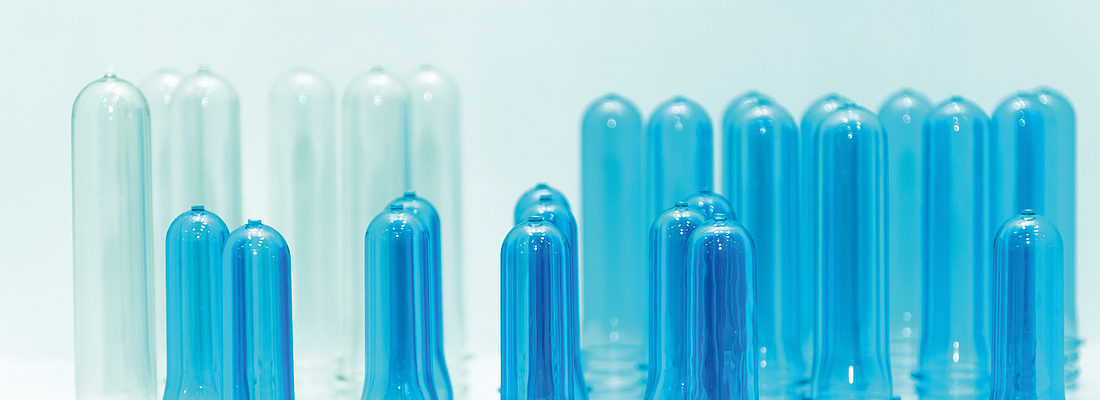
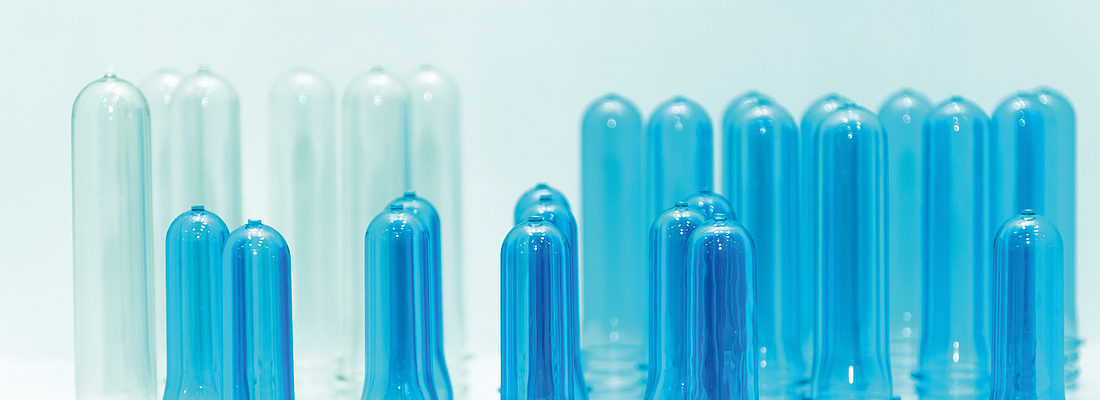
The global approach to saving raw material in the bottle base - Part 2: Preform solutions offered by the industry today
In general, PET lightweighting initiatives help packaging businesses be more economical and also sustainable. Lightweighting helps to improve the environmental footprint of PET packaging and reduce the amount of resin usage. But: Lightweighting also has an influence on the bottle performance. In this context, preform bases are currently subject to much discussion in the PET packaging industry.
comPETence was approached by a bottling company to address the topic of preform bases. After various discussions and attempts at comparing the alternatives on the market, we soon realized that this is both an interesting and provocative topic.
“We sell packaging - not drinks”
The industry faces enormous cost pressures. Today bottling companies tend to see themselves as vendors or traders of packaging and its recyclable material. In comparison, their product almost fades into the background and – from a cost perspective – the contents are of secondary importance: “We sell packaging - not drinks.”
Several statements from our conversations in bottling plants show why we are happy to, and indeed must, address this topic:
Anything new tends to make us feel uneasy and uncertain. But if there is a chance of saving material, we should try and do so for every project – both to save costs and to help the environment.
Our job is to maintain production. How can we test all of the alternatives?
