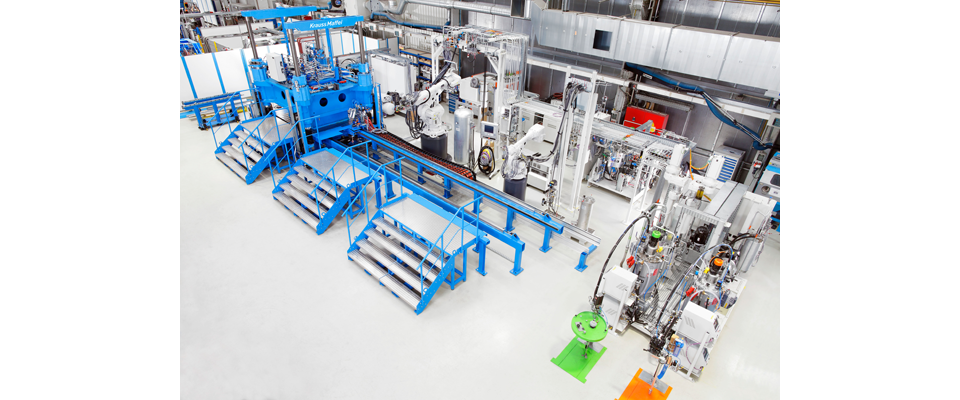
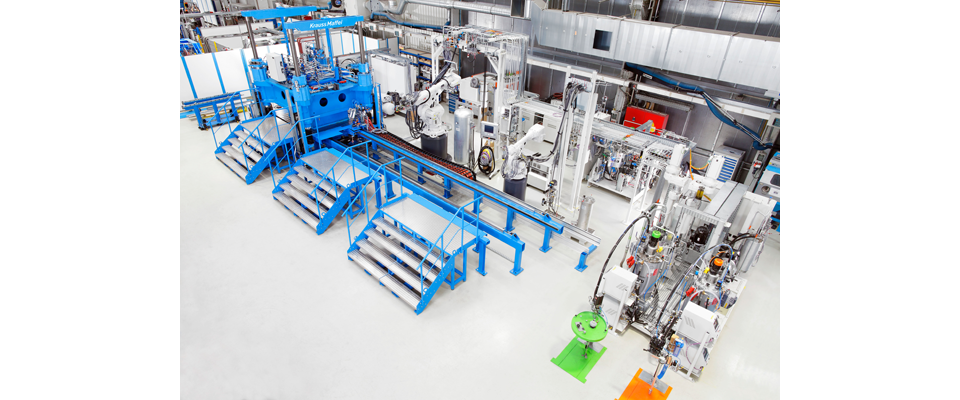
LFI mould carrier. (Photo credit: KrausMaffai)
Injection Molding
Can be freely combined: New shuttle mold carrier complements lightweight construction TechCenter of KraussMaffei
- New MX mold carrier for LFI and SCS spraying technologies
- Focus on development of large-format visible components with Class A surfaces and spraying applications
- Covers entire process chains from idea to series production
KraussMaffei expands its TechCenter with a new shuttle mold carrier and its competence in the area of fiber-reinforced lightweight construction. The new MX mold carrier with a clamping force of 4,000 kN has a flexible design and can be combined both with the LFI process (Long Fiber Injection) or with spraying applications such as the SCS process (Structural Component Spraying). But surface technologies such as R-RIM (Reinforced Reaction Injection Molding) with polyurethane are also possible.
From idea to series production
"The market for fiber-reinforced composites continues to develop very dynamically. We support our customers sustainably from the idea to the serial production. That's why we are continuously modernizing and expanding our lightweight construction TechCenter and offering our customers optimal conditions for developing and testing new production-ready technologies and automation tasks", explains Sebastian Schmidhuber, Head of Development of Reaction Process Machinery at KraussMaffei.
The new shuttle mold carrier is part of a complete system, which has a separate cab and robot for the LFI and SCS spraying processes. A total of five different mixing heads are available for the different tests and automation tasks. A special shuttle carrier is used to quickly transport the bottom mold between the machining stations of the bottom mold. As a result, the foam discharge, for example, can occur in the bottom mold outside of the clamping unit. Another distinguishing feature of the series is the tilting movement of the upper and lower mold fixing platens. "We offer our customers the necessary flexibility and can quickly change over to the respective automation task. And this is possible throughout the entire process chain", adds Schmidhuber.
LFI stands for Long Fiber Injection. The process permits a wide range of applications. Anything is possible in the series from a small trim part for a car interior to a large structural component with a Class A visible surface. Since this is a PUR process where mold cavity pressures are < 10 bar, LFI can be used at the same time to produce a high-strength sandwich element with a honeycomb structure as the core layer.
Structural Component Spraying (SCS) is a further development of LFI honeycomb technology. SCS further reduces the thickness and the weight of the top layers, with the aim of optimizing lightweight construction. In SCS processes, layers composed of fiber mats and honeycomb cores are sprayed with unreinforced PUR, inserted into a mold, and pressed into shape.
Unique lightweight construction TechCenter
The KraussMaffei TechCenter in Munich is leading-edge. On over 4,000 m² more than 25 systems from injection molding, reaction processing machinery and extrusion technology are available for internal tests and customers to optimize their processes in practice or test prototypes. KraussMaffei is at the forefront of developments, particularly in the area of fiber-reinforced lightweight construction. In terms of Reaction Process Machinery this includes, for example, the different RTM processes, Pultrusion or the LFI process, as well as the thermoplastic FiberForm process in Injection Molding Machinery.
The comPETence center provides your organisation with a dynamic, cost effective way to promote your products and services.
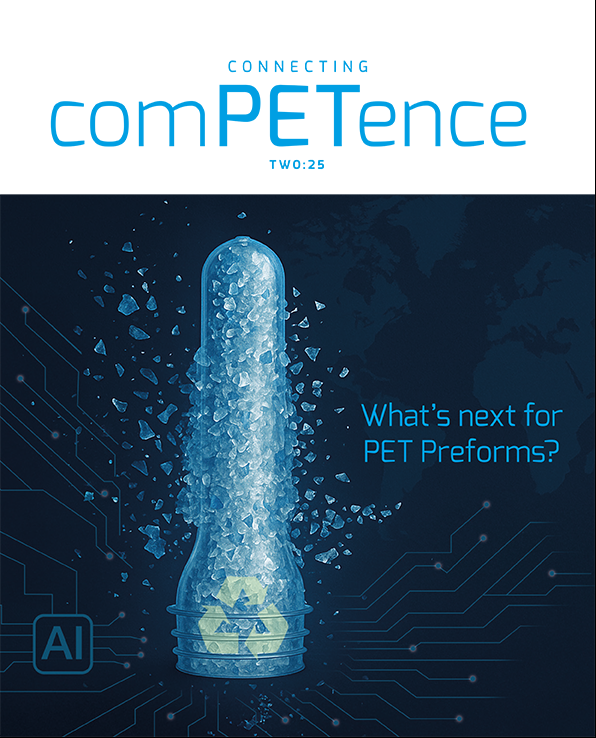
magazine
Find our premium articles, interviews, reports and more
in 3 issues in 2025.