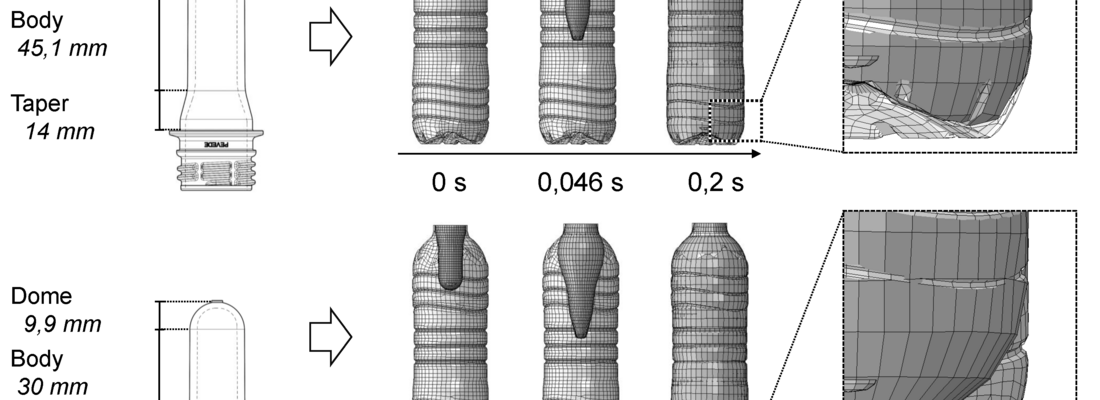
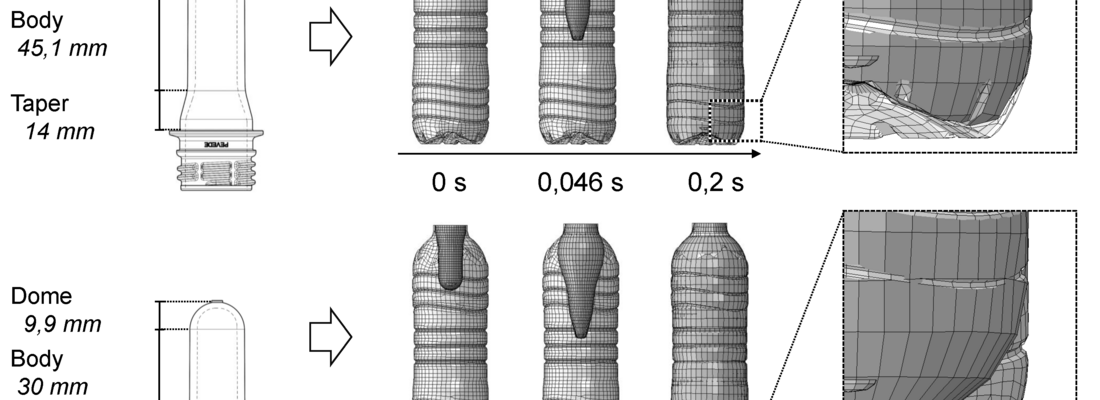
In order to reduce development time and costs, preform and process design in the two stage stretch blow moulding process of PET bottles is increasingly supported by simulation tools. An example are virtual bottles which support the early design process as prototypes or the production as digital twins.
The virtual bottles can be created by process simulations or heuristics based on production data. In most cases, the simulations are not designed for extremely high stretch ratios and the prediction of material failure. Thus, these simulations are reaching their limits in case of lightweighting. This deficiency is addressed in a research project at the institute of plastics processing (IKV) in Aachen. Since the research project is still in an early stage, this article provides an outlook.
Limitations of material models
Prediction models for the blowing process are used to generate virtual bottles to determine their properties such as wall thickness distribution or other properties. The models used, are either heuristic models or physics-based simulations. Heuristic models predict the wall thickness based on production data. These models are therefore common in companies which have a large amount of production data at hand. Physics-based simulations use material models to predict the deformation behaviour of the preform and generate the virtual bottle. These approaches are predominantly used in research institutions. The focus of the current research project are physics-based simulations but the results might be transferred to heuristic models.
