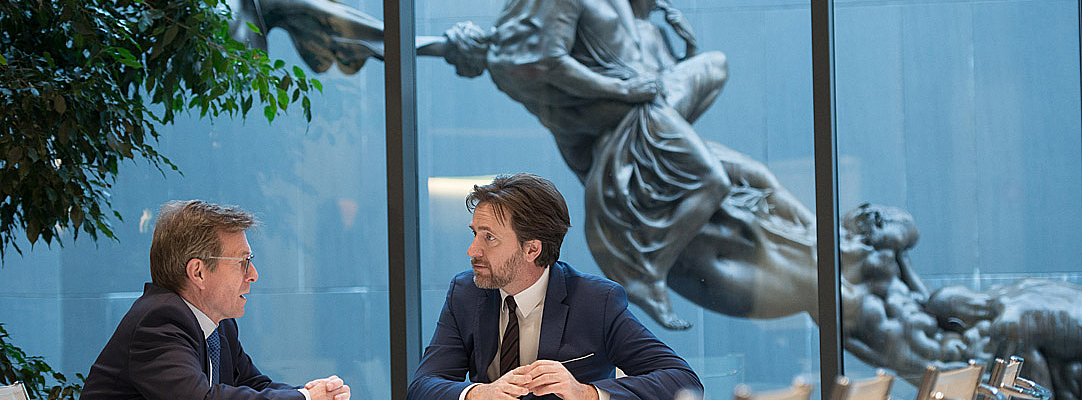
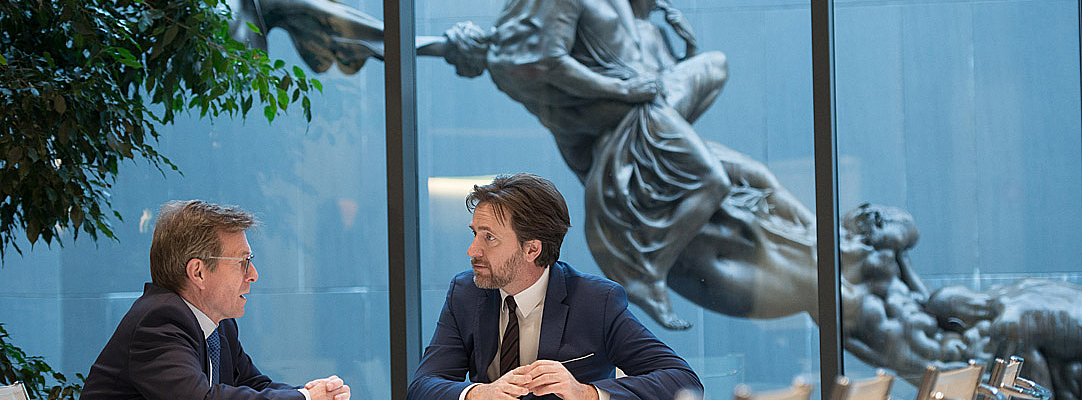
Source: PETnology
Meeting challenges in the film packaging market head-on
Our high degree of vertical integration is the heartbeat of our company
Thanks to its versatile applications in a diverse range of industries, plastic film remains a key material. Films are still one of the most important products of the plastics industry – despite environmental concerns. Market researchers expect global plastic film consumption to rise to 71 million metric tons by 2020. An interview with Dr. Andrea Rigliano, Emilio Del Re, Andrea Carraro, BANDERA, on the challenges within the packaging film market by Prof. Dr.-Ing. Otto Appel
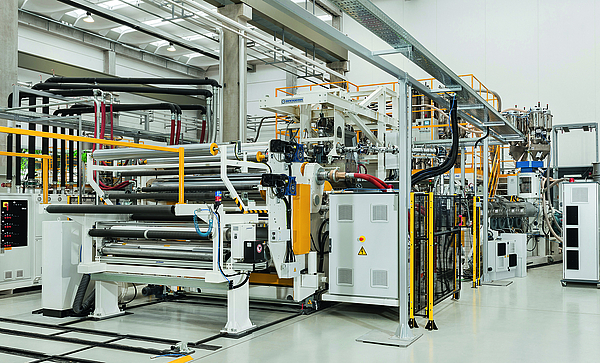
Demand for plastic film shows strong regional variation. One major difference lies between applications in “saturated” industrialised nations and the dynamics in emerging markets in the Asia-Pacific region, South America, the Middle East and parts of Eastern Europe. China and India, the world’s most populous countries, naturally have a massive share in consumption and growth potential. Together, the two countries account for around one third of the global film market.
