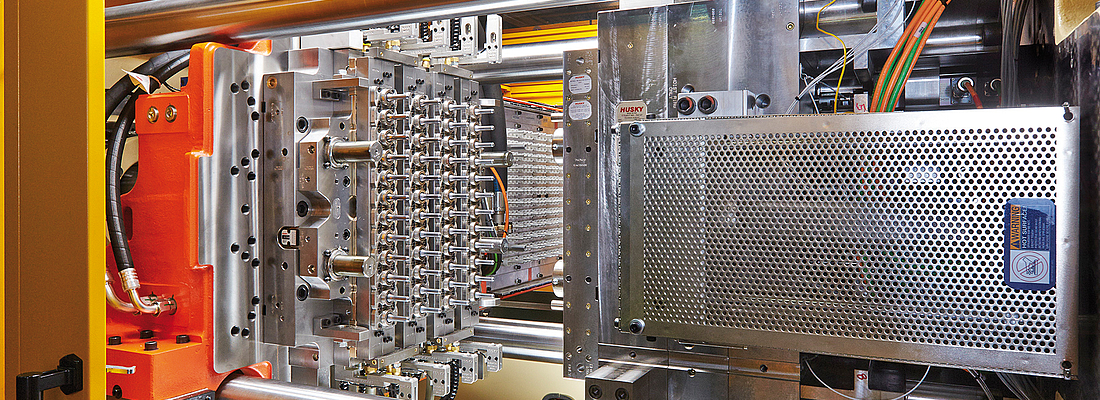
Since the early days of PET adoption in the packaging industry this material has been recognized for its outstanding properties, allowing it to replace glass and aluminum in many food, beverage, home and personal care products. In addition to the functions of containing and dispensing a product, as well as delivering a marketing message to the consumer, a package must provide necessary protection for its content, at least for the duration of the planned shelf life. Some simple examples include the need to keep the carbon dioxide content of a carbonated beverage from escaping, preventing oxygen from reaching sensitive juice and sauce products and limiting exposure to light for dairy applications, including visible, ultra-violet or infra-red. While PET provides a better gas barrier than many other packaging polymers, it is still permeable and some gas exchange takes place between the content of a package and the environment, often becoming the factor that limits product shelf life.
The challenge of providing adequate product protection increases as package sizes decrease. The rate of gas ingress (or loss) is proportional to the surface area of a package, while the total amount of gas that can be allowed to enter or leave a package is dictated by the product volume. Surface to volume ratio inevitably increases as package volumes decrease.
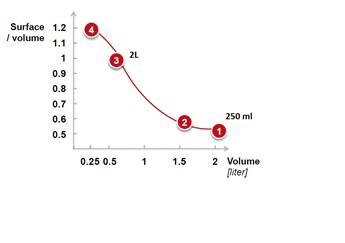
Fig. 1: Barrier requirements become more challenging as package volumes decrease
This requires packages to have improved barrier properties to support the necessary product shelf life. Market trends, driven by a consumer preference for smaller packages (portion control and on-the-go consumption) and the ever-increasing need for brand owners to differentiate their products on store shelves, suggest that smaller volume packages will become increasingly more common. A small volume package also allows brand owners to offer their products in emerging markets at a price point that is accessible to the larger group of potential consumers without eroding the value.
There are multiple approaches to extending the barrier properties of a PET package and the ultimate choice of the technology will be dictated by multiple factors. Among those factors are the level of required barrier improvement, the need to maintain production flexibility, constraints placed by the logistics chain and of course, the total cost to produce.
The easiest solution to improving the barrier properties of a traditional PET package is to blend PET at the injection system extruder with one of the many barrier materials available on the market. The resulting blend will have improved resistance to gas permeation (passive barrier) or may even actively trap oxygen molecules (active oxygen scavenger) in the polymer matrix.
