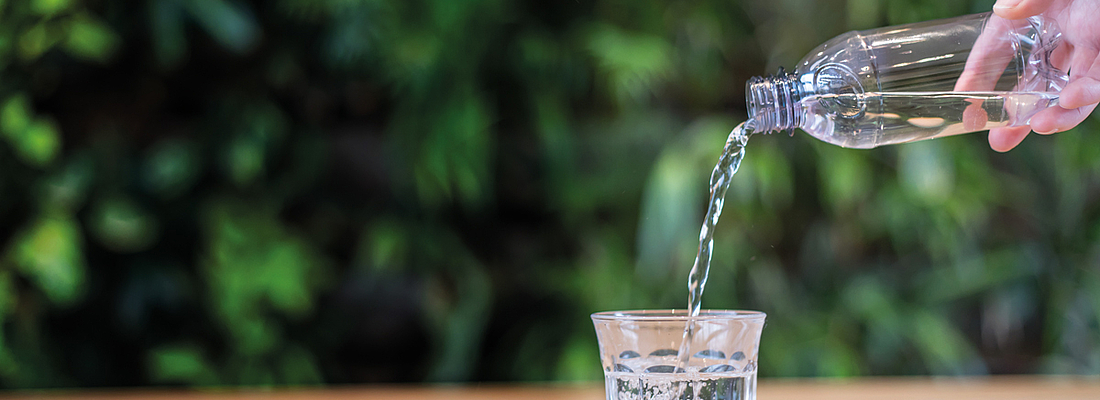
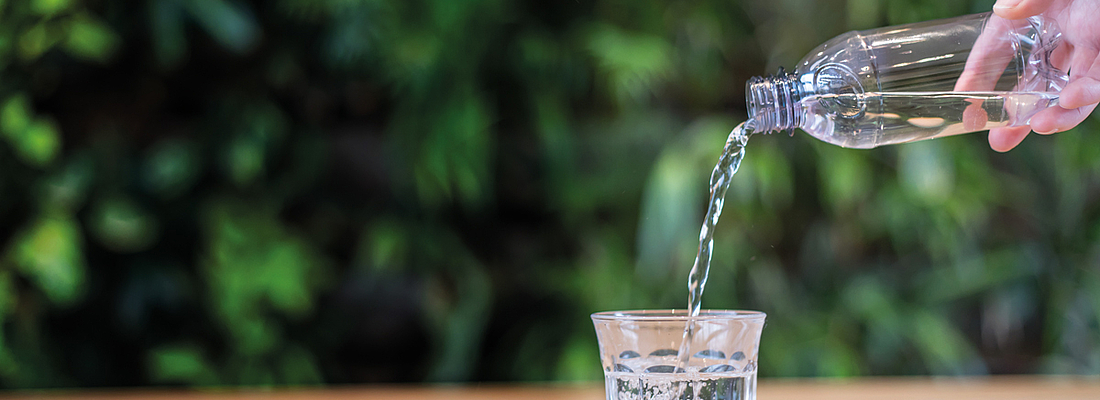
Photo credit: Avantium
A combination fit for future sustainable barrier packaging solutions
PET and PEF
Poly(ethylene 2,5-furandicarboxylate) (PEF) has a barrier that is reported to be up to 19x better on CO2 /1/ and up to 10x better on O2 /2/ than that of PET. Therefore, PEF can applied as an alternative for incumbent barrier solutions. Besides the fact PEF is from renewable feedstock, PEF has favorable properties for recycling.
Recycling of barrier materials in the PET stream
The trend of moving towards packaging solutions that fit the circular model has become so apparent during the last years, it hardly needs any introduction. At the same time, there has been a strong increase in the demand for barrier packaging solutions. Barrier layers and -additives can be very effective in improving CO2 or O2 barrier for rigid or flexible PET packaging. As such, these developments can result in dramatic weight reduction; the foremost important driver in a sustainable circular approach. However, the barrier materials that are currently commercially available can encumber or even obstruct recycling of such packages and us such true circularity.
Poly(ethylene 2,5-furandicarboxylate) (PEF) is a bio-based polyester with a known good barrier performance /1/ /2/. As such it can compete with commercially available (passive) barrier materials such as MXD6 and EVOH. One of the drawbacks of using these existing barrier materials is that they typically have poor compatibility with PET, resulting in poorer performance of resulting resin blends. Therefore, there is a need to have proper separation of the barrier layer from the recycled PET stream, for example by flaking (with the aim to delaminate the barrier layer) and subsequent sorting. When applying a passive thin barrier layer the latter case, converters need to balance between easy delamination of the barrier layer from the PET and the performance of the multilayer article during its use. Data published on bottles made of blends with PET and PEF /3/, suggests that PEF would not necessarily need to be separated from the PET stream as it hardly influences the processing behavior of recycled PET and its performance in bottles. Additional studies have led to an interim approval by EPBP of PEF to enter the European PET bottle recycling stream at up to 2% of the total volume of that recycling stream /4/.