We spoke to Bandera’s Dr Andrea Rigliano, Emilio Del Re and Andrea Carraro about the challenges and technical solutions facing the global plastic film market. In our interview, we primarily focused on flexible and rigid packaging for food and non-food applications.
MARKETS
Which regional markets is Bandera particularly active in?
Rigliano: Bandera has a very strong presence in South America, Europe, China, Saudi Arabia and the Middle East. The Indian market is also growing rapidly. In response to these positive developments, we will soon be opening new commercial and after sales service plants in some of these countries. The PET sheet market in particular is currently experiencing strong growth. Today, PET sheet and blown film each account for 50 percent of total sales. The positive market outlook means that the size of plants and machinery is increasing, generating higher output. The current throughput for large-scale plants is 2.4 to 2.6 metric tons per hour.
What are Bandera’s key figures for 2016?
Rigliano: Our total turnover was approximately 85 million euros in 2016. This is a 7 percent increase compared to 2015, with a 15 percent increase in the PET rigid film packaging sector. We expect a 15 percent increase in total turnover in 2017, as compared to our record year in 2015. In other words, we are looking forward to another record year. We also added new technical hires in 2016, for a total of 173 employees; 70% of the whole team is involved in designing, manufacturing and servicing product lines.
TRENDS IN FILM
What are the reasons for the film market’s continued growth – despite environmental concerns?
Rigliano: Well, there are quite a few, such as the barrier properties of films or composite films, extension of shelf life, thermal stability, recyclability and sustainability. As far as recyclability and sustainability are concerned, the focus is on the volume of material used, in other words on film thickness, as well as on recyclate processing, energy consumption and thus on production costs.
What are the changes in consumer behaviour that play a role here?
Rigliano: Packaging units such as yoghurt cups or other thermoformed food packaging are becoming smaller – a trend that we are also observing in PET bottles. Consider an example from Italy: Until 1990, Galbani cheese was available in 1kg or 500 gram packages. 250 gram packages were added later, and today even 120 gram packages are available. The variety of the packages are wider and with attractive designs.
PACKAGING CHARACTERISTICS
What packaging characteristics are required in this context?
Rigliano: The most urgent request by the food industry includes the possibility to use recycled clean material as PET against habit to use PS for instance. Possibility to lower the weight of thermoformed packages is also a strong argument especially in Europe to keep as lower as possible the tax amount on plastic packages distribution.
How does Bandera deal with higher market demands in terms of technology and costs?
Rigliano: Observing market trends is very important to us, both with respect to all materials which are currently being used for film production as well as those which will be used in the future. Polyethylene (LDPE, LLDPE, HDPE) holds around 73 percent of the plastic film market. Our blow film plants produce films for all kinds of applications, including for agricultural use. The questions we ask ourselves today are: What are the developments in the areas of PP, PS and PET “rigid” film. Thanks to the excellent characteristics and options that PET offers, PET film is becoming ever more important for high-grade packaging, both as monolayer and multilayer film. We are working with our customers to find ways to meet a variety of requirements. The technical solutions we are developing together include material solutions, material combinations and – ultimately – plant designs which will help us create film with the required product characteristics at a reasonable cost with high efficiency on long terms.
