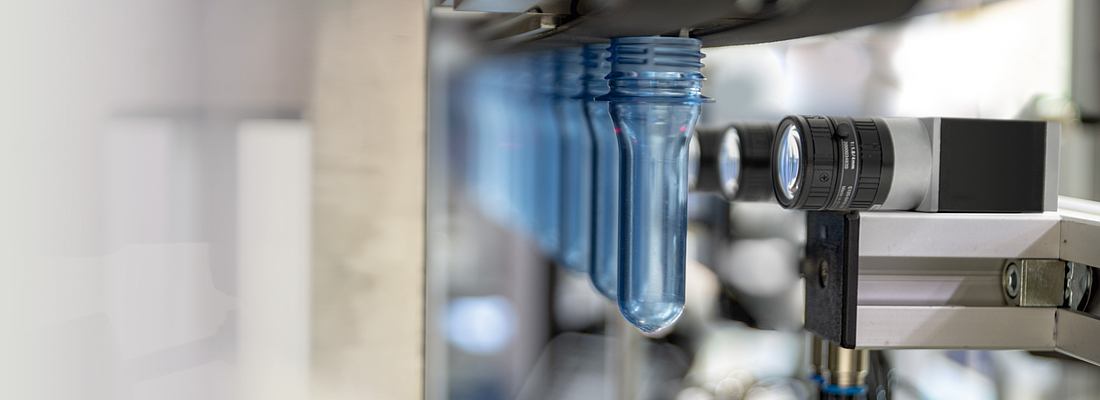
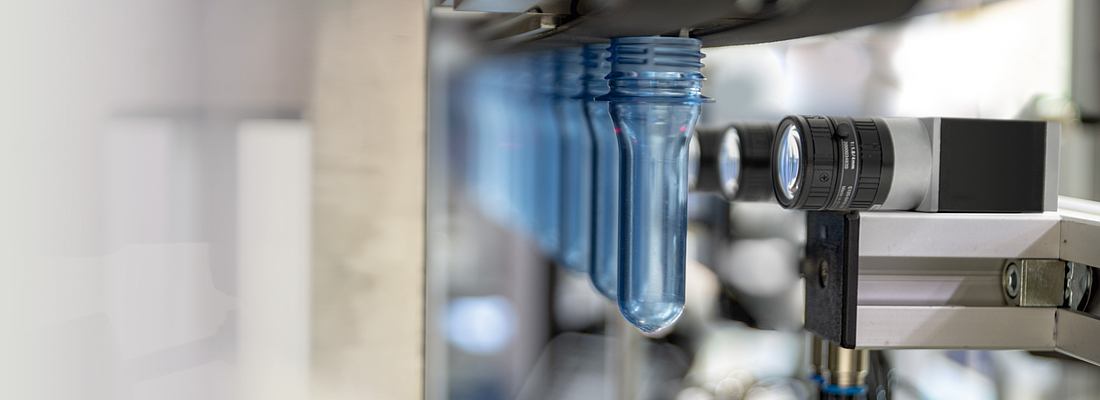
25 Years of Intravis — A Success Story from 3D to 2D. Inspection, Monitoring, Control: the Evolution of Image Processing
With this comPETence interview by Prof. Dr.-Ing. Otto Appel congratulates Intravis on 25 years of excellence. As the Aachen company Intravis celebrates 25 years in business, it’s the perfect occasion to reflect. What are the roots of this company? How did it all start? What did the technological environment look like back then? How has it changed? We take a look back and ahead with Dr. Gerd Fuhrmann.
Anyone who knows Gerd Fuhrmann knows that he is a family man. And so it’s no surprise that we begin by talking about our families. About our children, who are growing up far too fast, and about the rich and fascinating experience of growing up. The actual purpose of our meeting is to discuss the history of Intravis, and we move onto this topic quite naturally as Gerd Fuhrmann describes his company as “one of his children” that has now come of age. This leads me to ask how he feels about the company’s growth and whether he worries that the closeknit nature of the Intravis family, which has always been very important to him, could be lost.
