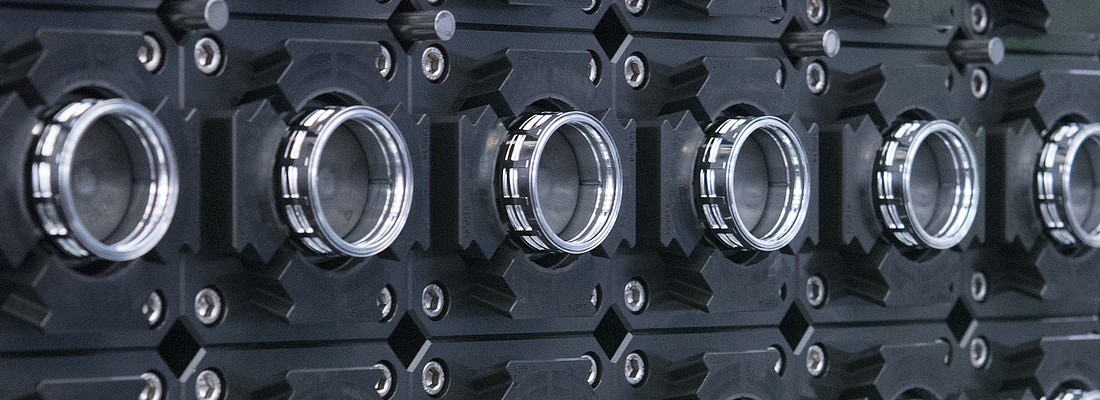
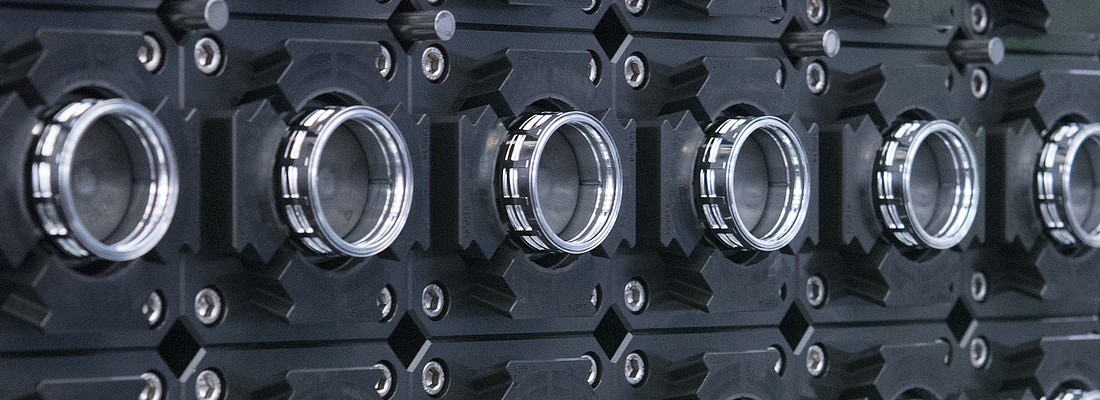
Nowadays, challenges for the caps and closures industry are spread out to various areas. On the one hand a unique closure design provides a diversification for customers and places a strong product branding. This means that dispensing valves, special tamper evident or the possibility of one-hand openings are just some of the key- requirements, which are essential for today’s caps and closure market and underline the uniqueness of the product design. On the other hand, global competition in this highly fragmented and competitive market requires sustainable solutions, like weight savings in cap designs or lowest energy consumption systems in the production field.
This multitude of diverse challenges has changed the demand of toolmakers in the last years. Today, z-moulds is a turnkey solution provider for the closure industry, who covers the entire process from design development to the start-up of a high-performance production system. This can start in an early stage where they develop new closure designs together with their customers according to customer’s performance criteria and end up in supplying a complete mould or even system for most efficient closure production.
INNOVATION AT HIGHEST PERFORMANCE LEVEL
z-moulds is well known as a global technology leader in the caps and closures industry. Numerous patents on mould technologies for an efficient production have been filed in the past years. The latest one is a new single face mould technology for 2-component parts introduced under the name z-smartfill®. One of the most known concepts, that is nowadays widely used and proofed since more than ten years is the z-slides® technology.
