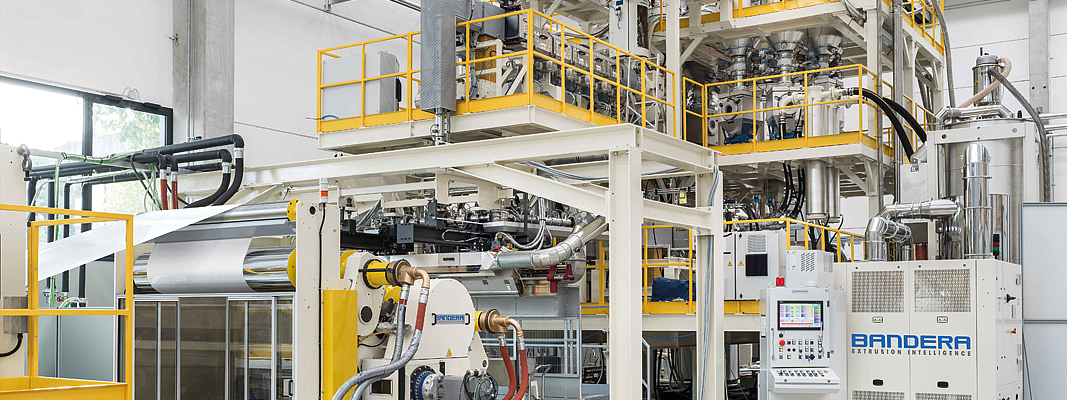
Bandera has developed innovative technologies for the rigid packaging sector and, specifically, for the PET sector. In the past 20 years, it has become one of the undisputed leaders in this sector, with nearly 300 extrusion lines supplied and operating at the major converters’ worldwide.
The success of the direct extrusion system, with the highly vented co-rotating twin-screw extruder is unequivocal. It has allowed the development of the market by suggesting a simple production process, with a low energy impact, avoiding old traditional pretreatment processes.
Thanks to the strong market pressure to regenerate post-consumer bottle PET and supply top quality bottle flakes, this market developed quickly, through the adoption of increasingly performing regeneration processes.
rPET has become an ‘opportunity’ and the circular economy has represented a model of growth for Bandera, in a sector where PET is appreciated for its good packaging characteristics, such as high transparency and resistance, along with easy identification as a product derived from recycled and recyclable materials.
In the past five years, technological evolutions have led Bandera to focus on new challenges. This has contributed to placing it among the top manufacturing companies producing top quality extrusion lines, not only for the packaging sector, but also for other sectors.
Both an efficiently performing extrusion section and effective downstream units are fundamental in obtaining a top line productivity.
For this reason, Bandera has pursued various different actions. The latter actions have initially involved significant R&D efforts and, subsequently, also a lot of industrial testing at the THOE (The House of Extrusion), which houses a strong wet trial running activity by Bandera at its headquarters, since 2015. Bandera often cooperates with the major converters in the sector in carrying out all of these activities. Specific NonDisclosure Agreements protect the confidential nature of the technological work and achievements, as well as the information shared.
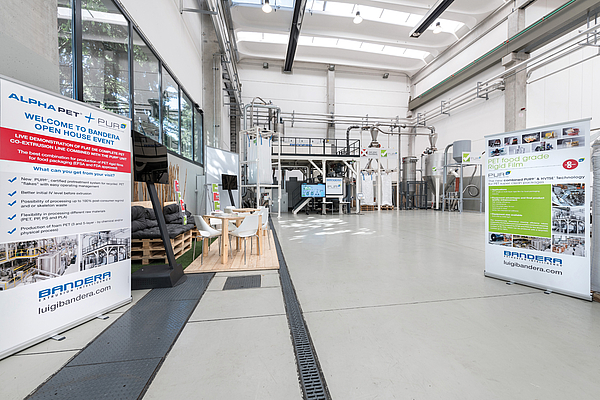
The results achieved are impressive:
- Definite top levels have been reached in the research for lightweight packaging, by improving the foaming of internal layers, lowering the specific weight of opaque multilayer films;
- processes to increase functional layers have been developed, cutting down on the costs of formulations and improving performances in the downgauging of technical films;
- the possibility of adding ennobling micronized mineral fillers, or specific master batches - possibly fluid, in order to characterize films in the subsequent thermoforming, form fill and seal or printing processes - has been improved;
- outputs per each single line have been upgraded, in order to optimize the consumptions per kg produced, while cutting down on waste products to the minimum, with an extremely accurate production efficiency (OEEE Overall Extrusion Equipment Effectiveness) in long term production cycles;
- the capability of extrusion lines has been increased, in terms of the necessary flexibility in transforming other recycled materials, either on a bio-degradable or bio-compostable basis, with no waste of time in switching resins;
- Increasingly safe and performing systems for film winding in rolls have been developed, tested and supplied; these systems are fully automated with a strong flexibility in covering both multi-reel and single-reel winding with maximum diameters.
