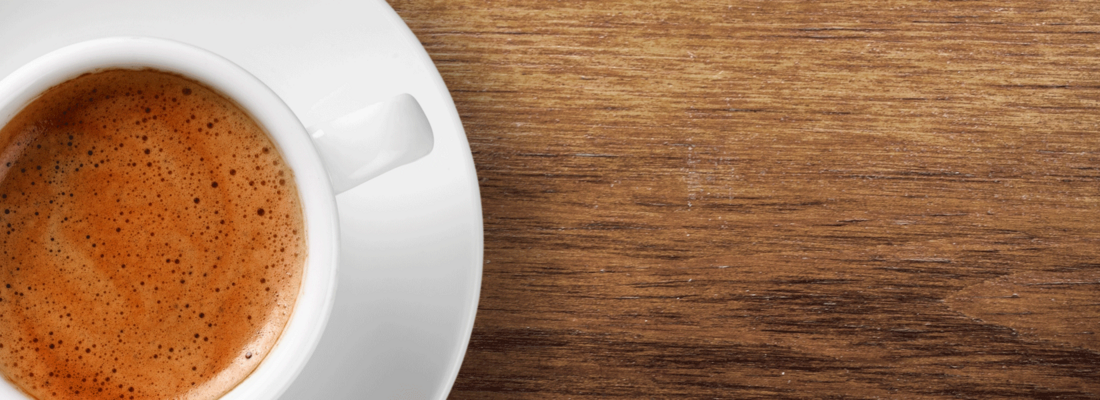
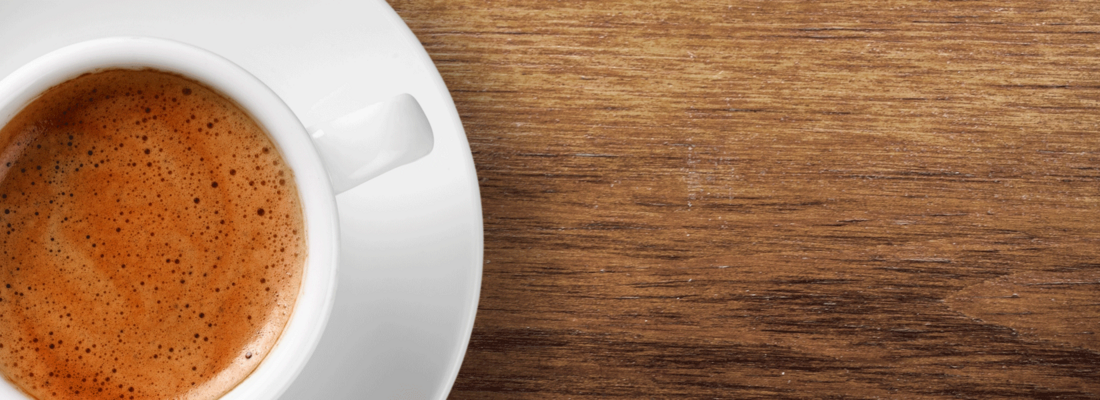
(Photo credit: Stock)
PET INJECTION MOULDING
Digital chat over coffee: How is Netstal’s new PET-Line side-entry machine doing?
Netstal has been supplying machines and complete systems for the production of PET preforms for 40 years. Due to the preform removal from the top, it requires special injection molds and post-cooling stations. The molds have a rather narrow and long design to ensure trouble-free removal between the tie bars of the machines. However, this space concept, which is good on the one hand, had a major weak point. The widely used molds for side removal are not compatible with this concept. For this reason, many customers were unable to switch to machines from Netstal. This gap is now to be closed by the new PET-Line with side removal.
It is now just over two years since Netstal introduced this new PET-Line with sideentry. So it’s time to take a closer look at the startup of the “new” one. We asked Stefan Kleinfeld, Product Manager at Netstal.
How is the PET-Line side entry developing?
SK: We are delighted with the start of the new PET-Line. We were rather cautious in our forecast for the ramp-up of the new system and are now finding that we are already selling twice as many PET-Line machines with side-entry as our top-entry predecessor. On the one hand, this has to do with the fact that we offer to new customers the new PET-Line only and, on the other hand, with the fact that the machine is currently the most modern production system for preform manufacture on the market.
That’s quite a statement. Where do you derive that from?
SK: The machine has an electrically driven toggle lever that enables very fast and precise movements. These properties pay off positively, as the cycle time can be shortened and mold wear is reduced to a minimum. In addition, the energy generated during braking is fed back into the machine, reducing the overall energy consumption of the system. With aXos 9 we have installed the most modern control system. Thanks to the integrated key operation Smart Operation, the entire system is particularly easy and intuitive to operate.
Has your idea been confirmed that you have broad market access thanks to the compatibility you have gained with existing mold concepts?
SK: The acceptance of the new compatibility is already shown by the fact that some new orders only include the pure injection molding machine without injection molds. Customers buy the new, energy-saving machine and can simply install their existing molds and produce with the newly gained advantages. Our approach has definitely been confirmed, so the new PET-Line with side entry will be the future at Netstal - replacing the older system with top-entry in the short term.
For the new development, Netstal first gathered experience with a small number of machines in a field test. Has this approach proved successful?
SK: Yes, that was definitely a good way to go. After that, there was time for another optimization loop, in which all the findings from production conditions could be incorporated.
What was the focus in this development phase?
SK: Thanks to our many years of experience with electrically driven toggle lever machines and hybrid injection units, we were able to focus specifically on our innovative developments. In particular, the focus was on the new, laterally arranged post-cooling unit with removal and transfer axis and several newly introduced options for improving preform quality and reducing cycle time.
Did you pay particular attention to rPET processing during this phase?