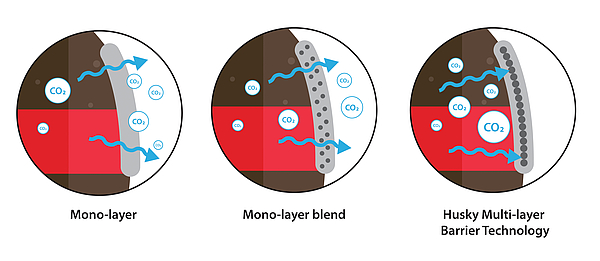
Fig. 2: Comparison of CO2 loss – mono-layer versus mono-layer blend versus Multi-Layer Barrier Technology
Not requiring any equipment changes other than the polymer dosing and mixing auxiliaries, this may be an appropriate solution in some situations. At the same time, the simplest solution, as it often happens, has serious limitations or even penalties. The barrier improvement factor is directly proportional to the amount of barrier material added to the blend. As the additive level is increased, the clarity and transparency of a PET bottle typically suffers, placing a limit on how much improvement can be reached while maintaining the desired package appearance. Even more significant is the barrier material cost penalty of a blend solution and its potential impact on recyclability when compared to a multi-layer package.
Bottle coating is another available option to improve the resistance of a monolayer PET package to gas permeation. A thin glass-like coating on the internal surface of a bottle can constitute a highly effective passive barrier to gas permeation. The coating is applied in a plasma treatment following the blow molding process. Silicon oxide coating is clear and transparent, while amorphous carbon coating imparts a light yellow tint to a clear package. The effectiveness of such coatings may be limited by the bottle creep, which may disrupt its integrity and lower the net improvement of the barrier properties. In contrast, the multi-layer co-injection barrier solution provides a greater package design freedom, since the package creep and deformation levels are less critical or even inconsequential for the barrier performance. It further allows to introduce active oxygen scavenger materials, preventing oxygen ingress and lowering oxygen content in the headspace. A multi-layer structure providing a barrier to light can also be created when required for the application.
On the operational level, coatings are attractive due to a low cost of consumable materials. At the same time, a plasma coating system represents an additional process step between bottle blowing and filling, which can pose a challenge to preform molders supplying multiple blowing sites. The choice of a system supplier is determined, among other factors, by the type of the coating selected. Quality control of a barrier coating is accomplished through monitoring of the process parameters. The silicon oxide coating itself can only be detected using laboratory grade instruments such as a scanning electron microscope. Quality of the barrier layer distribution in a multi-layer preform can be confirmed by both non-destructive and destructive inspection means.
A multi-layer preform is produced in a sequential injection or a simultaneous co-injection process. In both cases, the resulting preform contains a distinct layer of the barrier material sandwiched between the inner and outer layers of PET. Even though barrier materials are typically approved for food and beverage applications, as an added benefit this results in only PET being in direct contact with such products. Preform blowing and filling steps subsequent to injection molding do not require changes to the existing production lines. This means that, when desirable, a producer is able to maintain the flexibility of operating a central injection molding facility supplying multiple blowing and filling locations.
Husky’s Multi-Layer Technology is a complete integrated system solution building on the best-in-class monolayer preform performance and reliability of the company’s HyPET HPP product line. Simultaneous co-injection results in faster cycle times and the ability to inject thinwall preforms, since both PET and the barrier materials flow into the mold cavity through the gate at the same time. The multi-layer melt flow is formed in the nozzle of the co-injection hot runner, while the standard mold cold half can be interchanged between the monolayer and the multi-layer systems, assuming the same hot runner pitch and nozzle interface is maintained. While a co-injection system must be configured with two injection units and a co-injection hot runner, as well as necessary auxiliaries and control system, Husky Multi-Layer systems offer complete flexibility to run mono-layers tools (complete mold and hot runner) or to produce mono-layer preforms without switching tooling, if this becomes necessary due to changes in demand, season or target markets.
Both passive and active barrier materials are more effective when used in a concentrated layer in a multi-layer package, compared to a monolayer blend with PET. The same barrier improvement factor (and the resulting product shelf life) can be achived in a multi-layer barrier package using approximately 50% or less of the blended barrier material. The effect has been reported with co-injection systems and confirmed in laboratory studies. This holds true for both the oxygen scavenger applications, where oxygen must be prevented from reaching the product, and for passive barrier applications, where carbonation must be kept inside the package, although the mechanism differs. In the case of a passive barrier layer, the gas permeation rate is reduced by creating a denser “fence” for gas molecules. In the case of an active scavenger, the useful capacity of the scavenger material is extended by ensuring only the oxygen molecules that reach the barrier layer are reacting with the scavenger and are trapped.
