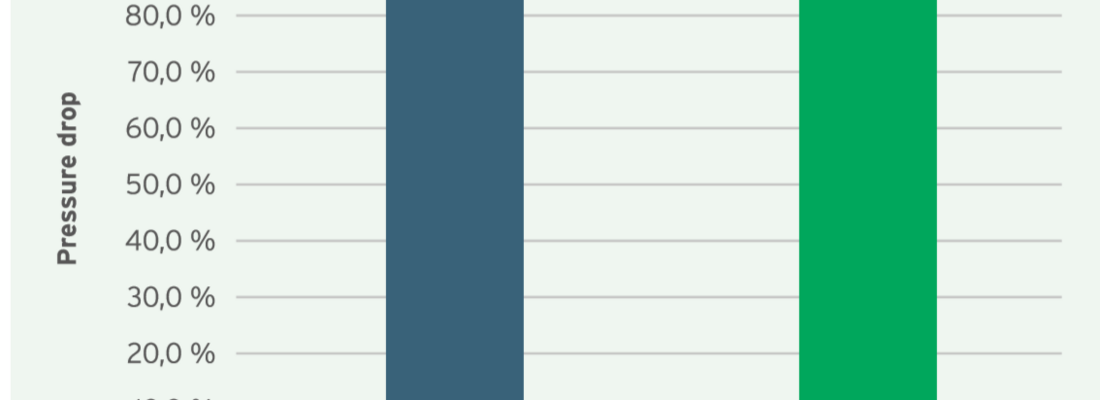
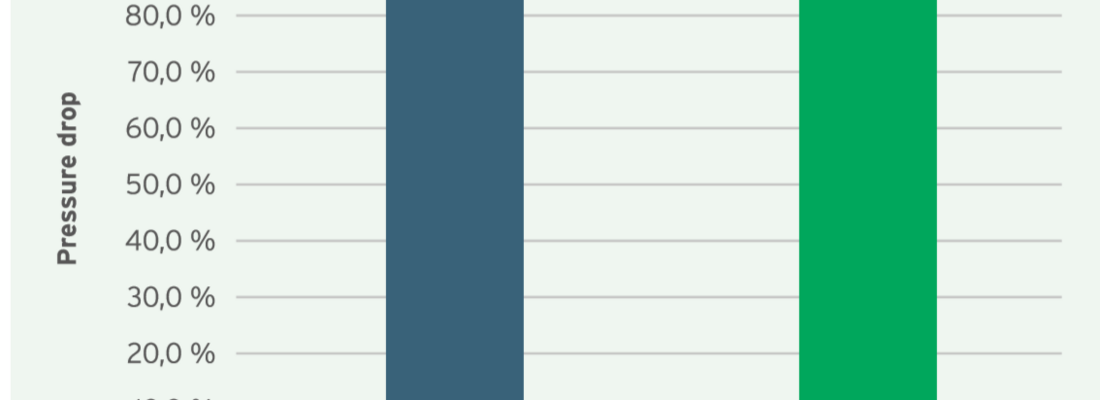
Thinner bases, less shearing, lower injection pressure: using movable cores in preform tools brings a great many benefits. The mould specialist MHT Mold & Hotrunner Technology AG uses the Active Flow Molding procedure to achieve them.
As anybody who has ever struggled to open a bottle with a short thread can tell you, the scope for saving material in this area has been practically exhausted. But what about the bases of PET bottles? These have also been the subject of attempts at optimisation for some time, as they are often thicker than they need to be for the stability of the bottle and use more plastic than strictly necessary. This high wall thickness can also sometimes be detrimental to the subsequent blow moulding process, particularly when the blowing machines are running at high speeds. Active Flow Molding (AFM) offers a new opportunity to considerably reduce wall thickness right from the primary shaping stage, by using movable cores in the tool. MHT Mold & Hotrunner Technology AG is now deploying this process, which is similar to injection compression moulding, in its high-cavity tools.
