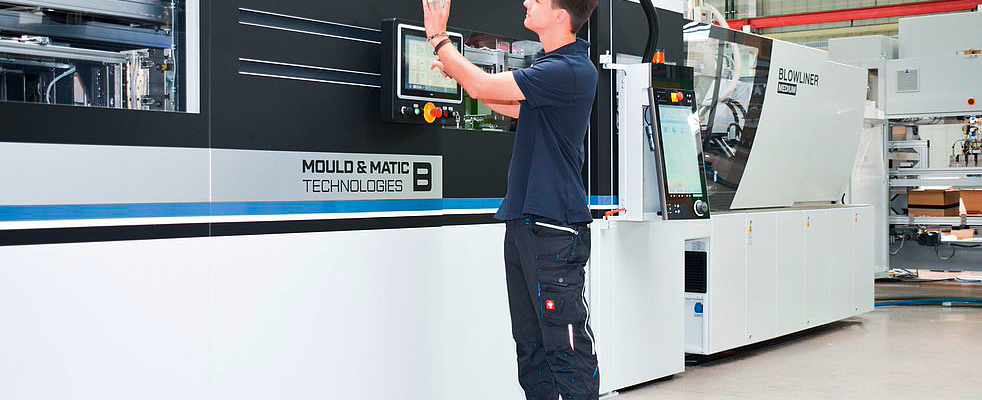
With the development of the Blowliner, the single-stage injection-stretch blow- molding machine, Kiefel’s daughter company Mould & Matic has opened up a new market. Bernhard Hornhuber, sales manager for blow molding technology, developed the Blowliner and is justifiably proud of his baby: “Customers really appreciate the fact that they get the extremely space-saving line completely from a single source - from granulate to packaging.”
The Blowliner is available in three sizes. The line processes PET, PP, HDPE and, thanks to its intelligent concept, can be upgraded to multi-layer applications at any time. Above all, the premium sector, which attaches importance to high quality and transparency of packaging in medium quantities, appreciates the 1-stage system. Hornhuber gets to the heart of the reasons: “Our customers need the flexibility to produce different containers with volumes between 10 milliliters and 5 liters on the same machine. The Blowliner fulfills all of these wishes and thus contributes to sustainable high plant utilization at our customers.”
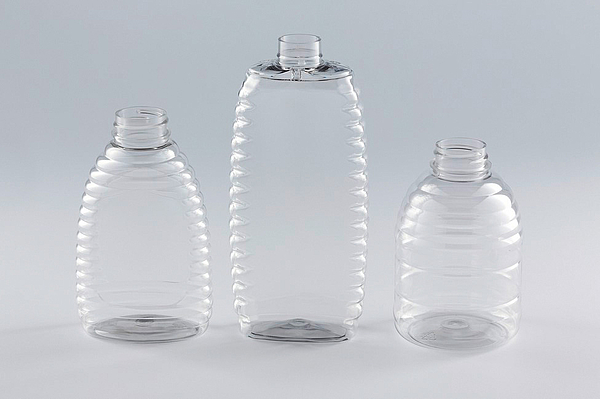
FOCUS ON THE PROCESS
The injection molding unit, a vertical hydraulic Engel machine, is at the beginning of the linear machine. Here the preforms are created; depending on the product these range from eight to 64 cavities. Still warm, they are removed by a linear robot with a gripping mandrel and the preforms are transferred to the stretch-blow unit. The machine works with one to four-rows blow tools that accept preforms with diameters from 10 to 150 mm. Each series of cavities has its own pre- and main blow valve so that the pre- and main blow pressures can be set individually. The entire stretch-blow unit has servo motor drives that provide exact repeatability, precision and energy efficiency. At the end of the blowing process, the vacuum gripper of the integrated linear unloading system removes the finished products from the tool and places them precisely on a conveyor belt or directly in boxes.
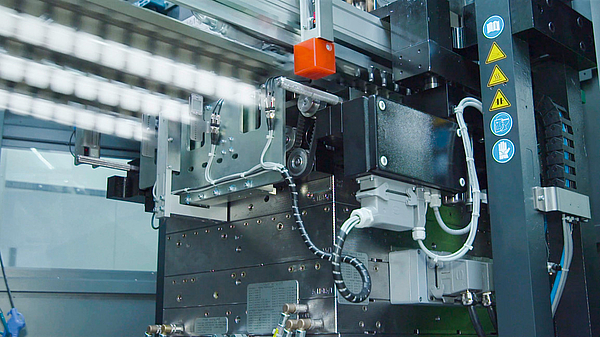
PRODUCTIVITY INCREASE
Many considerations owed into the tool technology during the conception of the Blowliner. Hornhuber recalls: “Our goal was to increase the number of cavities and thus productivity with additional optimized cycle time for existing plants. It should be possible to use the hot side of the tool to manufacture very different products in terms of size and thus number of cavities.” The solution lies in a balanced hot channel tool with a needle lock system. This provides the capacity for different product sizes and tool configurations. The Blowliner M permits cycle times of ten seconds, the little brother Blowliner S can even manage less than eight seconds.
