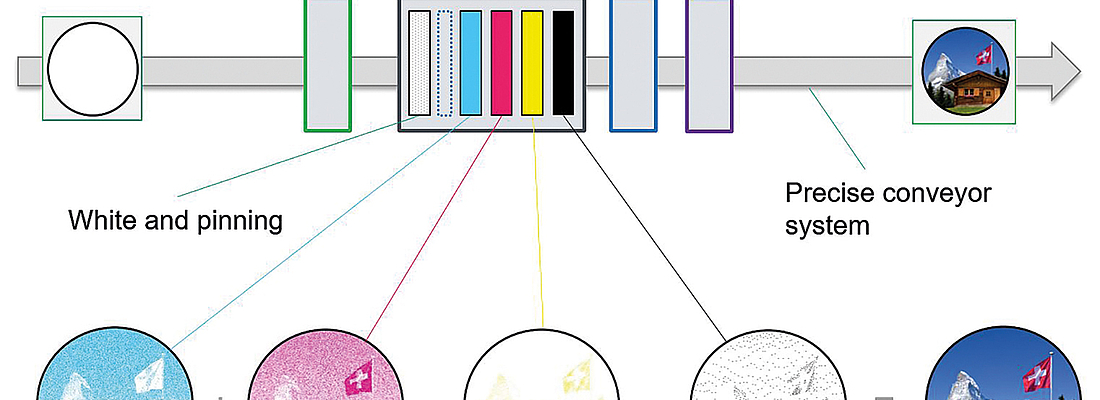
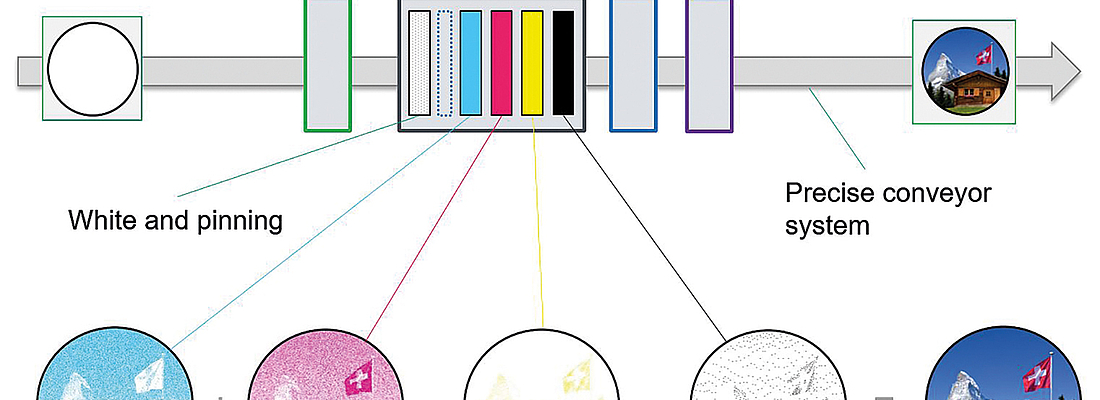
Pool Competencies
Innovative: Digital Printing Technology and Closure Inspection in High-Performance Segments
The closure is a part of every bottle. Every consumer touches it, uses it and pays attention to it. Mostly it’s the only part that consumers can see when the bottle is on the shelf, the ideal place for advertising and messages. As well as closure is suitable as a collector’s item.
1 Introduction
Mechanical printing machines, either based on pad or dry-offset technology, are the established printing options for closures. Digital printing for closures is a relatively new and innovative, even revolutionary technology. The motivation for printing a closure will change completely with digital printing, because now almost everything can be printed, at any time with absolutely flexible in format and printing. It’s all about flexibility and time-to-market.
2 Artwork
A RIP service (Raster Image Process) allows artwork to be transferred directly from digital production to the file to be loaded onto the digital printer (Fig. 1).