To sum up the current state of the art, cores in PET preform moulds have always been fixed in position and the sprue area in the subsequent bottle base is a very tight fit. The molten plastic has to be pressed into the cavity under very high pressure, so that it can find its way to the thread at the other end of the preform. The longer and thinner the item, the less advantageous the flow length to wall thickness ratio. If the tip of the preform towards the sprue is formed at a more acute angle, rather than in a half-circle as previously, the molten plastic flows more easily, leading to initial savings of materials and energy. These preform variants, some of which are subject to licence, have been on the market under various names (e.g. MHTsaveBASE) for about 10 years. Other processes are based on stamping and moulding processes immediately following the injection moulding procedure. The aim is to increase the base contour whilst reducing wall thickness. This is done using plastic deformation – with its all-too-familiar disadvantages, such as increased tension in the plastic and the thinning of the amorphous area of the bottom wall thickness.
MHT has therefore pursued a different AFM strategy, leading to its successful development of the technology in a fourcavity mould, which it now plans to deploy in multi-cavity tools. The key feature is that the cores are movable, resulting in a mechanism similar to those used in injection compression moulding. The individual stages are as follows: during the injection process, the molten plastic pushes the core back and the available sprue opening increases. The plastic flows in more easily, the flow path ratio is more favourable, injection pressure drops (about 9 percent at current tests) and there is less shearing. Once the preform is almost completely full, the core travels forward (up to 6 millimetres) into the end position through the still-liquid molten plastic. Surplus mass at the base is pressed into the wall and the thread is completely filled right to the top. The thin base is achieved during primary shaping and therefore carries little tension. In one case study the project team was able to reduce weight from 41 g to 40.5 g in a test preform for a 2 L bottle. Extrapolated to a 96-cavity tool and 1 million cycles (less than annual output), this gives a saving of 48 tonnes of PET.
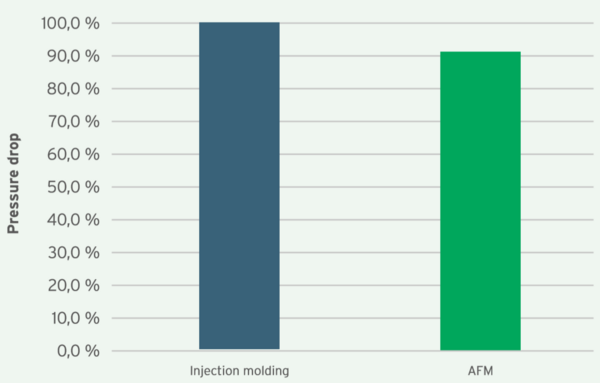
Fig 1: Pressure drop during injection lower with AFM
To allow the cores to move, a new version of the mould cavity was needed and the (now longer) cores were bisected: the core base part is connected to the drive unit, the core contour continues to provide the shape. A special combination of coatings was selected for the core and locking ring. The tool itself has four plates on the moving side – two more than usual – to make room for the combination of hydraulics and springs. As it is the molten plastic that pushes the cores back, a singleacting cylinder is sufficient, whereby the pressure level roughly corresponds to that of the injection moulding machine.
The core contour has a cone at the tip, the Antiflex base. This makes it possible to avoid what is known as core shift, which can create problems in thin-walled applications in particular. Very long, thin cores tend to bend due to the injection pressure, meaning that they are no longer perfectly centred within the cavity, leading to walls of uneven thickness. The AFM technology can be used in all existing PET injection moulding machines and requires no special equipment. An external hydraulics package drives the cores, a process requiring very few machine signals.
