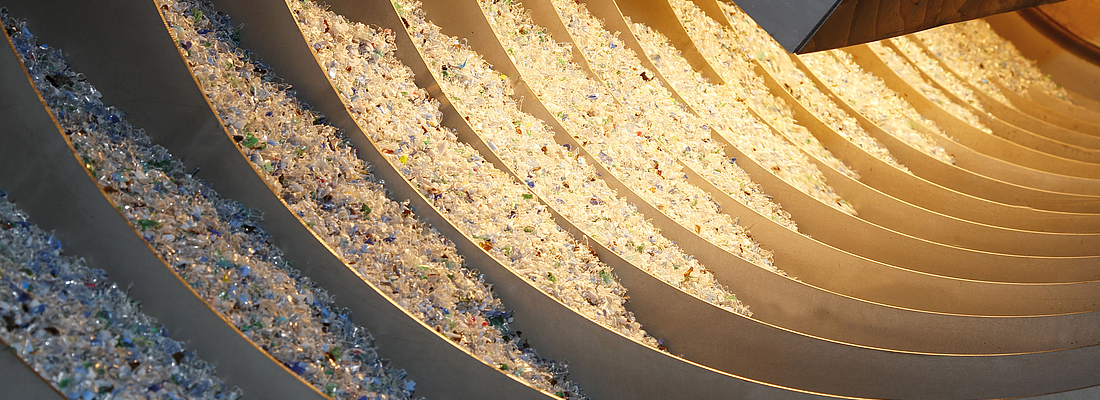
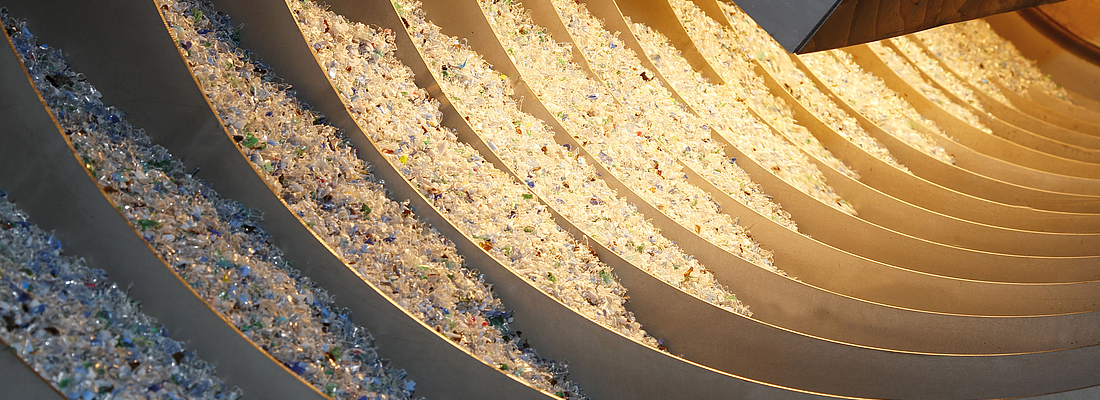
If Post Consumer Recycling Ware is to be processed directly in PET Film Extrusion, a process authorized by FDA or by EFSA is the latest solution today or will be an almost indispensable solution especially in future. With its IR-CLEAN System, KREYENBORG now offers an attractive alternative for the use of Post Consumer Ware – the direct decontamination without any kind of vacuum technology.
The focus in the development of the IR-CLEAN® was especially put on the requirements and general conditions of PET Sheet Extrusion. The experience made with IRD Crystallization and Drying Systems installed upstream of Sheet Extrusion Lines in many applications has shown that PET Post Consumer Recycling Material is used at 100% on rare occasions - this is revealed from the given circuit in sheet production, where edge trims and skeleton waste from thermoforming processes are regularly conveyed back into the extrusion process. These Inhouse Flakes are moreover often combined with a share of up to 30% PET virgin material, which is mainly used to stabilize the IV degradation in the extrusion process. In this way, the share in Post Consumer Flakes in sheet extrusion is reduced to partly less than 50% of the entire throughput. Further differentiation is also possible with respect to the products manufactured. The food packaging produced in the thermoforming process - usually salad or meat packaging - has a substantially shorter shelf-life and is partly subject to a cooling chain process. In this way, the relatively highly set limit values, as they are for instance needed for Bottle- to-Bottle recycling for Mineral water bottles, do not always apply.