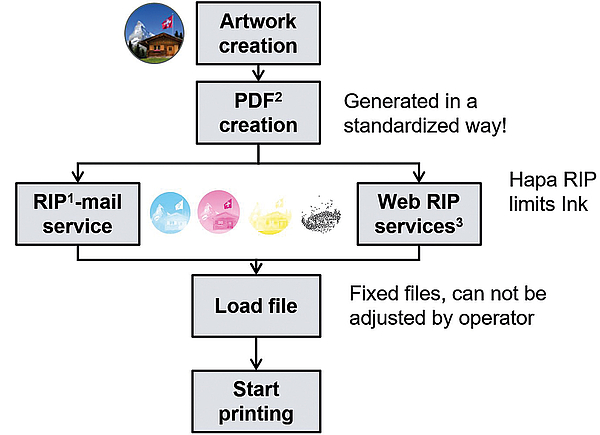
3 The Digital Printing Process
Everything has to go hand in hand. Specialists first analyze the closure application, carefully considering the polymerization kinetics of the ink and the curing times. The value of the dynamic behavior of an ink in terms of viscosity, surface tension, flow properties, adhesion and opacity on the respective print head is calculated to optimize the printability of each ink for accurate placement of the ink drops. (fig. 2).
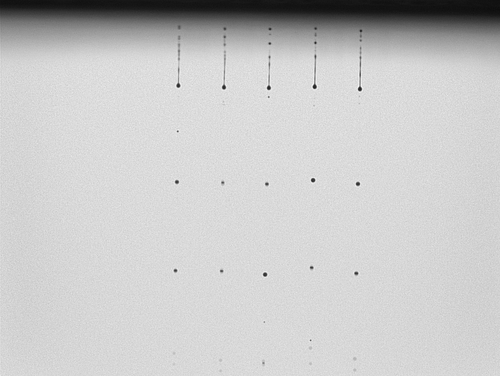
3.1 Technology
Our technology is utilising inkjet-based digital printers. The inkjet printer creates your image by transferring tiny droplets of ink to the closure. The first layer is white, if necessary, then cyan, magenta, yellow and black. By mixing these colours up to 80% of the Pantone colours can be printed (fig. 3).
The digital printing process is well suited for personalized direct marketing. With this type of printing process, variable printing is possible, which allows any type of direct marketing. In this day and age, it is common marketing practice to consider each customer as an individual with different composition and needs - and personalization is unrivaled thanks to digital printing.
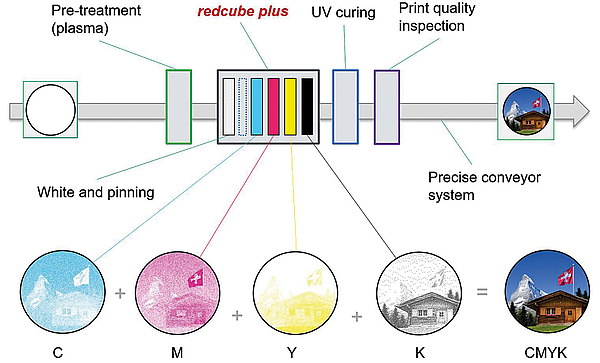
3.1.1 Surface Pre-Treatment with Plasma
In order to successfully print a plastic surface, ink should be able to wet the surface to achieve proper liquid adhesion. This requires Corona Treatment and Plasma Treatment technologies. Plasma can be described as partially ionized gas. Therefore, by selecting a gas mixture, pressure, and power, the effects of the plasma treatment on any surface can be precisely tuned.
3.1.2 Surface Wettability
The wettability depends on a specific property of the surface: surface energy, often referred to as surface tension (fig. 4).

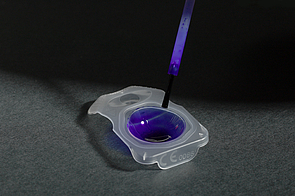
The wettability can be easily detected by contact angle measurements. The contact angle is the angle between the tangent line at the contact point and the horizontal line of the solid surface. (fig. 5).