There are different approaches for modelling the deformation behaviour of PET. These approaches model the stress of PET during biaxial strain. A common method for the biaxial characterization of PET are stretching frames that allow the elongation of samples at speeds of up to 3000 % per second. Figure 1 shows the stretching frame of Blow Moulding Technologies, Belfast, Northern Ireland. The measurement is performed on quadratic samples. The samples are locked by clamps, where one clamp per stretching direction is equipped with a force sensor. Before starting the measurement, the samples are heated convectively in an oven. Afterwards, the samples are stretched equibiaxially and a computer records the force and the nominal strain of the sample. The result is a stress strain curve as show on the right side of figure 1. The curve is obtained at a Hencky strain rate of 400 %/s at a temperature of 100 °C. In general, the stress increases almost linearly at low strains and reaches with further elongation a plateau region. At high strains, the stress curve leaves the plateau and rises almost exponentially. In this phase, the polymer chains are oriented, which leads to a sharp increase in the strength of the material. This effect is called strain hardening or strain induced crystallisation.
Various modelling approaches have been applied to the simulation of the two-stage stretch blow moulding process. The most promising results offer hyperelastic and visco-hyperelastic models, since these models predict the strain hardening. The Yeoh-model is a hyperelastic approach that is used in combination with a time temperature shift and a prony series for the consideration of viscoelasticity [2,3]. The model predicts the deformation behavior of PET phenomologically through a polynomial function. The physics-based glass-rubber-model is a popular visco-hyperelastic model that is used in the simulation of the stretch blow moulding process [4,5]. The advantages of the Yeoh-model are its simplicity and robustness, while the glass rubber model predicts the material behaviour more precisely.
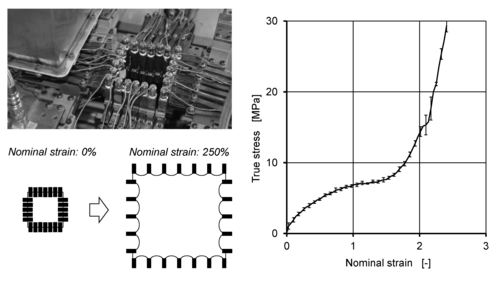
Figure 2 shows the stress strain curve predicted by the Yeoh-model and the glass-rubber-model compared to the measurement shown in figure 1. The parameter of both models were fitted on the single curve with the software MATLAB, The MathWorks Inc., Natick, USA. The Yeoh-model is slightly more accurate, since the focus of the glass rubber model is the prediction of the temperature and strain rate dependent material behavior. In both cases, the modeling of the strain hardening leads to an almost exponential increase of the stress at high strains. This strong increase prevents further elongation of the material.
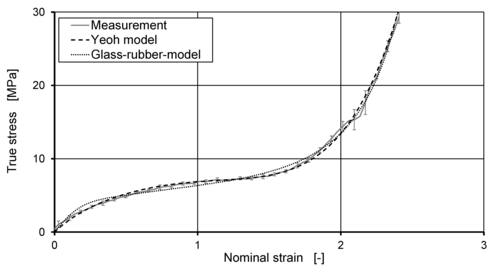
The prevented elongation at high stretch ratios restricts certain preform geometries in the forming simulation, especially with lightweight preforms. Figure 3 shows in the top area a process simulation performed with a 18,5 g standard preform. The simulation uses the Yeoh-model. At the beginning, the preform is stretched with the rod while the preblow pressure is applied simultaneously. The inflation of the preform starts after 0.046 s and after 0.2 s the bottle is fully formed. In another simulation, the preform weight was reduced to 15.5 g by lowering the height of the preform body to 30 mm. The results are shown in the lower part of figure 3. In contrast to the previous simulation, the bottle is not fully formed at the bottom, because there is an equilibrium between the final blowing pressure of 20 bar and the stretching resistance of the material. This equilibrium does not occur in industrial mass production. The material is either stretched slightly further or the material fails. This inaccuracy in the simulation inspires a more detailed investigation of the material behaviour of PET at high stretch ratios.