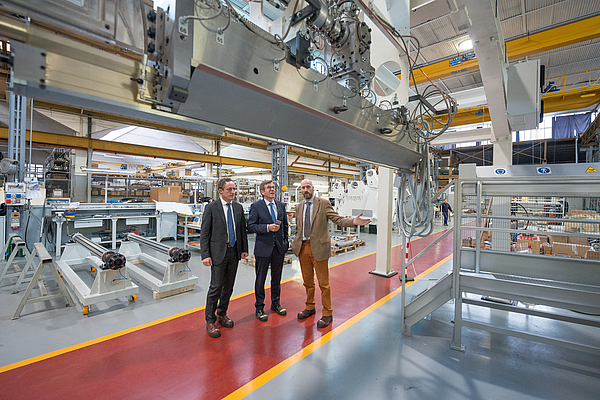
COST DRIVERS
Rigliano: It depends on the application. Let us look at the example of a typical 3-layer APET structure A-B-A for fruit packaging. The two external layers are made of 0.036mm thick virgin APET, while the internal layer consists of 0.428mm RPET (such as bottle scrap). The resulting film has a thickness of just 500 micrometres. The price of material is a key cost driver. That is why we use as much PET scrap as possible. To do this, we need the right technology and plant designs, which in turn have varying levels of energy consumption. Our high-vacuum twin screw extruder (HVTSE) design for PET, for instance, does not require dehumidifying. Co-rotating screws feature a specially designed profile to ensure that the PET polymer is processed very gently, with no thermal and hydrolytic degradation. Processing a high proportion of recyclate without the need for dehumidification considerably reduces costs.
Del Re: Plant availability is also a cost driver, which is why we focus on applying suitable concepts for reducing downtime. Customers also need their plants to be flexible. This is why Bandera has developed concepts which can process APET, CPET, PETG, E-PET, PP or PLA PS. In most of the cases, a recipe changeover does not require line shut down or warm change.
Carraro: This flexibility is particularly important in the sheet market. Most of Bandera’s plants allow processing polyolefins, PS, PLA (which is particularly relevant for the US market) or PET multilayer – even with scrap material. This means that the technology and the plant design provides great flexibility. As far as “PET rigid film technology” is concerned, we have partnership with PTI in the USA. In 2010 we came to an agreement with them. We supply the hot part, i.e. extruders, while PTI deliver downstream equipment, such as calenders and winders. The market has welcomed this cooperation. Octal in Cincinnati, USA, for instance, – one of the big players for raw materials and PET sheets – has recently taken two Bandera/PTI plants into operation.
Rigliano: Multilayer composites make it rather difficult to provide the required processing flexibility, particularly due to the different melt characteristics. The piping between the melting unit and the die can vary depending on the material: PET flows like “water”, which means that it only requires a small pipe diameter, while PP needs a larger diameter. Our extrusion lines have been designed with these special requirements in mind. We can place the extruders near the floor, which makes for easy access and maintenance. Fully automatic screen changers are integrated for the processing of recyclable materials. We use a dedicated system for this purpose, which has been designed to meet our top requirements in terms of throughput and highest melt flow speed and lowest residence time.
How do you manage this type of project?
Rigliano: We start off by establishing customer and market requirements, based on which we carry out material screening and assessment, and determine the projected film composition, layer structures and corresponding recipes. Our focus lies on dimensioning and positioning the system units for the entire plant in such a way as to minimise the footprint. Those pre-engineering activities take around two months. After that, the platforms are designed and the entire plant is built, taking into consideration all requirements with respect to materials, throughput and quality.
Carraro: We are currently in the process of having a plant with a 180sqm extruder platform for PET-PP-PET approved. This plant with a twin screw extruder for PET for yoghurt packaging produces multilayer structures consisting of five layers. We are responsible for engineering the line from start to finish. This is a special service we offer our customers.
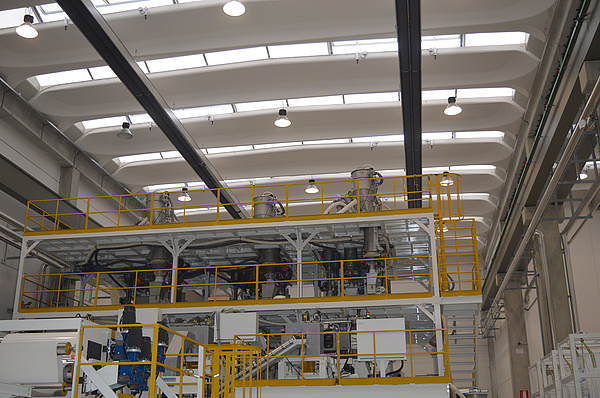
How many plants are you able to set up and take into operation at any one time?
Rigliano: At our Technical Centre, we can approve and test four packaging plants at the same time. Agricultural blow film applications are a different story, though, because the plants are up to 40 metres high and have a throughput of more than two metric tons per hour.