Even though light barrier applications do not involve gas diffusion mechanisms, similar material cost and package performance advantages are derived from a multi-layer technology. Shelf life of dairy products (such as UHT milk) processed for long shelf life at ambient temperature is limited, among other factors, by the breakdown of riboflavin (vitamin B2) and oxidation of proteins and lipids triggered by exposure to light, leading to a loss in nutritional value and off-flavors. Monolayer preforms containing significantly above 12% of a TiO2 master batch (titanium oxide commonly used to produce a strongly opaque white) are difficult and at some point impossible to stretch blow, thus limiting the extent of light barrier that can be achived. In contrast, multi-layer preforms containing a black PET layer hidden within an opaque white PET achieve signicantly lower light transmission, blocking up to 99.99% of light up to 650 nm wavelength, while reducing the amount of expensive opaque white additive that is needed.
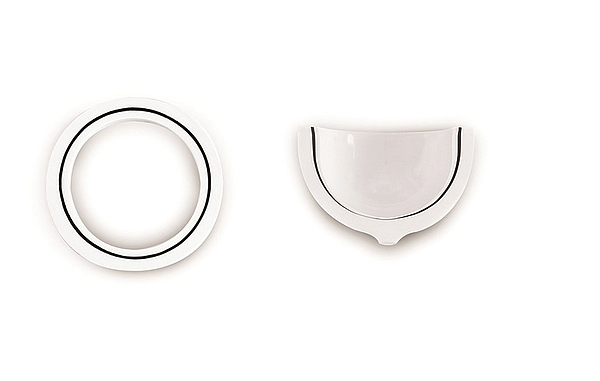
Fig. 3: Multi-Layer Barrier Technology positions the barrier exactly where it is needed. Pictured left is a biased black layer positioned away from the surface towards the core. Pictured right is a fully encapsulated dome
The ability to provide uninterrupted barrier layer coverage through the preform dome improves total package barrier performance and is especially important for oxygen and light sensitive applications. In particular, some food types (for example pasta sauces) do not readily mix inside the package, creating a potential for local oxidization of the product in segments of the package not covered by the barrier layer, causing spoilage. The Husky hot runner design and control system allow molding of the multi-layer preforms with either closed or open dome tips (with or without barrier layer in the bottle base), in the former case providing outstanding control over the termination (trailing edge) or the barrier layer.
In 2015, Husky began working with select early adopter customers to introduce their Multi-Layer Technology to the market. Customers have since chosen to rely on this solution for a variety of applications, including for carbonated soft drinks, mineral waters, juices, sauces, and now seeing expansion into dairy, beer and personal care products. In all cases, Multi-Layer Technology has enabled customers to achieve an equivalent shelf life at a lower cost or improved shelf life at the same cost while maintaining the full flexibility of an injection molding solution with no additional constraints on downstream equipment or logistics.
An important factor to lowering the total cost to produce is the ability to precisely dose and distribute just the right amount of barrier material for a given application while maintaining the robust productivity expected of Husky HyPET HPP systems. It is well known that material cost is a major contributor to the total cost of a package. Barrier materials, while making up a relatively low (typically 2% to 15%) percentage of a package’s weight are substantially more expensive than PET. This makes it critical to ensure the minimum necessary amount of barrier material is delivered to each mold cavity and distributed in the most effective manner within the preform.
This level of advanced control is only possible with a fully integrated system that utilizes a unique, state-of-the-art hot runner design. The hot runner is based on technology that enables an unprecedented level of balance, even before any controls are tuned for the application. This reduces the number of times melt flow is split in the hot runner, which is the single most significant contributing factor to hot runner imbalance.
This hot runner technology also provides an unprecedented level of design freedom, optimizing melt channel layouts of two material melt delivery systems for a high degree of thermal control. Many barrier materials have a lower melting point and are more temperature sensitive than PET. Overheating and excessive residence time may lead to material degradation. This not only impacts preform and bottle quality, but can also increase hot runner refurbishing intervals. With Husky’s co-injection hot runner the two material delivery systems are thermally separated and independently controlled by the embedded Altanium control system, ensuring the barrier material is only subjected to the PET processing temperature when the two materials are combined prior to the gate.