This technology is one of the key-concepts for today’s beverage caps producers. With the four sliders moving only in-and-out of the single slider frames, z-moulds established a new level of efficiency in closure production and reached a significant reduction in operation costs. The movement of this innovative ejection concept leads to a huge stress reduction on the mould materials and therefore to a high increase of the typical “wear parts” lifetime.
The big difference to common slider movements is that in this way the sliders only move forward, in mould moving direction, initiated by the ejector – while with all other known technologies the sliders move either left and right in front of the mould nor being bended during their movement. All these movements are adding stress to the sliders and this leads to the fact, that all sliders are typical “wear parts”. z-slides® is different: There the sliders are always just being moved simply forward, while releasing the TE-band, and backward, while closing the mould.
One of the first customers that used this technology has been ALPLA, Austria’s well known global packaging company. Especially the fact, that all cavities in this system are individual and changeable without disassembling the complete mould, have been a big key point for ALPLA.
Walter Knes (Business Unit Manager Injection at ALPLA, ® Austria): “We were pioneers in using the z-slides system since their origin. We are now using this more than 10 years. The flexibility and simplicity of this system convinced us from the beginning on.”
The cavities can be completely disassembled from the front of the mould. Only four screws need to be unlocked and then the cavity stack can be pulled out. This means that the mould has not to be taken out of the machine and be disassembled to change any part of the cavity. This single cavity concept leads to a high rate of standardization and allows customers to switch cavity parts between multiple moulds. For all beverage closure sizes up to 32mm the pitch between each cavity is always 70mm. This means that all closures as 26mm, 27mm, 28mm PCO1881, 28mm PCO1810, 29/25mm and 30/25mm have the same size of cavity frame and therefore it can be used the same mould parts for each different type of closure.
– Only the cavity related parts, the parts that are directly in contact with plastic, are different according to the closure design. This means, that the customers are flexible for future changes and can switch onto new designs by minimal investment.
For Coca-Cola Amatil in Australia and Indonesia this was a key fact for their start in closure production in 2012.
David Chalmers (Operations Manager PSD at Coca-Cola Amatil, Australia): “Coca-Cola Amatil commenced lightweight, high speed 1-piece closure Self-Manufacture in 2012 utilising z-moulds closure mould technology. The Project was a total success, awarding Coca-Cola Amatil with world’s best practice in the TCCC system for closure design, weight and performance. I have since installed a further 7 closure systems with another 3 moulds currently being fabricated.”technology since more than 10 years. The flexibility and simplicity of this system convinced us from the beginning on.”
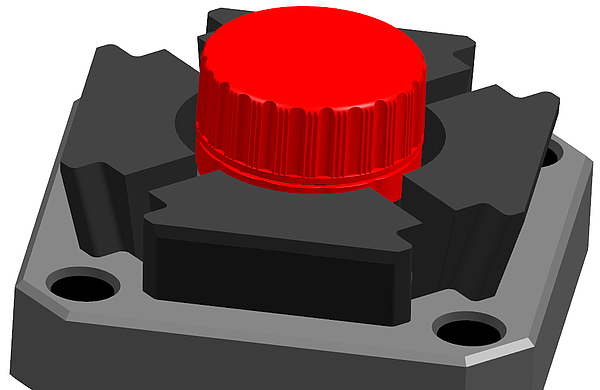
Fig. 2: The four z-slides® in the slider frame moving outside to release the tamper evident band of the beverage closure.
The cavities can be completely disassembled from the front of the mould. Only four screws need to be unlocked and then the cavity stack can be pulled out. This means that the mould has not to be taken out of the machine and be disassembled to change any part of the cavity. This single cavity concept leads to a high rate of standardization and allows customers to switch cavity parts between multiple moulds. For all beverage closure sizes up to 32mm the pitch between each cavity is always 70mm. This means that all closures as 26mm, 27mm, 28mm PCO1881, 28mm PCO1810, 29/25mm and 30/25mm have the same size of cavity frame and therefore it can be used the same mould parts for each different type of closure. – Only the cavity related parts, the parts that are directly in contact with plastic, are different according to the closure design. This means, that the customers are flexible for future changes and can switch onto new designs by minimal investment.