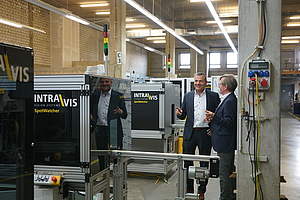
G.F.: It’s wonderful to see Intravis evolve, to see it “grow up” and enter uncharted waters. Am I worried? No. We’re still very much a family within the company, that’s something which is extremely important to me. But there’s a right time for everything. It’s like changing nappies — it’s an essential step, but then you move on to the next step. Everything changes and evolves. We’re moving forwards with Intravis and I’m very glad that we decided to let our little engineering office grow. I’d say that this choice has helped us to stay alive, given us a raison d’être. Because we need to be a certain size to survive in our markets. I think in this sense we’ve done everything right, including focusing on a single market.
Of course, there also comes a point when you have to be able to let go. My question is about the attention to detail that I’m sure was a huge part of those early years for you. As the company grows, the boss can’t be involved in every aspect of the business down to the same level of detail. Do you find it easy to delegate responsibility?
G.F.: Looking back on how Intravis has developed, I can say that every part of the journey has been both challenging and enjoyable in its own way. Of course, Company Formation Objective: Construction of microtomography equipment -> hence the name “IntraVis” - 80486 Processor - Coaxial networks in serial configuration - Camera technology: 640 x 480 (partially interlaced) - analogue output (frame grabber) predominantly CCD technology when we started out I was very much hands-on — soldering circuit boards, purchasing cameras and lenses, providing customer support for our systems. Would I still like to be soldering circuit boards today? No, I wouldn’t. Do I enjoy being a point of contact for decision makers at major international companies and brands, and helping to shape strategy? Yes, I do. The time that my company took to develop was time that I needed and used for my own personal development. As time has gone by and things have changed, I’ve worked in a lot of different roles. But there are two things I can say for certain. I was always a passionate engineer, through and through. And I always wanted to work with cutting-edge technology. Both of these things are still true today — even if I don’t solder circuit boards any more (laughs). My focus has necessarily shifted to the bigger picture, to our overall strategy. What can we do to reach our customers and provide them with added value? That’s the front line for me, that’s where I get involved, liaising with staff at every level. So I have delegated responsibilities, but I’ve managed to stay in touch with every area of the business.
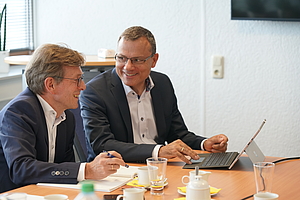
The atmosphere in the company is very important to you. Where does that come from?
G.F.: Yes, very important! When I founded the company, my vision was about more than just the technology. It was absolutely crucial for me — and still is, and always will be — to ensure that our team feels like a family. This is something that became increasingly clear and increasingly important to me. Not because I had encountered a lot of good examples. Before I set out on my own, I worked in a lot of different places, including in large companies. I often found them to be extremely impersonal. People didn’t really know each other, even colleagues who worked closely together. Once, when I was an intern in Munich, I suggested to the rest of my department that we go to a beer festival in the city. Their first reaction was pure astonishment — people in the company just didn’t have ideas like that. But we went, and spending the evening together helped the group to find common ground that they hadn’t realised they shared. I had similar experiences when I worked as a scientist. Most of my colleagues seemed to have real tunnel vision. They were all wrapped up in themselves and their research projects. Spending time together, being considerate of each other, taking an interest in each other? Forget about it. And that’s something that I just wanted to do better.
Have you found that more difficult as the company grows?
G.F.: The tasks involved in management are constantly being redefined and, of course, they’ve become more wideranging over time. Creating structures, supporting individuals, setting an example. I’ve made sure not to lose sight of that. Of course, I go about things in a different way now that I’m not a line manager any more, for example. Today, I have to make sure that the unit, department and group leaders are embodying and implementing the Intravis leadership mentality. This is no mean feat. I’m sure you’ll agree that, sometimes, technology-loving engineers don’t quite seem to be naturals when it comes to people skills and socialising. The only thing to do here is offer training and set a good example.
Your own roots, of course, aren’t in plastic technology. How did Intravis find its way into the plastics industry?
