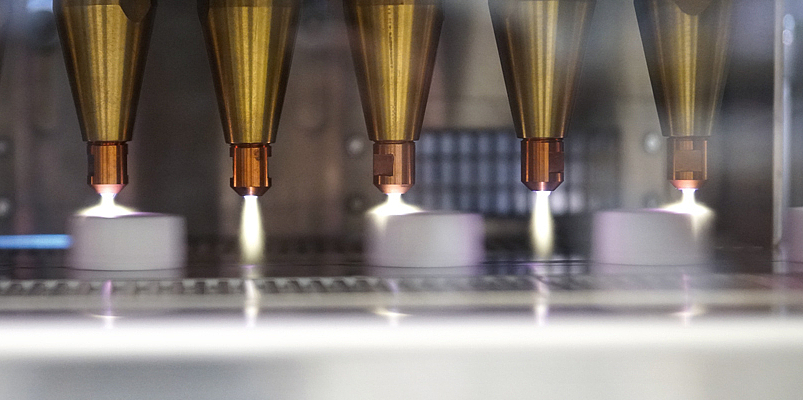
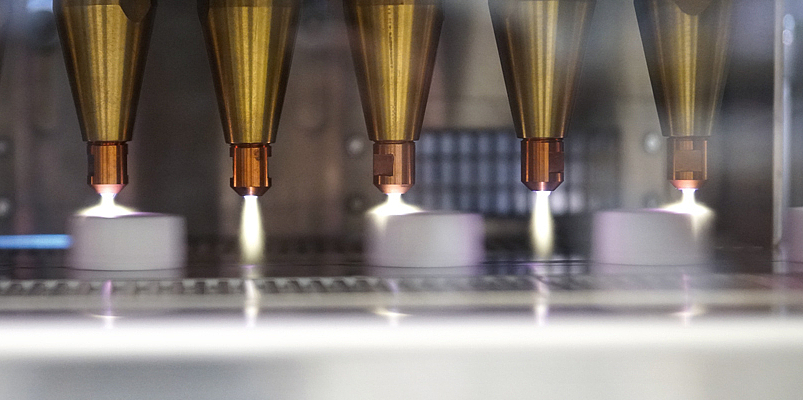
Printing has always intrigued humans — both the printed medium and the technology responsible for it. From preserving and sharing stories and information to advertising products and publicising incentives to buy, printing serves many purposes, even in a time when digital media are shaking up the market with their disruptive innovation. Even today — perhaps especially today — a printed book, photo collection or magazine is something special for a lot of people, something they enjoy holding in their hands. What would Gutenberg find interesting about modern printing technology? What would challenge him if he considered the technical, financial and marketing aspects? What would he say and what inspiration might he draw when he found out that we can print on media other than just paper — packaging, for instance?
Printing on packaging
Printing on packaging is an already established process, typically performed using mechanical techniques such as pad printing or dry offset printing.
Digitally printing packaging units such as bottles or caps is still a new, innovative technology in comparison. It does offer great potential; however, there are some hidden challenges in regard to production, technology, techniques and costs.
- Production potential: new manufacturing processes made possible
- Technological challenges: material, inks, pre-treatment, migration, recycling
- Technical challenge: positioning at high speeds • Financial challenge: marketing at what price?
Production potential
Today, caps are primarily printed where they are manufactured. They are injected into a mould, formed, inspected, sent to storage and later retrieved to be sent to the printer, where a feeding system positions them on a sort of needle, predominantly for mechanical printing. Setting the cap on the chuck is a delicate procedure, as the cap could suffer damage. It is important to avoid such damage both for the sake of sustainability and because damage to a product in the refining stage of the process chain can be quite costly. The printed caps are then either returned to storage or transported to the customer/ filler, who also keeps them in storage until they can be fed to the capper in the filling line.
What is different with digital printing?
In essence, the workflow remains the same with digital printing processes. However, depending on the process, digital printing offers some interesting alternatives and the potential for optimising filling lines in production. Today’s high performance standards are particularly impressive. Up to 90,000 caps can be individually printed per hour.
This has the following advantages for production:
- Simplified storage: Only non-printed caps are stored.
- Flexibility: Simple adjustment of the printing equipment enables quick changeover including to other cap sizes.
- In-house production: Printing can be integrated into the filling line just before the capper. The cap can be adapted inline to a given bottle or filling product.
- No need for warehouse storage: At high outputs, it can even be advantageous to produce, print and inspect the caps directly inline together with filling.
