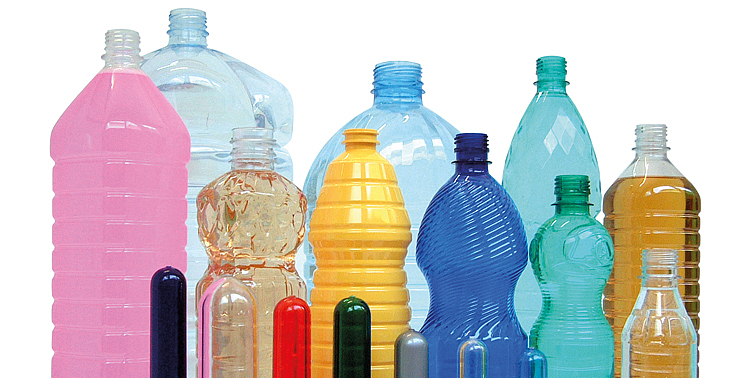
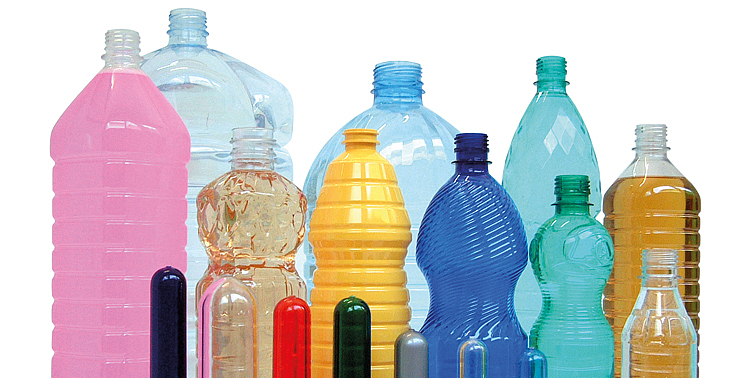
In today’s era of Industry 4.0 and IoT, the food & beverage industry demands increasingly more automated, versatile, interconnected and efficient bottling and packaging solutions, capable of manufacturing large batches of products in the most economical and eco-friendly way.
To achieve these goals, bottlers like Colombia-based Gaseosas Leticia S.A. (Fig. 1), the smallest bottling plant in The Coca-Cola Company’s network, decided to invest in high tech machines and installed a SMI’s EBS K ERGON, a camfree stretch-blow moulding machine featuring a fully electronic bottlemanufacturing process.
Gaseosas Leticia – as confirmed by the company’s CEO Mr. Hauptman Puentes - began its activity 50 years ago with just six employees and a small production of 25 cans of soft drinks per day (around 625 cans per month), while today they sell 2.000 per day (50.000 cans per month).
Over the years, Gaseosa Leticia S.A has evolved constantly. Being part of the Coca-Cola Group has certainly given the company an added value, but there are other factors which are just as important that have allowed this Colombian company to gain a leading position in the region; for example the talent of employees and collaborators and the latest generation technology within the production department.
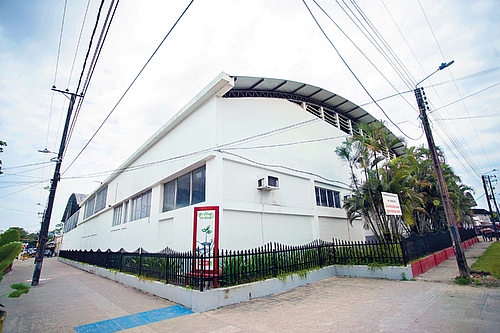
Fig 1: Gaseosas Leticia, the smallest bottling plant in the Coca-Cola Company’s network
Compact preform-heating module
The EBS K ERGON stretch-blow moulding system has an innovative preform-heating module featuring an extremely compact design, allowing it to be integrated into a single machine module along with the stretch-blow moulder carousel (Fig. 2). The module features a horizontal preform feeder chain and an optimized ventilation and aeration system. Moreover, the infrared lamp units, responsible for heating the preforms in transit, are equipped with a system of thermo-reflective panels made of a highly energy-efficient composite material situated both in front of and behind the lamps. This technically advanced solution ensures excellent reflection of the heat generated by the IR lamps, and consequently ensures a more uniform distribution of the heat over the entire surface of the preform. The inside of the module is also equipped with an aluminium diffuser, to provide optimal temperature control and prevent overheating problems. The blow-moulding pressure is automatically regulated according to the bottle format, offering unquestionable advantages compared to the manual adjustment solutions used on the linear stretch blow moulders that SMI’s EBS K models compete with.