G.F.: You’re right. I got involved with plastic technology when I was working on the first orders that we received. A quick bit of background — I trained as an electrical engineer with a focus on telecommunications, and did a doctorate at the research centre Forschungszentrum Jülich in cooperation with RWTH Aachen University. I also studied business administration via distance learning with FernUniversität Hagen. That in particular gave me the idea of setting myself up independently in the field that I wrote my doctorate on: microcomputer tomography. This technique can be used to generate three-dimensional images of the inside of small samples, perhaps the size of a fly’s head. That’s also where the company’s name comes from. Intra for “into” or “inside” something, vis for “visualisation”.
And at that point you still weren’t thinking about plastic technology at all?
G.F.: No, initially I was working with tomography, then with sewing needles and fishhooks. And a lot was determined by the particular circumstances in our region. Another bit of background — when we started out in 1993, coal mines were being closed across the Aachen region, a major industrial sector was collapsing. The EU declared us an Objective 2 region and set up programs to provide economic support for new companies working in technology. This made it possible for us, as well as other businesses in the region, to take our first steps. In fact, we built a microtomography instrument. And it was a complete flop. Why? We were too far ahead of the curve. When I presented it at a major automobile company, the instrument was well received. But they made it clear that the internal process of validation, budgeting, approval and ordering would take two years. “And by then we’ll be broke,” was my answer to that — and we had to look around for something else.
Such a huge setback right at the beginning?
G.F.: In retrospect, it’s really good that things didn’t go to plan right from the start. That forced us to think about cost And at that point you still weren’t thinking about plastic technology at all? G.F.: No, initially I was working with tomography, then with sewing needles and fishhooks. And a lot was determined by the particular circumstances in our region. Another bit of background — when we started out in 1993, coal mines were being closed across the Aachen region, a major industrial sector was collapsing. The EU declared us an Objective 2 region and set up programs to provide economic support for new companies working in technology. This made it possible for us, as well as other businesses in the region, to efficiency every step of the way. So this disappointment actually broadened our horizons. We took a step back, from three dimensions to two. Instead of spatial reconstructions, we focused on flat images and on evaluating these images. The very first technical product we worked with was sewing machine needles, which used to be big business in the Aachen region, alongside the textile industry. Back then, the needles were checked by hand. The workers would place a few needles side by side and roll them back and forth with their little finger to sort out any defective ones – see “Klenkes – landmark of Aachen” on page 70. This manual needle inspection is very interesting from the point of view of image processing, because it’s essentially a “token search”. That means you’re just looking to see which token, or part, is different. Nothing is being measured, just compared. If it deviates from the rest, it’s defective. I got to know the manager of a large needle factory, who was very open to technology. He made the first order we’d received that came with the promise of a follow-up order. “Build us a needle inspector, and if it works, we’ll buy another one,” was essentially what he told us. And the instrument we built could carry out really comprehensive inspections. The needles rolled onto a device which we could then use to inspect their entire surface, including the eye and the point. We could even check if the company’s stamp was in the right place — which in a sense anticipated the technique for recognising cavity numbers in preforms. It worked brilliantly, and six machines were installed. We made it into the local press with the headline “Intravis replaces the ‘klenkes’”. I can say with relative certainty that that company was one of the last in the region to close its doors — that’s how competitive our image processing technology made it. So we were already in contact, and after the needle inspection machine we worked on inspecting fishhooks.
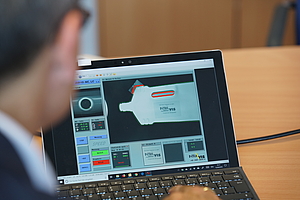
At that time, were the challenges mostly related to image processing or more to handling within the system, e.g. sorting out the faulty needles?
G.F.: We’ve always believed that the system needs a comprehensive, integrated approach. And we’ve always seen ourselves as holistic engineers, so in that respect visualisation and mechanics have always gone hand in hand. Our head of design has been with me since day one. He’s a mechanical engineer. So you can see that mechanics was very important right from the beginning. He’s employee number 25, and that includes all of the assistants who served drinks at our launch party. To illustrate how much we’ve grown: back then we checked 2–3 needles per second, now it’s 70 caps per second. But back then that was still incredibly fast.
Was image processing on the brink of a breakthrough when you launched?