Technological challenges
First and foremost comes the protection of the product, the packed material. Preventing contamination and migration is a must, requiring the coordination of physical and chemical factors. This refers to ink quality, ink polymerisation and curing, surface activation and composition for ink adhesion, migration, and the ink’s scratch resistance. No foreign substances may be introduced into the contents of the bottle that are harmful to health, cause any unacceptable change in the product or have an organoleptic effect on it (affecting sensory properties such as taste, smell, colouring, etc.). The point of contact between the ink and the plastic surface must be perfectly polymerised. UV-polymerised ink fulfils these requirements, but non-polymerised ink does not. The other important aspects are recyclability and sustainability. What impact does the ink have on the closedloop material cycle and the recycling process? How does its carbon footprint compare to that of mechanical printing?
Technical challenge
Top-speed digital cap printing technology creates challenges when it comes to control and regulation — to correctly positioning the caps so that the flying ink droplets land where they are supposed to.
Financial challenges
System costs drive advances in printing techniques and technology. The higher machinery costs, in comparison to established mechanical processes, can only be compensated by reduced operating costs — less downtime, shorter changeover times, considerably greater flexibility in cap formats and printing, lower costs for storage, logistics and personnel, etc. This is the key to a higher return on investment.
What if...?
What if caps were no longer dyed and bottlers just used a singular base colour, individualising the caps using printed motifs instead? Would that lead to greater sustainability? It would certainly no longer be necessary to change colours in the injection moulding machine during production. It would also be interesting to know whether dyed or printed caps are more environmentally friendly, or which one can be better recycled and leaves a smaller carbon footprint.
If that piques your curiosity, have a look at the in-depth article on digital cap printing technology by Matthias Hermle and Cédric Simon of IMD on page 66 .We put these questions to Matthias Hermle, CEO of IMD, as the spokesperson for the team which developed this new technology.
Inspection Technology Leading the Way Toward Digital Printing Technology: An Add-On Made Possible by Combining Skillsets
- The Interview -
CC: IMD is practically synonymous with inspection. How did you decide to dedicate yourselves to digital printing?
It was more or less random. It started with a discussion with Beat Rupp (former CEO of Hapa, current CEO of PackSys Global) where I found out a little bit about the speed of the printing process. We were talking about blister printing, so it didn’t even have anything to do with beveragerelated technology. I saw a product in my mind’s eye which we inspect with our machines: caps. It quickly became clear to me that at a speed of 60 m/ min, we could print 1,500 pieces per minute — or 90,000 caps every hour. In this performance range, digital printing can be carried out directly after the injection moulding stage. Of course, the next thing we asked ourselves was: Can cap inspection and printing be coupled? Can both steps be combined in a single machine? They both require the caps to be properly positioned, so it could be quite advantageous.
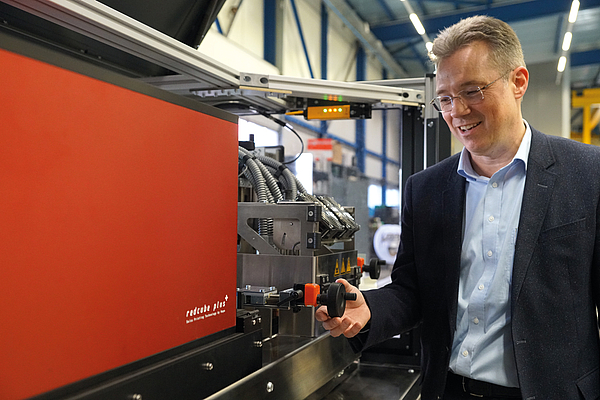
CC: What were your initial concerns?
We spoke with many experts as well as with our own experienced people and asked them for their opinions. And they were unanimous: the issue is adhesion. It seemed like it would be difficult to prevent the printed ink from falling victim to the slip additive — we assumed that the additive would strip away the colour from the cap. The problem seemed insurmountable, since so many others before us had failed. But we simply gave it a try anyhow by bringing all the specialists together. And looking back, it holds true that innovation emerges when you least expect it, as was the case for us.
CC: So it quickly became clear that you were on the path to success?
We learned that in many ways, digital printing cannot be compared with the mechanical printing process. We had to go a different route. In the beginning, we did run into a number of problems which we hadn’t seen coming, but which are inevitable in the face of such an adventure. I remember that the greatest challenge was getting the ink to adhere to the surface of the plastic material — it could be washed away by a jet of water. Optimising this devoured a lot of time, but it was worth it, as proven by our IMDvista Closure Digital Print System (CLDP). Now, the ink even stands up to the requirements of aseptic fillings, as tested in our laboratory with a specially designed inspection process.