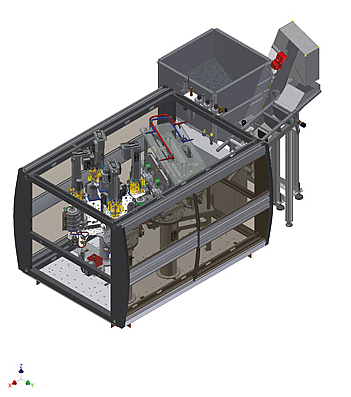
Fig 2: EBS K ERGON stretch-blow moulding system
A fully “cam-free” stretch-blow moulding process
Another important innovation is the motorization of the mechanical mould unit (Fig. 3), that has turned SMI’s EBS ERGON stretch-blow moulders into a real “cam-free” system through its integration with the electronic stretching rod:
- Significant advantages in terms of greater kinematical accuracy, less maintenance, less vibration, less noise and longer life. With only a single servomotor, the new configuration handles both the up & down movements of the bottom of the mould and the opening & closing of the mould-holding unit, greatly reducing mechanical stress and noise, which this machine section is subjected moulder to in the traditional cam-equipped solutions;
- Thanks to this new technology, the dead angle of the stretch-blow moulding carousel shrinks by as much as 10° if compared to the previous generation range, making the structure much more compact;
- The mould-holder’s opening/closing movement are optimized according to the effective diameter of the bottles to be produced. Since this leads to a gradual reduction of the opening/closing stroke, the stretchblow moulding cycle is shorter as the container’s size decreases;
- A motorized stretch-rod eliminates the need of a pneumatic cam and the related time needed to change it, since the servomotor automatically sets itself according to the production speed.
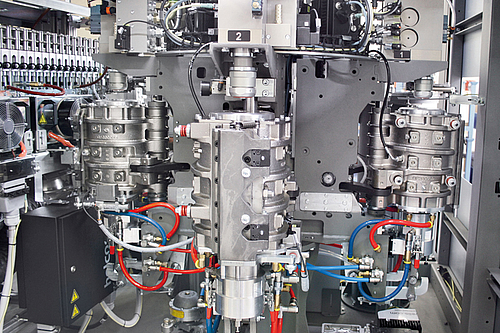
Fig 3: Blowing wheel
New group of valves
The new group of valves reduces the blowing time (Fig.4), as well as the dead volume by 50%: This spared time can be used to reach higher speeds, to have the bottle cooled down or to get a compromise between the two things.
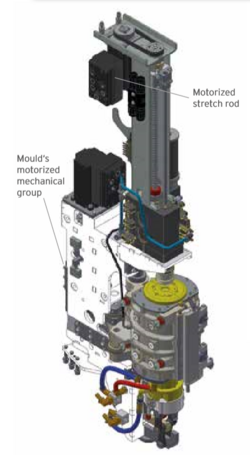
Fig 4: Blowing Station Pre-blowing time: 80* ms Blowing time: 350-400* ms Dead volume: 0.15 L per cavity (*Production of 1.5 L bottles)
AirMaster air recovery system
Double-stage system for the recovery of high pressure compressed air (Fig. 5) mounted as a standard equipment in all of the EBS K models . This allows to reduce by about 45% high pressure air consumption compared to a standard machine.
The machine’s two stage “AirMaster” enables to juxtapose the basic air recovery system with a second plant, in order to recover and recycle a portion of the air of the high pressure blowing circuit. This system ensures a remarkable reduction of the compressed air consumption and of the energy costs. The air recovery system with AirMaster is composed of two systems:
1. The first one allows to recover the air, which is subsequently used for the preblow phase, the LP air network that feeds external units and the service air circuit, has the following traits:
- each stretch-blow moulding station is equipped with three air discharge valves: one of them feeds the recovery system by blowing some air into a tank; the second one discharges the air which cannot be recovered; the third one puts in and takes out air to/ from the PX tank;
- the air recovered is used for the preblow phase, the LP air network that feeds external units and the service air circuit. The operating pressure is controlled by electronic adjusters;
- when the air recovered exceeds the air quantity required by the pre-blowing circuit and by the service air circuit, the air in excess is used to feed the low-pressure line for external units.
