

Post-mold cooling is an important part of the preform molding process. Athena PET machines offer an extensive set of features to optimize performance and improve part quality. Diagnostic tools like Axis Trace and Cycle Time provide real-time data needed to shorten cycle times. The optional Duo configuration and part ejection technology built into cooling tubes significantly improve preform handling and cooling. Transfer pins and cooling tubes are customized to improve part quality before preforms leave the machine. This flexibility helps customers get the most out of their preform molding machine.
Setting up a new process on a PET machine requires adjustment and fine- tuning. This creates an opportunity for machine operators to ensure that each component is working as quickly and efficiently as possible. While this process is commonly applied to injection and mold functions, it can be similarly applied to a post- mold cooling (PMC) system. Athena Automation’s PET machines are similar to other preform molding machines in that they have a robot, part handling system, and a method of cooling preforms outside the mold. What sets Athena apart is the amount of flexibility and adjustment available in its PMC system. Users have control over an extensive set of variables and options to get the best performance.
The PMC system consists of three major components: the side-entry robot, the transfer station, and the cooling station (Figure 1).
Each component is able to move separately from the actions of the platens. The robot system carries a cooling plate with a set of cooling tubes that accepts parts from the mold. Moving along two axes, the robot can move in and out of the mold and toward the transfer station. The transfer station position can be adjusted during set-up but is fixed in place during operation and supports a transfer box and plate of transfer pins. The transfer box rotates 360o to transfer preforms to and from the cooling station or dropped onto the conveyor. The transfer pins provide preform cooling and are able to transfer parts. The cooling station is an optional item that supports a second cooling plate and set of tubes. The cooling station is also able to move towards it to accept parts from the transfer station but does not enter the molding area.
The major PMC components are organized into two primary configurations: Mono and Duo. The Mono configuration consists of a robot with a cooling plate, and a transfer station with a transfer pin plate. This configuration provides up to 3 stages of cooling to preforms. The Duo configuration consists of a robot and cooling station each with a cooling plate, and a transfer station with two transfer pin plates. This configuration provides up to 6 stages of cooling to preforms.
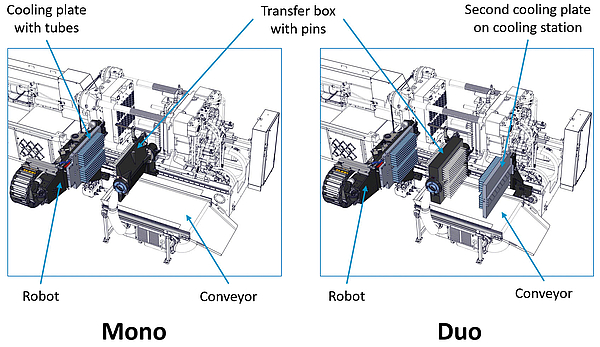
Fig. 1: Comparison of Mono and Duo post-mold cooling configurations.
SHRINKING CYCLE TIME
Cycle time is reduced by minimizing the time spent by each component as they perform actions and by finding new ways to overlap actions without compromising the original function or part quality. All PMC components move independently from the platens, allowing them to be programmed to work in anticipation of events like mold opening or closing.
The HMI is used to adjust the position and timing variables that govern when and where the robot enters the molding area allowing the robot to more safely accelerate into the mold (Figure 2). Conversely, the robot can be tuned to spend less time waiting for the mold to open, and spend more time cooling the part engaged with the transfer pins.
The transfer station has similar adjustability. Though fixed in place during operation, the transfer station can be positioned closer to the robot using a manual adjustment during set-up. It is also possible to adjust the transfer box rotation speed so that preforms can be moved from the robot to the cooling station or onto the conveyor more quickly.
