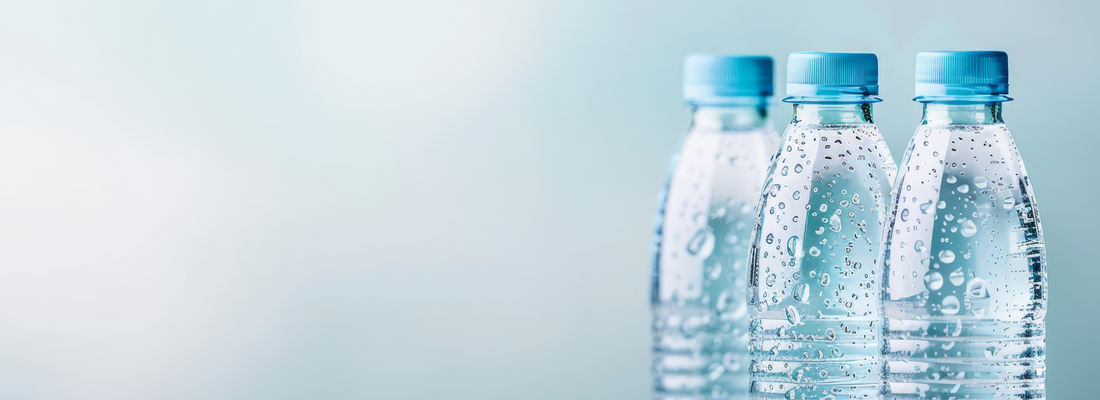
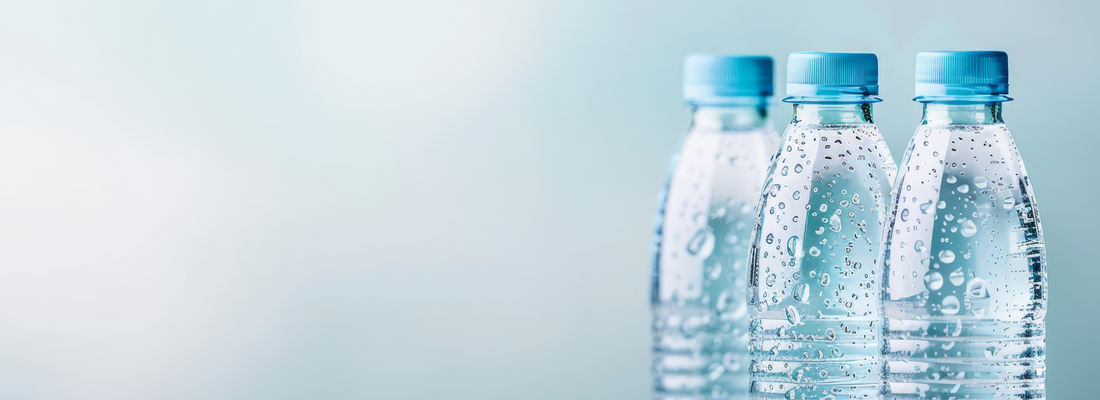
(Photo credit: Mikus - AdobeStock)
rPET Characterisation
From Haze to Clarity: rPET Characterisation with Advanced Material Characterisation Techniques
Using BMT’s pioneering material characterisation capabilities, the mechanical behaviour and associated processing window of recycled PET (rPET) preforms are methodically quantified and compared against their virgin counterparts. Obvious disparities in the above metrics between virgin and rPET resins strengthen the argument for these critical behaviours to be understood and measured prior to adoption, allowing for specific tailoring of the forming process, therefore mitigating unnecessary downtime on machines and reducing material wastage.
The push for sustainable packaging
Poly-ethylene-terephthalate (PET) has long been the material of choice for rigid packaging applications due to its versatile properties and widespread availability. As a semi-crystalline thermoplastic polymer, PET exhibits a high tensile strength, low density, and excellent optical clarity, making it suitable for diverse applications in industries such as food and beverage, pharmaceuticals, and personal care. Its robust mechanical properties, including superior stiffness and impact resistance, allow for the creation of lightweight yet durable packaging solutions. Additionally, it demonstrates excellent barrier performance against moisture and gases, contributing to the preservation and shelf-life extension of packaged products.