Injection molders familiar with co-injection will recognize that in the attempt to improve hot runner balance and ensure melt flow and temperature rates are as uniform as possible across multiple gates, the hot runner may be tuned by lowering and raising temperatures of manifolds and nozzle tips. Husky hot runners provide control flexibility through an increased number of manifold zones and individually temperature controlled tips. Traditional pneumatic actuation of valve gates has been upgraded to an electric servo, plate actuated synchronous valve gate system. At the same time, the high level of balance means that the range of temperatures used in further tuning the performance is significantly reduced, further decreasing the maximum temperature experienced by barrier material.
Over millions of cycles of of production use in the field, Husky customers have commented on the barrier hot runner’s performance stability, and this is without the need for unplanned maintenance. When running temperature sensitive barrier materials, purging both hot runner melt delivery systems with PET during system shut-down and re-start is a good practice that has been automated. Even the best maintenance practices may leave room for unplanned events, such as contamination of source resin by foreign material. If a contamination particle finds its way into the hot runner, the most likely area for a blockage is the hot runner nozzle, where melt passages are smallest. It has historically been notoriously difficult to clean this area, often requiring complete hot runner disassembly. The HyPET HPP5 barrier system features a front removable nozzle design, which allows the maintenance or replacement of hot runner nozzles while in the press, by latching over the mold cavity plate to expose the tips.
While co-injection molding is still more complex than traditional mono-layer injection molding, the operation of the complete system is facilitated by Husky’s intelligent, preform-centric control system, integrating all aspects of the injection molding process and auxiliary equipment. Process setup for a new application begins with establishing a mono-layer process for preform quality. When barrier material injection is enabled, the control system automatically adjusts the PET injection profile based on the barrier content and generates the barrier injection profile, which can be further fine-tuned by the operator. Customers new to co-injection have found the Husky system user friendly and were able to confidently operate it in production after a short period of training, while being assured by the fast and effective support available through Husky’s service network for all aspects of system operation.
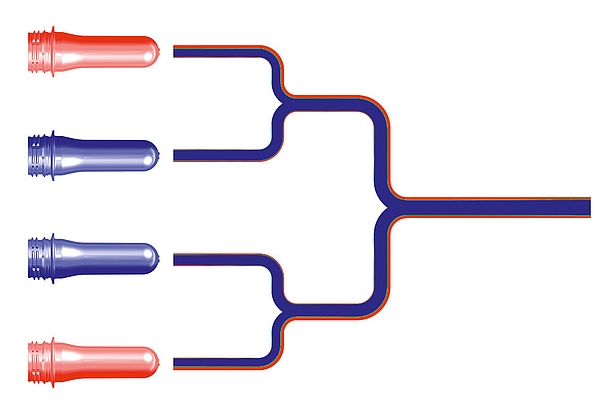
Fig. 4: Conventional manifolds split the melt channels many times, which creates shear related imbalance.
Husky’s Multi-Layer Technology offers a complete, integrated solution for manufacturing food and beverage products requiring enhanced barrier properties that is highly cost-effective, productive and flexible. It allows brand owners to rely on PET for more appealing packages. Packages that stand out on store shelves and support conversion from alternate materials, all factors that help to support the growth potential of PET packaging.
Early adopter customer sees success with Husky’s Multi-Layer Technology
When introducing its new Multi-Layer Technology Husky partnered with one of Europe’s best known preform and PET bottle manufacturers to test and validate the solution in the field. Having already established a proven track record of working together to validate new technologies, Husky knew this European customer would be a good fit as an early adopter partner. The two companies also shared a common goal of developing solutions that push the PET industry forward, as well as grow the addressable PET market. It was also perfect timing for Husky’s customer, as they were experiencing maintenance, service and stability issues with their existing co-injection barrier systems and were looking to find an upgraded solution.
The installation and start-up of the first Multi-Layer system in the customer’s European facility was fully supported by Husky’s regional service engineers, as well as their Multi-Layer Barrier subject matter experts who were present from the company’s headquarters in Bolton, Ontario, Canada. As part of the qualifying process, the system successfully completed uninterrupted production runs for two Multi-Layer preform applications, one being a 28 gram preform for a carbonated water bottle application and the other a 14 gram preform for a juice application.