How can we get a sense of the various technologies and their influence on our product and production?
What does this mean for preform production? What does this mean for bottle blowing as well as the bottle itself and its characteristics?
Though we run the most modern and expensive plants, they are operated by employees who only receive a few weeks of training. It’s like we’ve put a Formula 1 racer in the hall, but the workforce is a far cry from these high end machines. In the end, the result should at least make the podium.
Why can’t the manufacturers of machines for injection moulding, blow moulding, and filling all be on the same page? Or at least agree on a few facts? Or are the physics of the machines so different?
When we consider bottle costs, material costs account for around 70 - 80% of total costs, depending on use, technology, and bottle size. It’s no wonder that since the introduction of stretch blow moulding technology, various adjustments have been made to minimize bottle costs.
On the other hand we must satisfy the diverse technical and technological requirements of the production process, which include such aspects as PET material, injection moulding, bottle blowing, filling, transport, and recycling. We must also consider the consumer, for whom convenience (to varying degrees depending on the product) and sustainability are important. All of these points are directly related to the wall thickness of the bottle and consequently the weight of the bottle.
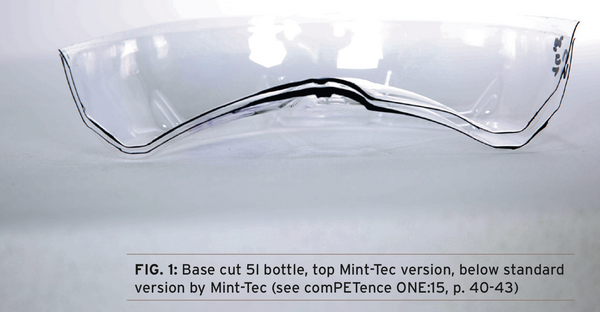
The operational performance process – PET stretch blow moulding
The PET stretch blow moulding operational performance process includes all activities that occur as part of the performance process, i.e. all activities from procurement to the sale of services (filled PET bottles). These activities should also be routinely considered:
Raw material use:
- Are the most technically efficient materials being used?
- Are the most economical materials being used?
- Is it possible to reduce the materials consumed?
Workforce:
- Quality of employees
- Quantity of employees
- Distribution of competences among employees
Machinery (in regards to technology):
- Quality of machines
- Quantity of machines
- Capacity utilisation
Capital expenditure
Point in time
Raum
In lightweighting other aspects come into play. In particular, the increasing complexity of process handling and control must be taken into account while also keeping in mind the flexibility needed on the filling lines.
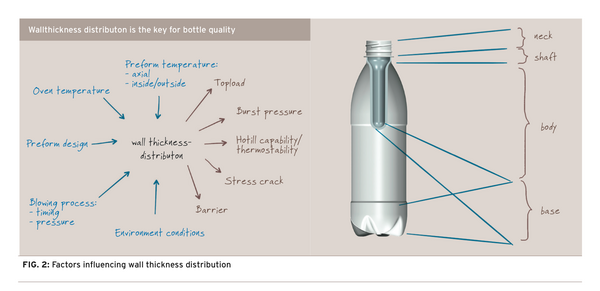
Wall thickness distribution is the key to bottle quality. But: What exactly does bottle quality mean today (figure 2)?
Lightweighting
The following must be considered in all lightweighting efforts:
-the consumable product must be protected (shelf life)
-the consumer must be protected
-the brand must be protected (its reputation should not be damaged by “fragile” bottles/containers)
While keeping these aspects in mind, we should question whether reducing material consumption is possible and rational. Image ... shows the various parts of a bottle where it is possible to conserve materials: Thread, shaft, support ring, preform body, preform base. In order for the bottle to fulfil its functions and specifications, each of these parts must have a certain wall thickness.
The rest of our observations will concern the preform base, which provides the material for the base of the bottle. After optimizing and reducing the weight of the preform itself numerous times, it is necessary to focus on the contour of the preform base in order to conserve more materials.
Figure 1 shows the extent to which the geometry of the preform base can affect the distribution of material in the base and consequently the weight of the bottle’s base.