A recent article on the miscibility of PET and PEF /5/ indicates however that PET and PEF blends are not intrinsically miscible. It is important to mention that the blends for this study were prepared by first dissolving both polymers in a solvent and subsequently mixing these solutions (solvent mixing). This method prevents any transesterification to occur. Only during DSC measurements, the resulting blends were shortly brought in melt, then quenched and subsequently a heating ramp was applied to determine the glass transition(s) in the enthalpic data. The resulting DSC traces show that for these PET/PEF blends the time in melt (without the presence of shear) was not sufficient to allow for transesterification, leading to a blend with phase separation between PET and PEF. Apparently, the transesterification of PET and PEF requires more time, and possibly shear, to fully take place, leading to a PET/PEF co-polyester with only one glass transition as observed in the previously mentioned study on bottles made from PET/PEF blends /3/. In the latter study, the PET and PEF are dry blended and subsequently injection molded into preforms. Obviously, this latter procedure allows for more transesterification, as the residence time in melt is longer. An actual bottle-to-bottle mechanical recycling route will allow for even more transesterification as this procedure does not only include an extrusion step, but also a solid state polymerization in addition to the injection molding step. Therefore, only an injection molding step is a worst case estimate of the amount of transesterification that can take place. Here, some additional PET/PEF blend data as produced by dry blending and injection molding will be presented, supporting the statement that PEF is a bio-based barrier solution that can enhance the recyclability of (multilayer) barrier containers.
Injection molding of blends
The mixture of PET and PEF was fed predried and dry blended into a Boy 50M injection molding machine at 170°C. The resin was molded into 76x76 mm2 plaques with a nominal thickness of 1 mm and a shot weight of about 13 g. The molding parameters were kept constant, with a melt temperature of 280°C, injection time of around 0.6 s and total cycle time of 24 s. The resulting total residence time of the polymer melt in the barrel is estimated to be 5-9 minutes, while the mold was kept at 20°C. Other than the injection pressures, no significant differences were observed during molding the plaques from the different blends. In addition to the PET and PEF blends, a PET and MXD6 blend (at a ratio of 95/5 wt%) was molded. Visually, there is a clear difference between the different blends as seen in Figure 1 (top), showing in transparency the logo and caption through 4 plaques of 1 mm thickness stacked.
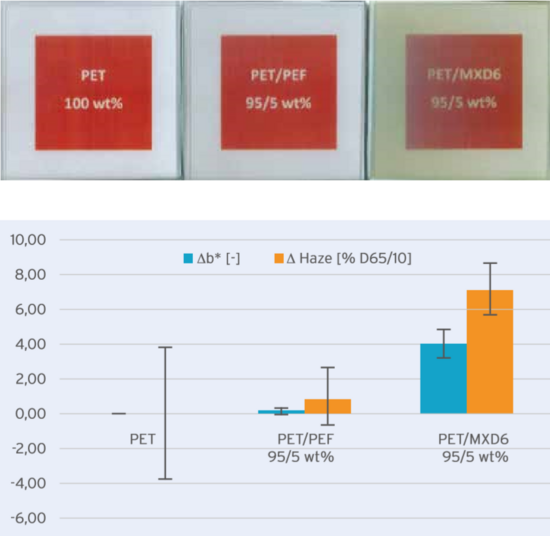
Fig 1: Visual appearance of 4 stacked 1 mm thick plaques of different compositions on top of printed paper (top) and average and standard deviation (error bars) of DELTAb* and DELTAhaze from direct color measurements on 5 plaques (bottom). Each composition was compared with the average value of 100 wt% PET.
A relatively high haze value for the 100 wt% PET control was found, which is probably due to the texture on the mold surface (Ra value is 0.4 µm). This roughness is the same for all the samples and therefore, only the differences in haze between the blends and the pure PET plaques are reported in Figure 1 (bottom). The results clearly show that PEF has a much lower b* and haze buildup than the MXD6 blend. It is worth noting however that blends of PET with MXD6 had much lower haze than plaques made from PET with only 1 wt% of PLA. For these plaques the Dhaze was found to be 44%; historically one of the reasons why the introduction of PLA in the bottle market was not successful.
The mechanical properties of the plaques made from the different blends were measured with a TA instruments Discovery 850 DMTA at an oscillating strain of 0.1%, a frequency of 1 Hz and a temperature ramp of 1°C/min. The resulting storage moduli as a function of the temperature are shown in Figure 2.
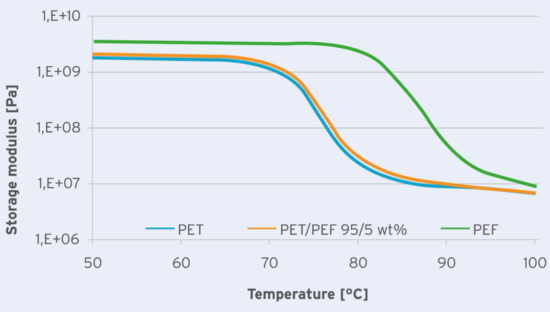
Fig 2: Storage modulus versus temperature as determined from DMTA measurements at an oscillating strain of 0.1%, frequency of 1 Hz and temperature ramp of 1 °C/min for PET, PET/PEF 95/5 wt% and PEF.
