Investigation of stretch ratio dependent material models of PET bottles in O2-barrier and topload simulation routines
This article describes an approach to determine virtual prototypes of PET bottles from a given preform design and process parameters using a three-dimensional simulation of the stretch blow molding process. The material behavior of PET bottles is described considering the dependency of the process induced local stretch ratio to the permeation and topload related material properties. The corresponding material model is used for the testing of the prototypes’ oxygen barrier and topload behavior.
The two-stage stretch blow molding process is well established for the large scale production of high quality PET containers with excellent mechanical and optical properties [1]. These benefits lead to a dominant market share in the field of packaging. The process consists of a heating and a forming phase. An injection molded preform is heated via infra-red radiation and afterwards stretched and blown into a mold [2]. The share of material costs of the entire process chain is about 70 to 75 percent [3]. The challenge in minimizing the use of material is ensuring the required properties of the bottle, such as a certain topload-behavior during the transport of the bottles on pallets and a certain barrier function, for example for oxygen-sensitive products. These requirements are achieved to a large extent through the material distribution of the bottle [5], that is determined by the preform design and the process parameters [3]. Another influence is the improvement of the material properties through the stretch induced material hardening in the process. This behavior is realized in CAE methods through stretch ratio dependent material models. These material models require a high effort in determining stretch ratio dependent material data, because the amount of samples and measurements increases strongly due to the accuracy of the model. Therefore, the contribution addresses the influence of the stretch ratio dependent material data on the properties of the bottle.
GOUVERNING EQUATIONS
The integrative simulation approach at the Institute of Plastics Processing at RWTH Aachen consists of a process simulation that is coupled either with a topload or an O2-barrier simulation. The heating phase is modeled through the radiation heat exchange between emitter and preform and the heat conduction in the preform [6]. The radiation flux from the environment on an element i is calculated through Eq. 1.
Where ? is the Boltzmann constant, ? is the emission coefficient, F are the view factors, ?i,j the Kronecker Delta and T the temperature. The radiation absorption is calculated through the law of Lambert-Bougier in Eq. 2. It describes the energy loss of radiation inside a solid material.
Where ? is the wavelength, q0’’(?) is the radiation on the body’s surface, ?(?) is the absorption coefficient, y the depth of the radiation in the preform. The heat conduction is calculated through Eq. 3.
Where ? is the density, cP is the specific heat, t the time, ?’’’ the internal heatsource and ? the thermal conductivity. The mechanical material behavior is modeled through a Mooney-Rivlin based hyper elastic Yeoh-modell in Eq. 4.
Where W is the strain energy, Cij are material specific constants and I1 is the first invariant of the left Cauchy-Green tensor. The permeation is calculated through the permeation coefficient P in Eq. 6.
Where is the oxygen volume flow through the barrier, A is the plastics surface, x is the plastics thickness and p is the oxygen’s partial pressure.
SIMULATION MODELS
The process- and topload-simulation routines are implemented in the simulation software Abaqus by Dassault Systèmes, Société annonyme, in Velizy-Villacoublay, Cedex, France. The coupling of these routines is achieved through software tools implemented in VB using the .NET framework by the Microsoft Cooperation, Redmond, USA.
The processes simulation was developed in [7]. The radiation heat exchange between Polyethylenterephthalat (PET) prefom and emitter is calculated through Eq. 1 in Abaqus. The resulting energy input on the perform’s surface is used to calculate the heat generation inside the preform. Therefore, Eq. 2 is solved with a wavelength-dependent absorption characteristic. The resulting heat source ?’’’ allows determining the heat conduction through Eq. 3 with the Abaqus FEM-solver. The forming simulation requires the temperature profile of the preform. The used material model is a stretch ratio and temperature dependent Yeoh-model in Eq. 5. The described process simulation results in a formed bottle with a certain wall-thickness distribution. The elements stretch ratio is calculated through the comparison of preform and bottle elements. The “virtual prototype” of the bottle is used for further tests. A topload simulation was implemented in [8], that uses stretch ratio dependent material data. Furthermore an O2-barrier calculation was implemented, that uses Eq. 6, for element-wise calculation of the oxygen flow through the barrier material.
Material data
The absorption coefficient is calculated from the wavelength dependent transmission spectra in Figure 1. The forming simulation uses material-coefficients Cij of the Yeoh-model in Eq. 4 based on stress-strain-curves. These curves were measured on a lab stretcher KARO IV, by stretching PET-films at different temperatures and stretch-speeds. The resulting stress-strain-curves for different temperatures are shown in figure 1.
The material properties for the topload and the barrier simulation were measured on probes of PET bottles with different homogeneous stretch ratios. Figure 2 shows the axial secant modules for the topload simulation in axial and circumferential direction on the left as well as on the right the permeation coefficients measured in permeation chambers with a non-invasive optical sensor of the company PreSens Precision Sensing GmbH, Regensburg, Germany.