In addition to spherical bases and other geometries, there are technological processes in use or in development today with the goal of thinning the preform in the base. There are two different fundamental principles for reducing the weight of the base:
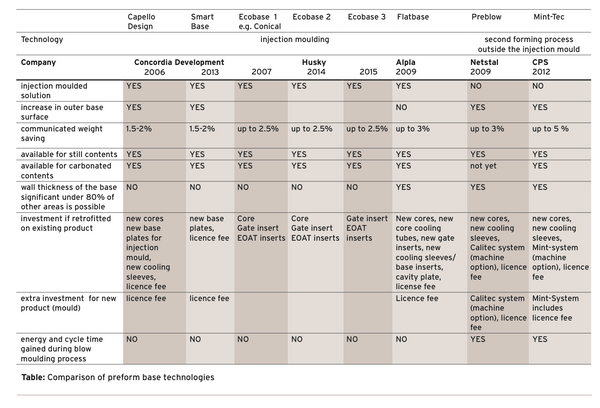
Process:
Lightweighting of a preform base by reducing the total preform weight. This affects the preform base and consequently the bottle base once the preform is blown.
Solution providers:
a. Capello Design, Concordia Development
b. Smart base, Concordia Development
c. Eco base, Husky Injection Molding Systems
d. Save base, MHT Mold & Hotrunner Technology
e. Flatbase, Alpla
II. Injection moulding of the preform and subsequent forming of the preform base
Process:
Lightweighting of a bottle base without reducing the total preform weight. In this second case, we observe a better distribution of the bottle base weight (by preblowing or forming the existing preform base) without a reduction in the preform weight. In this case the only way to save bottle weight would be to utilize a lighter preform.
Solution providers:
a. By blowing/preblowing the base area
- Preblow, Netstal
b. By pressing the base area
- Minting, Creative Packaging Solutions (CPS)
General points
One of the most important characteristics of a preform is its base and in particular its thickness and its internal geometry. In fact, the function of a preform base is to offer enough mechanical resistance to the stretch rod so that the preform body can be properly stretched before being blown.
If a preform base is too thin, there will not be enough mechanical resistance to the stretch rod. As a result, the preform tip, rather than the preform body, will be stretched.
This can be avoided by reducing the temperature of the preform tip, but this has two potential negative consequences:
• The material on the preform tip will not stretch or will not stretch enough because it is too cold
• Consequently, all of the material will remain stuck at the bottom of the bottle unable to be stretched
In order to ensure that the material maintains proper bi-orientation stretch ratios, the diameter of the stretch rod tip should always be smaller than the internal diameter of the preform tip, otherwise the stretch rod will impact the preform tip too soon, altering the stretch parameters (as if stretching a shorter preform) and deviating from the injection point during high and low pressure.
It is important to consider the airflow inside a hemispherical preform (the air flowing in the space between the exterior of the stretch rod and the interior of the preform) and how this will be affected by a change to the internal geometry of the preform base.
A petaloid base has to withstand a series of tests, such as stress cracking, burst, thermal stability and rocker bottom tests. Each of these tests has specific requirements that do not necessarily coincide.
For example, in order to obtain the best possible stress cracking result it would be best to eliminate most of the material at the bottom of a bottle base, but doing so would negatively impact the results of the burst and thermal stability tests.
Therefore it is important to strike a balance between amorphous material, its thickness and its dimensions according to the kind of bottle base used.
The discussions above make clear that everything is becoming increasingly complex. As a result, we recognize that the design of the preform base is of fundamental importance.
Statements on PREFORM BASES
Jochen Forsthövel; Krones:
In general: The thinner the base, the less the heat that must be applied to the base and the less the heat that must in turn dissipate over the base of the mould. The lower the wall thickness of the base, the quicker the preform can be heated through.
On the subject of preform bases or rather lightweighting projects, the following should be considered: Is the new preform to be designed for an entirely new project or is it intended for use in a project for which a retrofit package will modify the injection moulding machinery in order to produce a lighter bottle with minimal investment costs.
In our experience, the best method for new projects is to design a short preform with a high degree of stretching and low base wall thickness. In terms of bottle characteristics and the process window, we see the best results with stretch blow moulding.
In general:
For new projects, we recommend preforms with a rounded base and a high degree of stretching.