For Coca-Cola Amatil in Australia and Indonesia this was a key fact for their start in closure production in 2012.
David Chalmers (Operations Manager PSD at Coca-Cola Amatil, Australia): “Coca-Cola Amatil commenced lightweight, high speed 1-piece closure Self-Manufacture in 2012 utilising z-moulds closure mould technology. The Project was a total success, awarding Coca-Cola Amatil with world’s best practice in the TCCC system for closure design, weight and performance. I have since installed a further 7 closure systems with another 3 moulds currently being fabricated.”
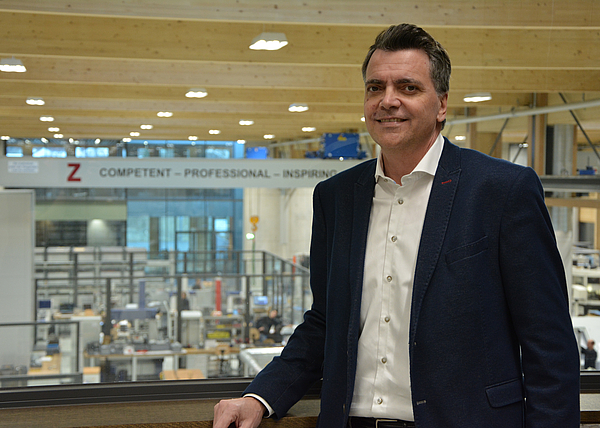
Fig. 3: Walter Knes at the z-moulds factory.
Not only the mould sizes for each cavitation are standardized through this, moreover the size itself could be decreased because the slider movement to the side is not necessary. This leads to a more compact construction and therefore safes up to 20% of weight compared to common lateral slider moulds. Furthermore, a significant reduction of energy consumption could be reached by the lighter moulds.
David Chalmers: “Fast cycle times, exceptional performance, low maintenance and minimal wear parts, great technical support and part design capabilities made z-moulds a perfect fit and partner.”
Another big difference to most other used lateral slider concepts on the market is that this system does not need any electronical control systems to control the position of the sliders. A simple physical stopper concept avoids any malposition by its logic. This simplifies the mould and avoids additional stoppages in the production due to malfunctions of the sensors
from the control system.
The technological progress, accomplished with the patented z-slides® technology, leads to a reduced requirement for maintenance and therefore increases the productive uptime enormously. Overall, this concept allows the highest efficiency in production combined with a very limited need on wear and spare parts.
If you want to find out more about this technology you can meet z-moulds during the NPE 2018 in Orlando (s. also page 112).
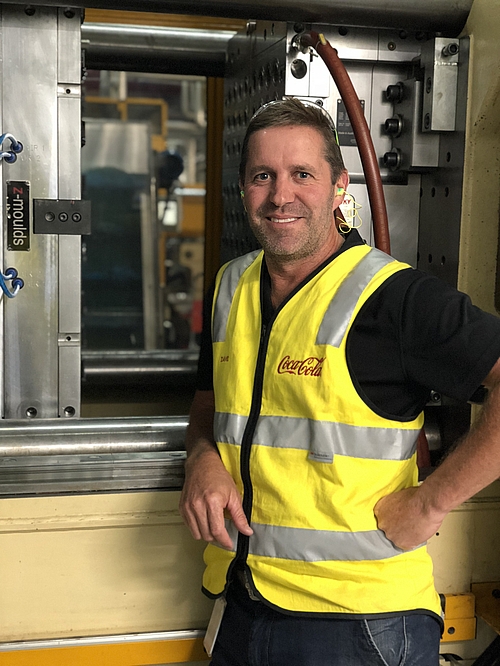
Fig. 4: David Chalmers in front of one of their z-slides® mould.