However, recycling processes applied so far for the decontamination of the PET Flakes are in most cases based on precisely these technically sophisticated bottle-to-bottle processes in which, apart from the food contact suitability, a build- up of the intrinsic viscosity (iV) by Solid State Polycondensation (SSP) is required as well. The vacuum technology required for this process is quite expensive and calls for intensive maintenance with a substantial amount of equipment and facilities. As in PET extrusion, compared to preform manufacturing, substantially lower viscosities can be processed, the build-up of viscosity is virtually not necessary at all.
These special aspects in PET lm extrusion were consistently used in order to offer to the final users an effective, but nevertheless easily manageable and cost-effective solution which can also be used and retro fitted regardless of the extruder type.
OPTIMIZATION OF A WELL-PROVEN PRINCIPLE
The IR-CLEAN® is a process- technological optimization of the well- proven IRD Infrared Rotary Tube that has already been used successfully on many occasions. The standard process of crystallization and drying of PET Post Consumer Bottle Flakes in the IRD Infrared Rotary Tube has been modified by an adjustment of the process parameters - this has resulted in astonishingly good decontamination results, which have been proven in several Challenge Tests in collaboration with the Fraunhofer Institute IVV (Freising / Germany).
The key to the good results lies in the general functional principle of the Infrared Rotary Drum - the reduced mass in the process and the steady movement of the material ensure a permanent surface exchange of the recycling material to be treated. Just to give an example: only roughly 350 kg of material are located in the rotary tube in a 1000 kg/h process. At the same time, the material is completely circulated in the helical mount of the Rotary Drum up to 15 times depending on the geometry and is thereby conveyed to the surface on a permanent basis. Moreover, the spiral mount welded into the Rotary Drum guarantees a precisely de ned ow of material (First-in, First-out) - this is an important aspect regarding the process monitoring and documentation.
This excellent mixing behaviour inside the Rotary Drum now combines the IR-CLEAN® with the quick and direct input of heat by infrared radiation. The short wavelength halogen radiation allows achieving high temperatures within a few minutes only, because the material is heated up directly without any hot air. In this way, two of the most important criteria for the effective decontamination are fulfilled - surface and temperature. At the same time, the IR-CLEAN® basic concept needs no more cooling water or pre-conditioned process air and - above all - no more expensive and high-maintenance vacuum systems.
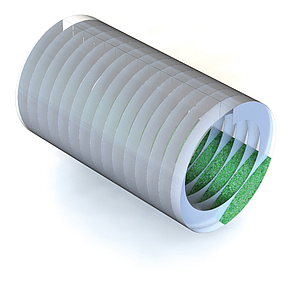
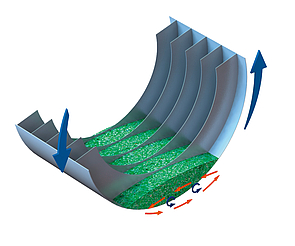
Fig 1: Internal helix of the rotary drum, in detail
IR-CLEAN® – EVOLUTION OF A WELL-PROVEN CONCEPT
Uncomplicated, effective and at the same time developed at low cost and precisely geared to the needs of the final user - this is the comprehensive understanding of the key features of the IR-CLEAN concept. All the more, the system performs this as an evolution of a well-established crystallization and drying technology, which already forms an interesting basis by a high amount of efficiency and flexibility. As the IR- CLEAN® represents a complete Super- Clean Recycling Process, it is above all attractive as a retro fitting solution for existing extrusion lines, but also as a low-cost and flexible alternative in new installations.