As the complexity of plants and of the films produced increases, isn’t it mandatory to test extrusion lines before setting them up on the customer’s premises?
Rigliano: 80 percent of our plants are tested in our “New house of extrusion” before being shipped to the customer. We use this facility both for machine approvals and for test runs for our customers. This boosts safety in view of increasing complexity and the growing number of market and customer requirements. Our geographically more remote customers in Asia or South America in particular appreciate the fact that we test the entire plant before shipping. However, there are deliveries which are not preceded by an acceptance test run: Customers who have several plants, in particular, only have individual components tested, which are then assembled and taken into operation on site.
Do you do any R&D work on your production plants?
Del Re: Yes, we always have a production plant dedicated to R&D for Blown PE film or PET sheet for various applications. We do work in all areas and at all levels of development, in order to improve existing systems and to find new, innovative solutions for our customers. One should not underestimate the demands placed on us by customers who desire flexibility. They may want to vary materials, such as PET, polyolefins, PLA, or various combinations of layers.
Carraro: We have a production line which we use as a demonstration line, and which can process up to 1.2 metric tons of material per hour. This allows Bandera to test its own developments under realistic production conditions, and to sell customers a finished plant. To give you an example, we used one of these production plants for developing foam PET rigid film back in 2009. Today, we also use our know-how to provide R&D services and to offer training for our customers.
Rigliano: The success of the demonstration plants is due to the recycling boom in Japan, Germany, Italy and – more recently – France. Over time, we were able to identify the limitations of standard extruders, which prompted us to break new ground by developing and using twin screw extruders.
What is the focus of your R&D activities?
Rigliano: Today, 80 percent of our R&D activities concentrate on PET flat film applications, with a particular focus on boosting performance and on processing 100 percent PET bottle flakes. Our customers are most interested in lightweighting and increasing the possible ratio of recyclable material.
Del Re: Rather than just looking at power consumption, customers today value overall line efficiency. Maintenance intervals and product changeovers are amongst the aspects that directly affect the cost structure. We consider ourselves the world market leader for these PET technologies.
Carraro: Many development projects are concerned with a three-layer film with a layer of recycled PET in the middle. Even for food packaging, this is a cost-efficient solution. One aspect that helps to keep costs down is the fact that PET film often uses antiblocking and antistatic agents. By using such additives only on the outer surface layers of these three-layer films, we reduce our use of additives. The functional barrier is typically recognized as FDA and EFSA approved process.
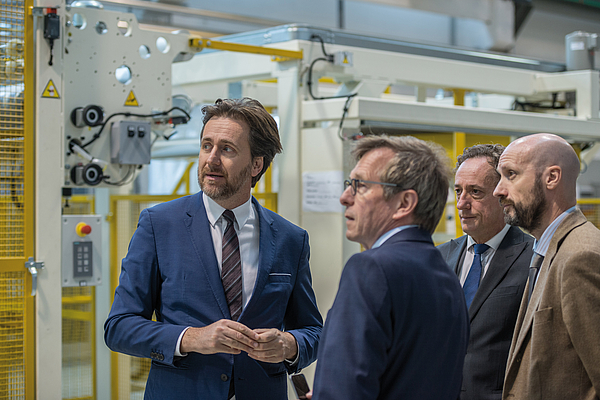
PLANT DESIGN
Market requirements create technological challenges that need to be overcome through the development of machines, plants and concepts. Question?
Rigliano: Our company has a very high degree of vertical integration. We produce our own blown film dies and screws for single screw extruders, rotating twin screw extruders for PET and counter-rotating extruders for PVC. This allows us to act and react faster than others. We can work with diameters between 45 and 320 millimetres for single screws, or up to 200 millimetres for twin screws. Helix mandrels come at an exit diameter of up to 2.6 metres. Our high degree of vertical integration is the heart of our activities even if we are supplying complete plants.
Rigliano: Today we focus on the design and development of plants, and on reducing manufacturing cost while increasing the usage of recyclate materials. The variable quality of flakes places high demands on process management.
Del Re: High output volumes of more than 2.5 metric tons per hour also require special processes for film cooling. We achieve this with special design of the calender rolls and the integrated design of the cooling circuit.