G.F.: We came along at the right moment. There had already been a wave of enthusiasm for image processing in the mid-1980s. People thought that this technology would make virtually every inspection task simple. That was a misconception. They took it too far, the bubble burst, and the enthusiasm ended in disaster, we can see that today. It was a major step back for the industry. When we started out in 1993, the whole thing began again. This time, it all rested on PCs. They were a ground-breaking development with enormous benefi ts for image processing. At that time there was still some talk of image processing using transputers, but in our view that was far too specialised, too much manual work. We focused on PCs and above all on their potential — each new generation of PCs would automatically give us another boost. So we worked entirely with the standard technology from the outset, and we were able to grow with it, you could say. It was exactly the right decision.
Needles, fishhooks — you hadn’t really made it yet, had you?
G.F.: You’re quite right. Basically, we were on the lookout. Where can we find promoters? Where can we use and adapt our technology? Which markets can we tap — with modified, but not fundamentally new methods? And we were essentially quite lucky in the beginning, and there was also something of a happy coincidence. We were pursuing two approaches around the same time. In 1995 I came into contact with the plastics industry for the first time. One channel was the optimisation of CDs and CD sleeves. We built a system for that purpose. The other channel was in fact the one that we ended up following into the future. But we really couldn’t have predicted that at the start. I’ll come to that in a moment. The catalyst might have been my conversation with a student who was working with us to write his thesis. His parents had a business producing plastic sheets, and he said to me: “Gerd, the plastics industry is where the money is, it’s where things are happening.” I got in touch with a nearby extrusion blow moulding facility. They had problems with flashes, and we were able to provide a quotation. Which was rejected out of hand. But that was, strictly speaking, where it all began.
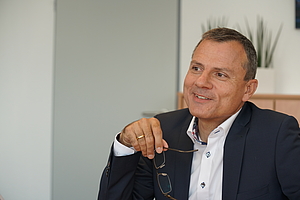
That could have taken the wind out of your sails. Or did it just make you more determined to succeed?
G.F.: If anything, I’d say we got a second wind. We received another order, this time from a company in the German region of Baden. We monitored the inmould decoration of extrusion blowmoulded bottles for them. And we actively advertised this in specialist media for the first time. In response to that I got a call from Switzerland, from a blow moulding machine manufacturer who described problems with flash. We clicked with each other right from the start, if I may say so. I visited the premises and he described the situation to me in detail — some containers were coming out with flash still attached to them and he was looking for a solution to separate them out. He was impressed by our idea of enabling the operators to “teach” their machines new bottle types simply by pressing a button, without needing to know anything about programming or image processing. Three suppliers made the shortlist for a field test. We hadn’t yet talked about money, only alluded to the sales potential. In short, we took part in the competition for free. The test was carried out at a blow moulding facility in France. We didn’t just have technical problems — our hardware briefly stopped working, the container we were testing was suddenly transparent and not through-coloured, and we had to wrestle with the French language. But things didn’t quite go to plan for the other companies either, so the deadline was extended for all of us. Two weeks later, we all had to present our systems again. In the end we won the contract. Our system’s user-friendliness tipped the balance.
That sounds like a breakthrough.
G.F.: Yes, you could say that. I was personally informed that we had won the contract by Günther Lehner, CEO of Alpla. I’ll never forget that meeting. Not just because Mr Lehner wanted to order 50 machines, a number that was inconceivable for me at the time. But in particular because it was such an enjoyable talk. I had to tell him that, as a small business, we couldn’t deliver 50 systems at once. And I also had to admit: “We need an advance payment.” He was understanding about everything, he approved the advance payment for all of the machines, he staggered the delivery deadlines and put us in a position where we were able to complete the order. That was absolutely the breakthrough. Alpla was a catalyst for Intravis.
Have you ever experienced anything like that again?
G.F.: In the last 25 years we’ve had more than a few customers say: “I have faith in you, Gerd.” With one of our recent developments, for example, the LayerWatcher. And with the PreWatcher, which can read cavity numbers. That was another customer who told us: “You can do it!” And we could. At the time, it was a world first. At some point, of course, there’s less room for trial and error, less tolerance. You see the change when an industry is established — it becomes tougher, more competition-oriented ... It’s a real shame, but it’s a natural development. Just look at the preform business. It’s always been high tech, today more than ever. The difference is that, previously, there was good money to be earned there. Now it’s a commodity and extremely competitive.