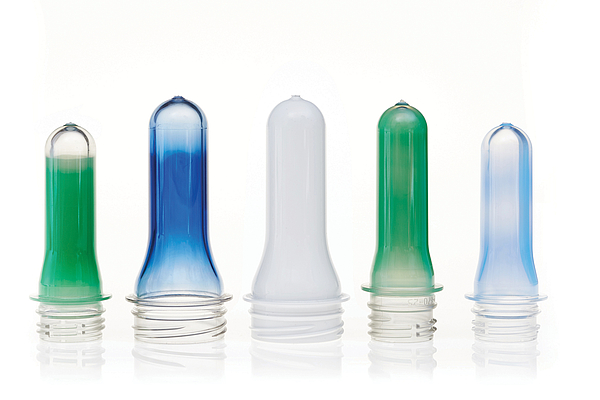
Fig. 5: Multi-Layer Technology for barrier is suitable for a variety of applications, including for carbonated soft drinks, mineral waters, juices, sauces, and now seeing expansion into dairy, beer and personal care products.
In fact, when comparing Husky’s new Multi-Layer Technology to their existing co-injection barrier system, the customer saw no change in performance after running the system for several months. In the past when testing alternatives they had typically seen deterioration in barrier performance after several weeks and that was not the case here. They also saw significantly better control of the barrier weight. The accuracy and repeatability to control the barrier content in the preforms produced on the new Husky Multi-Layer Barrier system was significantly better than what they were currently achieving. Both applications were produced with a tolerance on the barrier content within +/-0.5% of the total preform weight. This was achieved while realizing a 40% faster cycle time.
When measured against the existing competitor co-injection system running the exact same application Husky’s Multi-Layer system ran more consistently for a longer period of time with no drop in performance and decreased hot runner maintenance. Today, this customer is continuing to work with Husky on future Multi-Layer Barrier projects.
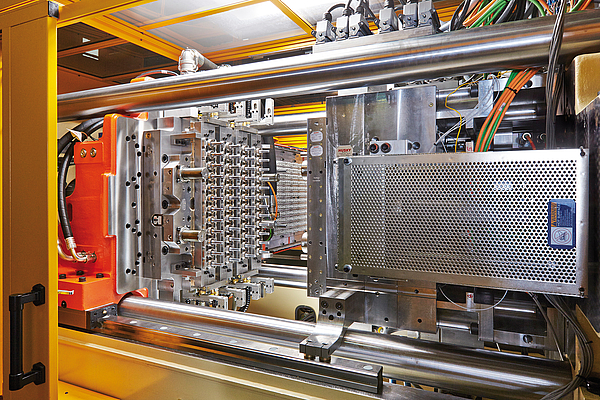
Fig. 6: Multi-Layer Barrier Technology combines the benefits of Husky‘s proven HyPET HPP5 system with a revolutionary new hot runner to enable the most precise and controlled dosing of barrier material.
The comPETence center provides your organisation with a dynamic, cost effective way to promote your products and services.
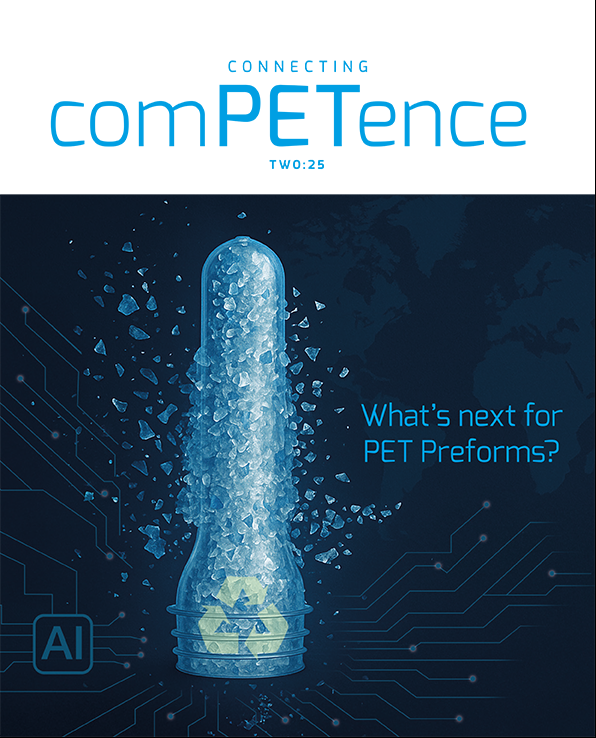
magazine
Find our premium articles, interviews, reports and more
in 3 issues in 2025.