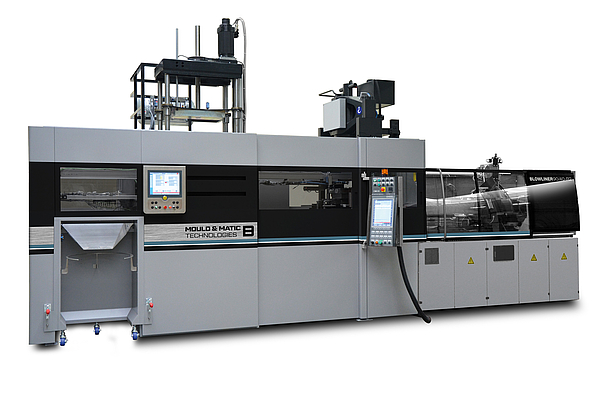
The comPETence center provides your organisation with a dynamic, cost effective way to promote your products and services.
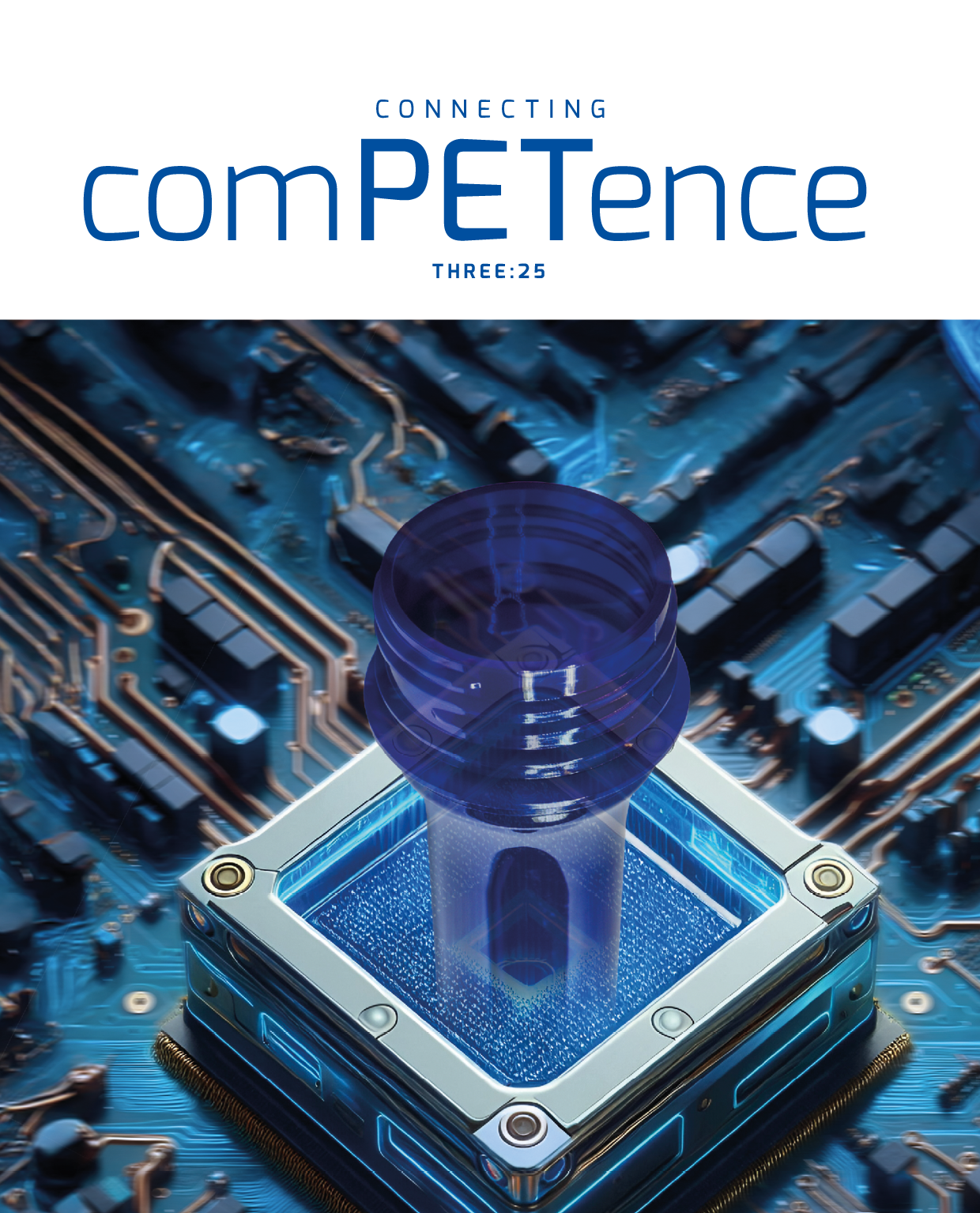
magazine
Find our premium articles, interviews, reports and more
in 3 issues in 2025.