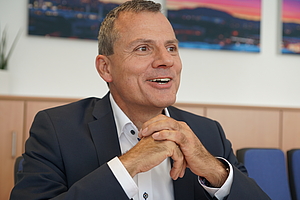
Did you review your products and your strategy as part of this major order for Alpla?
G.F.: Yes, it was precisely then that we decided to really focus and not to work on fishhooks any more. That’s the only way to understand the industry’s unique language and to speak this language yourself. You can be much more involved and understand the problems that arise, you can see the direction the industry is developing in, how new influences need to be handled. And of course you build up a network, you integrate, you become an important part of the network. And that provides validation and spurs you on. This has also led to a number of new developments — for example, the inspection of barriers, leading to the BarrierWatcher and in turn to the LayerWatcher, which can p r e c i s e l y measure the position and thickness of the barrier. We were also the first company to take the basic inspection process further, to track an item, perform a second inspection and assign the result to the item, etc., making it possible to combine results at the end and decide whether the item needs to be discarded or not.
Could you describe the method?
G.F.: The technology behind it is something known as a sequencer, which we developed ourselves. It was about five years ahead of the curve in the image processing industry. We didn’t immediately realise that at the time, and we had one or two patents that we ended up forgetting about. The whole world was working with PLC, with cycle times of 20–30 ms, and we were in the microsecond range thanks to our proprietary hardware, which had its own processor. I’m still impressed by the software technology that we used — programmed in assemblers — in order to reach those speeds. That made it possible for us to do certain things that other companies hadn’t yet managed. We should have taken out a lot of patents back then, but we were too small still. Today we do patent new developments, and a few of our patents have made waves in the sector, if I may say so.
Could you give an example for our readers?
G.F.: Yes, one example is a method of spark testing that doesn’t require the electrode to be introduced into the item. The method makes it possible to detect any micro cracks at the gating point of the cap. Previously, the electrode had to be introduced into the cap while a high voltage was applied to the opposite electrode. Sparks occur if there are micro cracks around the gating point. With our system the electrode stays outside the cap, and we are able to direct a very straight beam downwards despite the relatively great distance. So there is no need to introduce the electrode into the cap.
How did you get to the point, in terms of technology, where you were able to create the systems of today?
G.F.: One important factor is of course the increase in processing power, from the 486 processor to the multi-core i7 processor. And software systems which exploit the full potential of these cores to increase operating speed also helped us enormously. Then, of course, there are the cameras. The first thing to mention here is the increase in the number of pixels — and the simultaneous drop in prices. The increase in pixels made it possible to use colour cameras. A colour camera needs three pixels to depict a single point of colour (RGB), meaning that it has only roughly a third of the resolution of a black and white camera. Today, we’ve moved on from 640x480 pixel cameras in black and white to megapixel colour cameras. The second factor is that we’ve progressed from a camera which produced 50 fields per second — with two fields making up one video frame — to around 100 frames per second. The third major development, which attracts somewhat less attention, is the light output, for example for extremely short flashes. To this end, we build some of our own tools that aren’t available on the market in the same form. We can “freeze” movements by robotic arms, for example, using extremely short flashes with a high light output, to achieve a high resolution and depth of field. That’s a hardware development. I haven’t seen quite the same progress in optics. In software, there is one development which promises a paradigm shift: the option to buy image processing software in the form of libraries. That’s something that we need to keep in mind.
Your sector has always been an extremely dynamic one. What does the future hold?
G.F.: It certainly has. In the future, we’re going to have to make sure that we can offer complete systems with all the peripherals — connections for injection moulding and blow moulding machines and for labellers, as well as financing solutions and the evaluation of the vast amounts of data that our systems deliver. That’s the challenge we face in the future, and we’re prepared and ready to take it on. At the end of the day, it’s all about providing the customer with a value that’s greater than the cost of the system. Here we’re really seeing the returns on the decision we made right at the beginning: not to focus purely on image processing itself but to offer system technology with comprehensive customer support.
In other words, from the simple to the complex.