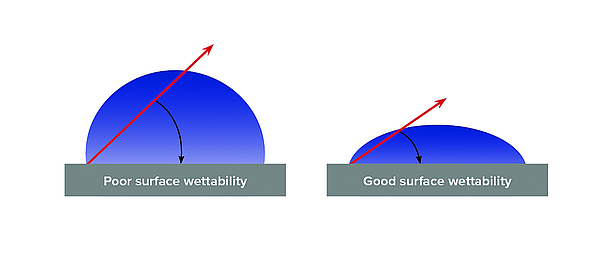
The higher the surface energy of the solid substrate in relation to the surface tension of the liquid, the better its wettability and the smaller the contact angle.
For proper bonding between a liquid and a substrate surface, the surface energy of the substrate should exceed the liquid tension by about 2-10 mN/m.
Fig. 6 shows the absolute surface energy values for solid materials, and the surface tension of many plastics, including polyethylene and polypropylene, is often insufficient for bonding or printing.
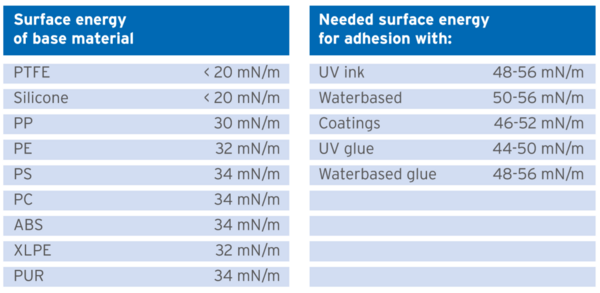
A surface treatment can improve the wettability of the material by increasing the surface energy of the material and positively affect the adhesive properties by producing bonding sites. The most advanced and successful surface treatment methods are based on the principle of high voltage discharge in air.
3.1.3 The UV Ink
UV inks are typically highly viscous, limiting the flow on the substrate. This, in combination with the instant or spot fixation provided by UV curing lamps, results in excellent print quality and fast overall operating speeds.
After curing UV inks are typically 100% solid, meaning that everything that is printed remains on the substrate. By using UV ink, there are no longer polluting VOCs that escape from ink solvents. Reducing air pollution is an advantage for those who want to pursue a greener approach to production. This is also of particular importance as most countries have strict laws that are constantly updating in terms of VOCs. The use of UV inks is one way to avoid production traps that may occur due to legal regulations.
The photo initiator is the key to the curing process as it starts the polymerization and cross-linking reaction. Under UV irradiation, the photo initiator fragments into free radicals, which are the reactive species for the polymerization of unsaturated species (moieties).
3.1.4 UV Curing Process
Long lifetime UV LEDs are carefully paired with the photo initiators in the ink. Power, ramp and time under UV light and the entire UV station is precisely selected for perfect ink cure and good migration results.
4 System and Engineering
Since the system must be flexible to handle multiple print and closure formats, many challenging mechanical engineering aspects regarding alignment rails, guides, jet streams, UV light holders had to be taken into account.
The system is also designed to easily print samples for customers. This shows one of the biggest advantages of digital printing: you can print samples with a very large format variation in minutes.
In addition, an intelligent sampling function enables quality control to remove any number of samples from the production run at any time without stopping the process.
The flexible “REDCUBE Plus” printing module from Hapa is the heart of the digital printer. It is able to print CMYK and white. Print-head maintenance is fully automatic with automated ink conservation and cleaning. For colouron-colour printing, two pinning stations are integrated as well.
For final inspection, an IMDvista print control system is part of the system to ensure that your customers receive only 100% compliant prints. The V5 Vision Control Center is the single controlling HMI that makes operation easy as found with all IMDvista vision systems.
The complete system with the plasma pre-treatment, printing, UV curing agent and the visual inspection, has production capacities of up to 1500 closures per minute (28 mm).
The system can be operated practically independently for days with only filling the ink tanks once per shift (fig. 7).

4.1 Caps and Closure Positioning
In general, it can be said that print shifts of more than 0.1 mm can be seen by the human eye. Requiring this level of precision means that the closure must not move more than 0.05 mm during the 5 print stations!