Despite the widespread use of PET in packaging, concerns regarding its environmental impact are ever-growing. PET production remains heavily dependent on non-renewable petrochemical resources, contributing to significant carbon emissions and the depletion of fossil fuels. Although widely accepted in global recycling streams, the scale of plastic waste and the energyintensive production process underscore the need for more sustainable solutions. In response, rPET has emerged as a viable alternative. Produced through the reprocessing of post-consumer and post-industrial PET waste, rPET offers the potential to significantly reduce the environmental footprint of PET production by lowering energy consumption and carbon emissions. Moreover, the use of rPET helps mitigate plastic waste and decreases reliance on virgin fossil-based feedstocks, aligning with global efforts to promote circular economies and reduce environmental degradation.
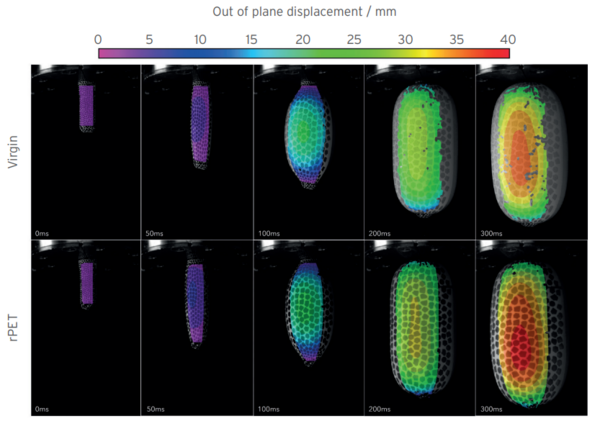
The hidden challenges of rPET processing
The incorporation of rPET into packaging applications presents notable challenges, particularly regarding processing control and maintaining material performance. Mechanical recycling is generally preferred over chemical recycling due to its lower complexity and reduced capital and operational costs. However, the mechanical recycling process can lead to degradation in the material’s properties. Repeated exposure to heat during processing causes polymer chain scission, resulting in a reduction in molecular weight and, consequently, diminished mechanical strength and durability. Variations in melt viscosity, crystallisation rates, and thermal stability are common in mechanically recycled rPET, further complicating its processability. These variations often prevent a straightforward substitution of virgin PET with rPET in packaging production, requiring necessary adjustments to processing parameters to ensure consistent quality and performance.
_______________________________
''The onset of strain hardening, or Natural Draw Ratio, is delayed by approximately 6% in the hoop direction for the rPET preform compared to the virgin under identical processing conditions.'' - BMT
_______________________________
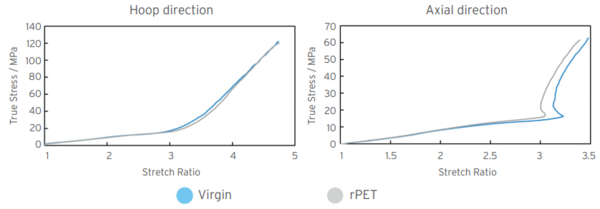
Freeblow insights: Virgin vs recycled PET
BMT’s BLOWscan device is an instrumented, labbased stretch-blow moulding (SBM) machine, capable of blowing preforms at conditions analogous to those experienced during production. The system combines high-speed imaging to capture preform deformation during the freeblow phase, along with three-dimensional Digital Image Correlation (DIC) techniques to quantify strain fields along its entire length. This integrated approach allows the user to generate extensive data insights into the deformation behaviour of preforms during the free-blow phase, enabling detailed analysis of the influence of various processing parameters on the SBM process.
An investigation into the free-blowing behaviour of a virgin PET preform with one of an rPET resin examined the influence of preform temperature and blowing parameters for both materials. The resultant contour plots are shown in Figure 1. Whilst the overall modes of deformation appear similar, a larger blowing diameter is associated with the mechanically recycled PET preform throughout the test window, as evidenced by the greater calculated out-of-plane displacements observed across the whole blown article at equivalent time steps.
Differences in material behaviour become increasingly evident when extracting the hoop and axial stress-strain responses. True stressstretch data, extracted from a point approximately halfway down the wall prior to deformation, reveals notable distinctions between the virgin and rPET preforms. The onset of strain hardening, or Natural Draw Ratio, is delayed by approximately 6% in the hoop direction for the rPET preform compared to the virgin under identical processing conditions. This slight change in strain hardening behaviour confirms the previously observed differences in global blowing behaviour. This would suggest an inherent variation in thickness distribution will be present in the formed bottle, which, if not addressed, may ultimately impact the post-processing performance characteristics of the final product.
