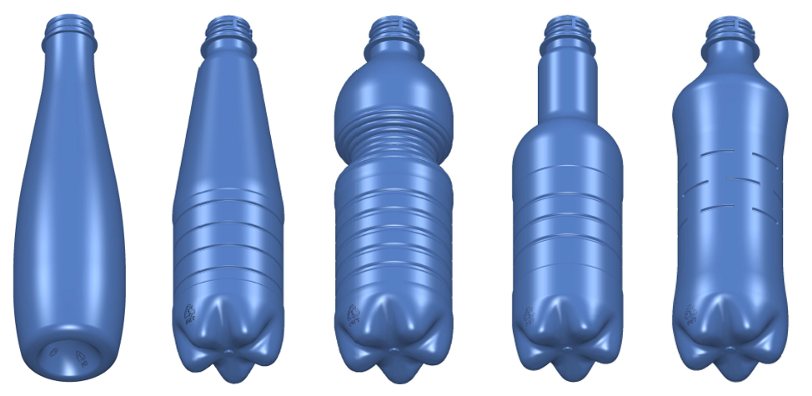
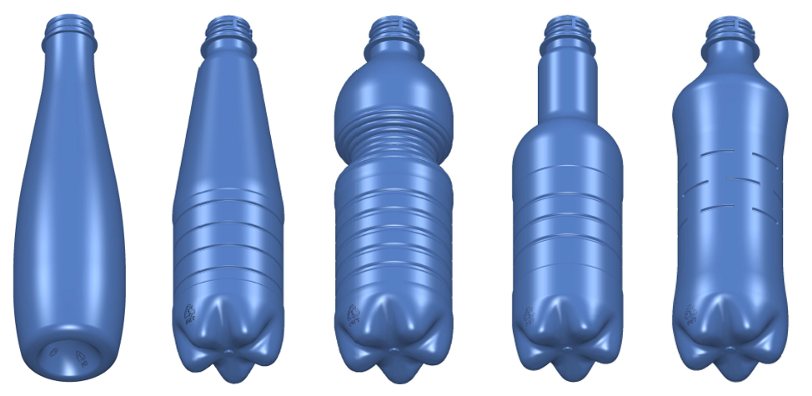
BOTTLE DEVELOPMENT
A well-prepared briefing will speed up the process to an approved bottle drawing
As a mould manufacturer, we always create our bottle drawings from a technical point of view. With our laboratory and the test blowing machine in the background, we benefit from a huge experience of what is technically feasible and where we assume issues with a suggested shape. This basically will help to align on the design for a new bottle, however, this also is related to the briefing which we get from our customers.
A detailed briefing is one key to receive the drawing you are looking for. Design briefings can vary – they can be very short, but already very clear. Or alternatively quite extensive, but confusing. With this article, we would like to discuss the essentials which we prefer to receive to speed up the design process and to brief our engineering team clearly. “Please provide a proposal for a 500ml slim and elegant water bottle which would be unique in the market“ – briefing completed. We really have received such requests in the past, but were not able to just share this with our engineering team as they would not know where to start. Still or carbonated water? Does “slim“ mean the client has a special diameter in mind? What is the individual understanding of elegant? What will be the preform weight for this bottle to consider volume impact or haptical properties already from the beginning? Of course, creativity is important, but with this briefing, there are just too many questions (fig. 1).
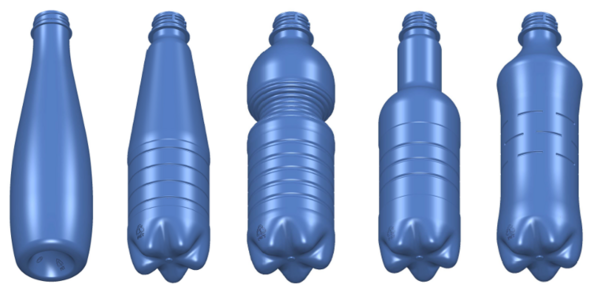
Other briefings are more clear as customers already know what they need to provide to our engineering team to get a quick drawing. No doubt that it is easier to work with already existing ideas in mind or having a reference bottle in front of your eyes. A frequent request is to increase or decrease an existing bottle to a new format, e.g. from 500 to 750 or 1000 ml. We then frequently ask if they have any fixed requirements such as the main diameter or the maximum height which is allowed for proper presentation in the shelfs later or to save costs while using existing personalization parts on the line.