Carraro: Many of our developments in PET sheets are closely tied to the use of a twin screw extruder. The advantages of combining process management with a twin screw extruder is that the material can be fed directly, without having to dehumidify the material first – this is easier and cheaper. We have optimised the process for maximum availability and performance.
Which technical solutions are there for improving plant availability?
Del Re: One important aspect is the cleaning of calender rollers. We can clean the roller surfaces inline, in other words while the plant is in operation, saving time and money.
Carraro: The global market for flexible and rigid packaging is currently seeing considerable demand, as the new innovation protective film for agriculture, the protective films for furniture industries, the new biodegradable bags.
Rigliano: In addition to cold packaging, hotfill packaging is also an important field of application. The CPET market was in decline for a while. Today there is continuous growth. CPET is particularly interesting for microwave applications. We strive to continually improve the thermal stability of hot packaging with new technologies and additives. This also applies to hot beverage cups, which should be thermally stable up to 90 or 100 degrees Celsius.
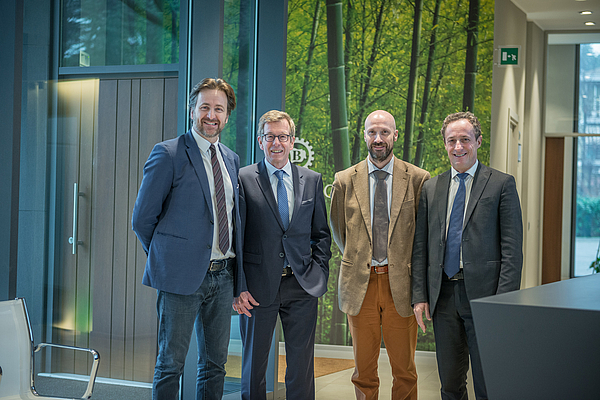
Are there any new developments which may open up new markets, maybe even beyond the packaging market?
Rigliano: Lamination extrusion coating are new developments in the production of multilayer sheets for PET. We are able to laminate or to coat by extrusion during the extrusion process, a development which was triggered by customer requirements. This technology allows us to feed in a barrier film via the calender, producing a new composite under extrusion conditions.
Carraro: Another market which is becoming increasingly interesting is the furniture industry, which has been switching from PVC to PET (editorial note: please also see IKEA on page 81). This is a market that expects extremely high-quality surfaces, creating new challenges for extrusion lines. Europe and US are very interesting markets which have already reached a top level of quality requirement.
When talking about packaging, we must not forget to mention the problem of waste. What is Bandera’s position, and do your customers ever ask you about this aspect?
Rigliano: The PET boom is due in part to its excellent recyclability, which is less favourable for other packaging materials, such as PS. All major brands now have a focus on sustainability and are considering substituting PS with PET. There are regions, such as California, where PS is banned. Here in Italy, too, some companies are looking into replacing foam PS with PET. All of this requires flexible plant and line solutions. Our customers want to be ready to face any changes in the future of packaging.
Carraro: In Italy and France, we are observing a marked trend from plastic bags towards biodegradable packaging. In Italy, all disposable bags are now made of biodegradable plastic, paper or fabric.
Rigliano: The concept of biodegradable plastic materials is not so easy to convey to the younger generation. In schools, children learn about plastic recycling, which is easier to understand: Collect, wash, reuse as a bulk container – this is a clear enough concept. But biodegradability is more difficult to explain. A survey here in Italy showed that 60 percent of standard plastics are recycled, while only 35 percent of biodegradables plastics are recovered.
Despite all the undisputed advantages of PET, it is a recyclable material that still ends up in the oceans. Adversaries of plastic often say that the plastics industry exploits the earth and then strews its products across the environment and in the sea.
Rigliano: There is no question that this is an issue which we have to get under control. How we manage used packaging is something that is up to each and every one of us. I sometimes even wonder whether the degree of civilisation in a particular country is reflected by the way waste is managed, in other words if used packaging is considered a recyclable material. It goes without saying that the more populous a country is, the more packaging is needed – but what waste management concepts are there? Take China, for example, which is producing vast amounts of waste and not managing it very well yet.