*additional FDA Petitions pending
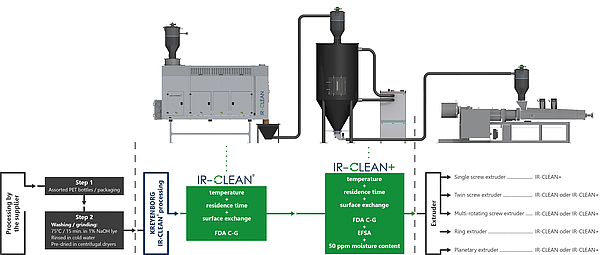
Fig 2: Process Documentation IR-CLEAN®
MODULAR CONCEPT ALSO AVAILABLE AS A RETROFITTING SOLUTION FOR EXISTING EXTRUSION LINES
The crystallization and drying concepts form the basic building block of the IR-CLEAN concept. If in the drying process, a differentiation is already made between the various residual humidifies required, the output may also be delimited in the Food Grade Process depending on the application. The IR- CLEAN® as a basic unit consists of an Infrared System alone and achieves, with a residence time of clearly below one hour, the limit values required by the FDA in one process step*. The residual humidity of < 300 ppm achieved at the same time is also completely sufficient for multi-screw or single screw extruders including degassing. If any lower limit values are required as for instance partly by the European EFSA, the system may be extended with a Finisher mounted downstream towards the IR CLEAN+ System. This extension consists of an additional drying hopper with a dry air system which primarily helps extending the residence time under high temperatures. This helps to reduce the residual quantities for contaminants with high boiling points such as benzophenone, and delivers as a side effect drying values of < 50ppm. This post-conditioning procedure can still be kept very short with a total residence time of 1.5 hours. Analogously to the IRD drying system, the entire energy consumption is reduced by up to 30% as compared to conventional systems. The reason for this is the fact that the material that has already been pre-dried and perfectly preheated by the IRD will be forwarded to the second drying or decontamination step, which allows minimizing the quantity of air and the heating capacity in the subsequently dryer / finisher substantially.
Both IR-CLEAN® variants achieve the values relevant for the FDA / EFSA already without taking into account the extrusion process, so that its retro fitting in existing singly-screw, twin-screw or multi-screw systems is possible without any problems. Apart from the conveyor technology, filtration units and demisters, the package developed by KREYENBORG also includes a comprehensive control package for the complete process monitoring including the documentation of the process parameters.
RESULTS OF THE CHALLENGE TESTS
The original material used for the Challenge Tests was a commercial PET bottle flake that was deliberately contaminated with defined model contaminants (surrogates). These prepared flakes were subjected to a commercial washing process (15 min. at 75 °C with 1% of caustic soda) and were then rinsed with cold water and mechanically pre-dried. This washing process forms part of the recycling process to be observed, but is also already ensured by the Supplier of PET Flakes.
The washed flakes were treated in the IR-CLEAN process, then analysed and finally subjected to a migration evaluation. The results show a cleaning efficiency of the IR-CLEAN process, depending on the surrogate, of 96 to 99%. A Letter of Non-Objection by the US Food+Drug Administration FDA was issued on the basis of these values, which confirms the harmlessness of the use of packing material with a 100% R-PET share under the criteria C-G (see table) already with the basic module IR- CLEAN®.
The results may also be used for the limit values determined by the European Authority for Food Safety EFSA. For the evaluation, however, the EFSA presumes a use of the packing material of 365 days at 25 °C, which is for example equivalent to a PET bottle of mineral water. On the other hand, the EFSA evaluation also makes a differentiation regarding the consumer and makes a distinction between admissible limit values for babies, toddlers and adults.
With regard to the later application, however, specifically the enhanced approach was selected, according to which thermoformed trays from PET Sheet Production are usually subject to other conditions of use than PET Bottles. Based on a typical use or the storage of a food package for e.g. meat products of max. 30 days at 6%, up to 100% of PET recycling material may be used from the IR CLEAN+ process for all scenarios.
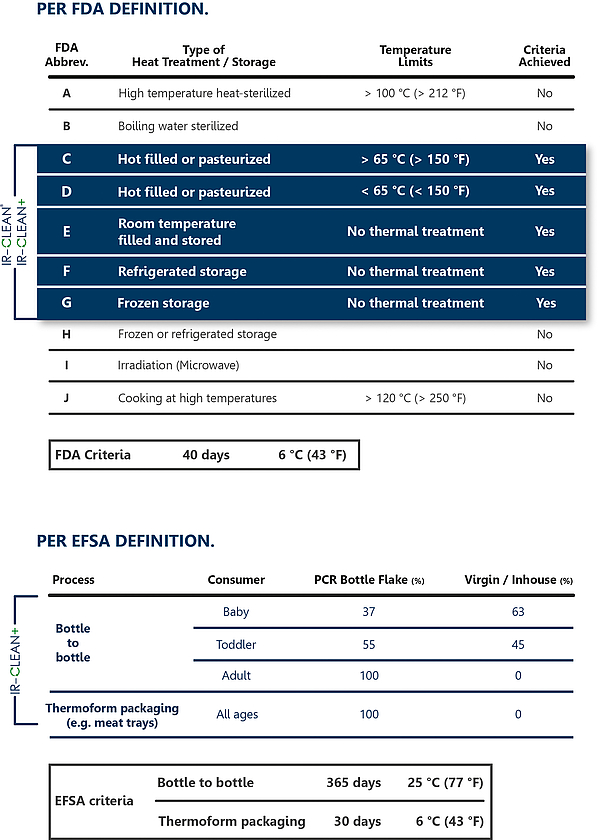
Tab. 1: FDA & EFSA Approvals
The comPETence center provides your organisation with a dynamic, cost effective way to promote your products and services.