G.F.: In fact, at the beginning we focused solely on detecting flash and separating out defective items. We do still do this today. But today the data collected is also sent to a central data and operations centre, from production sites which are in some cases located all over the world. Discrepancies and problems on the lines can then be detected from the centre, and measures and solutions can be put in place. If necessary, servicing instructions can also be given to the relevant staff on-site. Our aim is to use the data situation to identify how the process is unfolding. That’s the future, that’s where we see ourselves, and it’s what our slogan describes: “We solve problems. Before they occur.” At Drinktec 2017, we presented this approach for cap manufacture together with Netstal. To sum it up, the systems no longer just define “go” or “no go”, good or bad — they deliver highly accurate readings at an unbelievable speed. As I mentioned, 70 caps per second are measured with an accuracy of 0.01 mm. This precision isn’t necessarily crucial for the plastic cap as a matter of course, not in every area, but it’s needed for early detection of any abnormalities in the process.
Are a lot of manufacturers upgrading to this technology? Or is there still some way to go until it’s used as standard?
G.F.: It’s still early days. I think things will develop in this direction over the next decade. But I want to warn people against believing that artifi cial intelligence will make the user obsolete. That’s a fallacy that spread for the first time in the 1990s, along the lines of “tomorrow we’ll have a self-confi guring injection moulding machine”. It will still be many years before all of that can be fed into the artifi cial intelligence system to enable unstaffed facilities. Every major development also has societal implications. What will trade unions have to say about production sites with no staff, what will hosts of QA employees have to say if a machine takes their job? We have to include these people, and manage the transition and everything afterwards to ensure that enough consideration is given to the societal aspects. Not everything can be replaced by hardware and software. There needs to be an understanding of that, and of the limitations, at every level of business. When it comes to introducing innovations on a large scale, we already know from our experience in major companies that if you don’t include people in the change, it will fail. The technology is one thing, but establishing a technology on the market is in part a political challenge, as we can see from the debate around Industry 4.0. So it will still be a while before we see fully automated, unstaffed factories.
How do you picture the transition taking place?
G.F.: I think the first step will be lightening the burden on machine operators so that they are able to supervise more lines without increasing their workload. And I think we’ll also see production sites with a reduced staff, as well as new business models involving, for example, absolute specialists monitoring multiple facilities from a central location. These specialists will then help the people on-site to effi ciently maintain high production standards. A lot of things are going to be possible, but at the same time a lot of questions are going to arise, in terms of hardware and software as well as sensor technology. We’re seeing so many new ideas — it’s going to be an extremely exciting journey, but a long one, for sure.
Thank you.
The comPETence center provides your organisation with a dynamic, cost effective way to promote your products and services.
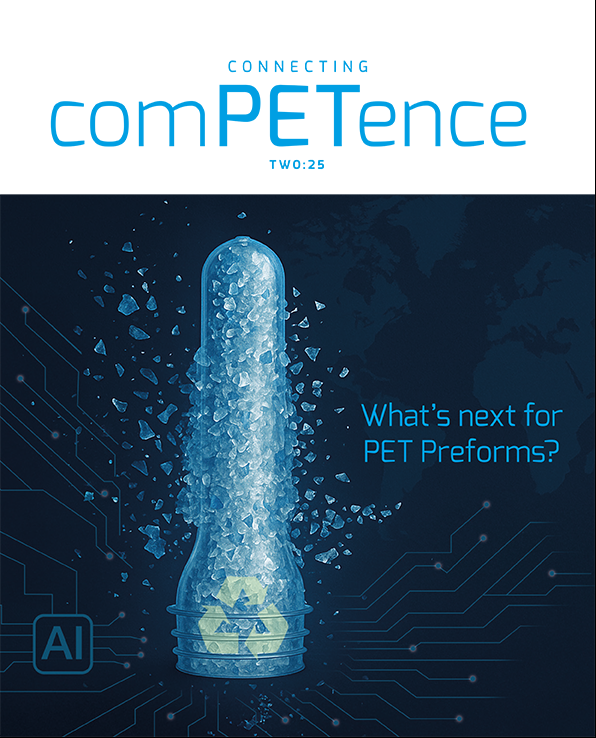
magazine
Find our premium articles, interviews, reports and more
in 3 issues in 2025.