The comPETence center provides your organisation with a dynamic, cost effective way to promote your products and services.
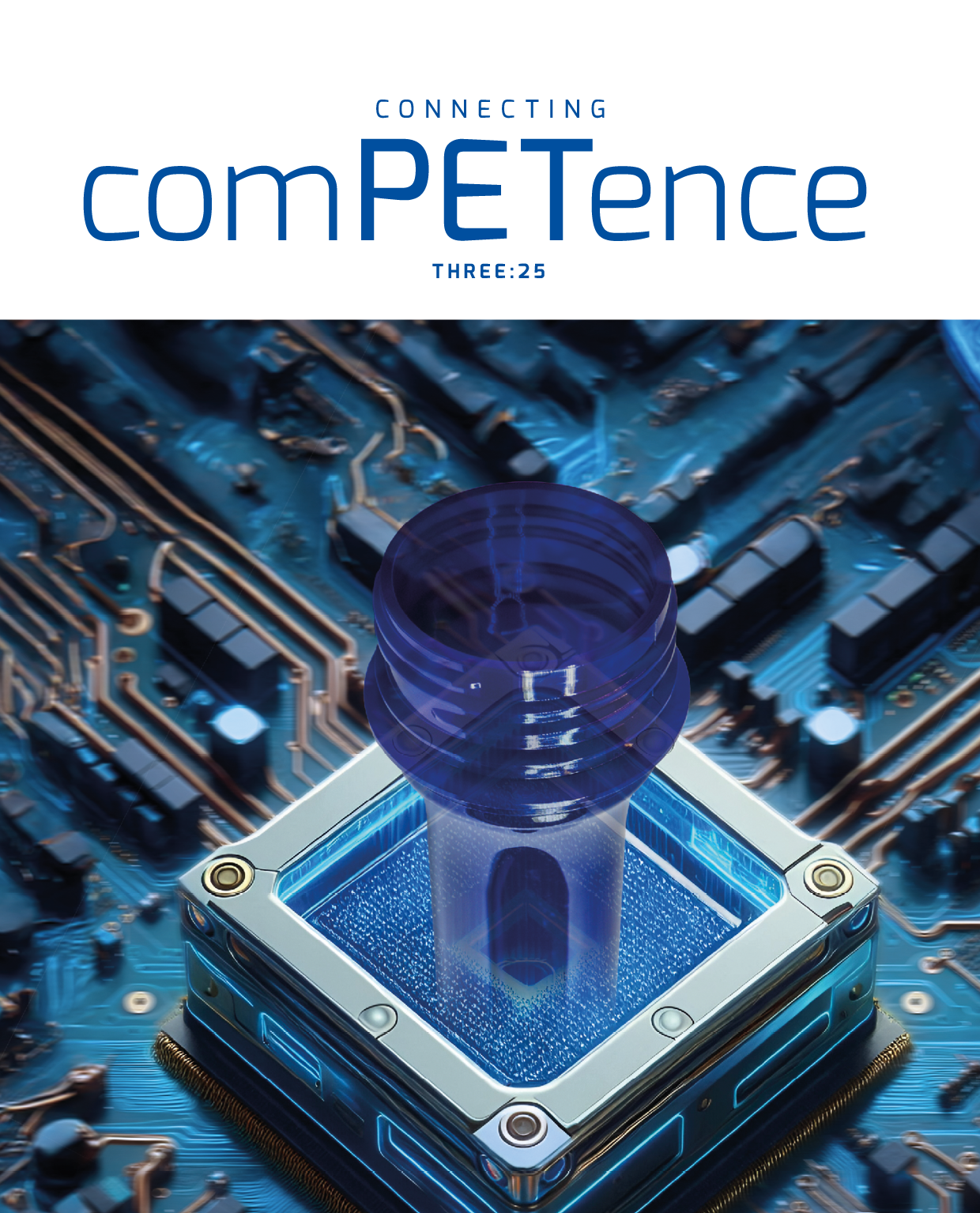
magazine
Find our premium articles, interviews, reports and more
in 3 issues in 2025.