From the trace it is clear that the plaque made from the PET/PEF blend has only one phase, resulting in only one glass transition with a value in between that of PET and PEF. The 5 wt% PEF blend only has a marginally small difference in mechanical behavior in the blow molding temperature window, supporting the observation that the blowing conditions of PET/PEF preforms do not differ much from pure PET preforms /3/.
Bottles made of blends
The influence of blending a barrier material into PET on bottle performance was assessed by producing a small (12 oz/355 mL) generic CSD shaped bottle containing 5 wt% PEF or polyamide (PA). The most obvious difference in bottle properties is the appearance as is visible in the photograph in Figure 2 (top): whereas the PET+PEF blend bottle remains virtually haze free, the PET+PA blend has a clearly visible haze. The difference in compatibility also becomes apparent in other bottle performance as listed in the table below Figure 3. The PET+PEF blend bottle performs on par with PET and actually has a bit better CO2 shelf life performance (in line with the previously cited study /3/).
However, the bottle containing 5 wt% of PA does not pass the CO2 barrier test as the bottles burst during the shelf life tests when pressurized at a 4.2 CO2 gas volume.
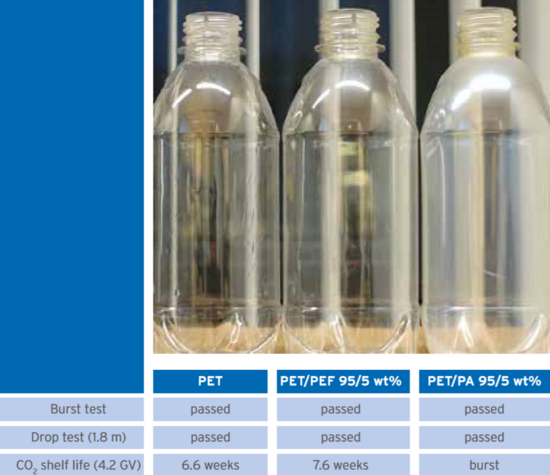
Fig 3: Bottles blown from preforms containing different blends with PET as base material. From left to right: PET, PET+5 wt% PEF and PET+5 wt% PA. The table below the picture contains performance data of the bottles made from the different dry blends.
Conclusion
When PEF enters the PET recycling stream in larger quantities (in the percents range), it hardly has any effect on the color and haze of the products made from the polymer coming from a mechanical recycling loop. This is a unique value proposition of PEF when compared to incumbent barrier materials and as such makes it a very interesting material to support the development of sustainable (multilayer) barrier packaging.
Acknowledgements
The support of ALPLA in the preform injection, bottle blowing and bottle testing is greatly appreciated
/1/ Burgess et al. Macromolecules (2015), 48, p2184-2193 doi:10.1021/acs.macromol.5b00333
/2/ Burgess et al. Macromolecules (2014), 47, p1383-1391 doi:10.1021/ma5000199
/3/ Duncan and Fagan WO2016/200653A1
/4/ https://www.epbp.org/download/319/interim-approval-synvinas-polyethylene-25furandicarboxylate-or-pef
/5/ Poulopoulou et al. Polymers 2020, 12, p225; doi:10.3390/polym12010225
The comPETence center provides your organisation with a dynamic, cost effective way to promote your products and services.
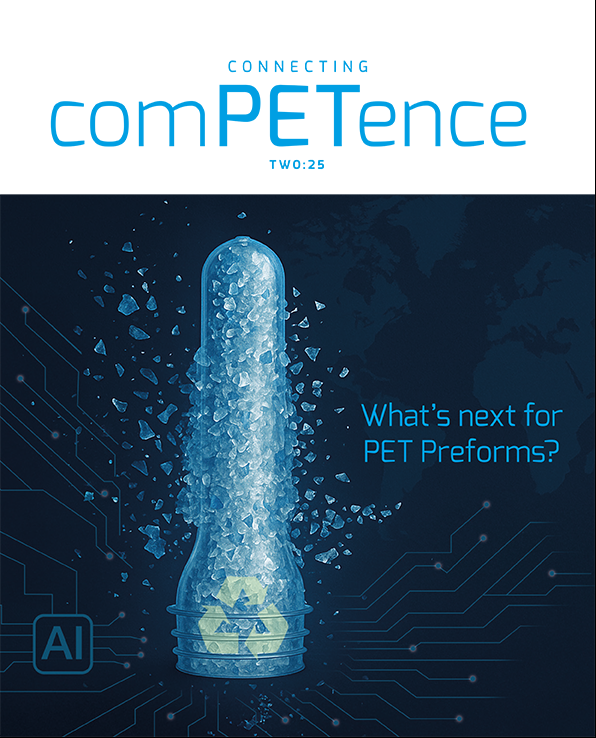
magazine
Find our premium articles, interviews, reports and more
in 3 issues in 2025.