2. The second recovery system comes up beside the first one and ensures the saving of further compressed air as it collects a part of the discharged air and uses it exclusively for the blow phase
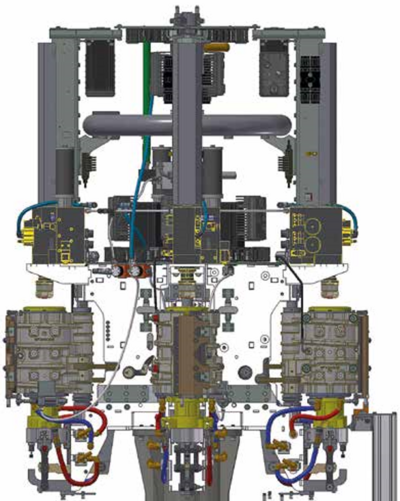
Fig 5: Air Master Air Recovery System
Easy to use thanks to the MotorNet System® technology
SMI stretch-blow moulders and integrated systems are designed according to Industry 4.0 parameters, fully automatic processes, electronically-controlled operations and wiring by field bus. These are synonyms of reliability, considerable operational flexibility and high performance. Hardware and software components are IoT (Internet of Things) ready, are “open“ and modular, comply with the most important international certifications and rely upon consolidated standards of the industrial field and of the packaging sector: OMAC guidelines (Open Modular Architecture Controls), sercos, PROFIBUS, IEC61131, OPC, Industrial PC.
In particular, by following the OMAC guidelines and the Omac Packaging Workgroup (OPW), SMI can guarantee easy integration with the other machines in line, user friendly technology and maintenance of the investment value. The automation and control system of SMI machines, called MotorNet System®, includes the following hardware components: MARTS (process controller), POSYC® (manmachine interface), COSMOS (digital servodriver for brushless motors), dGATE and aGATE (remote IP65 I/O digital/ analogic modules).
The MARTS is a PAC (Programmable Automation Controller), based on an industrial PC, which can be programmed in IEC61131 languages. The COSMOS servodrivers and the dGATE/aGATE I/O modules are connected to the PAC via sercos. The POSYC® is a HMI terminal, (touch screen IP65), based on an industrial PC with solid state drives.
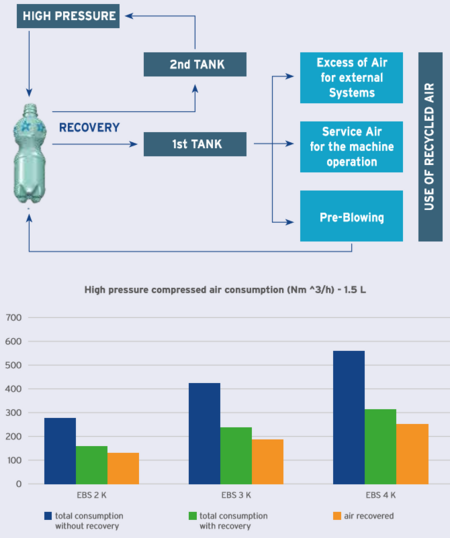
Fig 6: Compressed air recovery system: examples of application on EBS K ERGON models 1.5 L bottles / 2250 bph-cavity / 33 bars
Functions menu of the MotorNet System:
- To set the heating profile for each preform and the parameters influencing the phases of the stretch-blowing process (from when the preform enters the heating module up to the container)
- To adjust the power of each lamp in each section of the heating module
- To control the operation parameters of each stretch-blowing station and monitor the whole stretch-blowing process in real time
- To store the parameters of each blown container
- To check and set the machine production speed, according to the different types of containers
- To carry out the changeover in a quick and easy way
- To solve or prevent any problems, thanks to the teleservice, the graphic alarms displayed on the POSYC® and the signal of the maintenance interventions to be carried out
- To have access to the on-line manuals on the POSYC®
- To ensure high outputs, excellent quality levels and very low noise
- To monitor the performance and analyse the down-times (Pareto diagram)
- To interchange the POSYC® with compatible Panel PC (SIEMENS, ALLEN BRADLEY)
- To interchange the COSMOS with compatible sercos pack profile servodrivers.
