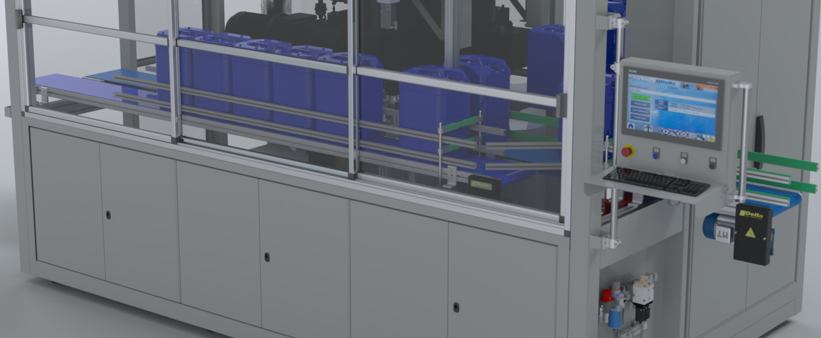
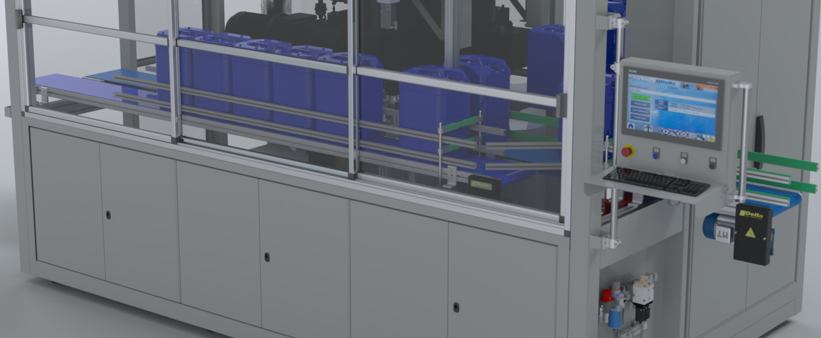
The benefits of coating bottles and containers are numerous. Amongst others, it greatly improves their barrier properties and, quite often, ensures their recyclability. In the meantime, it is more economical than other solutions. Now, Delta Engineering presents a range of new coating machines. The technology at the core of them implies new uses of plasma. This has remarkable advantages in the fields of processing, product quality, health and, last but not least, the environment.
Technology
Plasma is one of the four fundamental states of matter, next to solid, liquid and gas. Now, the Belgian company Delta Engineering presents a new range of coating machines, based on PECVD (plasma-enhanced chemical vapor deposition).
In general, CVD in all its forms achieves very homogeneous surface coatings; however, PECVD has the additional advantage over thermally activated CVD that it can operate at lower temperatures. Also, PECVD enables an increased deposition rate.
Delta Engineering now offers a PECVDtechnology depositing thin films from a gas state to a solid state on a substrate, such as the inside of bottles. More precisely, the gas mixture used by the company contains acetylene (C2 H2 ). Microwave energy causes the gas to reach its plasma state. The acetylene molecules split into highly reactive methylidyne radicals (CH*). They all bind, immediately, with the inner surface of the bottle, thus creating a carbon coating. Hence, it is a non-exhaust process. The appropriate properties of the coating are obtained by choosing the right mixture of gases injected in the bottle.
Some of Delta Engineering’s new, advanced coating machines imply three steps. In those cases, as a first step, argon plasma cleans and etches the inner side of the bottle, making it easier to be chemically modified. As a second step, a carbon layer is added with the coating technology using acetylene, as described above. In a third step, the company uses R134a, a well-known HFC. With microwaves, the HFC-molecules of R134a are broken down and create a protecting carbon-fluorine layer inside the bottle.
The latter three-steps technology is quite remarkable. Today, most technologies fluorinate by means of direct fluorination; however, this method is under pressure because of the dangers of escaping gas, which is not environmentally friendly and might intoxicate workers. Delta Engineering’s new solution, however, brings on the scene fluorination using plasma treatment. Thereby no gas gets into the atmosphere. Instead of fluorine gas, the company uses the non-ozone depleting R134a. This R134a is also known as a refrigerant, one that is very common indeed and is used in a wide range of refrigeration and air conditioning applications.
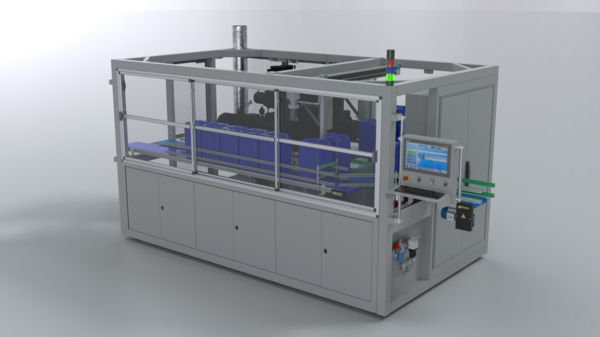
Materials
PET With its new range of coating machines, Delta Engineering brings carbon coating of PET bottles to a next level. Of course, there are other technologies to get the desired barrier properties. An example is co-injection (multilayer) which, unfortunately, has a very high CAPEX. Another example is using plastic blends (chemical additives to improve the barrier properties). These, however, often have unwanted side effects such as effecting clarity, stress cracking, etcetera. Delta Engineering’s plasma coaters clearly stand out from these in terms of material cost, lightweighting, recyclability, and operational performance for production.
HDPE
The enhanced barrier properties of HDPE bottles and containers treated with fluorine are lauded since long. Delta Engineering now succeeds obtaining them by using its very promising HDPE plasma coating technology. It uses that instead of direct fluorination, which use elemental fluorine, an extremely reactive gas. The new coating machines, however, use chemically bound fluorine atoms. These are harmless - actually, bound fluorine is even quite useful, as we all know since we brush our teeth with fluoride toothpaste, which contains it.