In order to achieve this level of accuracy, the closures are precisely transported on an innovative stainless-steel vacuum belt that resists the heat and energy of pretreatment and UV curing. Plastic belts are unsuitable due to the extreme loads.
4.2 Inspection and HMI
Finally, the well-known IMDvista Vision System inspects the printed closure. Special lighting and a high-resolution colour camera ensure that every printed closure has perfect print quality before shipment to the customer.
Easy operation for the complete system with just one HMI, the IMDvista V5 Vision Control Center controls the entire system including the print parameters.
The system is secured though a biometric authentication system to ensure system validation.
In other words, printing on a digital printer always gives the same results in terms of both print quality and ink quantity.
5 Food Contact Materials and Migration
More and more food products are being manufactured on an industrial scale and sold through retail chains. Their production and distribution are subject to increasingly stringent regulations. Almost all countries now have detailed standards for food safety.
The umbrella regulation for the production and marketing of food products is the food safety regulation (EC) 178/2002. There are also a number of subordinate regulations regarding food contact materials and their production. The European Food Safety Authority (EFSA) designates all items that are intended to come into contact with food as food contact materials.
The main regulations are as follows:
- Food Contact Materials (EC) 1935/2004
- Plastics (Plastic Implementation Measures) (EU) 10/2011
- GMP (Good Manufacturing Practice) (EC) 2023/2006
5.1 Who is Responsible?
Basically, the person or company that markets a product is legally responsible for ensuring that the manufacturing process for both food (content) and packaging complies with the regulations. Partial responsibility for the various packaging components is, however, usually delegated to the suppliers through a declaration of conformity.
This sounds relatively simple in theory however is far more difficult in practice. The main problem is that the proof of conformity cannot be provided directly during the manufacturing process of the closures, but only after a timeconsuming process carried out by an accredited institute. In addition, the relevant migration properties depend on the content, the barrier properties of the packaging, the storage conditions, the shelf life of the products and their further processing. In practice, closure printers hardly know all these parameters and can rarely provide analytical proof that migration values are complied with each order. Reliable proof of conformity is therefore only possible through cooperation along the entire value added chain.
Manufacturers of branded goods and retail chains fear above all, in addition to the legal consequences, a loss of image. Many of the major food manufacturers and retail chains have therefore already developed house standards derived from EU regulations and that are applied accordingly throughout the value chain (e.g. Nestlé, Danone, REWE and McDonalds).
Low-migration ink systems promise a way out of this situation, but do not expect any standard or EU regulations for lowmigration inks. The term “low migration” is rather used by ink manufacturers to identify UV inks that can comply with regulations when used properly on the particular type of packaging.
6 Abrasion with test results
Ink adhesion is often confused with inadequate drying, which is not always the case. It is advisable to use appropriate test methods to reliably determine the actual cause.
IMD has introduced their own test procedures because tape and cross-cut tape tests are controlled by the operator and/or depend on the test material (tape). Therefore, the tests are not repeatable.
7 Future and outlook
7.1 Current status
The first system has been running in real production since February 2017. Over 200 million closures have already been printed, from standard logos to special ads.
7.2 Curved surfaces
Concave or curved head-plates of closures are always a big challenge for the mechanical printers. These hurdles do not affect Inkjet technology. The print is as perfect on smooth surfaces as it is on curved forms. Not even the injection gate presents an obstacle to this technology.
7.3 Recycling
This is a very interesting aspect of this new technology. Undyed, transparent closures are best for recycling. Therefore HDPE in its “pure” form would be ideal for recycling, also for circular use and re-producing closures. Individualization and differentiation can be achieved very efficiently by digital printing. At this point, the investigations and tests are still ongoing. The question is how to separate the ink from the HDPE material.
7.4 Marketing Options
In addition to the high print quality, the security and stability of the process, it is the marketing options that enable the system to make a breakthrough. And here I come back to the introduction: A closure is suitable as a collector’s item. Imagine that you can print 20 different images in a repeating sequence in the same printing process. This opens up an unimaginable field of marketing options.