Validation of the process simulation
Figure 3 shows the comparison between the measured and calculated temperature profile on the inner and outer preform surface. The simulated temperature is lower than the measurements, because the model does not take the transmitted radiation through the preform into account. The deviation in the bottom and the head of the prefom is caused by the modeling of the absorption behavior. In the model, the incoming radiation enters the preform orthogonal to the surface and that causes errors in these sections. The comparison between the measured and calculated wall thickness distribution of the bottle is shown in Figure 3. The comparison shows a good agreement between simulation and measurement, despite the errors of the reheat simulation.
Application of the topload and barrier simulation
The process simulation was applied to four different preform geometries to test the influence of the stretch ratio dependent material data on different scenarios. The tool for the forming simulation was identical in each simulation. The different preforms in figure 4 are taken from a preform-optimization in [9]. The results of the process-simulations were used for a topload and an O2-barrier simulation with either constant or stretch ratio dependent material properties. The wall thickness distribution of the resulting bottles is shown in figure 4. Preform 3 has the highest amount of material in the body of the bottle and preform 1 has the lowest amount.
Figure 4 shows also the result of the topload-simulation. The used constant stretch ratio is 4.0 in circumferential and 3.6 in radial direction. Preform 1 has a homogeneous wall thickness distribution in the body of the bottle and therefore homogeneous stretch ratios in that region, but the consideration of the stretch ratio dependence leads to a difference of 20 % in region of failure. Preform 1 has the most varying wall thickness distribution, but nearly the same topload behavior with either constant or stretch ratio dependent material properties.
Table 1 shows the oxygen transmission rate (OTR) of the O2-barrier simulation at 23 °C with either constant (CSR) or stretch ratio dependent (DSR) permeation coefficients. The used constant stretch ratio is 4.7 in circumferential direction. The difference in the permeation coefficient for different stretch ratios is approx. 10 %. The results of the simulations are in that magnitude. But in contrast to the topload simulation, preform 1 has the lowest stretch ratio dependence because of the homogeneous wall thickness distribution. The difference between CSR and DSR in case of the OTR depends on the stretch ratio deviations of the whole bottle while the topload result depends on the stretch ratio deviations of the region of failure.
CONCLUSIONS
An integrative simulation approach of the stretch blow molding process with a topload and an O2-barrier simulation was used to determine the influence of stretch ratio dependent material properties of different preforms. The result of the simulation shows, that the influence of these properties are highly dependent on the preform shape and the tested property (topload or O2-barrier). Therefore, it is not yet possible to precisely determine the influence of a stretch ratio dependent material model due to the wall thickness distribution of the bottle. Further studies will focus the development of sseparate models to assess the influence of a stretch ratio dependent material model for various properties.
ACKNOWLEDGEMENTS
The research projects (14124 N and 16257 N) of the Forschungsvereinigung Kunststoffverarbeitung were sponsored as part of the “Industrielle Gemeinschaftsforschung und -entwicklung (IGF)” by the German Bundesministerium für Wirtschaft und Energie (BMWi) due to an enactment of the German Bundestag through the AiF. We would like to extend our thanks to all organizations mentioned.
The comPETence center provides your organisation with a dynamic, cost effective way to promote your products and services.
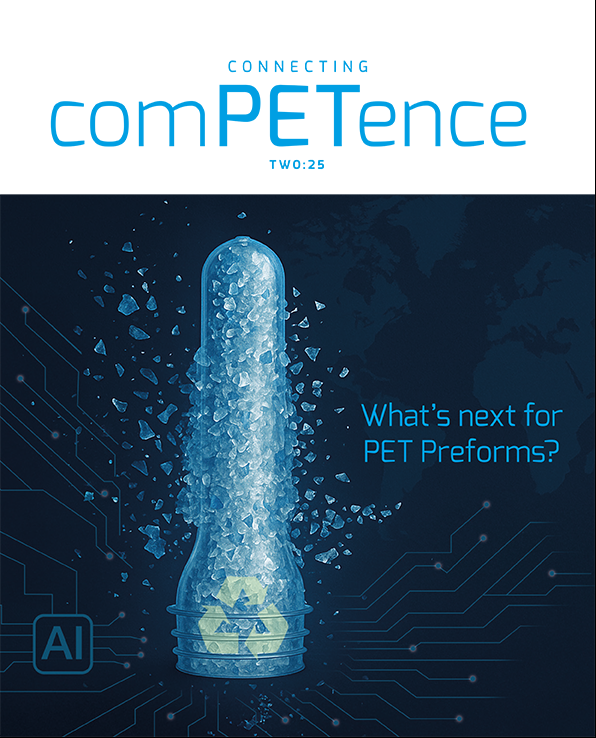
magazine
Find our premium articles, interviews, reports and more
in 3 issues in 2025.