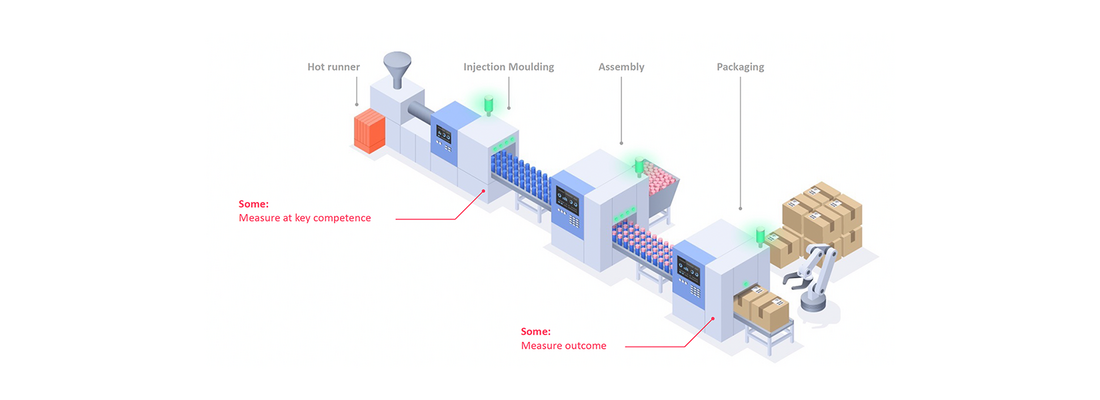
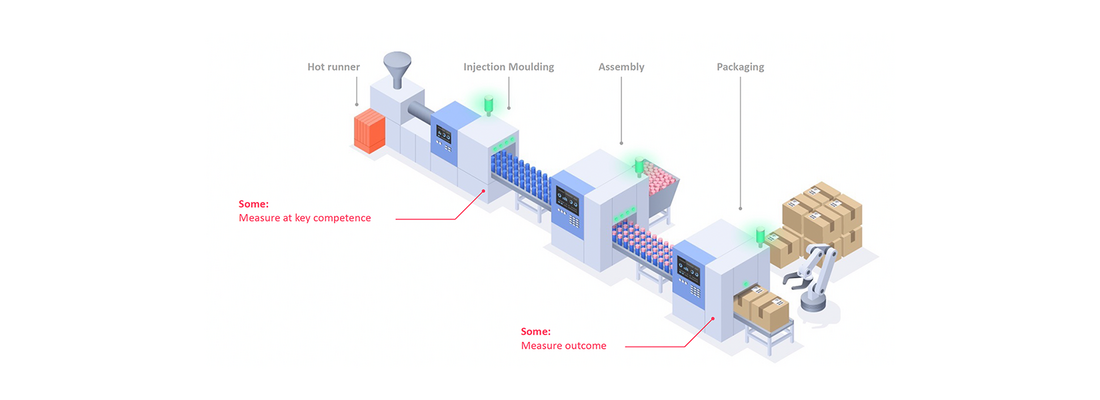
comPETence magazine | ONE:22 | Digital Transformation
Predictive maintenance: New opportunities for further growth, greater efficiency & increased customer satisfaction
There are many reasons to start the digital transformation of the manufacturing processes. And - maintenance is a critical factor. It is key for the success of a producing company, as maintenance costs account for up to 40% of the total costs taking into account the personal, procurement and the commissioning. A number of questions occur: How to prevent escalations? How to maximize availability? And how to structure aftersales processes profitable as an OEM?
To maintain strong positioning, machine builders and manufacturers have to meet the highest quality standards, in some industries with output error tolerances far below 1%. While traditional approaches, mostly based on manual inspections and human communication, are error-prone and not scalable, smart technologies enable companies to optimize all relevant dimensions at the same time: improved quality, reduced costs and increased turnover. With data driven predictive maintenance, machine breakdowns can be avoided and the entire procurement and commissioning of resources can be designed very lean. LEAD provides a software tool that connects interval-based maintenance plans of the OEM’s (machine builders) with the real machine data from the machine operating company. It is designed to run maintenance processes more effectively and works with every type of machinery (injection molding, assembly, packaging, injection tools,…).
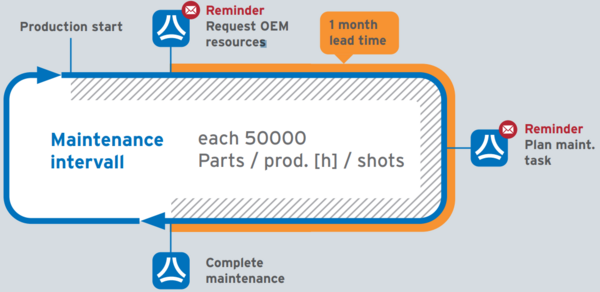
The benefits of using the smart solution for predictive maintenance are:
- Structured receipt of spare parts and service requests (OEMs)
- Build up a profitable and digital aftersales (OEM)
- Ensure provisioning of spare parts timely to avoid escalations
- Software triggering organizations by timely reminder for due maintenance
- Iteratively optimize maintenance intervals on real data
- Automatic and digital documentation with media
The implementation of the system can be done easily, as it only requires registration in the LEAD platform and optionally a small IOT gateway collecting data from machine and sending to LEAD cloud.
The path towards an integrated smart platform includes different steps:
- OEM creates maintenance plans in LEAD app and invites customers
- Producer can simply connect the invited maintenance plans via LEAD with their machines and thereby use machine data
- With a sufficient lead time the producer is timely reminded to request necessary resources from OEM simply with the press of a button.
- Timely reminder to plan maintenance and assign responsibilities in LEAD
- On completion of the maintenance task all information including text and media is documented automatically
For instant usage of the tool, the entire system can also be used without any connection of a machine to a maintenance plan. Then, not based on machine data but only based on time intervals (i.e. weekly, quarter year, half year, yearly). By that, OEMs can plan and organize maintenance services for their customers independent of their involvement.
Graphics: LEAD
The comPETence center provides your organisation with a dynamic, cost effective way to promote your products and services.
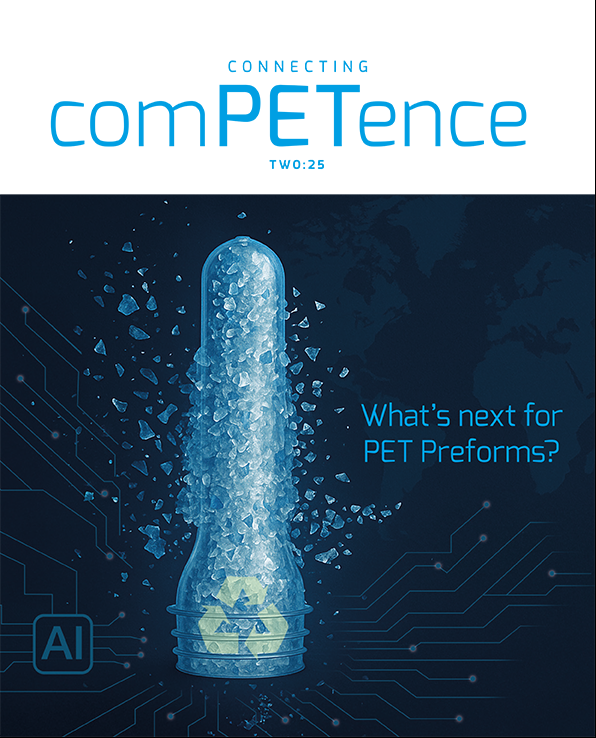
magazine
Find our premium articles, interviews, reports and more
in 3 issues in 2025.