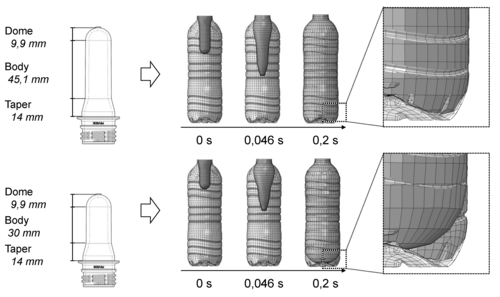
Upcoming investigations
The modelling of the material behaviour of PET at high stretch ratios is closely related to the failure of the material. Failure of PET due to large biaxial strain has not yet been investigated, but there are various approaches in other fields of plastics processing. A broad application of failure models is used in the design of fibre-reinforced plastics. The investigation focus on phenomenological failure criteria, which are widely used for anisotropic composite materials [6, 7, 8]. Possible criteria are a maximum stress criterion, which specifies a maximum value for the stress or a maximum strain criterion, which specifies a maximum strain. If the values are exceeded in the respective criteria, the material fails. Other approaches take the biaxial deformation into account. A possible approach is the Caddell-Raghava-Atkins model, that considers pure biaxial strain under the assumption that no shear stresses occurs [9]. Furthermore, the Tsai-Wu criterion is potentially suitable. The criterion is widely used for anisotropic composite materials as it allows further stress states to be taken into account [10].
The failure model will be calibrated through experiments on the membrane inflation rheometer (MIR), illustrated in figure 4. The MIR is a measuring device to determine the mechanical properties of plastic films by deforming the sample under pressure. For this purpose, a pressure vessel and a cylinder are separated by the sample. Both components are filled with tempered silicone oil. During the measurement, a piston moves through the cylinder in direction of the film. As a result, the oil is displaced and inflates the film. The sample is formed along a guiding grid in order to guarantee a uniform deformation of the film. The MIR allows high elongations until material failure. To locate the local elongation through a speckle pattern and the time of failure, this process is observed by high-speed cameras.
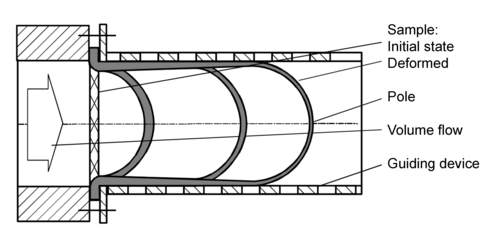
The MIR’s guiding grid forces an equibiaxial deformation in the pole of the film. This deformation state is sufficient to calibrate the maximum stress and the maximum strain criterion as well as the CaddellRaghava-Atkins model. The calibration of the Tsai-Wu criterion demands a higher variety of biaxial deformation states. This demand leads to the design of new guiding grids of which one is exemplary shown in figure 5. The circular cross section of the initial grid is modified to an oval shape. As a consequence, the stretch ratios in the horizontal direction are considerably higher than the ones in vertical direction. The calibration of the failure criteria is done by a reverse engineering approach where the measurement of the MIR is performed experimentally and virtually through a simulation. A comparison between experiment and simulation indicates the quality of the model’s parameters, which are changed until an agreement below 5 % is achieved. Furthermore, the modeled stress values at high stretch ratios are investigated in these experiments. A possible result is the weakening of the modeled stress in the range of strain hardening.
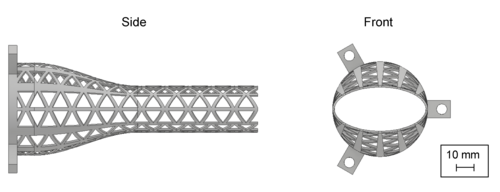
Conclusion and Outlock
The discussed research project at the IKV deals with the investigation of extremely high stretch ratios and the prediction of material failure in simulations of the stretch blow moulding process. Current material models for the deformation of PET predict an almost exponential increase of the stress in the range of strain hardening. This strong increase prevents the further elongation of the material and affects the forming simulation, especially with lightweight preforms. This limitation inspires a more detailed investigation of the material behaviour of PET at high stretch ratios up to 4 as well as the calibration and evaluation of a failure criterion.
The aim of the overarching research objective is a more detailed prediction of the material behaviour at high stretch ratios. The associated model modifications are integrated into a simulation of the two-stage stretch blow moulding process used for the weight optimisation. In past optimisations, the preform weight has already been reduced from 18.5 g to 15.5 g. The modified model should enable a further reduction of the bottle weight.
Acknowledgements
The research project 20158N of the Forschungsvereinigung Kunststoffverarbeitung is sponsored as part of the “industrielle Gemeinschaftsforschung und -entwicklung (IGF)” by the German Bundesministerium für Wirtschaft und Energie (BMWi) due to an enactment of the German Bundestag through the AiF. We would like to extend our thanks to all organizations mentioned.