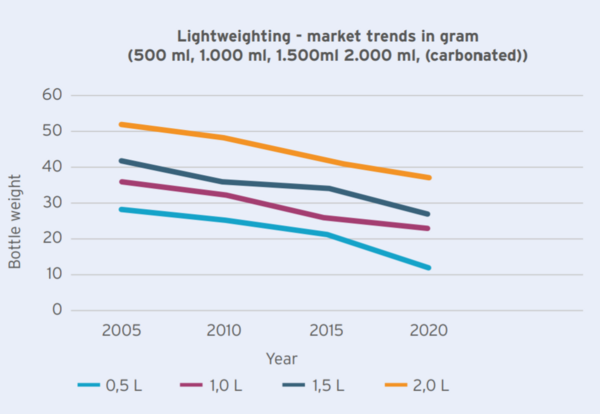
Marketing Department vs. Technical Team – better together!
For sure it is important to have the right people involved in the design phase. Doing a bottle project from a marketing perspective only will be very creative, but most likely not feasible on the production line without having a reduced efficiency. Getting the right know-how during the individual steps of the design phase therefore is quite important. With our experience of making more than 100.000 moulds during the recent 40 years, we always try to balance the feedback between different departments in order to guide our customer to a reliable solution.
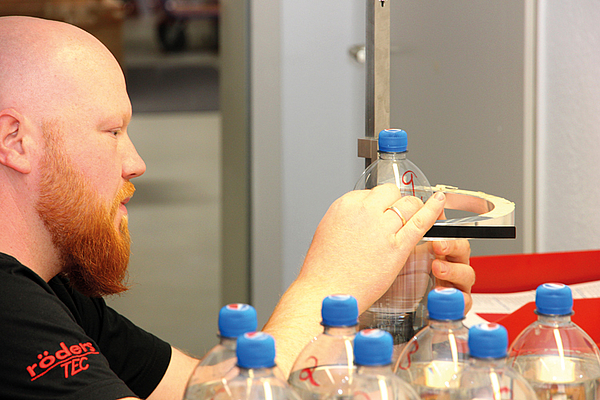
Testing with preferred preform option will give a reliable feedback
What we have seen over the recent years is that testing of new shapes with a qualified laboratory report is getting more and more useful for all involved parties. Since end of last year, we have set our lab to the next level by putting a brand new 1Blow 1XL blowmoulding machine into operation.
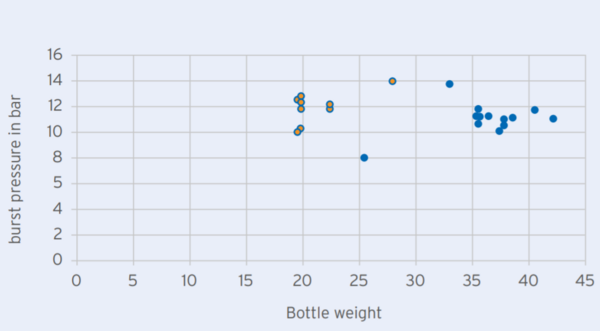
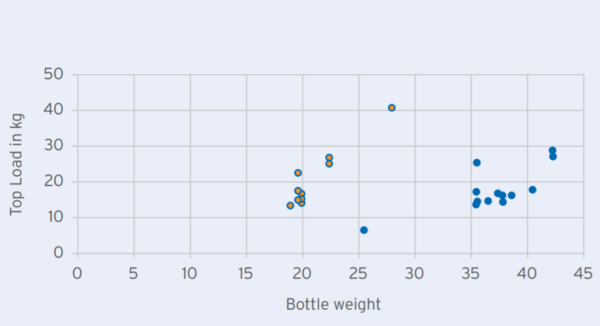
Together with our certified lab equipment, we on short notice can blow a couple of hundreds or thousands bottles with the preferred preform weight and resin and on the one hand ship them to the customer for marketing purposes, line trials or palletization testings and on the other hand perform all important testings on our own. The customer will benefit from quick results and feasibility reports if the created design will meet all requirements or not.