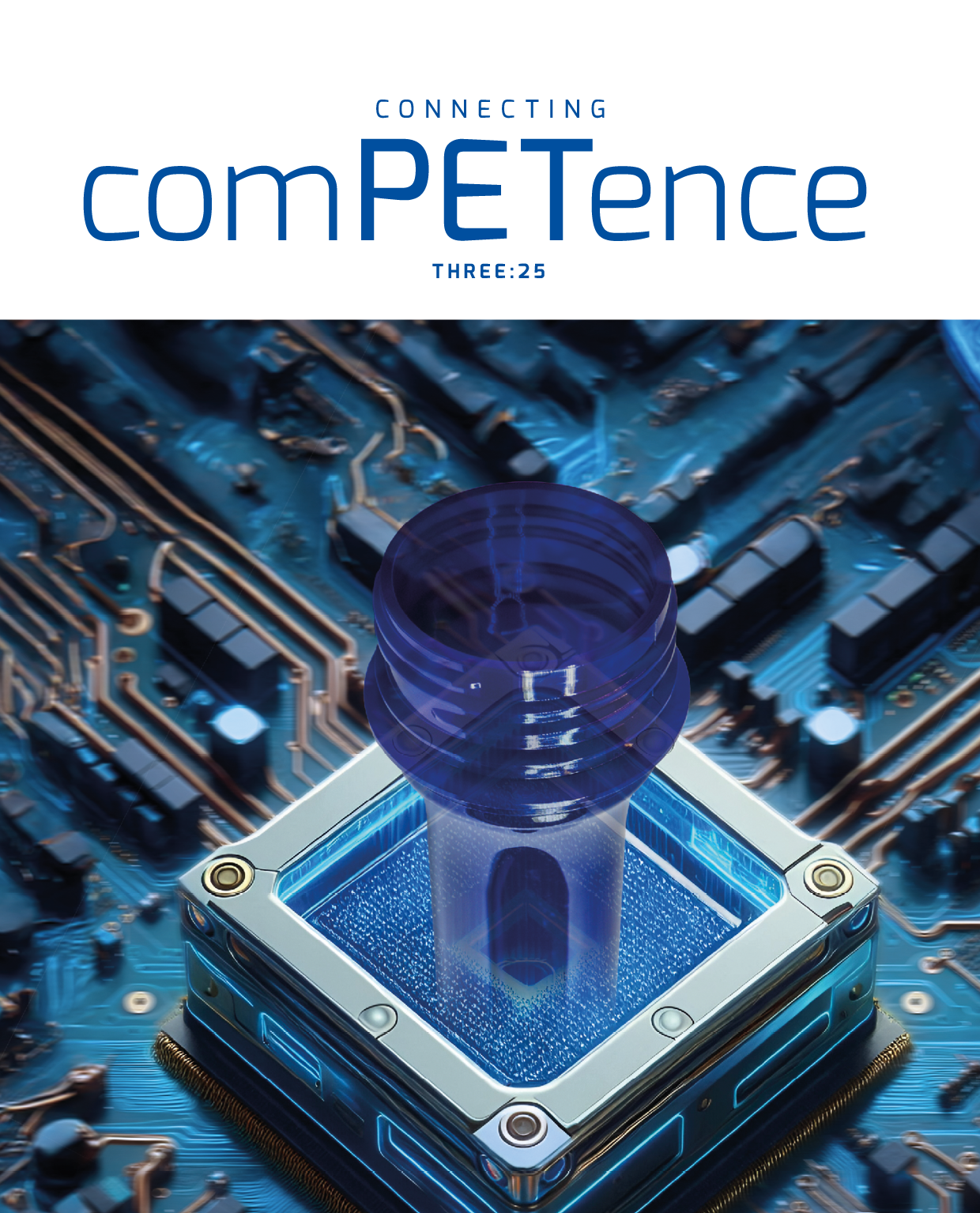
magazine
Find our premium articles, interviews, reports and more
in 3 issues in 2025.