For retrofit projects we prefer smart base technology, because the preform has a nearly rounded base.
The disadvantage of the new base geometries, the so-called conical bases, is that some of their bases have “sharp” contours. This can lead to problems, because these contours tend to make the process window less stable and also make it more difficult to find the correct process parameters. The other serious issue is the so-called memory effect. This means that in a thermal stability test as well as with increased blowing station output, the gating point area returns to the preform geometry. In other words, the free shaping of the base can cause problems here.
The preblow process sometimes results in slight fluctuations from centre that are amplified during bottle blowing and lead to stress crack and burst bases. These problems do not arise with the Mint-Tec process because the base is not shaped freely.
Today, new injection moulding systems make it possible to produce a preform with side walls that are 70% as thick but without the PET material used in the preform base area having negative effects on the later blowing process. Therefore we see that the standard preform offers advantages with the new generation of machines. In our experience the critical hurdle for extreme applications and low base weights is the thermal test: here sharp bases, as is the case with the conical base and the original Capello Design, can be damaging.
Dr, Klaus Hartwig; Nestlé
When interviewing Klaus Hartwig from Nestlé last year (PETguide 2014, p. 6-11), he said that “…efficiency is extremely important but it comes after requirements like product quality and consumer value.” So, the consumer must be at the center of our innovations and efficiency is a very important part of every development, but should not be the sole focus.
Dietmar Marin, Hermann Riedlsperger; Alpla
The various approaches to modifying preform bases in order to make bottles lighter are a fundamentally positive development that allows for the conservation of PET material while taking costs and the environment into account. We do not suggest that every bottle be blown with an Alpla Flatbase preform, but when it makes sense, we do it for the aforementioned reasons – in cooperation with our customers and with great success. We have already implemented many projects, including many very large projects, and each year we deliver several billion preforms with our flatbase to our customers and our own stretch blow moulding operations. In the process, we have learned a lot.
We consider each project individually. Pushing the current technical-technological limits of PET technology requires the very best at all levels to keep the entire process under control. Without a doubt, the process window is tighter, requiring new generations of machines, experienced operators, and plants in excellent condition. All things that are also required to produce a super lightweight water bottle with an 8g preform with a spherical base.
New developments are often initially met with resistance, making it extremely important to support the user. Project-related optimisations also take place so that conserving materials with our Alpla Flatbase preforms is more user-friendly.
The best performance is achieved when the system is well-coordinated. The investment is worth it; it protects the environment and your wallet.
The comPETence center provides your organisation with a dynamic, cost effective way to promote your products and services.
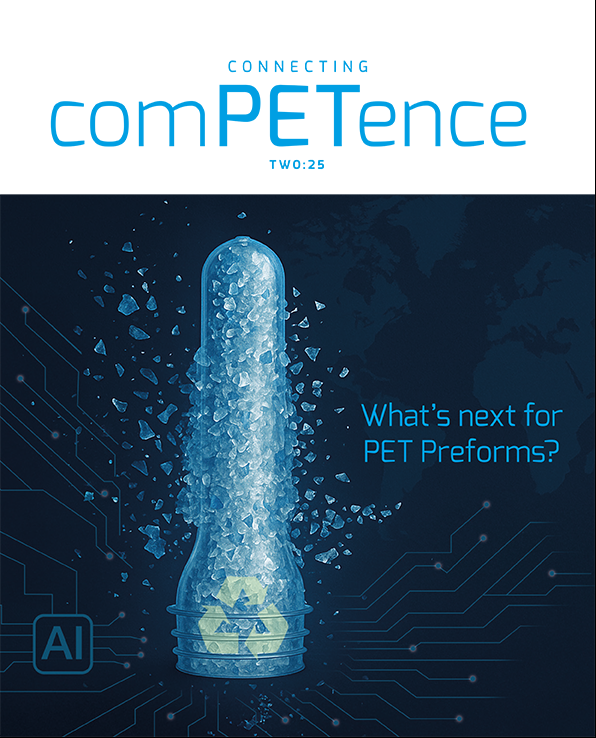
magazine
Find our premium articles, interviews, reports and more
in 3 issues in 2025.