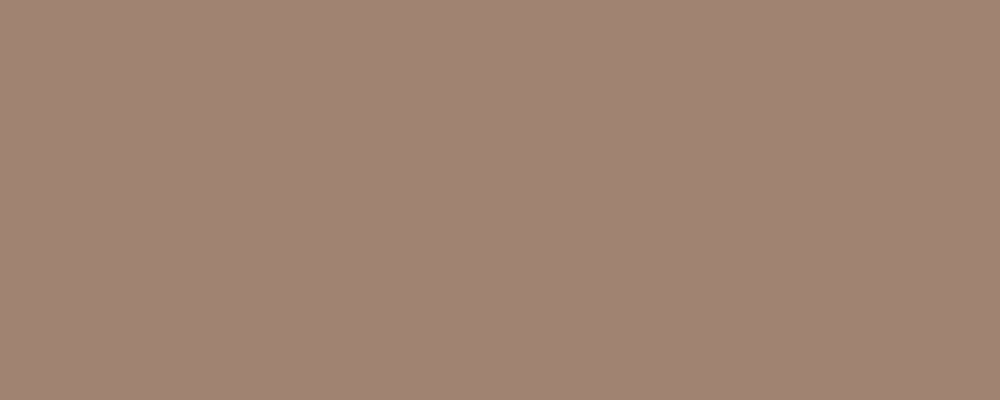
“Most certainly” — Bernd-Thomas Kempa, Managing Director of KHS Plasmax GmbH in Hamburg, is convinced. “More than 5 million bottles per day are coated with our technology in 20 installed units around the world.” And we are not even close to reaching market saturation, he continues. Quite the opposite – Kempa notes that according to trends, which see smaller containers replacing larger containers and increasingly sensitive drinks being bottled in PET bottles, there is future demand for coating technology. A good reason for the company to construct a new production hall in Hamburg and increase total production capacity.
Plasma technology, which had already been used in the pharmaceuticals industry for some time, conquered the PET beverage bottle market around 10 years ago. In the Plasmax-process, which was developed by KHS, pure silicon oxide, or glass, is deposited in low-pressure plasma to form a 50 nm thick internal coating for PET bottles. “As a result, we are combining the advantages of the unbreakable, lightweight PET bottle with the barrier properties of a glass bottle”, explains Kempa. KHS has only recently begun to offer Plasmax+ technology, where an additional glass top coating is applied to the SiOx layer. It is used for more demanding bottles and consumable products with a pH greater than 4.5, as the resulting barrier coating is even more flexible and resistant.
The Eckes-Granini Group has recently installed the third Plasmax system for the first time as a block version with the stretch-blow moulding machine. “The Plasmax coating extends the shelf life of quality orange juice in case of sensory and vitamin C content at ambient distribution”, says Bernd-Thomas Kempa, explaining his customer’s purchasing decision. The coating costs around one cent for each PET bottle, which is typically considerably below the mark-up of a multi-layer bottle. “However,” Kempa admits, “the bottle manufacturer does have to prepare for slightly higher space requirements, as the coating unit is needed in addition to the stretch-blow moulding unit.” According to Kempa, this additional outlay is absolutely worth it as far as sustainability and environmental protection are concerned. “The SiOx layer can be separated from the PET bottle during the standard recycling process and the PET can be reused – in contrast to a multi-layer bottle, which is generally made from inseparable individual coatings where the reusable materials cannot be recycled.”
Eckes-Granini is a typical Plasmax technology customer because juices and sensitive sports and health drinks are currently popular with consumers. For this reason the application areas for the bottle coating have changed considerably in recent years. Coating technology was originally conceived for beer bottles made of PET; in Western Europe however, the take-up of PET beer bottles has shown a rather sluggish development. “Ultimately the consumer decides which direction we take”, emphasises Kempa, “and with beer, Western European consumers prefer the traditional glass bottle.” In contrast, the beer market in Eastern Europe has developed quite differently, and it is common practice there to use plastic containers for beer. However until now, plastic was typically used for large containers, such as 1.5 to 3 l bottles. “The relationship between volume and surface is more advantageous with larger containers, and therefore the shelf life is less of a problem than with smaller containers” Kempa explains. But recently, smaller bottles have become increasingly popular in Eastern Europe too. “What is more, nutrition drinks and baby foods constitute another excellent prospective application for the Plasmax technology. As such, our technology has tremendous potential for further growth”, Kempa is pleased to report, and he concludes by declaring that Plasma technology is now so established in the market that it is no longer a subject of discussion, as, of course, it is already in use.
The comPETence center provides your organisation with a dynamic, cost effective way to promote your products and services.
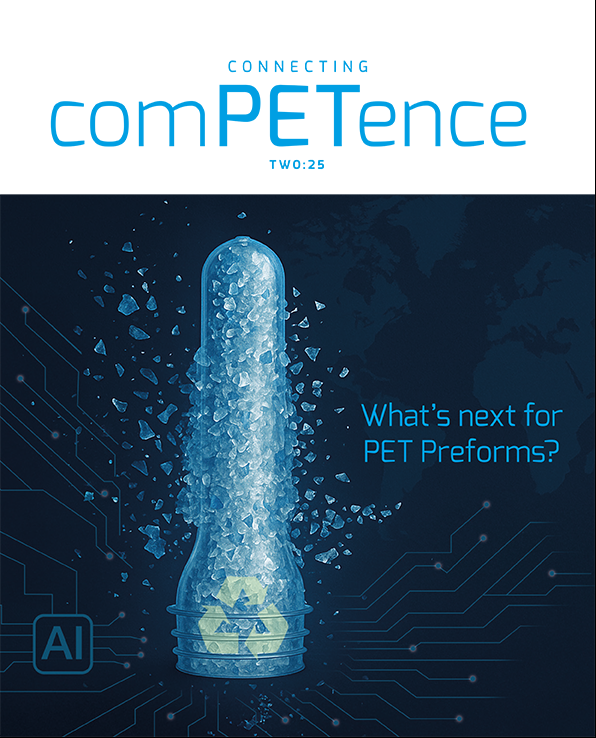
magazine
Find our premium articles, interviews, reports and more
in 3 issues in 2025.