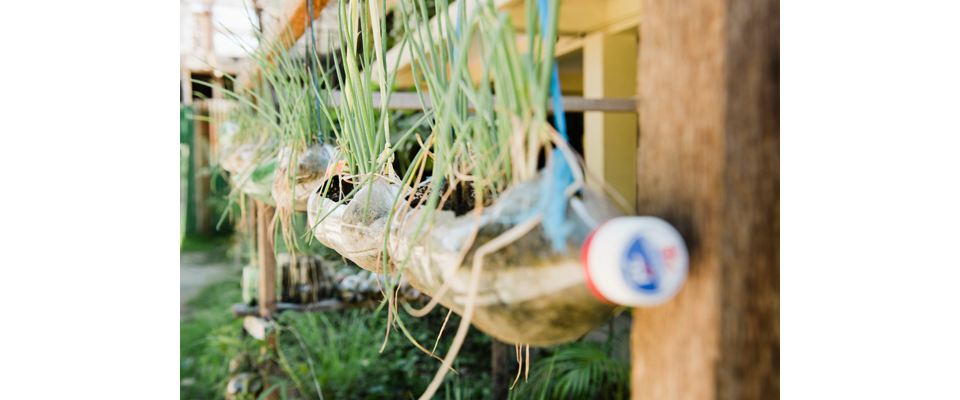
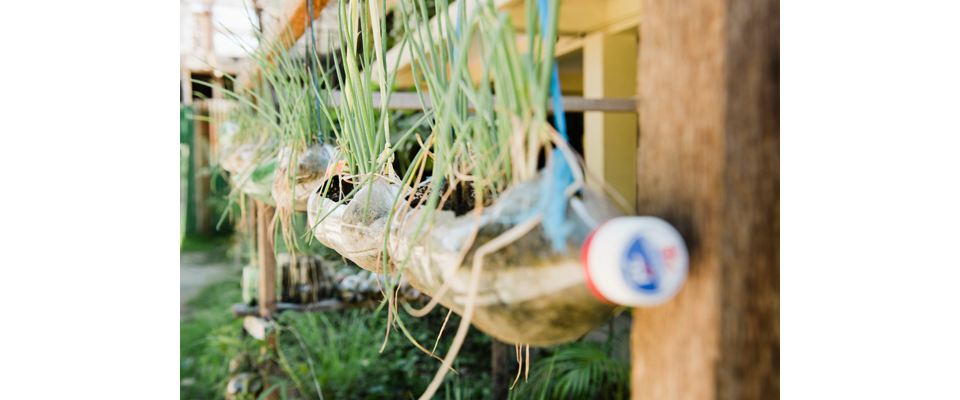
PET containers and plastic packaging are currently very much the subject of public criticism. One priority is to reduce and recycle the same. KHS supplies dedicated systems for this purpose and has at its disposal a wealth of expertise with which it strongly assists its customers in their striving towards greater sustainability. (Photo credit: KHS)
The beverage industry and the protection of the environment: reduce and recycle are the order of the day
KHS tackles the challenges posed by sustainable packaging and already offers market-proven systems to this end
The global debate on packaging waste, the associated use of resources and increasing regulatory pressure have further intensified the call of the beverage industry for new, alternative packaging systems. Concerns not only focus on saving on resources in the production process but chiefly on the packaging itself. PET containers and plastic packaging are currently very much in focus. One priority is to reduce and recycle the same. KHS supplies dedicated systems to meet these criteria and has at its disposal a wealth of expertise with which it strongly assists its customers in their striving towards greater sustainability.
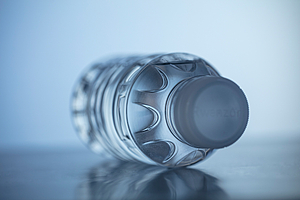
KHS has been a partner to the beverage industry for 150 years and knows what it wants. In this sector the subject of sustainability has long been an issue. On the one hand there are climate goals to be met – or specifically a steady reduction of the carbon footprint in beverage production to be achieved through the development and use of systems which increasingly save on energy and resources. On the other ever greater importance is being attached to devising innovative packaging machinery which is of benefit to beverage producers and consumers alike. The way to produce ever more sustainable primary and secondary packaging involves two major lines of approach: recycle and reduce. In the first, packaging material is to be kept in constant circulation where possible by it being reclaimed, processed and continuously reused. In the second, many different ways are to be found of using less and less packaging material in order to save on resources and avoid waste. KHS pursues both of these objectives and offers specific technologies to this end.