Through this latest investment, Gaseosas Leticia aims to widen its production capacity by bottling soft drinks under the the Coca-Cola brand in 0.5 L and 2 L PET bottles.
The comPETence center provides your organisation with a dynamic, cost effective way to promote your products and services.
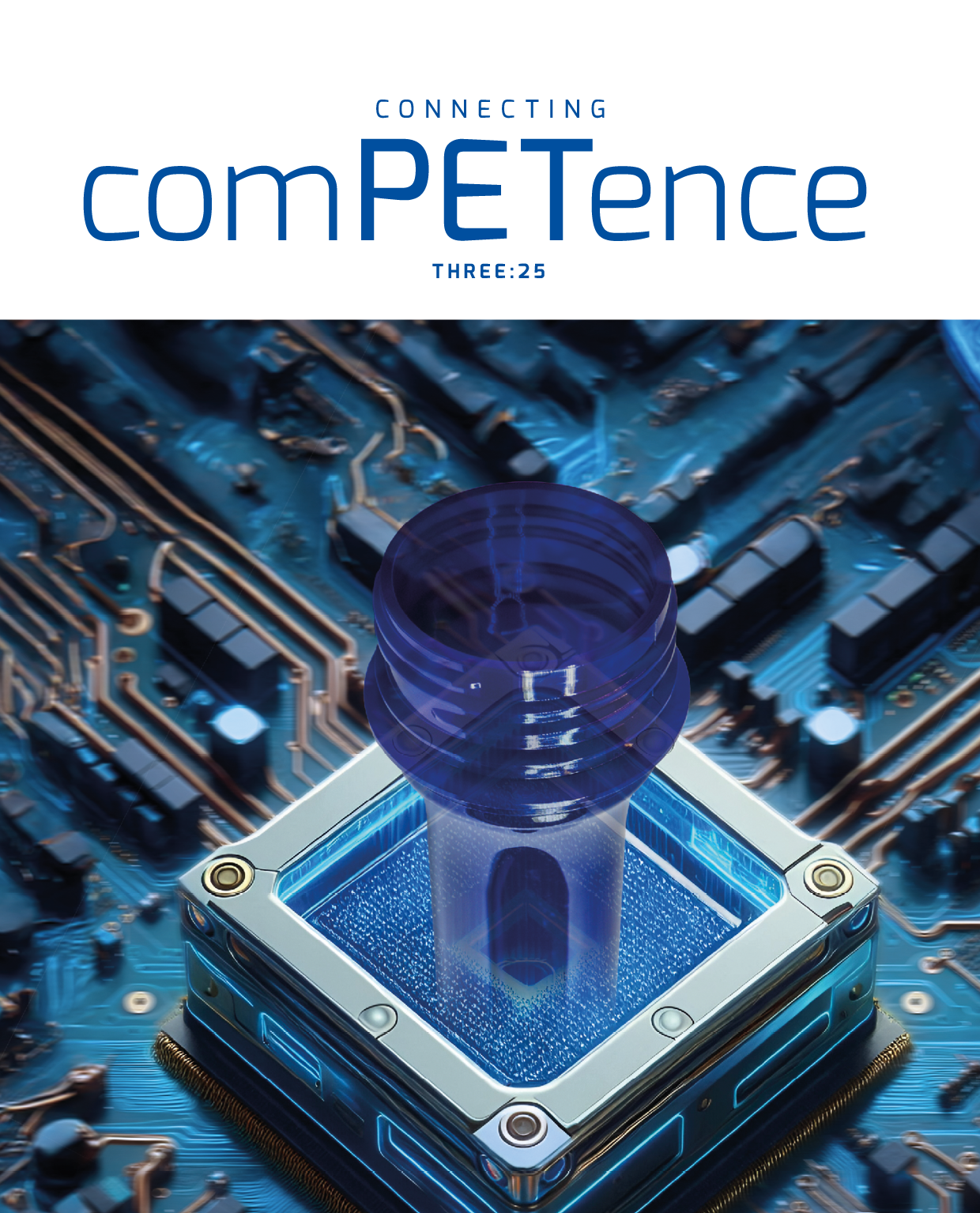
magazine
Find our premium articles, interviews, reports and more
in 3 issues in 2025.