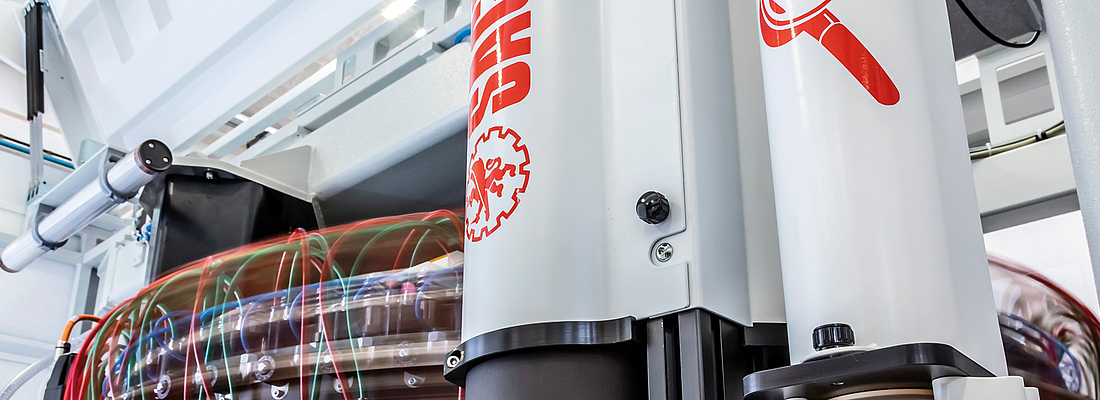
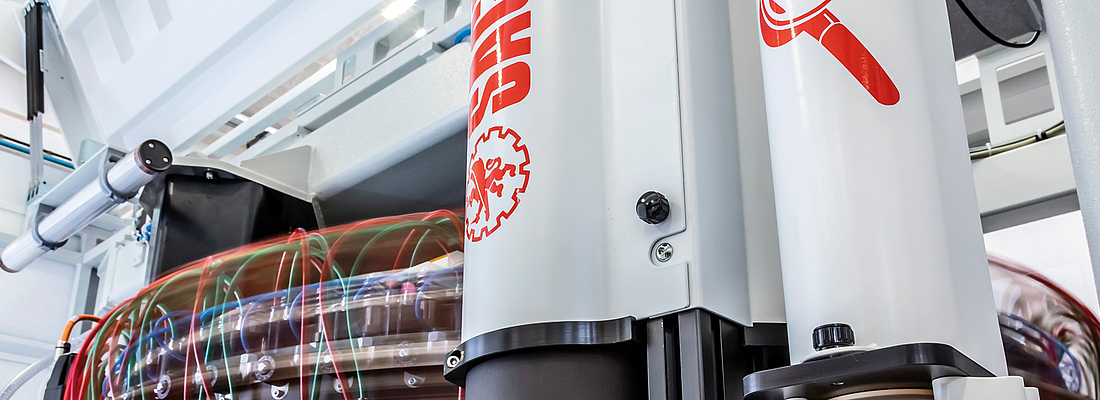
comPETence magazine | ONE:22 | Inspection and Digitalization
Digital inspection for caps and preforms, a twofold challenge - SACMI's drivers towards the future
SACMI presents its drivers for development in the sector. From state-of-the-art cap lines, on which the company has set a new technological standard worldwide, to new challenges in the area of automatic in-line quality control of preforms.
Everyone talks about it, few actually use it. The digitalisation of inspection, not only as a quality control of the individual product but also as a driver to make the production process more efficient, sustainable and profitable.
The first company in the world to offer its CCM cap machines with an integrated vision system, SACMI has set a new technological standard for the industry. Today, all or almost all producers operating in closures - even on alternative platforms to compression - provide for this type of control within the process.
The prospective challenge is twofold. Further evolve the controls on the cap lines to set up predictive actions and process feedback. Transfer some of the recognised advantages of in-line inspection to PET preforms, even in the light of the “ecological transition” and therefore the use of new families of raw materials such as recycled PET.
Computer Vision Software r-evolution by SACMI
The Computer Vision revolution in rigid packaging is to extend the concept of “vision” from the mere analysis of product defects to the gathering of information to correct and optimise the process.
As a technological leader in the production of compression presses for caps - increasingly evolving in the direction of lightweight and new tethered standards - SACMI offers a complete line of vision systems that allow 100% in-line control of production.
These systems can reach very high speeds - even exceeding 300,000 caps per hour - and it is not only possible to achieve total control of both the external part and the internal part of the cap but also to read the number of cavities to generate immediate statistical reports on defects and measurements.
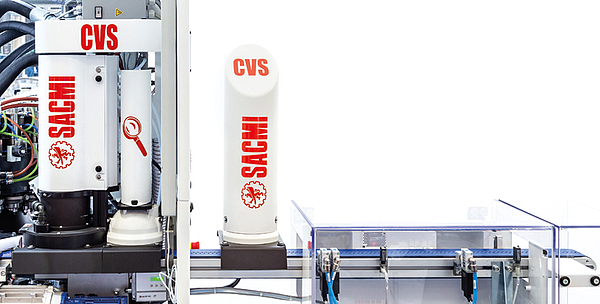
In general, when production deviates from the preset parameters, with Sacmi CVS the operator is alerted in real time and supported in setting the necessary corrective actions on the machines that, in the near future, could be governed in a totally automatic way.