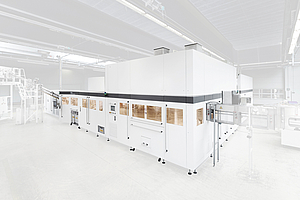
FreshSafe PET®: the only fully recyclable barrier system
One big step towards engineering a strong, efficient and thus sustainable circular economy is to improve the recyclability of PET bottles to such an extent that they are suitable for bottle-to-bottle recycling. Fruit juice bottles in particular often comprise multilayer, blended or scavenger materials which are designed to protect sensitive beverages from external influences such as oxygen pickup. The aforementioned additives contained in the preforms often prove a hindrance to pure-grade recycling, however, and thus to their use in full bottle-to-bottle recycling. With FreshSafe PET® – a patented plasma coating system – KHS provides the only accredited fully recyclable barrier system to date which significantly increases recycling quotas for PET beverage packaging with enhanced product protection the world over. This has been confirmed by a number of recycling associations such as the EPBP1 and APR2. In the above process the inside of the PET container is coated with a wafer-thin protective layer of silicon oxide (SiOx) or chemically pure glass. This technology replaces the additives otherwise required. It guards sensitive products such as fruit juice and nectar against the penetration of oxygen and other substances and clearly reduces any additional loss of CO2 from carbonated beverages. The taste is retained, the beverages have a longer shelf life and full recyclability is made possible by this process.
Growing demand for rPET container systems
Another way of further improving the ecobalance is to increase the amount of recyclate or rPET used in PET containers – in some cases up to 100%. KHS provides the technology for this option. For example, in cooperation with bottler Mineralbrunnen Allgäuer Alpenwasser, preform manufacturer Plastipack and Berlin startup share the systems supplier has developed and successfully launched to market a 0.5-liter and 1.0-liter PET bottle made completely of recyclate. “Manufacturing a PET bottle from 100% recycled PET is possible – yet the devil lies in the detail. We have to approach this from a number of different angles,” says Arne Wiese, product manager for Bottles & ShapesTM at KHS Corpoplast in Hamburg, Germany. “Chemically recycled PET yields qualities which exactly match those of virgin PET. There are no restrictions here.” Yet much of the rPET used on the market is PET cleaned in vacuum conditions. “Here, qualities vary depending on the method of production,” explains Wiese. However, the quality of the rPET affects the bottle stability and weight. This means that the poorer the quality of the recyclate, the more stable the bottle has to be. This can be achieved by either increasing the weight of the bottle or optimizing the preform. “If a bottle is so light that it just about satisfies the requirement for stability, then any recyclate of an inferior quality means that this specification is no longer met,” Wiese states. Furthermore, at present rPET is not available in the required quality and quantity. Germany may boast the largest percentage of recyclate used in bottle-to-bottle recycling (32.6%), yet the remainder of over 65% is primarily used in the film or textiles industry. In addition, suitable puregrade recycling systems are also largely lacking the world over.
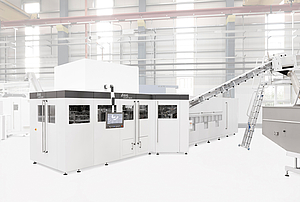
Full concept Bottles & Shapes™
The impact the use of recyclate in different quantities and qualities has on the stability and weight of the bottle is taken on board, however, in order to positively influence the ecobalance. On the basis of various design criteria and material properties the holistic Bottles & ShapesTM consultancy program offers line-compatible bottle systems and solutions which strike the right balance between cost and sustainability issues, marketing criteria and user handling. “This calls for a wealth of expertise which we can provide with our decades of experience,” confirms Wiese. Moreover, KHS stretch blow molders have been optimized so that they can process preforms which contain up to 100% recyclate and, alternatively, biopolymer constituents3 – in other words, from renewable raw materials. “The relevance of these materials will increase considerably in the future. Here, we’ve provided the technical means of generating an increase in added value right down the line while saving on resources – such as with the new InnoPET Blomax Series V generation of stretch blow molders,” Wiese continues.
Secondary packaging with a high savings potential
The KHS Competence Center for secondary packaging systems in Kleve, Germany, has long been working on alternatives to classic shrink film. Many of these require extensive testing on the machinery. “The greatest challenge for us is the processability of the packaging materials,” says Karl-Heinz Klumpe, packaging product manager at KHS. “Shrink film made of recycled plastic demonstrates very different shrinking properties versus film made of new material. As an engineering company we can’t provide all the answers ourselves but instead have to coordinate closely with film manufacturers.” KHS stages workshops with these partners in order to do just that, where the participants aim to find out how the percentage of recyclate in film – as stipulated by the new German Packaging Law, for example – can be increased further. Changes to the chemicals or recipe of the film and adaptation of the machine equipment are among the necessary measures which need to be taken here. “The basic proviso is that there’s a standard of quality which is accepted by the big bottlers’ marketing departments. With film made of 100% recyclate the shrink results aren’t yet satisfactory. We’re continuing to rapidly drive development together here to close the gap between growing recycling requirements on the one hand and the demand for packs of ever increasing quality on the other,” Klumpe emphasizes.
