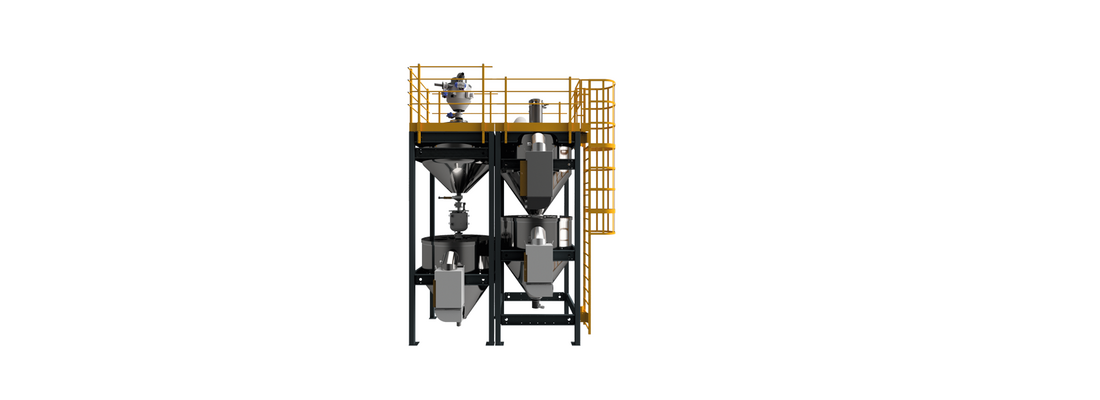
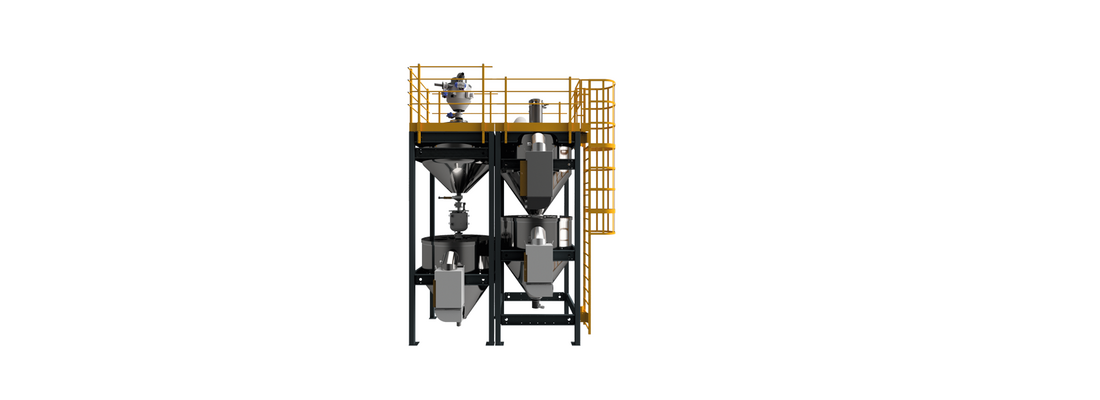
(Photo credit: PET Solutions)
rPET and Preform Production
Continuous Vacuum Drying Technology by PET Solutions
The production of preforms stands as a pivotal stage in the fabrication process of PET bottles, ever-present in the beverage sector. A crucial aspect of preforms production lies in the meticulous drying of PET granules or flakes before injection molding.
rPET, an eco-friendly plastic derived from recycled PET, finds extensive application in the manufacture of plastic bottles, food packaging, and textiles. Despite its sustainability, rPET confronts several challenges:
- Quality: The quality of rPET varies significantly based on its source and recycling methodology. Contaminants like beverage residues or label and PVC remnants or other plastic types can compromise its suitability for certain applications.
- Contamination: The intricacies of PET recycling often entail challenges in eliminating all contaminants from the plastic, potentially leading to inferior quality products and complicating future recycling endeavors.
- Energy Consumption: The PET recycling process demands substantial energy and water resources, contributing to greenhouse gas emissions and environmental strain.
- Processing: rPET materials required dedicated drying process to avoid resin degradation (rPET thermal history), yellowing effects (rPET thermal history), sticking phenomena (poor crystallinity) and condensable contaminants generation.
- Supply: The availability of rPET may be constrained, particularly with escalating demand, resulting in price hikes and limited accessibility for businesses.
In recent times, vacuum drying has emerged as a favored technique for drying PET material in preforms production. Vacuum drying boasts numerous advantages over alternative methods, particularly for materials sensitive to heat or necessitating gentle handling.
A paramount benefit of vacuum drying in preform production lies in its capability to prevent PET material degradation. Moreover, the amalgamation of heat and vacuum facilitates expedited drying, thereby enhancing production efficiency.
A paramount benefit of vacuum drying in preform production lies in its capability to prevent PET material degradation. Moreover, the amalgamation of heat and vacuum facilitates expedited drying, thereby enhancing production efficiency.
Uniform drying across the material is another advantage of vacuum drying, attributable to the even moisture removal facilitated by reduced pressure. This ensures consistent quality in the final preforms product.
Furthermore, vacuum drying proves to be more energyefficient than conventional methods, owing to reduced pressure necessitating less energy for moisture extraction. This translates to cost savings and a more sustainable production process.
Overall, vacuum drying emerges as a dependable and efficient solution for PET material drying in preforms production. Its advantages encompass temperature control, speed, uniformity, quality, and energy efficiency, rendering it increasingly favored in the beverage industry. With the increasing demand for PET bottles, vacuum drying is ready to retain its pivotal role in preform production for the near future.