SK: Yes. With the new two-stage injection unit, a new screw design was used, which we had introduced a good year earlier with the PET-Line top-entry with excellent results. The new PETX screw design shows significant advantages, especially with high percentages of recycled PET or PET flakes. Producers confirmed a significantly larger process window, better homogenization of the melt, and good mixing even with challenging additives.
What does that mean in detail?
SK: For some customers, it turned out that a two-stage drying system - i.e., a main dryer combined with a smaller booster dryer directly above the injection molding machine - was no longer necessary. Without the booster, the energy consumption when drying the granules could be significantly reduced and amounts to an incredible 72,000 kWh per year and machine.
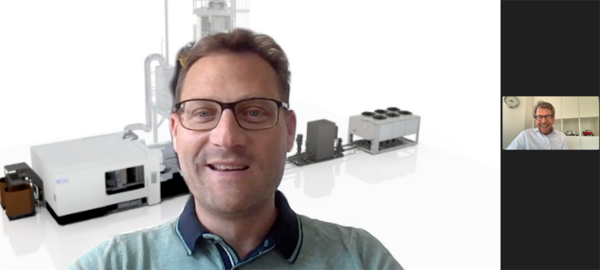
The main innovations related to the tool and dismantling area. Are they working as intended?
SK: Our specification was a tidy and easily accessible mold area that allows fast mold changes and, of course, supports a wide variety of molds and hot runner generations. Initial feedback from users showed that there was still a need for optimization in this area at the beginning.
_______________
''Our side entry approach has definitely been confirmed, so the new PETLine with side entry will be the future at Netstal.'' - Stefan Kleinfeldt
_______________
What were the sticking points?
SK: In the first phase, we had to exchange the cable sets between the machine and the hot runner during a changeover in order to be able to cover different manufacturers and generations. This circumstance was error-prone and time-consuming. The adjustments were successful. The different heating zones can be set via the operator panel, so changing different cable sets is no longer necessary. Fast format changes are essential for preform converters. A further need for optimization arose with the preform boxes underneath the mold. Too many preforms landed next to the box and were scattered around the machine area. Not only was this unsightly, the preforms also had to be laboriously removed from the machine. Overall, we managed to quickly rectify deficits that we recognized under production conditions.
Was there further potential for optimization with the well-running machine?
SK: Yes, this was already apparent in the prototype machine in the side removal area. Already in the concept phase of the new machine, we took into account that the removal axis can run a vertical stroke. The optional upward and downward movement of the axis serves to provide an additional cooling station at the removal gripper. The concept is based on the common pitch distances of 50 and 60 millimeters. Whereas on the prototype machine you had to adjust this range by manual intervention, you can now make this adjustment automatically on the operating unit. During development, we assumed that customers would either use tools with a 50 or 60 millimeter pitch and not have to switch back and forth as often. The current findings from the field test were therefore extremely useful for optimizing the system with regard to the production conditions.
Let’s talk about the post-mold cooling system.
SK: From the start, the master-slave drive on the removal axis works flawlessly and customers achieve excellent lock-to-lock times. We have optimized the axis for the transfer unit. It is responsible for removing the preforms from the cooling sleeves of the removal gripper and placing them on the discharge belt. In addition, it must implement the internal cooling of the preform. Here it is essential that sufficient process air is available. Based on interim results from the field test, it turned out that we had a problem at precisely this point. During the analysis, we came up with something clever: After optimizing the flow technology, we were able to provide the necessary amount of air in an energyefficient and resource-saving manner and thus achieve the desired result.
In terms of the process, the only thing that remains is preform quality control, which is increasingly becoming the standard. This is real-time monitoring. Do the systems in the market have this option?
SK: Yes, and we had equipped some of the first machines with the additional option of preform quality control. A problem quickly became apparent with the accessibility to this integrated device: the regular cleaning and inspection of the cameras and surfaces could not be carried out satisfactorily. So we optimised the vision control system and the interfaces to the machine. With the new technical status of the machine, which will be delivered from August 2023, this weak point has also been eliminated in a production and customer-oriented manner. Interested customers can now order this option again and benefit from the improved inline quality control.
Thank you for the digital meeting.
The comPETence center provides your organisation with a dynamic, cost effective way to promote your products and services.
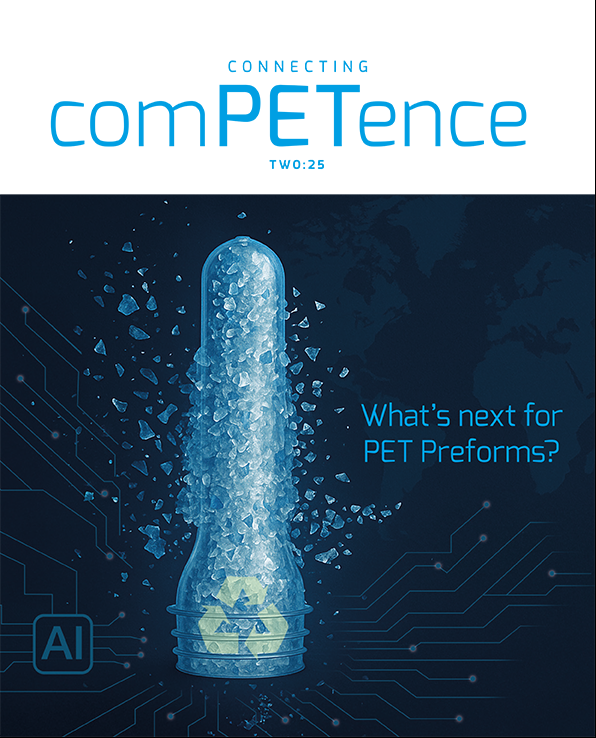
magazine
Find our premium articles, interviews, reports and more
in 3 issues in 2025.