For some years now SACMI has been developing PVS (Preform Vision Systems), an extensive family of solutions for sample inspection and off-line reprocessing of 100% of production.
SACMI has already extended the number and type of controls to other stages of the cap line. For example, in parallel with the introduction of the new tethered standards, extending the potential of controls to include CVS-Cut inspection.
The challenge of preform inspection
In spite of the fact that the direction of travel on the cap lines is clearly visible, as SACMI offers a complete range of vision systems that can be integrated both on its own compression presses and on other platforms, it is the preform inspection that may be the most important challenge at both an industrial and a technological level.
Extremely more complex, due to the quality of the parameters to be taken into account and the structure of the production process itself, preform inspection is almost never carried out automatically. For some years now SACMI has been developing PVS (Preform Vision Systems), an extensive family of solutions for sample inspection and off-line reprocessing of 100% of production.
The next step will be to integrate the in-line system into almost all preforms produced, with throughputs of up to 96 preforms in around 5 minutes, the same order of magnitude as the “laboratory” solution (SACMI PVS002), performing complete checks on every area of the preform including weight, temperature and cavity number readings.
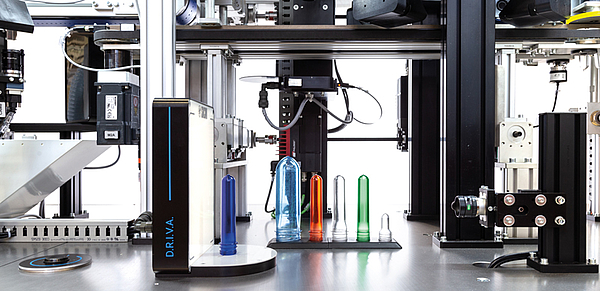
Why a “total” in-line inspection for preforms?
Automating inspection - which is already possible with SACMI’s current family of PVS systems - is the first major step towards the digitalisation of inspection in this area. For speed, repeatability of the process, number of parameters that can be considered objectively and repeatably. In general, the return on investment is becoming more and more attractive due, for example, to the guarantee that such systems offer the management of entire batches of potentially defective preforms.
The second step is the integration of the system into the machine. With the forthcoming market launch of the PVS156 system, just a few months after the development of the new IPS300 injection moulding machine, SACMI is proposing the “final revolution” in this sector too, i.e. the possibility of constant, continuous monitoring of production quality.
As a result, even a non-expert operator can have valuable information at his/her disposal to generate feedback on the process, saving time and avoiding critical issues in production as far as possible upstream.
Configurable according to customer requirements, PVS156 generates statistical reports in real time and does not interfere with the press work cycle. As a result, even a non-expert operator can have valuable information at his/her disposal to generate feedback on the process, saving time and avoiding critical issues in production as far as possible upstream.
The green challenge
Precisely because it is capable of generating feedback on the production process, quality control becomes a source of competitive advantage for the customer. In addition to reducing nonconformities, it enables the quality and accuracy of routine controls to be increased.
But there is more. With the advent of new recycled resins, such as rPET, process deviations could prove to be much more frequent (due to possible contamination of the resin, unexpected changes in rheological composition, etc.).
This is why SACMI is working alongside its customers to support the green transition with this new approach to inspection, addressing two families of specific needs: to make quality control automatic - and therefore as operator-independent as possible - and to facilitate the transition underway in rigid packaging towards a profitable future of sustainability.
Photos: Sacmi
The comPETence center provides your organisation with a dynamic, cost effective way to promote your products and services.
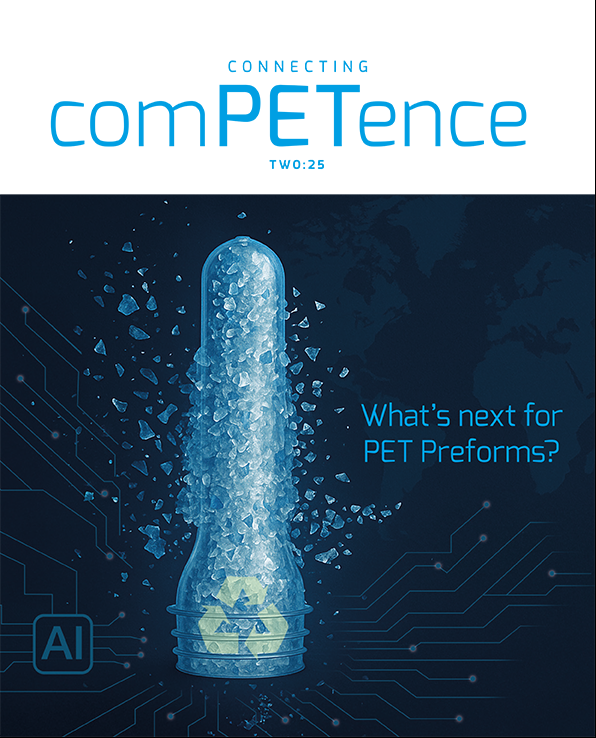
magazine
Find our premium articles, interviews, reports and more
in 3 issues in 2025.