Del Re: Italy has introduced a packaging tax to curb the amount of packaging used, which amounts to 120 euros per metric ton and in all Europe there is a tax on packages to improve the recycling process.
Carraro: It is clear that we cannot do anything without plastics, but growing sales figures should not lull the industry into a false sense of security. To avoid polluting the oceans, industrial companies, industries and - above all - governments have to reinforce efforts by using innovative technologies.
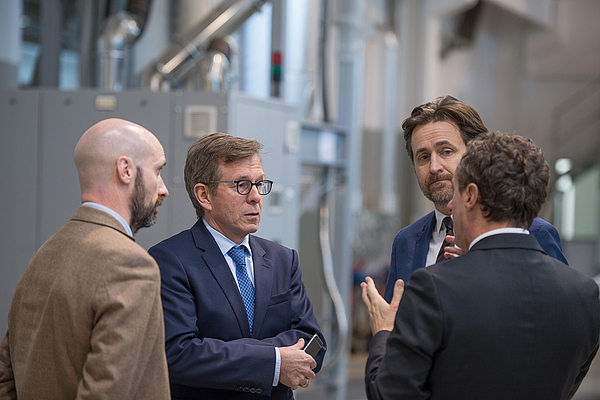
PLASTICS IS LIKE POLITICS
Rigliano: Plastics is like politics. If you understand it, you can talk about it. If you don’t understand it, you should stay out of the conversation.
What challenges are you expecting for the future?
Rigliano: The technological challenges of the future are very well reflected in our ongoing and upcoming development work. The following R&D projects of Bandera are of great interest to the market and have the highest potential for developing into future industrial applications that will boost our business:
a new generation of multilayer sheet extrusion lines with a foam core layer consisting of PET, PP or PLA;
a new generation of flat extrusion die coating systems for the extrusion of high barrier composite films based on PET and PP;
a new purification system to be used in the high-vacuum direct extrusion process and targeted to markets that are highly sensitive to EFSA certification issues connected to the usage of 100% recycled materials in food packaging in a single layer;
a new generation of MDO systems for both rigid and flexible films;
new compact extrusion lines with chill rolls for PET cast films;
an innovative soft-touch roll stack polishing and cooling calender for the extrusion of both semi-foamed PET and PP film.
Another challenge lies in attracting young engineers who are passionate about technology and prepared to travel worldwide to service our plant start-ups. This poses a real problem for us. Young generations of the past had such a passion for technology, but now they must be combine also the willingness to meet customers in remote countries to listen to them and propose technical solutions and train them locally how to take advantage of the technology on field.
The comPETence center provides your organisation with a dynamic, cost effective way to promote your products and services.
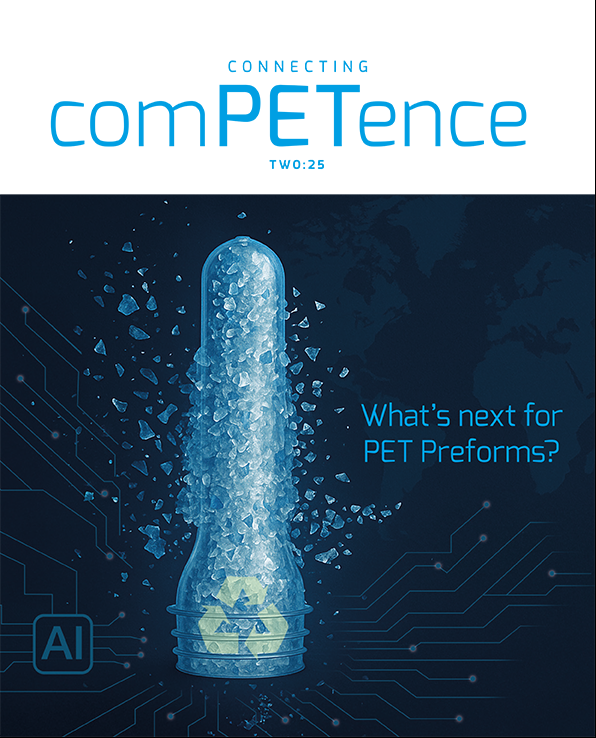
magazine
Find our premium articles, interviews, reports and more
in 3 issues in 2025.