CC: Machinery, control and inspection is one thing, as you know, but surely ink is another. With the new IMD machine, you’re no longer just inspecting, but also producing. In other words, you have to deal with production materials. Are you also involved in developing the ink?
You’re absolutely right. Handling and inspection are our strong suits. We turn to our partner Hapa for the ink and ink handling needs as well as for controlling the print heads. Hapa develops the ink itself — for the pharmaceutical industry, too, for instance — so the people there know how to deal with ink used for highly delicate products. The basic formulation for ink suited to food industry applications was already there, and Hapa was already familiar with things such as water resistance and low migration. So they are an ink specialist, and we are a specialist in mechanical engineering and cap handling, well-versed in alignment and speed. Our collaboration was a match made in heaven, promising great success in food industry applications. And today, we have an exclusive deal with Hapa for this application.
CC: What’s special about the ink you use?
We use UV-curable inks. All these inks have an above-average pigment content so that minimal quantities produce maximum results. The opacity of our white e.g. is unsurpassed – meeting cover requirements in a single pass. When the ink reacts with UV light in the curing process, the monomers polymerise, forming a tough film. The results are high abrasion resistance and chemical resistance. It all starts with the ink, but for good adhesion everything has to come together: the ink’s dynamic viscosity, and its surface tension, which has to match that of the substrate.
Strictly speaking, the digital technology in question isn’t printing in the literal sense, because the ink droplet has a trajectory and lands precisely at its target destination on the medium which is to be printed, in four colours plus white (W-CMYK). This is how we manage to print 1,500 caps per minute (28 mm) — no mean feat. It’s certainly exciting and challenging.
CC: How is the print quality?
The best. We’ve got that down pat. We can print the finest lines, just 0.1 mm thick. And they adhere to the surface of the medium. There are really great macro photographs of this.
CC: Are the print heads specially developed by Hapa?
The print heads are standard modules. The special and exciting part is how they are controlled as well as the automatic ink handling, including supply, cleaning, flushing and conservation.
CC: Assuming the trajectory is correct and the “landing point” is hit, will the ink remain on the cap? Or, put differently, does the ink adhere reliably?
One core issue was the surface treatment. If you want to know if colour will hold to the surface you want to print, you have to wet the surface. Wettability describes the tendency of a solid to form a common interface with a liquid which comes into contact with it. One measure of wettability for a particular liquid is the contact angle. A wettability profile of a solid, known as the wetting envelope, can be created by determining the surface free energy. We learnt from experience that not only the Dyne value is important, but also the match with the ink. There was a lot we had to learn.
CC: Can the polymerisation — or the transformation of monomers into polymers — be measured?
We can use FTIR spectroscopy in the lab to measure precisely what percent of the solid ink still contains monomers which could migrate. Each ink is analysed and measured separately.
CC: What are the optimal conditions for digitally printing caps?
Contrary to the experiences we’ve had with mechanical printing systems, the outcome with newly produced caps is very good. Transparent caps are particularly suited to our technology since UV light also acts on the ink via diffuse radiation from below the cap.
CC: Looking at your digital printing system as a whole, what are the biggest differences to the mechanical printing processes?
Established standard systems require human intervention regularly, approximately every 15 to 30 minutes. This means readjusting and above all mixing the inks. The quality is therefore heavily dependent on the operator. I once heard from a customer in the US who gave up printing with a mechanical machine because he and his team just couldn’t get to grips with the process. It requires proper specialists with experience in ink handling and a hand for mechanics. Customers who use our digital printing technique will not run into problems like the one I just mentioned. Secondly, cap handling is a significant element of working with modern mechanical printers. As I said, it’s easy to damage the caps when positioning them on the mechanical mounts, the chucks. Now, we do sell inspection systems for inspecting whether or not caps are in good condition after printing — meaning free of damage — but from a business standpoint, isn’t that ... dumb? With our digital system, the caps cannot be damaged. And thirdly, even the gating point and domed or concave caps can be printed with our system — a considerable advantage from a marketing standpoint. What the new process could mean for marketing remains to be seen; it’s still early days.
CC: What applications is your system suitable for?
At the start, we expected that it would only be useful for custom applications and small-scale production, e.g. of specialty items. But today we believe that digital printing will become the new standard. Since it’s so simple and safe for producers, everyone who is already interested in printed caps but has reservations about the associated difficulties will be printing themselves in the near future. Admittedly, the acquisition costs are around twice as high as for standard printing processes, but when you crunch the numbers and factor in all the advantages, digital printing will still prevail — not least because the printing process can be integrated into the production line. Think about it for a moment. If you have a machine capable of printing everything from PCO caps to push-pull caps to caps used for agricultural purposes, combined with short changeover times of just a few minutes, then the storage capacity needed can be drastically reduced, depending on the project.
