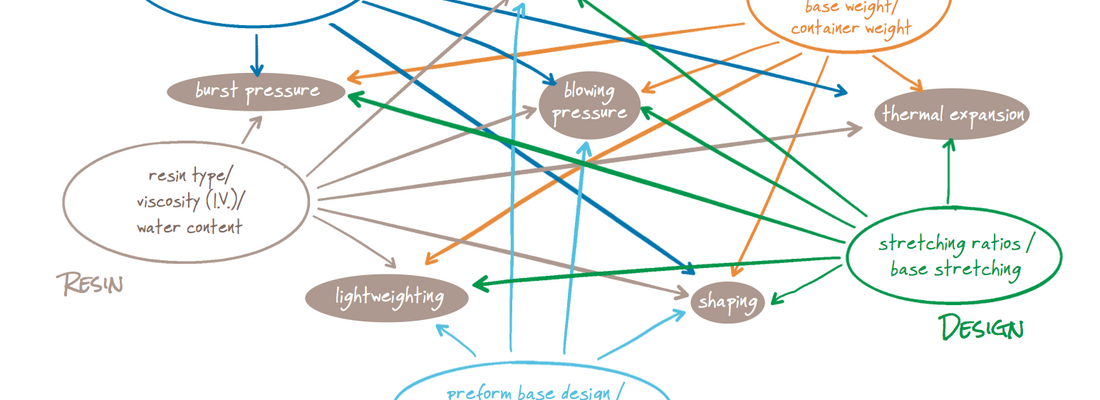
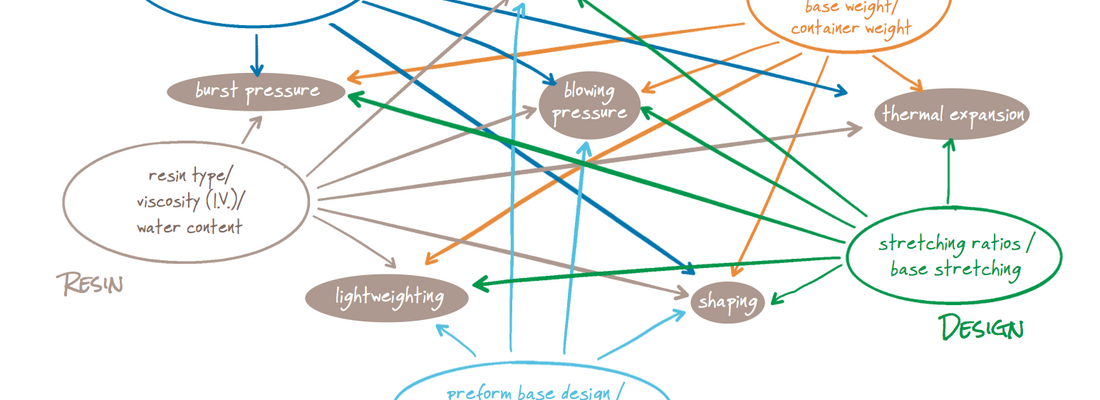
Blowing pressure – Blowing pressure is a more complex topic than it might appear at the first glance
We do not sleep well with the unknown in the back of our heads. We all are human and human nature is to find explanations. Our success as a species developed with our cognitive skills and that imprinting urges us to understand things. There is, however, limited information about many things and there are of course –especially when things get complicated- limited possibilities to get the whole truth. As we clearly like to sleep well we will find ourselves simple solutions that can go as far and be false as superstition.
What does that have to do with our industry you might ask? Even in our modern and fact based PET world we sometimes have cases of this cognitive bias. Simple and plausible theories regularly override the more complex and more difficult to understand reality. One example is the pervasive hype about special preform base geometries from a couple of years ago (yes, I agree that a lighter preform makes a lighter bottle but there are different opinions on how to best go about this). A similar topic is today’s - blowing pressure.
There are suggestions in the market that claim the reduction of blowing pressure can be targeted easily with an improved venting of the base of the blow mold. When you take a closer look it becomes obvious that the topic is not such an easy one. Necessary blowing pressure is a more complex subject than these claims make it seem.
Let us first have a look at what happens during blowing of the bottle. A preform is heated to a temperature above the glass temperature of the respective material, usually PET. Then the preform is stretched and the developing balloon is blown into a blow mold. The material is forced by the blowing pressure towards the wall of the blow mold and then touches the usually cooler walls of the mold and “freezes”. In case the PET cannot touch the wall in the available time long enough and does not cool down it shrinks back after release of the blowing pressure, thus the bottle is not fully blown. Some areas of the mold are touched earlier and some later. The later ones are usually the areas with more local stretching of the material like the feet of the bottle base or embossed design features somewhere else in the bottle.