Other materials
Delta Engineering won’t halt at providing good barriers to PET and HDPE. New solutions for other materials are in the pipeline, amongst others plasma enhanced coating of PP. To be followed!
Coating properties
Carbon
Delta Engineering’s carbon coating makes bottles less susceptible to ingress of oxygen (O2 ) and loss of carbon dioxide (CO2 ), and improves water vapour barrier as well. It is an inert layer, preventing any PET-related migrations (with for example acetaldehyde) towards the contents. The layer is also resistant to delamination, under, amongst others, hot and humid conditions. It increases the shelf life of products bottled in PET by a factor of up to five. Furthermore, the coating is food grade.
Applications for carbon
Thanks to Delta Engineering’s carbon coating, PET gets suitable for lots of chemicals, as well as drinks such as beer, sauces, water, tea, coffee, juices, sport drinks, etcetera.
Fluorine
Fluorine greatly reduces solvent permeation and chemical attack. It also reduces or eliminates paneling - the compromising, after some time, of the plastic walls of a bottle or container. Furthermore, it prevents container discoloration, reduces or eliminates odor emission as well as loss of flavor and fragrance. Moreover, it reduces or eliminates loss of active ingredients and interaction of the container with the product. These benefits are not restricted by size, shape or container manufacturer.
Applications for fluorine
Delta Engineering’s new plasma coaters are quite helpful for products prone to hydrocarbon transmission through their plastic packaging (table 1).
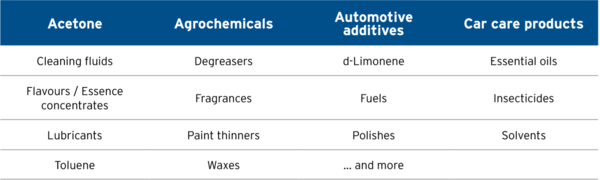
Table 1. Applications
Recycling & circular economy
In the circular economy, products can be made out of finite materials or on basis of renewables. It is a system in which resource input, waste and emission are minimized by closing loops. The new range of coating machines definitely helps achieving that goal.
In a circular economy, products which are made of finite materials ought to be designed to be as easily recyclable as possible. Now, bottles and containers designed to be coated using Delta Engineering’s new coating machines stand out by their minimal thickness: about 100-150 nanometer. This negligibly small layer ensures that the packaging remains a monolayer one, and that the ground material of the bottles and containers can easily be re-mixed. The packaging can then be recycled in standard recycling processes, and recycling it has no impact on the thermo-mechanical properties of the material.
Also renewables can enter into play. The new range of plasma-based coating machines are perfectly able to coat packaging made on basis of renewables such as bio-PET and bio-HDPE. They remain just as easy to recycle as their fossil-based counterparts.
Sustainability
Delta Engineering’s plasma coating machines pave the way for more sustainability. They make recycling more efficient and effective, an essential step towards a circular economy. Furthermore, they open new opportunities to make packaging that has less weight but still meets all desired criteria: less weight means reducing cost as well as carbon footprint. In addition to that, the new PET Plasma Coaters are non-exhaust types, thus making an end to exhaust gases escaping in the atmosphere.
Minimal product cost
Plasma coating is a viable alternative to replace multilayer technology. Apart from high capital investment in hardware, the running costs are high as well. Depending on the product, cost from a multilayer bottle is easily 30 to 100% more expensive in comparison against monolayer technology. Plasma coating machines are simple to operate in comparison with the complex process conditions of multi-layer technology.
Proven technology
The new coating machines build upon lots of experience gained in the past. The company bases its new carbon coating technology on a discovery made by a Danish engineer in the 1950’s. Since then, the technology has been gradually improved, and has proved itself worthwhile. Delta Engineering lifts the technology to a higher level.
The technology for plasma fluorination has been on the market for 10 years now. This very promising technology is approved by a major agrochemical firm.
The comPETence center provides your organisation with a dynamic, cost effective way to promote your products and services.
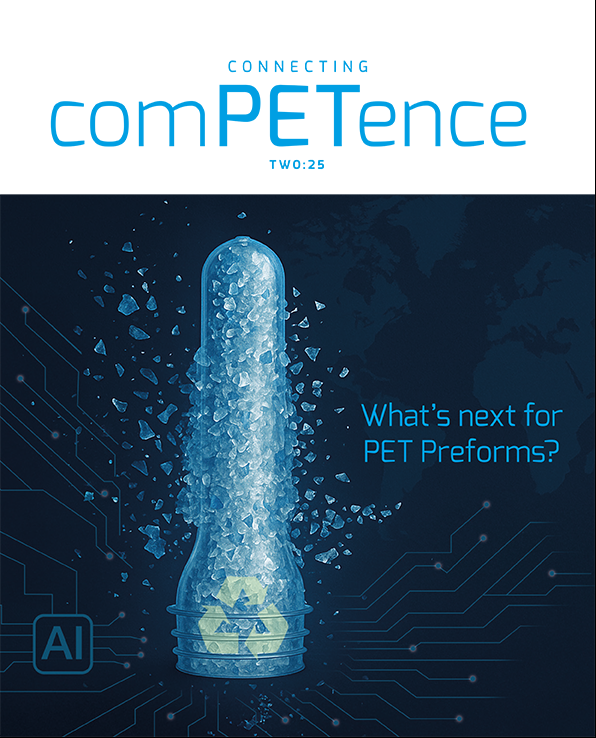
magazine
Find our premium articles, interviews, reports and more
in 3 issues in 2025.