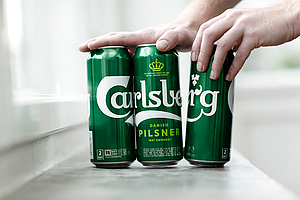
Unique Nature MultiPackTM system
With the development of the Nature MultiPack™ KHS already has a film-free pack in its portfolio which is a pioneer when it comes to sustainability. This reduced form of secondary packaging even makes conventional shrink film on multipacks completely redundant. Here, PET bottles or cans are held together by nothing more than several strong dots of adhesive which are easy to remove. A self-adhesive carrying handle readies the pack for transportation. The dots of adhesive themselves do not impair the quality of the material to be recycled in any way whatsoever as they are easily removed during the recycling process. The Nature MultiPack™ was launched to market as a six pack of cans by the Carlsberg Group under the name of Snap Pack in 2018. Danone Waters first made successful use of this packaging system in 2016 when it launched its Prestige PET bottle for Evian. With it plastic waste is completely avoided as there is no more film packaging to be disposed of.
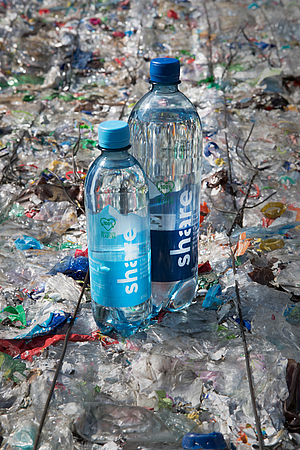
“The current debate on packaging waste has clearly further heightened our awareness for environmentally-friendly packaging systems,” says Klumpe. KHS now offers many different market-proven systems –particularly for PET containers and secondary packaging – which have been proved to specifically help its customers in their endeavor to be more sustainable. “We all take the public discussion seriously and are working directly with all those companies involved on further developments in an attempt to curb the pollution of our environment by plastic as much as we can with the help of our expert knowledge and expertise,” he adds. “In the end we’re all consumers and all of us bear clear responsibility for our own personal actions.”
__________________________
(1) The European PET Bottle Platform is a voluntary industry initiative that provides PET bottle design guidelines for recycling.
(2) The Association of Plastic Recyclers is a North American trade association which strongly advocates the recycling of all post-consumer plastic packaging. To this end the association draws up guidelines and issues certificates for sustainable packaging design, among other things.
(3) For containers like these sugar cane can be used as a raw material instead of crude oil, for instance. The notable characteristic of this material is that special mineral substances are added to the polymer. This cuts down on the amount of plastic in PET bottles without detriment to their resilience, stability and technical properties. The world market for bioplastics such as the above is forecast to grow by 25% in the next five years.
The comPETence center provides your organisation with a dynamic, cost effective way to promote your products and services.
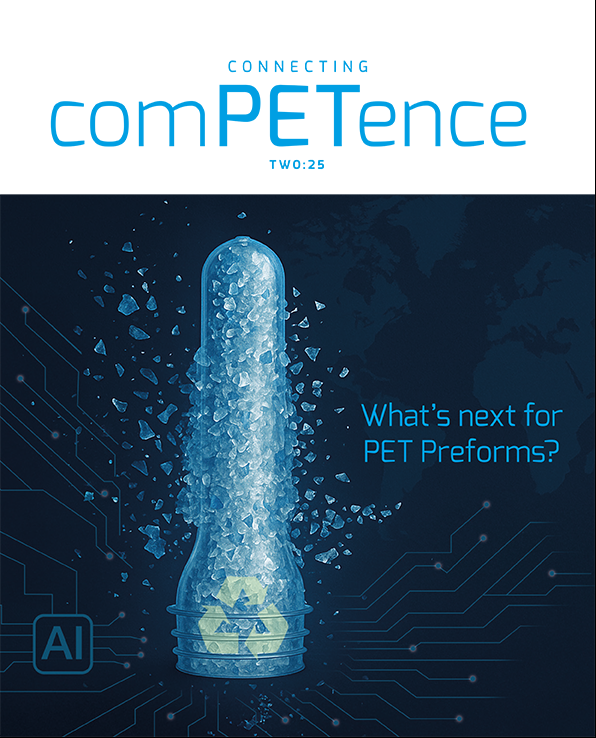
magazine
Find our premium articles, interviews, reports and more
in 3 issues in 2025.