Sources
1 SALOMEIA, Y. M.; MENARY, G. H.; ARMSTRONG, C. G.: Instrumentation and Modelling of the Stretch Blow Moulding Process. International Journal of Material Forming 3 (1995) 1, S. 591-594
2 YEOH, O. H.: Some Forms of the Strain Energy Function for Rubber. Rubber Chemistry and Technology 66 (1993) 5, S. 754–771
3 HOPMANN, C.; RASCHE, S.; WINDECK, C.: Simulative design and process optimization of the two-stage stretch-blow molding processAIP Publishing LLC, 2015, S. 50011
4 MENARY, G. H.: Modelling Injection Stretch Blow Moulding and the Resulting ’in Service’ Performance of PET Bottles. Queen’s University of Belfast, 2001
5 ZIMMER, J.: Analyse und Optimierung des flüssigkeitsgestützten Streckblasenformens. Technische Universität Dortmund, 2015
6 ZHOU, Y. X., MALLICK, P. K.: A non-linear damage model for the tensile behavior of an injection molded short E-glass fiber reinforced polyamide-6,6, Materials Science and Engineering A - Structural Materials Properties Microstructure and Processing 393 (2005), S. 303-309
7 MIR, H., FAFARD, M., BISSONNETTE, B., DANO, M. L.: Damage modeling in random short glass fiber reinforced composites including permanent strain and unilateral effect, Journal of Applied Mechanics-Transactions of the Asme 72 (2005) S. 249-258
8 GÜNZEL, S., TRAPPE, V., RUDOLPH, H.-V.: Betriebsfestigkeit kurzfaserverstärkter Thermoplaste - Ein neues faserverbundorientiertes Auslegungskonzept unter Berücksichti-gung des Schädigungsmechanismus. 37. Tagung DVMArbeitskreis Betriebsfestigkeit 2010
9 CADELL, R.M.; RAGHAVA, R.S.; ATKINS, A.G.: A yield criterion for anisotropic and pressure dependent solids such as oriented polymers. Journal of materials science 8 (1973) 11, S. 16411646
10 TSAI, S. W., WU, E. M.: A General Theory of Strength for Anisotropic Materials, Journal of Composite Materials 5 (1971) 1, S. 58-80
11 DETROIS, C.: Untersuchungen zur Dehnrheologie und Verarbeitbarkeit von Halbzeugen beim Thermoformen sowie Simulation und Optimierung der Umformphase. RWTH Aachen, Dissertation, 2001
The comPETence center provides your organisation with a dynamic, cost effective way to promote your products and services.
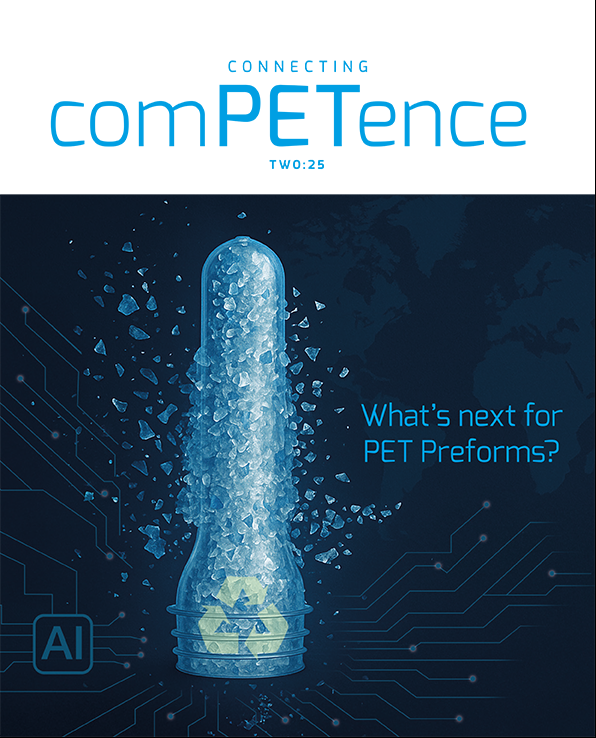
magazine
Find our premium articles, interviews, reports and more
in 3 issues in 2025.