Pinpointing pearlescence
Pearlescence, characterised by a milky haze on the surface of PET bottles, is known to significantly diminish the aesthetic appeal of the finished product. Although the material’s structural integrity remains intact, this visual defect can often create a perception of lower quality amongst consumers. Pearlescence, also known as stresswhitening, occurs when the material is stretched beyond its capacity, leading to the formation of microcracks in the material structure. The incorporation of rPET further complicates this issue, having already undergone thermal degradation, leading to increased crystallinity and a higher propensity for pearlescence formation. To address this challenge, manufacturers must even more tightly control the processing parameters to preserve the clarity and aesthetics of formed bottles. Most commonly, pearlescence is managed by increasing the temperature of the region undergoing maximum stretch, however care must be taken to avoid thermal crystallisation.
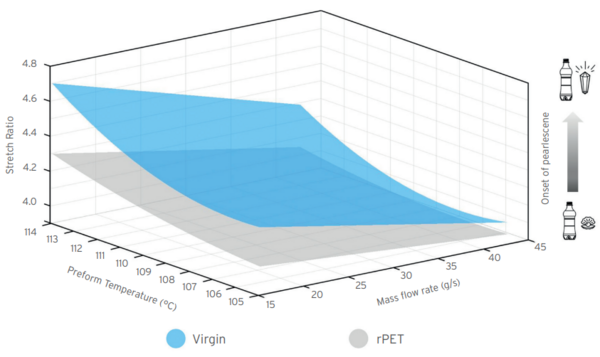
Leveraging the DIC techniques described previously during FSB testing, BMT have pioneered a protocol to identify the associated stretch in which the onset of pearlescence is identified as a function of the applied processing conditions. Preforms are specifically prepared to enable the tracking of stretch throughout the deformation process, while simultaneously monitoring optical behaviour and the emergence of pearlescence during free-blow. A range of conditions including preform temperature and mass flow rate are systematically varied to determine their effects on the subsequent onset of pearlescence – with an earlier calculated onset indicating higher propensity of this phenomenon at lower stretch ratios. The graph below (Figure 2) highlights the difference in onset with the experimental variables between virgin and mechanically recycled PET preforms.
For all combinations of preform temperature and mass flow rate, the surface plot for mechanically recycled PET consistently falls below that of virgin PET, indicating a heightened sensitivity to pearlescence behaviour during the SBM process. The plot further illustrates the susceptibility of both resins to specific combinations of processing parameters. Notably, low-temperature, highrate deformation is strongly associated with the early onset of pearlescence at lower stretch ratios, while high-temperature preforms subjected to lower mass flow rates exhibit reduced pearlescence formation. These findings emphasise the narrower processing window when transitioning from virgin to mechanically recycled PET, highlighting the need for precise control of processing parameters to successfully form bottles from rPET while mitigating the appearance of pearlescence.
The clear difference
With the ability to precisely identify the associated stretch ratio responsible for initiating pearlescence in each resin, single cavity mouldblow trials were conducted on virgin and rPET resin for the BMT bottle geometry. Internal and external temperature profiles of the preforms were measured and ensured to match using BMT’s patented THERMOscan device following IR heating, and prototype bottle samples produced using the BLOWscan. The image below (Figure 4) presents two resultant bottle samples: (a) the BMT bottle produced from virgin resin, and (b) the BMT bottle made from mechanically recycled PET.