The HMI features an Axis Trace tool that is used to collect measurements and graph user-selected variables (Figure 3). Variables are superimposed on the plot so that they can be reviewed together. This tool is ideal for comparing speeds and positions of the robot, clamp, and transfer station to identify time savings and opportunities to overlap actions. A Cycle Time page provides users with a breakdown of all of the machine’s primary actions, their duration, and their order within each cycle. Both tools display information in real time, allowing users to fine-tune the process quickly without having to step away from the operator’s position.
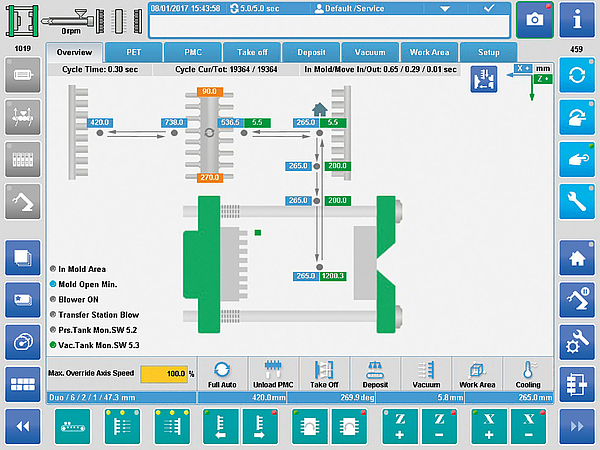
Fig. 2: Sample screenshot of PMC variables on the HMI.
PART HANDLING
Reducing the cycle time is not the only way in which the PMC system is fine- tuned. Preforms must be transported efficiently and the machine must accommodate a variety of handling requirements since they are designed in a variety of shapes, sizes, and weights. For example, preforms with long and straight bodies tend to be more difficult to eject from the cooling tube because of shallow draft angles and large surface areas. Athena’s PET machines come with the option to use a cooling plate that ejects preforms pneumatically or a hybrid method incorporating a pneumatically- driven piston that physically pushes “stubborn” preforms out of the cooling tube. The pistons ensure that all preforms are ejected from the tubes consistently.
Adjustability is also built into the transfer station when depositing preforms onto the conveyor. As the transfer station rotates to deposit the preforms, the vacuum releases, allowing parts to drop off. The release position can be adjusted manually, depending on preform weight and size. Combined with the ability to adjust rotational speed, users can push the machine to new limits.
All adjustments available on Athena PET machines work in tandem, allowing greater flexibility and adaptability to accommodate different preform types.
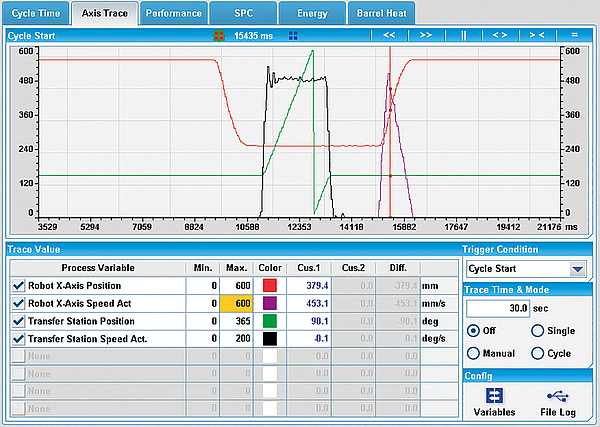
Fig. 3: Sample screenshot of the Axis Trace tool.
COOLING THINGS DOWN
Post-mold cooling performance is critical to any preform system. Athena applies solutions tailored to the preform to ensure effective part cooling outside of the molding area. Cooling tubes and transfer pins incorporate unique features that reflect preform geometry. Inside each cooling tube is a profile that provides intimate contact with the preform as it cools and shrinks. The fit of the tube profile is carefully designed to guide the soft shape of the hot preform as it shrinks from rapid cooling. This fit is designed for uniform cooling through contact. Transfer pins provide air cooling to the internal surfaces and neck finish using vacuum-generated air flow. Athena’s transfer pins hold the preform in place during transfer and provide cooling using the same pin and in the same cycle, thus increasing cooling time.