______________________________________________________________________
To be provided for a quick design process
-
Bottle size = required fill-level volume and needed headspace
-
Product to be filled
-
CO2 -level or use of nitrogen during the filling process
-
Name of the bottle/project
-
Preform neck finish + estimated weight, if available: preform drawing
-
Requirements for bottle dimensions such as main diameter, total height, label area dimensions to meet existing personalization parts
-
Labelling: Sleeve or standard label
-
Base design: Petaloid, 6-feet, Champagne base, Star base, a reference type from an existing project or any other requirements
-
Further details
The comPETence center provides your organisation with a dynamic, cost effective way to promote your products and services.
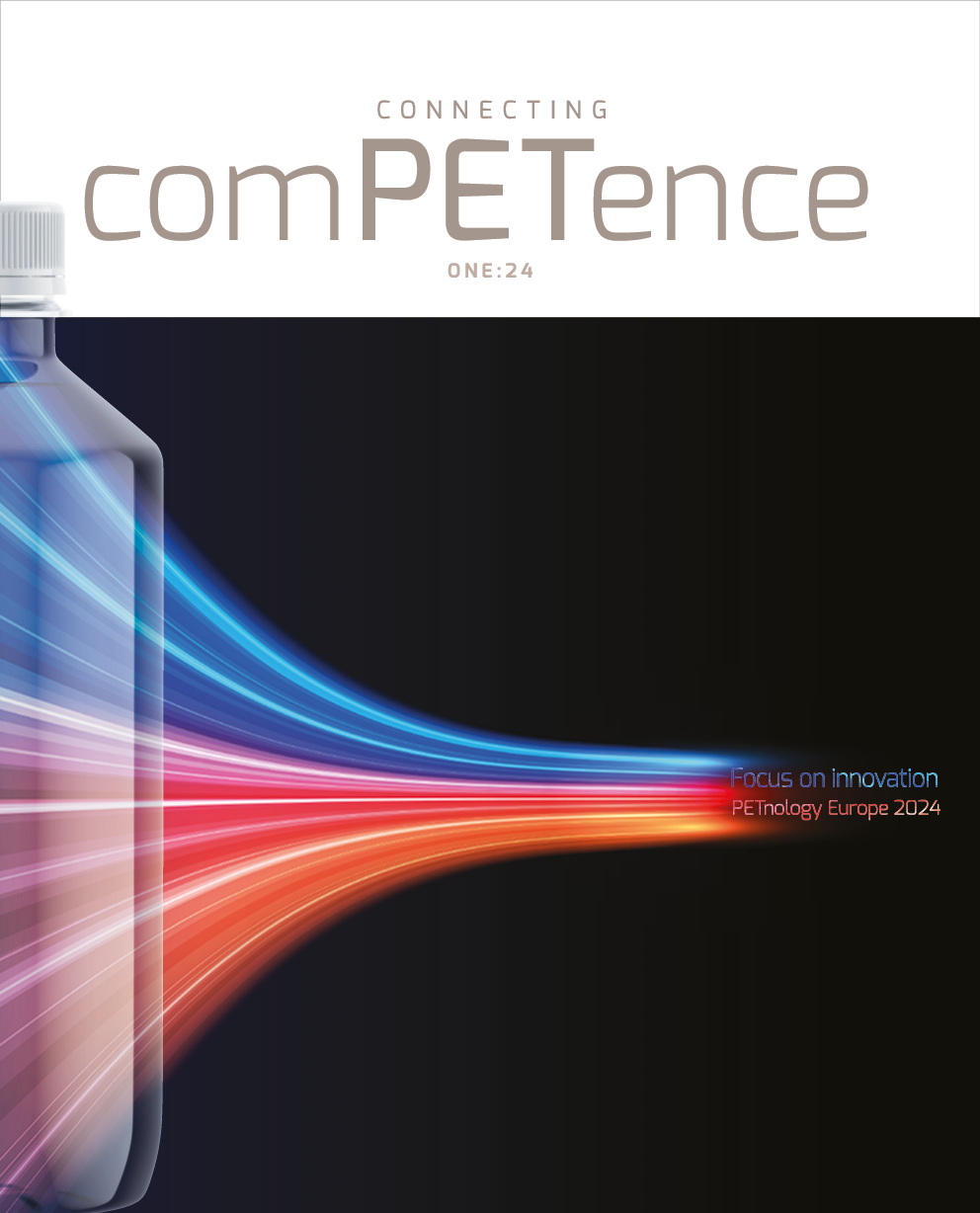
magazine
Find our premium articles, interviews, reports and more
in 3 issues in 2024.