__________________________
''These findings emphasise the narrower processing window when transitioning from virgin to mechanically recycled PET, highlighting the need for precise control of processing parameters to successfully form bottles from rPET while mitigating the appearance of pearlescence.'' - BMT
__________________________
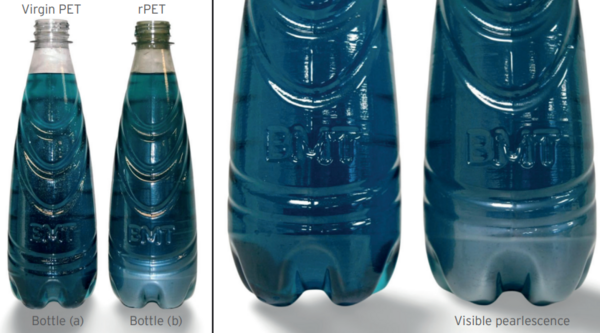
The image above illustrates the impact of switching materials without adjusting for their specific processing windows. Bottle (a), made entirely from virgin PET resin, exhibits optical clarity with no visible signs of haze. In contrast, bottle (b) displays a pronounced area of pearlescence concentrated around the base, where the highest stretch ratios are known to typically occur. Utilising the data obtained from earlier experimental trials, adjustments to the processing parameters were made, resulting in the production of a third prototype sample, shown in the subsequent image: (c) – the BMT bottle produced from rPET, following optimised process parameter guidance.
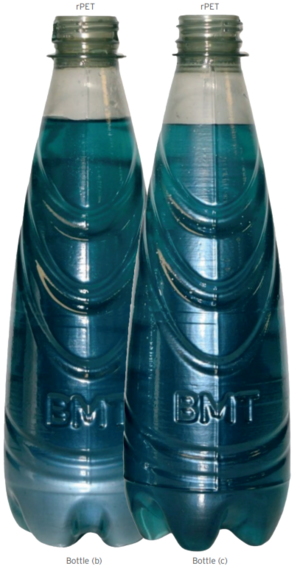
Following data-driven process optimisation, complete removal of pearlescence-induced optical haze is observed when comparing bottles (b) and (c). This comparison underscores the value of systematically characterising pearlescence development with stretch and showcases the potential of substantial time and cost savings when switching materials, whilst not compromising on bottle performance.
Data into action (conclusion)
The work presented demonstrates the critical importance of prior understanding of the behaviour and processing characteristics of mechanically recycled PET in packaging applications before substitution of the material. Through BMT’s advanced material characterisation techniques, significant differences between virgin PET and rPET have been identified, highlighting the need for precise control of process parameters to avoid performance degradation and visual inconsistencies such as pearlescence. By systematically quantifying the mechanical properties, onset of strain hardening, and susceptibility to pearlescence, manufacturers can tailor the stretch-blow moulding process to optimise the performance of rPET bottles. This approach not only mitigates concerns related to the appearance of the final product but also reduces waste and machine downtime, ensuring a more efficient transition to sustainable packaging solutions. As the demand for environmentally friendly packaging grows, the insights and methodologies outlined in this article provide a robust framework for achieving highquality, rPET-based products without sacrificing performance or appearance.
The comPETence center provides your organisation with a dynamic, cost effective way to promote your products and services.
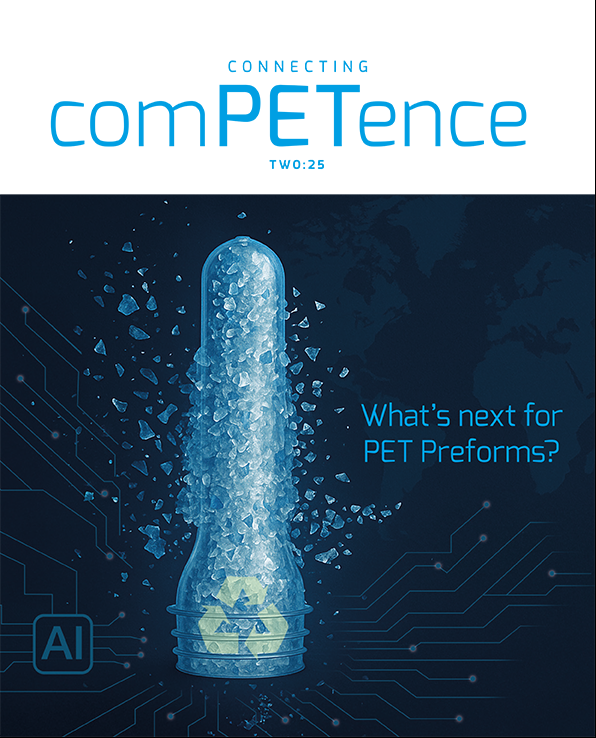
magazine
Find our premium articles, interviews, reports and more
in 3 issues in 2025.