- Moreover, the engineering of complete lines has been adapted, searching for leading PET applications that may prove effective in the regeneration of PET for applications other than food packaging (i.e. for the so-called NOBLE RECYCLING). These other applications are addressed to various industrial sectors, such as those of technical and sophisticated films for the furniture coating film sector (ultra-high quality), or for the synthetic flooring sectorfor using PET as a viable alternative to PVC or PP in other industries. Bandera also recently added new material PURIFICATION systems (before the extrusion process) to its own existing proprietary technology of the highly vented twin-screw extruders. This was done with the objective of fulfilling possible requests for production of single-layer films readily suitable for food packaging, in line with the EFSA and FDA Directives.
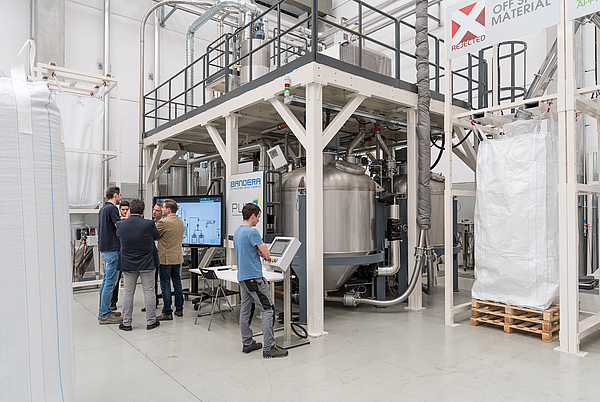
For the year 2019 and for next year, Bandera has several extrusion lines that will be operating during the first semester of 2020 and is concentrating on some very interesting projects:
- a 5-layer extrusion line with a net width of 1450mm, with thickness from 120µm to 1,6 mm, having the possibility of processing foamed materials, with possible mineral fillers, in-line, offcalender lamination system and semiautomatic winding station;
- a 3-layer extrusion line, with a net width of 1800mm, having the possibility of processing PP and PLA, besides PET, with a fully automatic winder for an output over 2,3 t/h;
- a single-layer extrusion line with the PURe pre-purification system, with a net width of 1050 mm, for an output over 1500 kg/h;
- a 3-layer, compact AGILITY LINE, with a net width of 900mm, for lot switching in processing quick production formats with highly boosted automation;
- PURe purification systems sized for an output of 800 and 1200 kg/h supplied for the upstream and combined with long, co-rotating twin-screw extruders already operating at existing customer sites.
Furthermore, for the whole second semester of 2019 and also for the whole year 2020, it will be possible to see and discover, at the THOE, an extrusion hardware dedicated to flat die technologies, representing the most advanced technological learning center for the packaging and converting industry. This center will also allow the development of new processes for PET - based films. In fact, such films are increasingly coated or co-extruded with further ennobling films. Above all, this center will allow the search for processes to comply with the demand for RECYCLABLE SINGLE MATERIAL USAGE, which may combine various PET layers, with additives in the melt foreseen to enhance their characteristics of high temperature resistance or higher barrier.
Substantially, we are dealing with a completely new way of supporting converters in challenging objectives to obtain innovative products, sharing knowledge and innovation with investors.
This project (which will consist of a complete extrusion line with nine flat die extruders and an in-line extrusion coating section) will represent a precious instrument for the sector of applied research, on a dedicated extrusion line with an industrial scale output.
The event will have a great technological value and will be shared with the major players, by invitations on a one-toone basis, allowing them to take full advantage of its potential. A specific Non-Disclosure Agreement will protect all information shared.
The line dealt with is not just an industrial production island, but an effective Learning Hub, which will not only be suitable for testing the performances of the most recent structures and formulations for special films, but also, above all, with recycled materials such as PET and/or organic materials, in compliance with European Directives on circular economy.
This will be an INCUBATOR OF IDEAS for the industry of extrusion, recycling and packaging, following our motto, EXTRUSION INTELLIGENCE.
The comPETence center provides your organisation with a dynamic, cost effective way to promote your products and services.
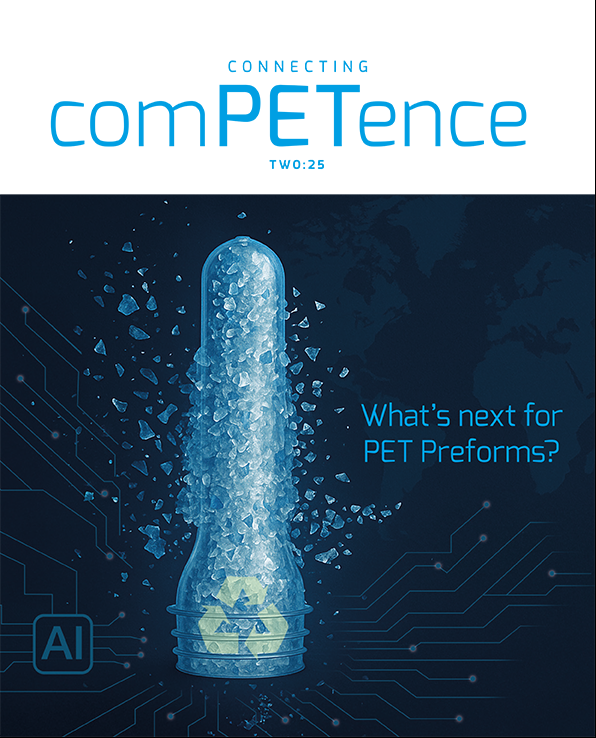
magazine
Find our premium articles, interviews, reports and more
in 3 issues in 2025.