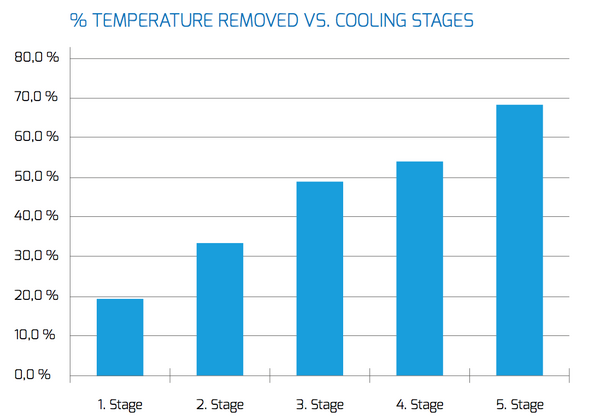
Fig. 4: The effectiveness of multiple cooling stages.
The Athena PMC system uses multiple cooling stages, so the preforms spend more time in contact with tube and pin, increasing part cooling dramatically. The number of cooling stages available for a preform depends on preform diameter and mold pitch. Most preforms are suited for up to three stages of cooling. The Mono configuration uses a single cooling plate and provides three stages of cooling. The optional Duo configuration supports two cooling plates (on the robot and on the cooling station) which provides up
to six stages of cooling. Using the HMI, operators are able to choose between Mono or Duo configurations and select how many cooling stages to use. Six stages of cooling are capable of reducing part drop temperatures as low as 35o C (Figure 4 & Figure 5).
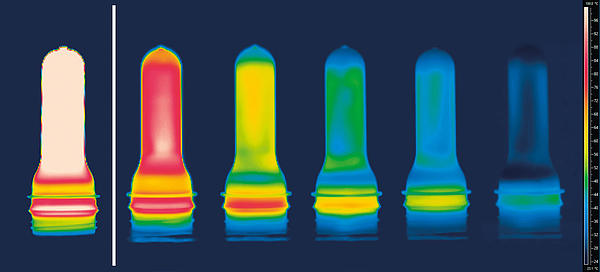
Fig. 5: Comparing external preform temperature (from left to right: out-of-mold, 1 stage, 2 stages, 3 stages, 4 stages, 6 stages of cooling). The preform used for testing weighs 24.7g, has a 38mm neck finish and a wall thickness of 2.8mm.
PROVIDING VALUE
Athena PET machines provide value because through standard features like the HMI-adjusted variables, trace function, and mechanical adjustments. Options like Duo (which includes an optional cooling station, cooling plate, and transfer pin plate) allow further optimization. Specialized solutions are also available for families of molds by sharing similar parts and minimizing the amount of tooling required to meet the PMC requirements but still providing flexible options.
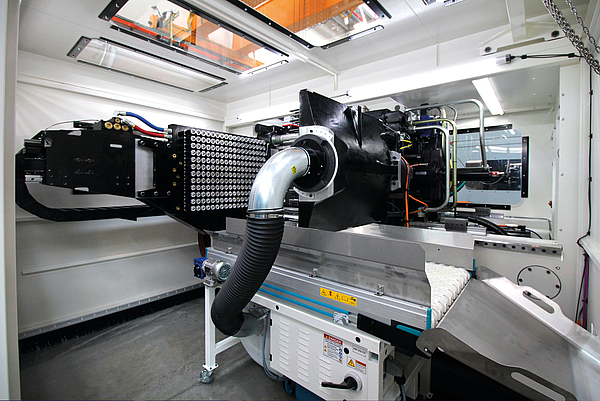
Fig. 6: Athena PET machine with a Mono PMC configuration.
The comPETence center provides your organisation with a dynamic, cost effective way to promote your products and services.
