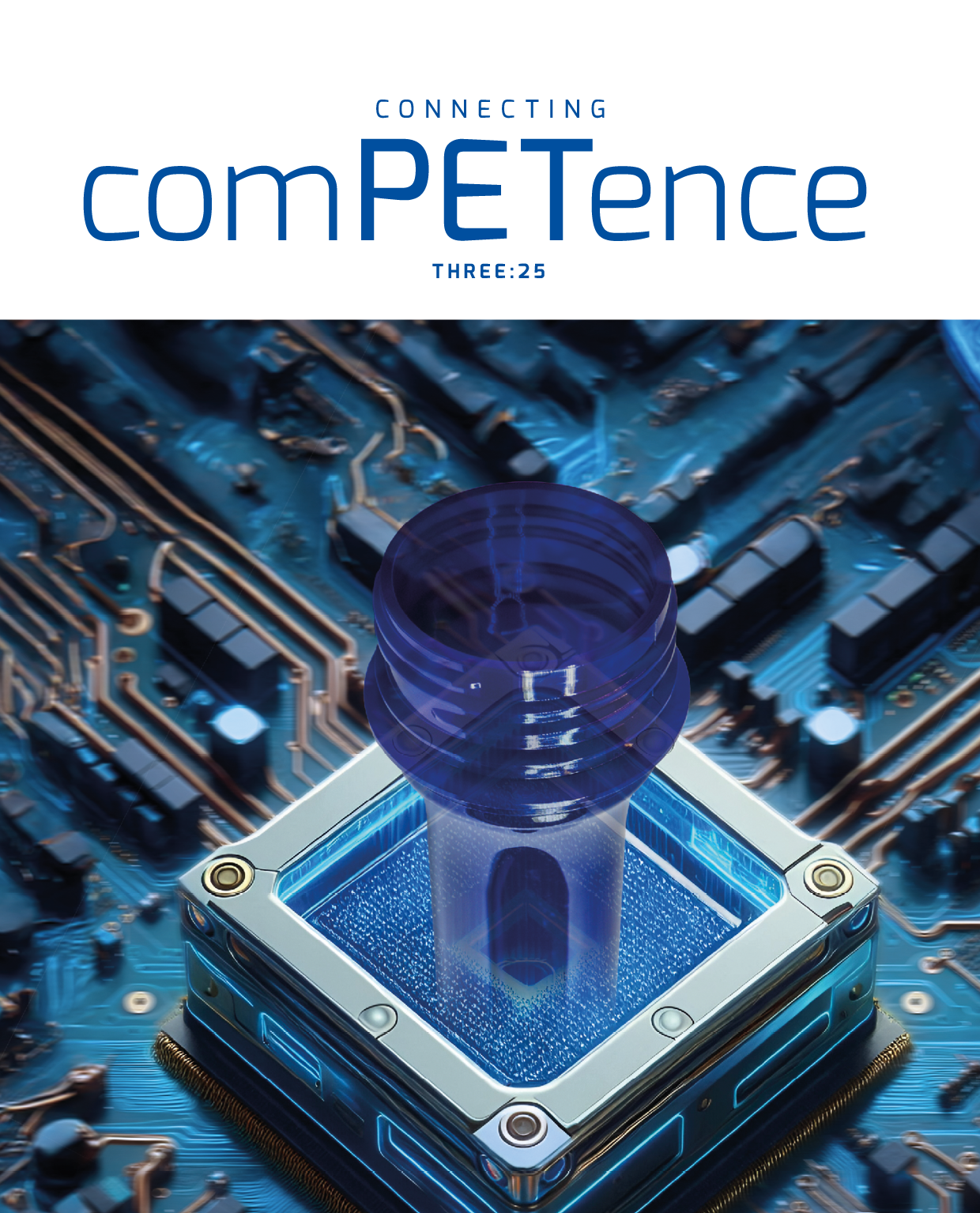
magazine
Find our premium articles, interviews, reports and more
in 3 issues in 2025.