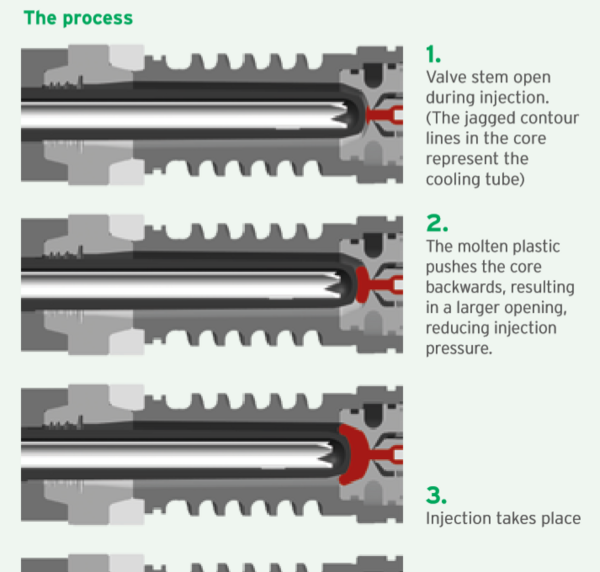
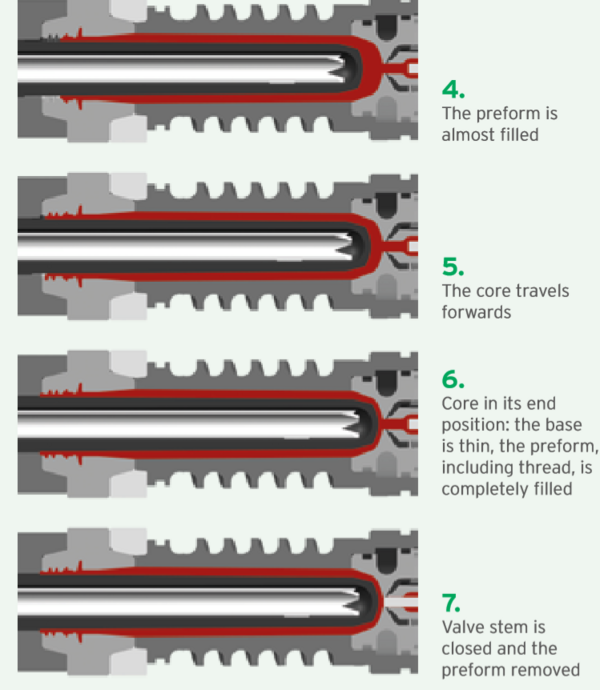
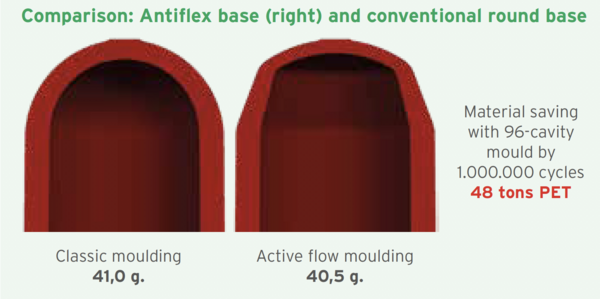
As stretch blow moulding and filling processes always come after preform production, it is important to include these in a new process. MHT has been part of the Krones Group since 2018, providing it with the relevant expertise on its doorstep. There is the option for customers to map out preform production using this technology with MHT in a prototyping process or, if required, all lab and stretch blow molding tests with Krones. Initial trials on the stretch blow machine have already been carried out, demonstrating improved base stretching; rotary filling system trials have also been carried out. The joint development team is planning further experiments – and then there will be nothing to stop the introduction of AFM in the preform market.
The comPETence center provides your organisation with a dynamic, cost effective way to promote your products and services.
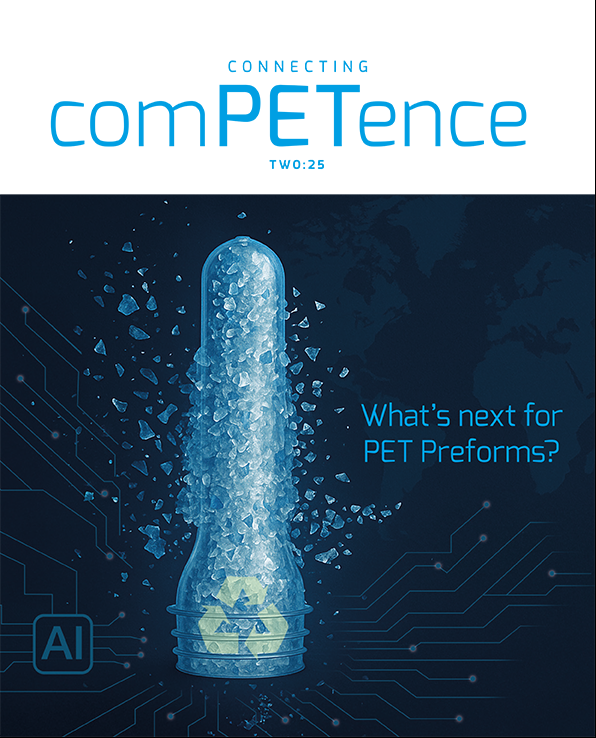
magazine
Find our premium articles, interviews, reports and more
in 3 issues in 2025.