The comPETence center provides your organisation with a dynamic, cost effective way to promote your products and services.
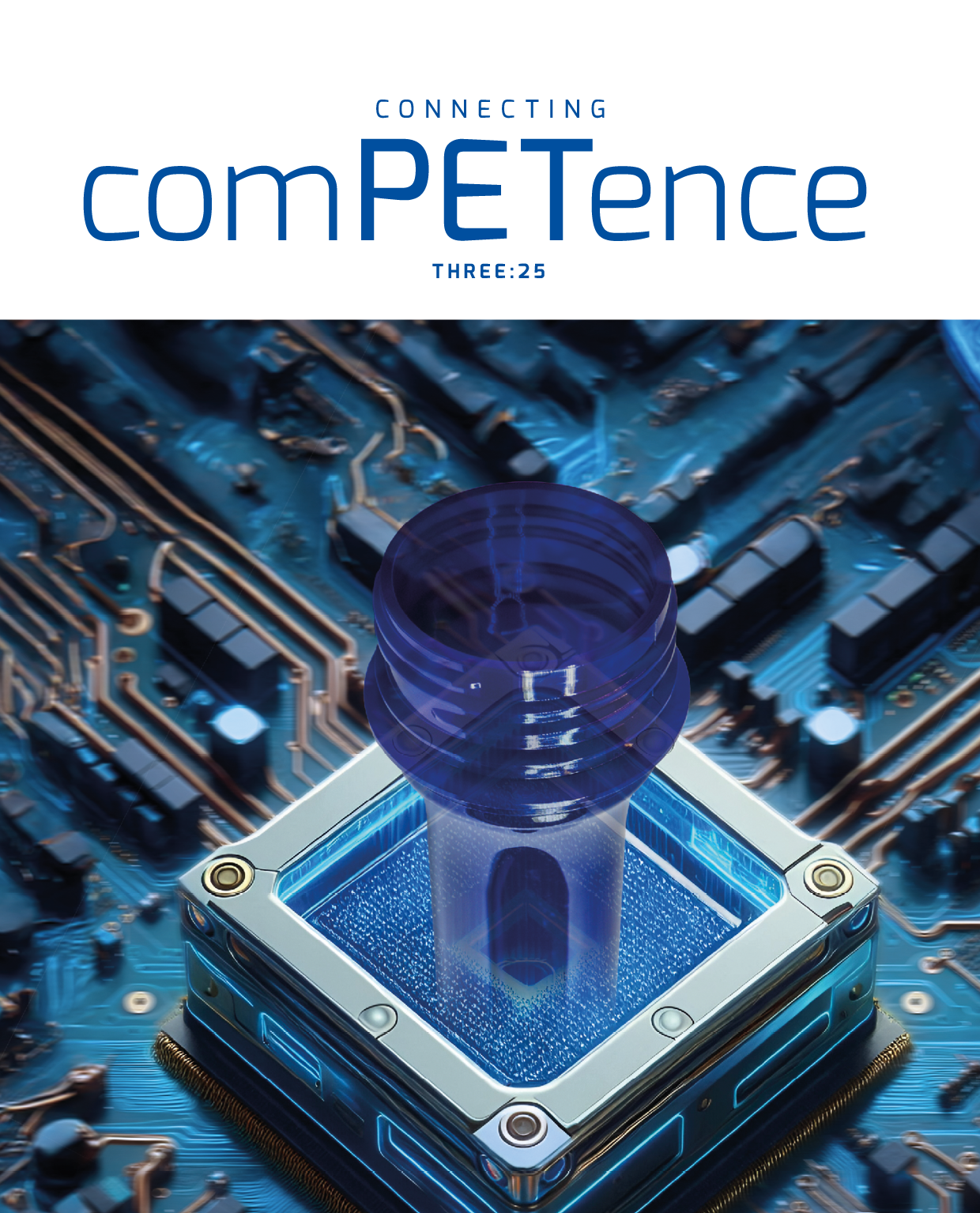
magazine
Find our premium articles, interviews, reports and more
in 3 issues in 2025.