PET Solutions presents an exemplary vacuum dryer solution tailored for PET preforms production: the DRV vacuum dryer. This specialized unit, built on the foundation of 4 registered patents, facilitates continuous vacuum dehumidification of rPET and virgin material.
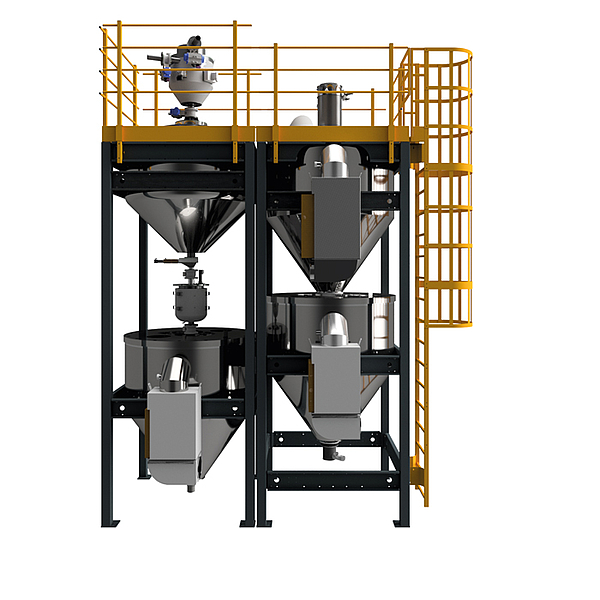
PET Solutions DRV features the so-called “Continuous Vacuum Drying Process”, incorporating four stages hoppers and hot air circulation system to expedite drying and ensure uniform drying across the material:
- 1 st Hopper: pre-heats the resin, gently removing superficial moisture from the material
- 2nd Hopper: heats the resin to energize the material
- 3rd Hopper: employing vacuum technology, creates a lowpressure environment conducive to moisture evaporation from the material
- 4th Hopper: temperature booster of the resin as a fine tune before injection molding
While alternatives exist in the market, the DRV by PET Solutions stands out for its efficacy and efficiency in PET preform production for several reasons:
- Fast Material Changeover: DRV technology reduces material changeover time by 65%, from 6 hours (standard drying) to 2 hours (vacuum drying).
- Condensable Removal: The DRV eliminates residual oil contaminants from recycled plastic without necessitating an oil condenser.
- Energy Efficiency: Designed with energy efficiency in mind, the DRV incorporates an intelligent and advanced control system that enables precise regulation of temperature and vacuum pressure. This minimizes energy consumption and operating costs, obviating the need for an oil condenser.
- Easier & Faster Maintenance: while Standard Drying Processes requires maintenance on process and regeneration filters, heat exchanger and molecular sieves, DRV Series only need maintenance on process filter
- No need of Oil Condenser: Condensable removed trough Continuous Vacuum Drying Technology, making superfluous the use of oil condenser and chiller water
- No more Dessicant Sieves: DRV is not equipped with Molecular Sieves as the moisture is removed trough a dedicated Vacuum Pump.
- Customer Layout Flexibility: PET Solutions DRV can be easily customized through various combination of the 4 hoppers and it is designed using a “Brick Modularity” concept.
- Ease of Use: Featuring a user-friendly touch screen control panel and intuitive interface, the DRV facilitates seamless operation and monitoring. Moreover, it boasts an automatic cleaning system and easy access to key components for routine maintenance.
- Safety Features: The DRV integrates safety measures such as safety valves, interlocks, high-precision sensors and alarms to ensure secure operation and mitigate the risk of accidents or equipment damage.
After four years of rigorous testing and comprehensive validation at both factory and on-site levels, PET Solutions’ DRV technology is now accessible in the market, with numerous units installed worldwide.
The comPETence center provides your organisation with a dynamic, cost effective way to promote your products and services.
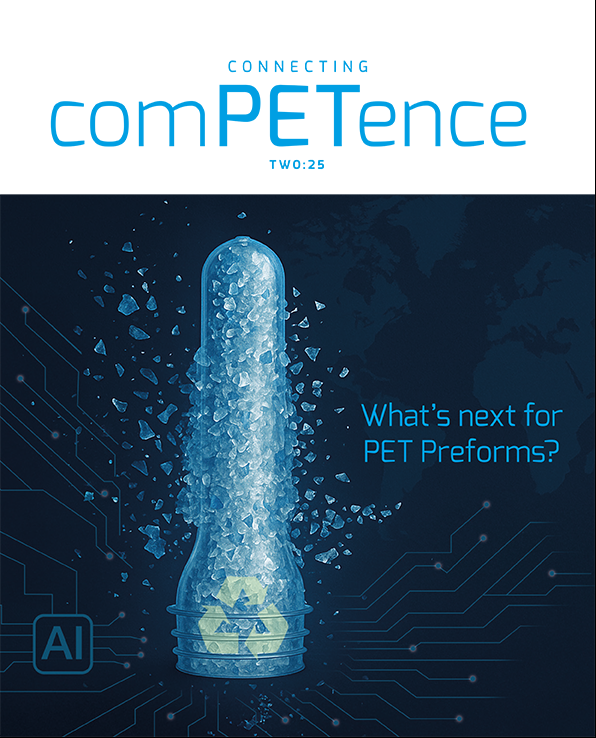
magazine
Find our premium articles, interviews, reports and more
in 3 issues in 2025.