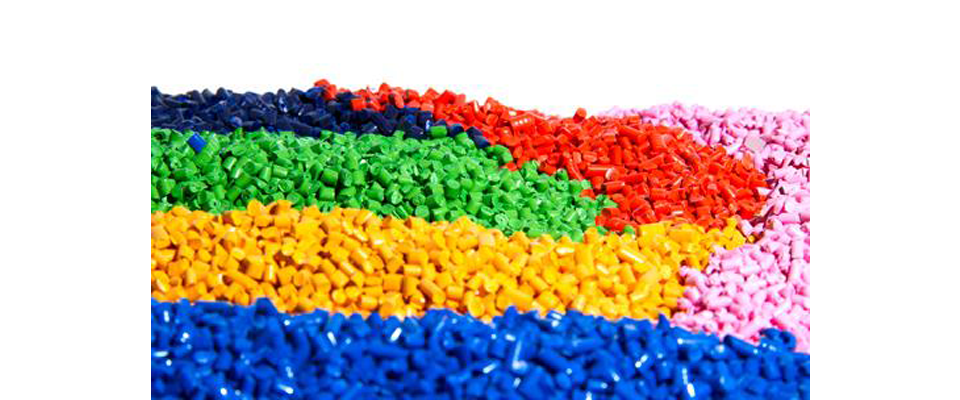
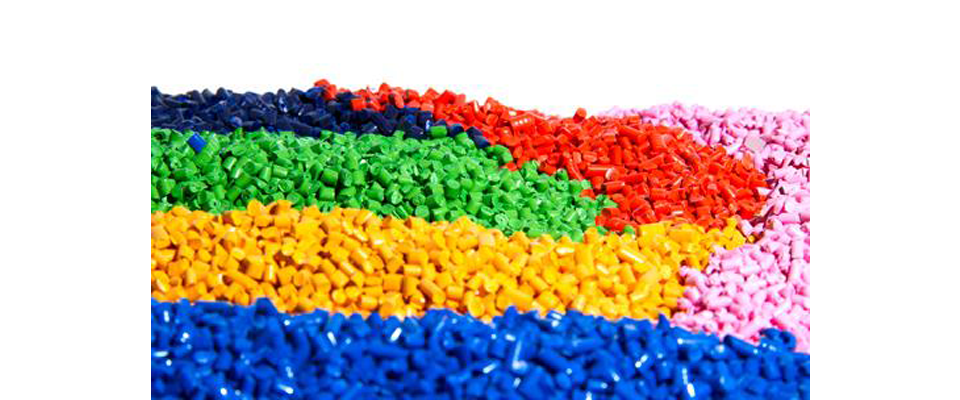
Photo credit: Carolina Color
Colour Masterbatches
Advantages of a color masterbatch for molding plastic products
Typically, a masterbatch is available in either a liquid or pellet form and is comprised of a concentrated mixture of pigments, dyes and/or additives to color plastic products. Masterbatch is used in place of fully colored compounded materials largely referred to as pre-color. This option can be more expensive due to volume minimums, inventory requirements and the threat of obsolescence whereas masterbatch mitigates these challenges.
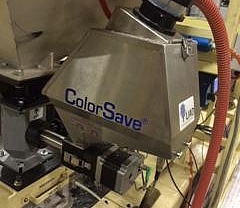
Even after being convinced that masterbatch is a better colorant option, many processors still debate whether liquid or pellet form is the better option? Both have advantages and disadvantages. The advantages of liquid color include: effectiveness at extremely low levels, good on long production runs, newer computer-controlled pumps for consistent delivery, and upfront costs can be lower. The challenges of using liquid color masterbatch are: liquid can cause screw slippage when higher levels are required, liquid carrier resin can separate from the color itself over time requiring offline mixing or peripheral online equipment like agitators, housekeeping issues present a challenge due to the constant threat of equipment malfunctions of hoses and tube sets due to wear and tear.
The advantages of pellet color masterbatch for plastic parts include: reduced housekeeping, zero waste and quick change-overs. Lastly, it avoids all hidden costs like additional hoses and tubes sets, agitation and consolidation that liquid color requires. The one historical advantage liquid has enjoyed over pellet masterbatch has been rooted in economics. That stated, there is new pellet technology that has come on the scene in the last few years that can both reduce cost and eliminate processing headaches. On such producer is Carolina Color, the innovators behind their patented G2 and G3 (patent pending) colorants.
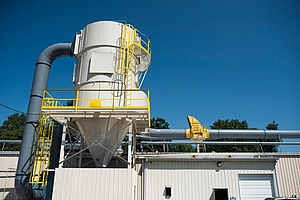
These pelletized colorant technologies feature the highest-loaded pigment, dye and/or additive packages in the industry. The colorant is exceptionally well dispersed, and can be effectively distributed in large and small parts at a reduced cost. Carolina Color's G2 targets outdoor products that feature up to 10- year warranties by bundling pigments and UV/AO at an average let-down ratio of 1%. G3 targets the packaging industry and offers an average let-down ratio of .5% for opaque applications and below that for transluscents. Carolina Color, since its founding 50 years ago, has been a family-owned business that manufactures color concentrates for the plastics industry from two ISO 9001:2008 certified locations in Salisbury, North Carolina, and Delaware, Ohio. These facilities provide 500+ customers with full-service production capabilities and comprehensive labs for color matching, quality control, and analytical testing. Carolina Color is capable of producing over 25 million pounds annually.
The comPETence center provides your organisation with a dynamic, cost effective way to promote your products and services.
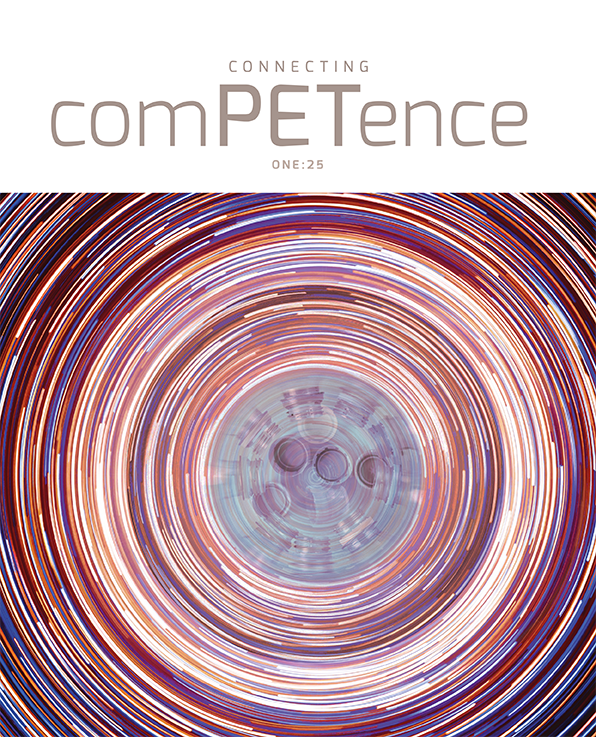
magazine
Find our premium articles, interviews, reports and more
in 3 issues in 2025.