Four general influences determine the necessary blowing pressure (figure 1):
-The shape that has to be blown – bottle and base design
-The necessary cooling time (where the material really touches the wall) in relation to the available process time
-The restoring force that the PET material has and
-The resisting force by air, that is unintentionally captured between blow mold and developing balloon, improper venting
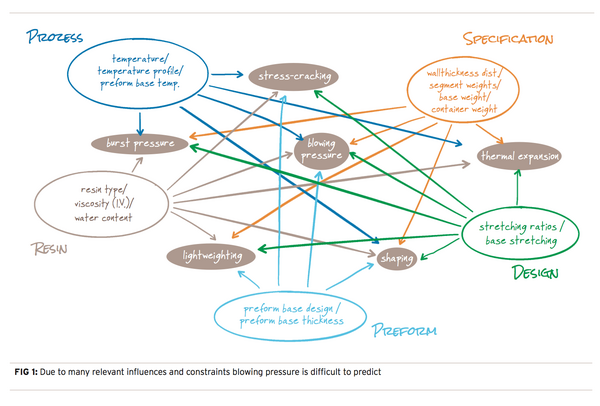
Bottle and base design
In item 1, shape, we find a good part of the reduced blowing pressures that can be seen in the data today. A very important part of the design is and has always been the design of the bottle base. You can tell that from the smooth and round shape of the feet and the relatively small stand ring diameter. KRONES owns a patent on the smooth shaping (“freeform”) of our “Carbo Classic Base”. Suitable shapes for polymers rather than the old style sharp-edged metal constructions. Also the better machinery on the line and more know-how in base design have resulted in bottle bases with much lower necessary stretch. That results in smaller stand ring diameters which a modern beverage line can handle, and which older beverage lines could not handle.
Bottle design itself, however, is a topic that is often marketing driven (e.g. visibility of embossings, certain shapes and proportions) and often cannot be changed.
Cooling time
Item 2, available and necessary cooling time, brings some interesting correlations. The available cooling time is very much a function of the machine/cavity speed, faster machine speed leaves less time for cooling. The necessary (real) cooling time is strongly determined by wall thickness and preform temperature (at least here our life became easier with the light weighting trend in the last years) and –here we have to use bold letters- bottle specification. Not fully blown details of the bottle design or slightly less base clearance might be OK for one application but for an especially hard specification for a CSD bottle base will require longer base cooling duration though the differences might not even be visible with the naked eye.
Restoring force
Item 3, restoring force, that is where a bit of material science comes into the play. Higher intrinsic viscosity (IV of the material) and lower preform temperatures need more blowing pressure because they keep the material tougher. On the other hand they improve also the bottle performance (creep, especially with elevated temperature, and stress crack resistance). And here we are again with bottle specification. Higher copolymer contents, lower IV, preform water content (water acts as a plasticizer) and a higher preform temperature make the material act softer – and usually at the detriment of the bottle performance. The second part here is preform design (including preform wall thickness), resulting in the stretch ratio. Higher stretch ratios need more force/pressure but yield –to a certain extent- better properties. A lower preform base wall thickness makes the blowing of the bottle base easier with lower pressure –especially with bigger and heavier bottles.
Venting
Last but not least also item 4, air trapped between the developing balloon and the blow mold can be the reason for a not fully blown bottle and the need for a higher blowing pressure. The blow mold should have in the areas where the balloon would otherwise trap air (that is usually where the material arrives last) venting holes to let the air out. If not the trapped air diminishes the resulting force generated by the blowing pressure and a higher pressure is needed.
conclusion
We at Krones have –with our experience of more than 1000 blowing tests each year- developed our own base venting solution that ensures 100% proper venting and keeps the hardware affordable with a solution that is also suitable for manufacturing.
These complex correlations make it very difficult to predict the necessary blowing pressure, especially when not yet all boundary conditions are known. In one case the thermo stability specification for the bottle might be the limiting factor for further decreasing the blowing pressure, in another case the preform base wall thickness may be the next thing to change on the way to lower blowing pressures.
In reality there might also be misleading cases of pressure optimization where apples are compared to oranges. A different PET resins can make it easy to reach a decrease. Test setups that do not take the whole picture into account can be seen, too. Process “optimizations” ignoring inconvenient parts of the bottle specification which may be difficult or very time consuming to test (like stress crack or thermo stability) often lead to “solutions” that seemingly allow to make good bottles with a lower blowing pressure. Also the complete molding/forming of the bottle is sometimes judged with subjective perception – especially when it is about design features that do not influence the bottle volume much, for example the shaping of embossings.
You see that with a closer look at it the blowing pressure topic is not only about resin or venting, but also about bottle and preform design, machine speed and -very important- specification. And as you can also see, the process requiring the lowest blowing pressure does not necessarily make the best performing bottle.
The comPETence center provides your organisation with a dynamic, cost effective way to promote your products and services.
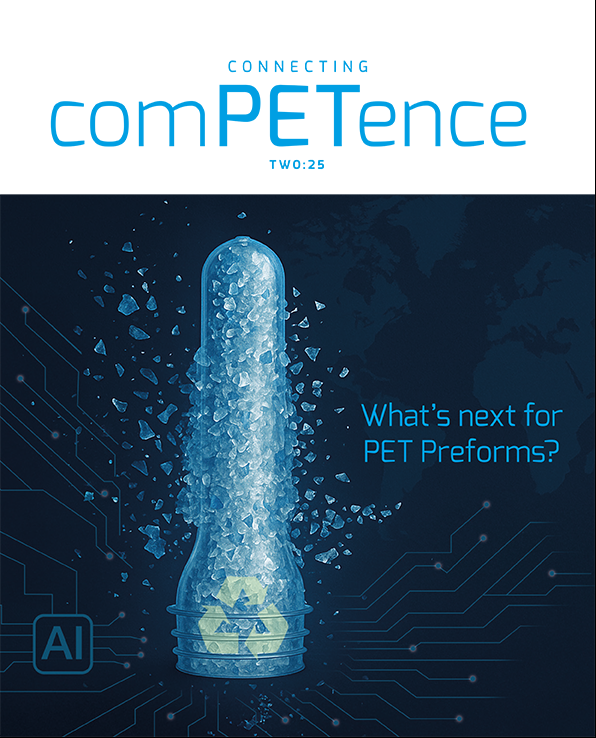
magazine
Find our premium articles, interviews, reports and more
in 3 issues in 2025.