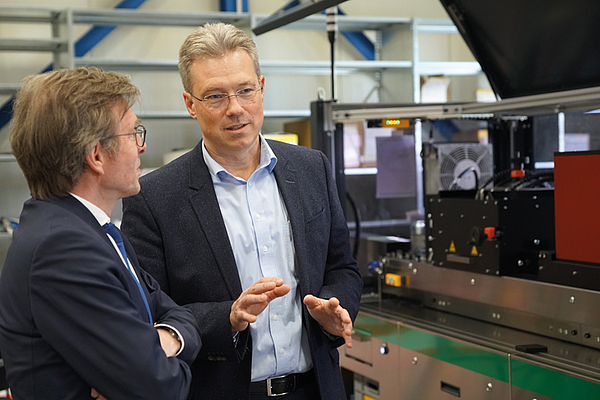
CC: What is your market approach?
We are currently introducing five machines on the market. We first want to gain experience and learn from this initial launch so that we can then enter the main market with a stable product. Things will really take off once brands and bottlers have recognised all the benefits — the flexibility, the simplicity and the potential for production optimisation. Not to mention the integration of the machine, and with it the printing process, into the production line.
CC: What if caps were no longer dyed and fillers just used a singular base colour individualising the caps using printed motifs instead? Would that lead to greater sustainability? And what would be more environmentally friendly — dyed or printed caps? Which one can be better recycled and leaves a smaller carbon footprint?
This is a complex question. We at IMD have developed a new innovative way of individualizing closures. This possibility was for us in the foreground. New possibilities, new production processes only arise when innovative ideas for new products are implemented. We will see the impact of digital printing of closures in the capacity range of up to 90,000 caps/h on the process and production technology of filling lines. We are not able to at this point of time to talk about the mentioned comparisons concerning recycling and CO2 footprint. That’s where we depend on analysis, that’s not our core competence, but I’m assuming that these kind of datas will soon available. But, you are right, about these challenges and goals, all developments must be measured.
CC: What ideas do you have in mind about marketing and individualization?
We must continue to develop and we will continue to communicate the new possibilities of marketing through the digital printing of closures. You can print almost anything on a closure, from simple logos to high-gloss images. Even “serialized” printing is possible. That is, you can print x different printouts in succession. Think of sporting events, sports clubs, music, etc. in this context, the closures can become collectibles. You can react quickly and create unique pieces by loading only one new parameter set - the bottle, the brand comes immediately on the market! I believe we are still at the beginning of great opportunities under marketing aspects.
CC: Thank you.
The comPETence center provides your organisation with a dynamic, cost effective way to promote your products and services.
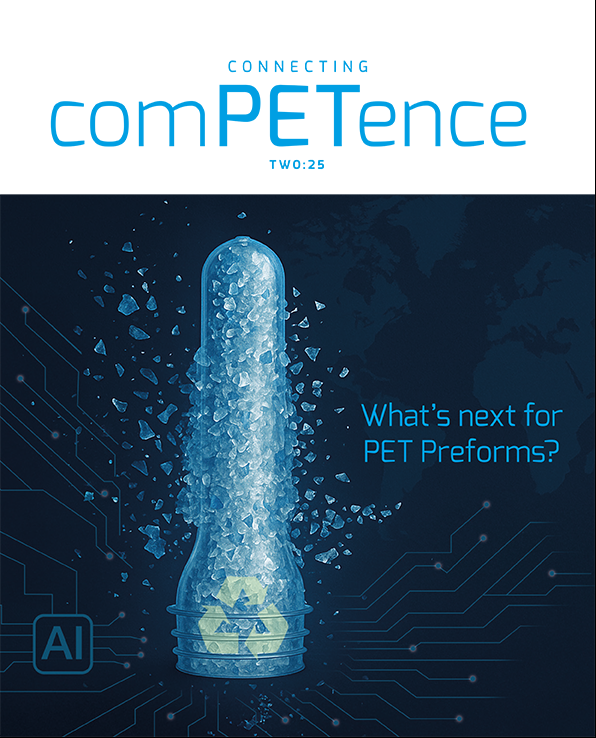
magazine
Find our premium articles, interviews, reports and more
in 3 issues in 2025.