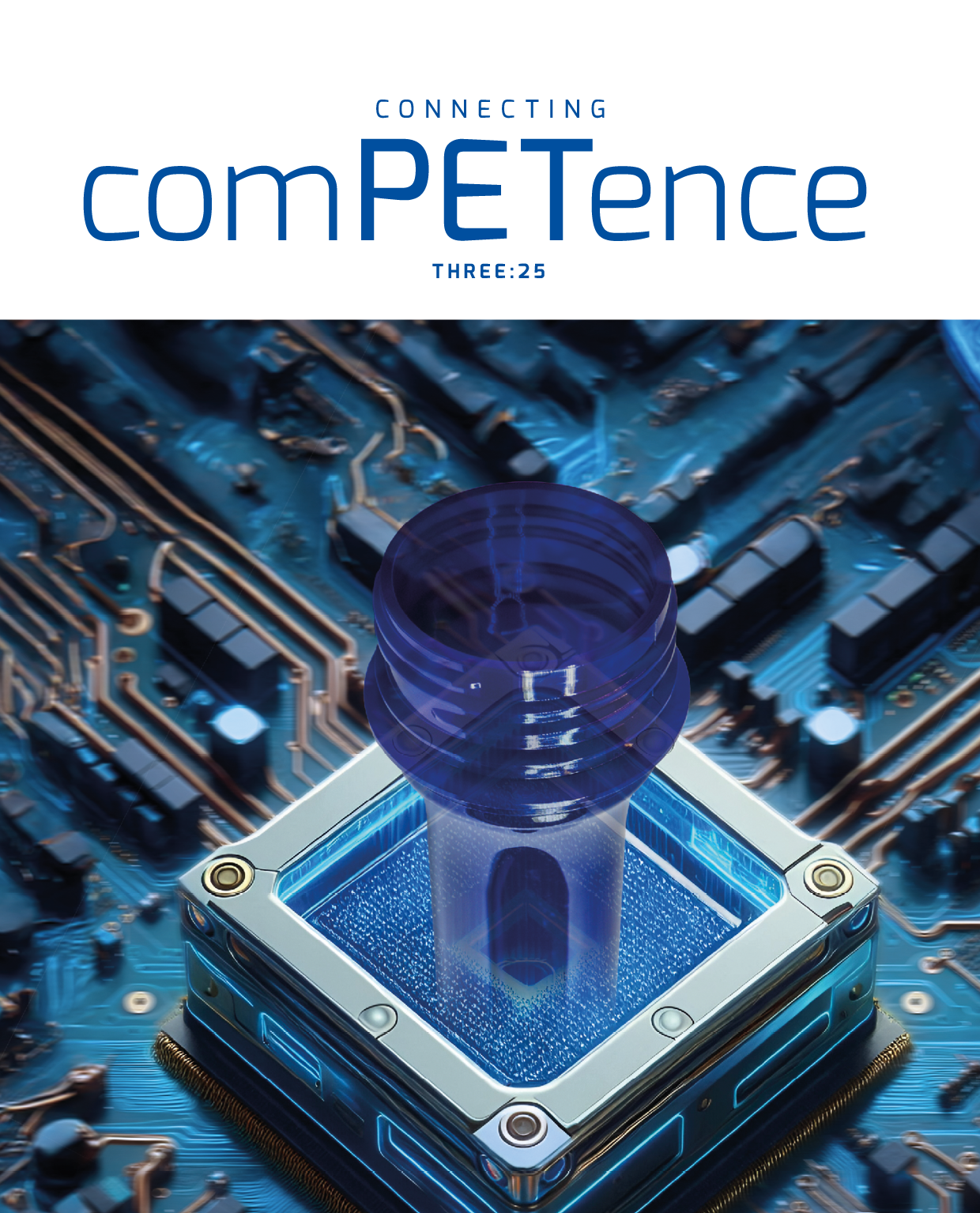
magazine
Find our premium articles, interviews, reports and more
in 3 issues in 2025.